Running a complex operation is not easy. Facilities such as hotels, schools and hospitals each have dozens of assets running, and inevitably breaking, on a daily basis. The resulting downtime can cost the business thousands of dollars and hours of headache.
Priced on per user or per location basis
Available on iOS, Android and Web
While there is no way to stop assets from breaking, there are ways to minimize the impact of that event. By reading this, you will learn the important aspects of reactive maintenance and how to better prepare your organization to handle the unexpected.
If you are looking to learn more about maintenance management, visit our guide on Work Order Management.
Recommended Resources:
- 7 Best CMMS Software For Small Business In 2024
- Facility Maintenance Software
- 8 Best & Free Digital Inspection Software in 2024
- Maintenance Management Software
- 11 Best Safety Management System Software For Workers’ Wellbeing In 2024
What Is Reactive Maintenance?
Put simply, reactive maintenance refers to the processes needed to address and correct any unexpected issue with an asset. Given the vast types of equipment in daily use in each business, reactive maintenance can span from small actions such as replacing a lightbulb, up to large processes such as fixing a faulty air conditioning system.
Typically, each issue triggers a work order, like the one below, to be completed by a maintenance technician. It is important to log all of the important work order details to ensure the issue is corrected to satisfaction.
Reactive maintenance is a part of every manager's work flow, but not all are able to effectively assess, prioritize and take action on each issue. To be prepared for equipment outages, managers must assess their asset inventory, gauge priority and create reactive maintenance plans that provide critical steps to minimize downtime.
What is Reactive Repair?
Reactive repair is a process of maintenance in which repairs are performed when a total failure happens. It is executed in case of machine failure or system crash before taking any steps to correct the problem. Reactive repair is often distinguished from preventive maintenance, which requires daily, scheduled maintenance to prevent problems.
Types of Reactive Repair(s)
A reactive repair can be classified into several types based on the nature and urgency of the repairs:
- Emergency Repairs: These are critical repairs that should be addressed promptly to prevent security hazards, and substantial damage, or to restore necessary services such as fixing gas bursts, electrical outages, or pipe leaks.
- Corrective Repairs: This involves fixing problems after they have been recognized during regular operations or inspections. These are not as critical as emergency repairs but are essential to revive functionality, such as fixing a malfunctioning machine.
- Breakdown Maintenance: This type of maintenance concentrates on resuscitating the gear into working order, like fixing a broken conveyor belt in a plant. It is a reaction to a complete gear loss.
- Failure Maintenance: Equipment is gradually run until it ceases to function, and only then is it rebuilt or returned. It is expected for elements that are either cheap or have a predictable lifespan.
- Postponed Maintenance: Repairs or maintenance duties that are delayed due to budget restrictions or prioritization of other tasks. It can lead to a backlog of maintenance needs.
Each type of reactive repair has its importance in terms of expense, downtime, and possible impact on procedures. The intention of strategy often depends on the specific context, the criticality of the equipment, and resource availability.
Types Of Reactive Maintenance
Due to the large spectrum of reactive maintenance, managers typically break the term down into further categories.
Emergency Maintenance
When an asset disruption occurs, the first question a manager should ask themselves is, “Is this an emergency?” Many assets can withstand partial outages or malfunctions and still operate in a sufficient manner to continue business. Other assets require immediate attention due to operation and safety issues arising from the malfunctioned part.
Maintenance Managers divide reactive maintenance into two categories, Emergency and Corrective Maintenance, to correctly assign priority in these cases.
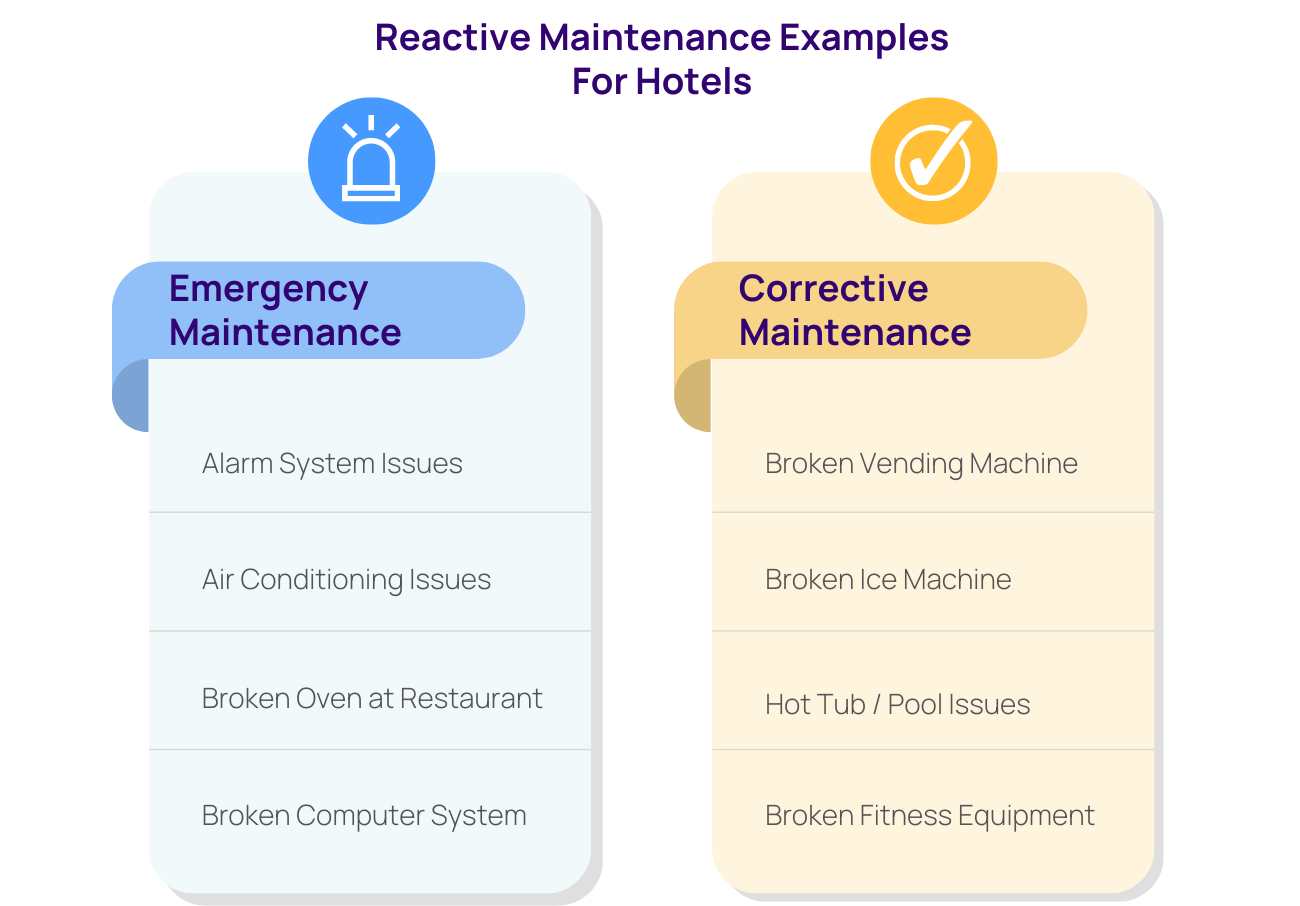
Emergency Maintenance is an activity that must be taken immediately to protect the safety of guests and employees, or to maintain critical business operations. These issues can not be put off and must be of top priority to correct to prevent significant losses.
Emergency maintenance may carry increased costs if the supply of important parts or labor are scarce.
One example of emergency maintenance that places safety at risk would be a malfunctioning alarm system. Managers must be quick to correct malfunctioning alarm equipment to ensure safety of their guests and employees. An example of emergency maintenance that places operations at significant risk is a broken oven at a bakery. Since a baker cannot produce goods without an oven, it is an emergency to correct the issue. Finally there are examples that pose both operational and safety risk and thus require emergency maintenance. Examples of this include a broken roller coaster at an amusement park, or a broken ski lift at a ski resort.
Corrective Maintenance
Corrective Maintenance refers to problems that do not create immediate safety or operational risks to the business. Oftentimes, these issues are important, but do not need to be corrected immediately to continue operating the business. This can be due to the broken part not being essential to the operations of the equipment as a whole, or if the asset itself is not essential to daily operations. In these cases, managers have time to shop around part prices, labor quotes and schedule a maintenance team to correct the issue. In some cases, managers may choose to ignore the maintenance task to prioritize other work or budget.
Examples of corrective maintenance include a broken vending machine at a hotel or light rusting of playground equipment at a school. Corrective maintenance is very important to healthy operations, and must be treated seriously. If not tracked properly, multiple issues can compile, turning what was once-easy corrective issues into an emergency issue.
Run to Failure Maintenance
Run to Failure Maintenance is a deliberate maintenance plan that allows an asset to continue operations until it breaks down and is in need of repair. Run to failure is implemented on assets that are not valuable enough to require ongoing preventive maintenance and monitoring, are plentiful enough that backups can cover the down time or are not integral to the continued operations of the business. Run-to-failure should never be implemented on critical operational equipment or safety related equipment.
Examples of run-to-failure maintenance include basic electrical assets such as light bulbs, televisions and telephones. These assets can easily be replaced in short order and do not require ongoing status reports to ensure uptime.
Examples Of Reactive Maintenance
🏨 Hotel Industry Example
The hotel industry requires many different types of reactive maintenance to sustain profitable operations. Each property likely contains equipment that will directly affect guest experience and thus constitute emergency reactive maintenance. These types of issues span from large problems such as broken HVAC and boiler room equipment to smaller (but impactful) problems such as a broken elevator or room key reader. For these examples, managers should have both preventive maintenance schedules to limit breakages as well as reactive maintenance standard operating procedures to minimize downtime in event of a breakage.
Hotels also possess assets that follow a run-to-failure model. These assets include vending machines, laundry and housekeeping carts, luggage carriers and more. Due to low replacement costs and limited business impact, these assets can be dealt with on a case by case basis.
👵 Senior Living Industry Example
The senior living industry uses a reactive maintenance strategy because of many of its extensive facilities, making it difficult to predict when equipment will fail or need servicing. In addition, these assets can be spread out across the community leading to less oversight and more localized impacts. This requires detailed reactive maintenance plans that cover the location and impact of each down asset.
Examples of emergency reactive maintenance in senior living include broken accessibility equipment for residents or down electrical and HVAC systems. Any one of these issues greatly elevates the risk of accident for residents and must be treated with corresponding seriousness. Senior Living facilities may also experience broken assets where time is less crucial such as a broken golf cart when the property has multiple. In these cases, the down asset does not lead to increased operational or safety risks in the facility.
🏌️ Country Club Industry Example
The country club industry is one of the best examples of reactive maintenance. The sector deals with golf courses, which are a large and complex investment. It's essential to keep them in good condition for guests to have a great experience.
There is a blend of preventive and reactive maintenance involved in maintaining a golf course. While ongoing maintenance such as watering and fertilizing the grass, mowing it, trimming it, and weeding should be scheduled, there are also reactive work orders that need attention. A great example of this is filling in divots left in the fairways and tee boxes by players. These cases likely start as corrective maintenance but can quickly compile into an emergency issue in providing a great golfing experience.
🏫 School / University Industry Example
Reactive maintenance is an essential part of running any school or university smoothly. Students, faculty, and staff can produce significant wear and tear on assets and ensuring safety is of utmost importance.
In elementary schools, even basic maintenance can be emergency maintenance. Any asset that is used by or relied upon for the care of children requires extra attention and speedy correction in event of a failure. Other resources such as chalk boards, toilet issues, or fading playground paint can be handled at a more leisure basis.
With universities dealing with many students in dormitories, maintenance staff doesn't always have regular access to rooms. Due to that, issues are not reported until an asset is completely broken or until the end of the semester. Issues with furniture, lighting, carpet and wall damage fall into this category. Managers need to be aware that many work orders can arise at once, turning small issues into larger outages.
How To Minimize Impact Of Reactive Maintenance
Minimizing the impact of reactive maintenance is dependent on:
🔦 Understanding Your Equipment Scope and Needs
The first step in overcoming this challenge is understanding what equipment and physical assets must be maintained. It includes knowing which assets are used and whether they are performing as expected. Top begin, make a list of all of the assets used in your business, both big and small.
Once you have your list, evaluate each asset on critical dimensions necessary to prioritize work. You can create ranges to group assets together. These dimensions may include:
- Frequency of use
- Replacement cost
- Impact on operations
- Impact on safety
- Inhouse vs external repair
🔎 Knowing What a Breakdown Looks Like
The next step is understanding how each asset could break down. For this, we recommend spending more time on assets that are more expensive and impactful to business operations and safety. Use past experience and research to identify assets that are more prone to and have multiple ways to breakdown. Also note assets that have few ways of breaking down as these are easier to create reactive maintenance standard procedures for.
🧮 Understanding the likelihood of that breakdown occurring
Once you know all of your assets and the many ways that they can break down, managers should try to gauge the likelihood of those events occurring. Details such as asset age and usage amount can drastically increase the likelihood of certain assets experiencing issues.
👷🏻 Understanding the cost of solving a breakdown through reactive maintenance
Once you have identified which assets are likely to experience down time, managers should research how much it would cost if those events occur. This provides many benefits including the ability to forecast reactive maintenance costs as well as frontload the maintenance contractor research so that fast action can be taken without the risk of overpaying or hiring unskilled technicians
🔧 Understanding the cost of preventive maintenance of the asset
Managers should consider preventive maintenance plans and their impacts on downtime likelihood and repair cost as there are often assets that can perform much better with added care. By understanding asset capital expenditure from both a reactive and preventive lens, managers can confidently make decisions that will affect their bottom line.
💰 Prioritizing the budget to focus preventive maintenance on high risk, high impact assets
When you have limited budget for preventive maintenance, it is crucial to prioritize investment to assets that have a high risk and a high impact on business safety or operations.
📋 Creating reactive maintenance procedures for all assets to be implemented in a time of breakdown
Now that you have a detailed asset prioritization list, it is time to create reactive maintenance procedures for each asset. These documents must be stored safely and regularly updated to ensure relevancy as well as to learn from past experiences.
Using a RACI Chart to Manage Reactive Maintenance
When a breakdown occurs, it is essential for all personnel to clearly understand their role in getting the asset back up and running. A RACI (Responsible, Accountable, Consulted, and Informed) chart is a valuable tool for assigning roles and responsibilities for reactive maintenance plans. These tables allow managers to provide multiple perspectives on each issue, with clear action guidance for each role.
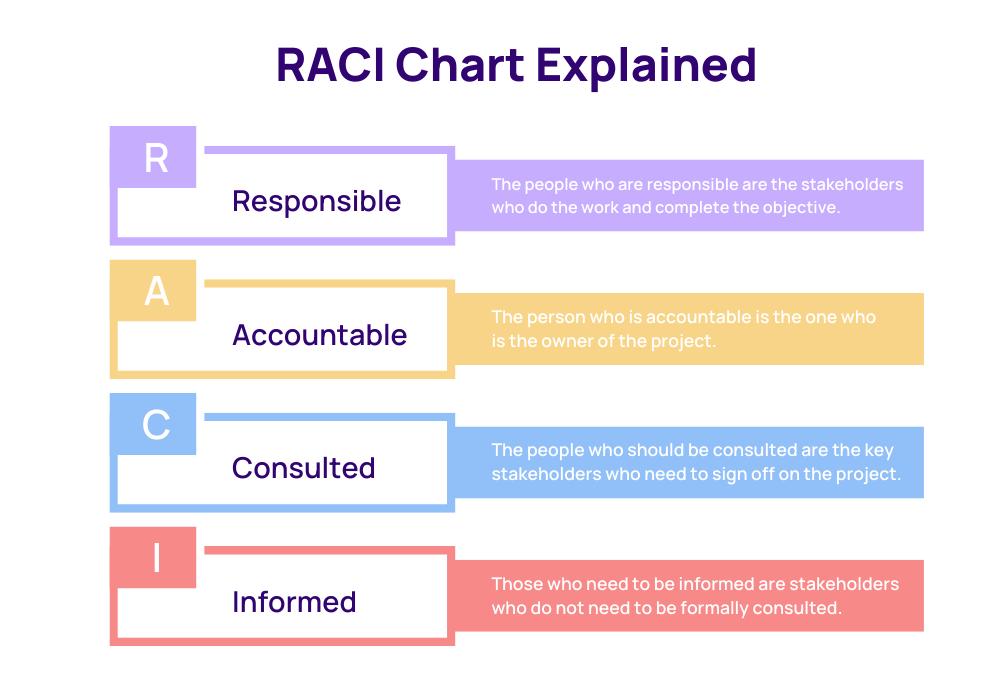
You can use these charts for any project, but they are beneficial when working on projects that involve multiple departments or teams. Due to this, they are helpful when organizing external contractors and ensuring internally that the work has been completed to standard.
How To Create A Reactive Maintenance SOP
This section outlines a five-step process for developing and managing Standard Operating Procedures within your organization.
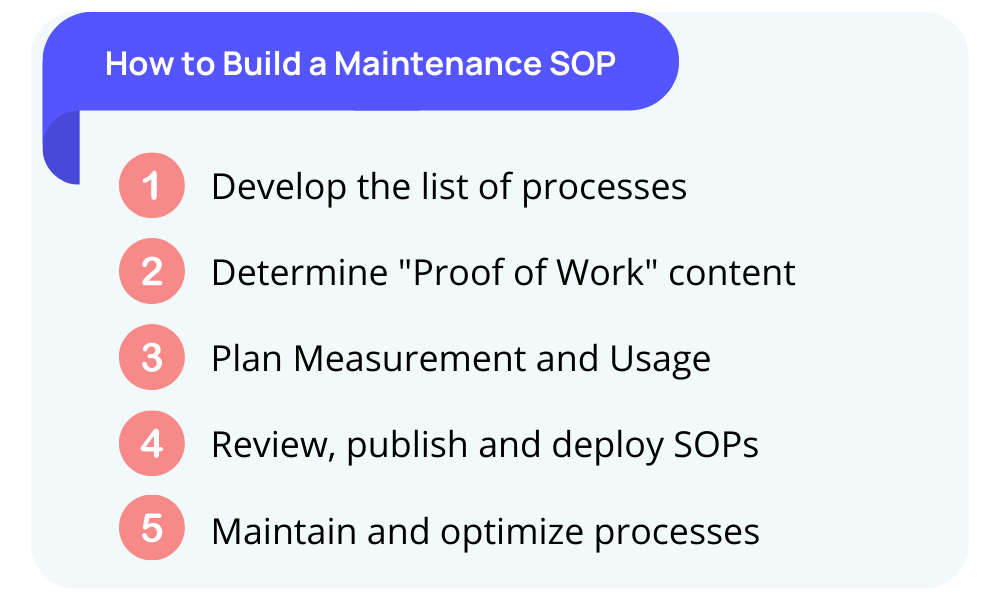
Step 1: Develop a list of processes you believe need SOP creation
The first step in creating a reactive maintenance SOP is to develop a list of processes that you believe need SOP creation. This step ensures that the organization identifies the right strategies and does not waste time on unnecessary ones. Focus your attention on assets that have a high impact but predictable manner of breakdown. This maximizes the likelihood that the SOP will be relevant in the fix.
Step 2: Determine "Proof of Work" content for your SOP
The second step is to collect information about the content of your SOPs. For example, does this document need to include pictures or graphics? Does it need to have step-by-step instructions? Will there be multiple versions of this document based on different job functions or locations? These questions help determine what information needs to be included in each record.
Step 3: Plan the process for managing and measuring SOPs
The third step is to plan the process for developing and managing SOPs. It includes defining where the SOPs will be stored, who can access them, when they should be updated, and what happens if they are not updated when required. It also includes defining who has authority over these documents and how they will be updated when needed. In addition, managers should review the SOP for measurability. From each SOP, a manager should be able to measure success and efficiency in order to optimize over time.
Step 4: Review, publish and deploy your SOP
The next step is to write it in clear and concise language. Next, you need to edit the document and make sure it includes all the necessary information. Once you have written your SOP, it's essential to review it often to ensure it's still relevant and up-to-date.
Step 5: Maintain and optimize your SOP over time
Once you have an SOP in place, it's crucial to maintain it. It means reviewing and updating the SOP every time there's a change in your facility. For example, if you add a new piece of equipment or make changes to an existing one, you'll want to update your SOP to reflect these changes. You can also use this opportunity to review any other updates needed. If the process has changed or there are new procedures, you'll want to update them in your SOP and make sure everyone is familiar.
How To Track Reactive Maintenance Costs
The cost of reactive maintenance can be challenging to track. Most organizations don't have a dedicated process for identifying and monitoring reactive maintenance costs.
The good news is that there are several ways to do so:
📋 Use Digital Checklists & SOPs
Digital checklists are a great way to track the condition of your equipment. They allow you to identify potential problems before they occur and provide detailed instructions on fixing them.
Additionally, digital checklists enable you to track the frequency at which certain repairs are performed, which helps you identify potential problem areas in your facility. By logging repair costs with each asset SOP, managers can quantify their total reactive maintenance costs by asset over time.
📊 Use Cost Schedule
If your facility has multiple components that need to be maintained independently, a cost schedule can help ensure that each element is fully supported. The cost schedule will include all of the parts required for each piece of equipment and their standard maintenance needs.
It will also include an estimate of what it would cost if something goes wrong or breaks down unexpectedly – so you know exactly how much money is being spent on maintenance inspections every year.
Other Maintenance Strategies To Consider
There are several maintenance strategies to consider for reactive maintenance:
🛠️ Preventive Maintenance
This type of maintenance involves regular checkups and replacements before the system or equipment fails. Preventive maintenance helps avoid major failures by keeping equipment in good working order.
Preventive maintenance is not just about the equipment but also includes a process improvement plan and employee training. Preventive maintenance is typically scheduled at regular cadences such as weekly, monthly, quarterly and annually. The best way to keep track of preventive maintenance is to put it in a centralized digital calendar like the free template below.
📈 Predictive Maintenance
Predictive maintenance uses data from sensors to predict when equipment will fail and alert staff before problems occur so they can stop the issue before it causes expensive damage.
This type of system requires special software and hardware, so you will need to invest in these before you begin this type of maintenance strategy.
🧰 Ongoing Maintenance
In this strategy, you will perform routine checks on your systems and equipment every few months or years rather than waiting until something breaks down or fails before taking action.
Ongoing maintenance is less expensive than other options because it doesn't require purchasing new equipment or spending money on repairs at the first sign of trouble.
FAQs
- What are some examples of emergency maintenance?
Below are some common examples of emergency maintenance;
- Burst Water Pipes: Quick repair is needed to prevent water damage and restore water supply.
- Electrical Outages: Fixing sudden electrical failures to prevent safety hazards and restore power.
- HVAC System Breakdown: Urgent repairs in extreme weather to ensure safety and comfort.
- Elevator Malfunctions: Quick response to fix broken elevators, especially if they are stuck with passengers inside.
- Severe Roof Leaks: Addressing leaks promptly to prevent structural damage and
protect interiors.
- What is the opposite of reactive maintenance?
The opposite of reactive maintenance is preventive maintenance, which involves regularly scheduled inspections and maintenance tasks to prevent equipment failures before they occur.
- What is Reactive Maintenance Workflow?
Reactive maintenance workflow is a process that is used when equipment fails or a system breaks down. This workflow typically follows these steps:
- Failure Identification: The process begins when a failure or breakdown is identified. This could be reported by machine operators, staff, or through monitoring systems.
- Issue Reporting: The identified issue is reported to the maintenance team. It can be done through various channels like direct communication, emails, or a maintenance management system.
- Assessment and Prioritization: The maintenance team assesses the reported issue to determine the severity and impact. Based on this assessment, the repair work is prioritized.
- Dispatching Maintenance Personnel: Once the issue is prioritized, the relevant maintenance personnel are dispatched to the location of the breakdown.
- Diagnosis: The technicians diagnose the problem to understand the root cause of the failure.
- Repair and Replacement: The technicians carry out the necessary repairs or replace faulty parts to fix the issue.
- Testing and Validation: After the repairs, the equipment is tested to ensure it is functioning correctly and safely.
- Documentation and Feedback: The maintenance work is documented for future reference. This documentation includes details about the failure, the repairs done, parts replaced, and any observations for future preventive measures.
- Resume Operations: The equipment is put back into operation once it is confirmed to be in working order.
The reactive maintenance workflow is characterized by its responsive nature, managing issues as they arise rather than preventing them through regular maintenance.
While this approach can sometimes be cost-saving in the short term, it can lead to higher operating costs and downtime in the long run compared to preventive maintenance strategies.
Wrapping Up
Maintenance is often viewed as a cost center. That can be true for reactive maintenance, but only if you don't see the bigger picture.
When done right, reactive maintenance can help you:
- Cut costs by reducing unplanned downtime
- Improve productivity by keeping equipment running at peak efficiency
- Minimize risks associated with poor machine performance.
In a nutshell, reactive maintenance isn't just about keeping equipment running. It's about keeping your business running smoothly and efficiently. Tools such as Xenia make this process seamless and digital to ensure proper audit trails and cost accounting.
.webp)
%201%20(1).webp)