Finding the best predictive maintenance software to manage your asset and facility maintenance can prove to be a real challenge.
Optimal maintenance management and operational efficiency can be achieved via the strategic selection of a new solution.
Nonetheless, there's no denying that it's a strategic process, with both imminent and future risks depending on the solution's suitability and your company's ability to adapt.
Every work predictive maintenance software, whether built with comprehensive functionality or just to simplify equipment maintenance activities, has its own set of advantages and disadvantages.
Today, we'll drill down on different aspects of predictive maintenance software, it’s cost and plenty of stuff that goes beyond the superficial buzzwords that often impedes deeper knowledge.
So, here’s to making an informed decision!
7 Best Predictive Maintenance Software In 2024
Here's a detailed list of the best predictive maintenance apps that you can try out for free.
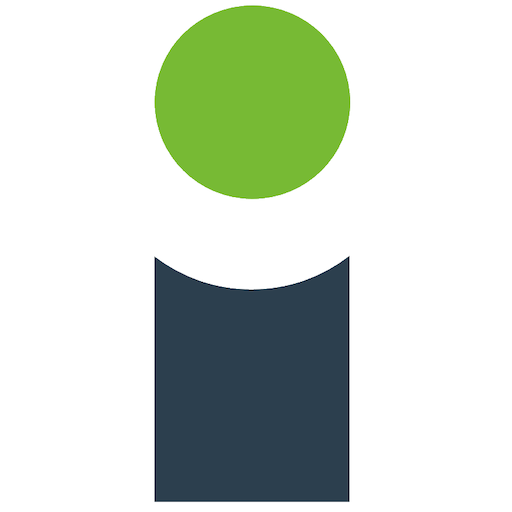
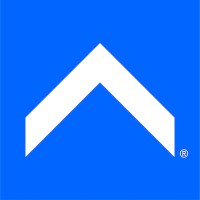
1. Xenia - Overall No. 1 Online Predictive Maintenance App for Businesses
.webp)
Transform your asset management with Xenia, an innovative AI-powered maintenance management platform designed for enterprise-grade applications.
And yes! It covers the predictive maintenance bit, since this application is an end-to-end maintenance management solution unlike any other out there.
Strong asset management, effective data collecting, comprehensive analysis, and simplified work order administration are some of Xenias' exceptional features that can assist you in anticipating and avoiding any maintenance related problems.
You can simplify your operations by combining inspections and audits, work orders, SOPs, and preventative maintenance workflow over a centralized dashboard.
On top of that, as one of the best predictive maintenance software, Xenia also offers different solutions that are integrated and proactive in nature, allowing you to maximize equipment performance, reduce downtime, and boost company efficiency.
Key Features
- Preventive Maintenance Scheduling: Stay proactive and connected to your maintenance schedule with mobile access.
- Inspections & Audits: Conduct inspections and audits through detailed work orders. Assign them to frontline team for active issue resolution.
- Customizable Operations Templates & Checklists: Create, download or customize any number of checklists for any predictive maintenance use case. Xenia has a repository of ready-to-use checklists that you can download in seconds!
- Tasks & Work Orders: Streamline your operations with features like centralized work orders, preventive maintenance scheduling, and detailed inspections.
- Chats: Xenia offers real-time notifications and updates, ensuring all team members are synced and aware of the task status, promoting effective collaboration.
- Corrective Actions: Using conditional logic and monitoring completion, create instant resolution work orders based on as soon as an issue is identified.
Pricing
- Free Forever: Free for up to 5 users, alongside access to all the basic features
- Starter: $99 / month for 15 users with access to core features
- Premium: $199 / month for 15 users with unlimited access to all the core & advanced features
- Custom: Need something tailored to your organization?
Go ahead and Book a Demo today to see how Xenia works in action.
Priced on per user or per location basis
Available on iOS, Android and Web
2. LLumin
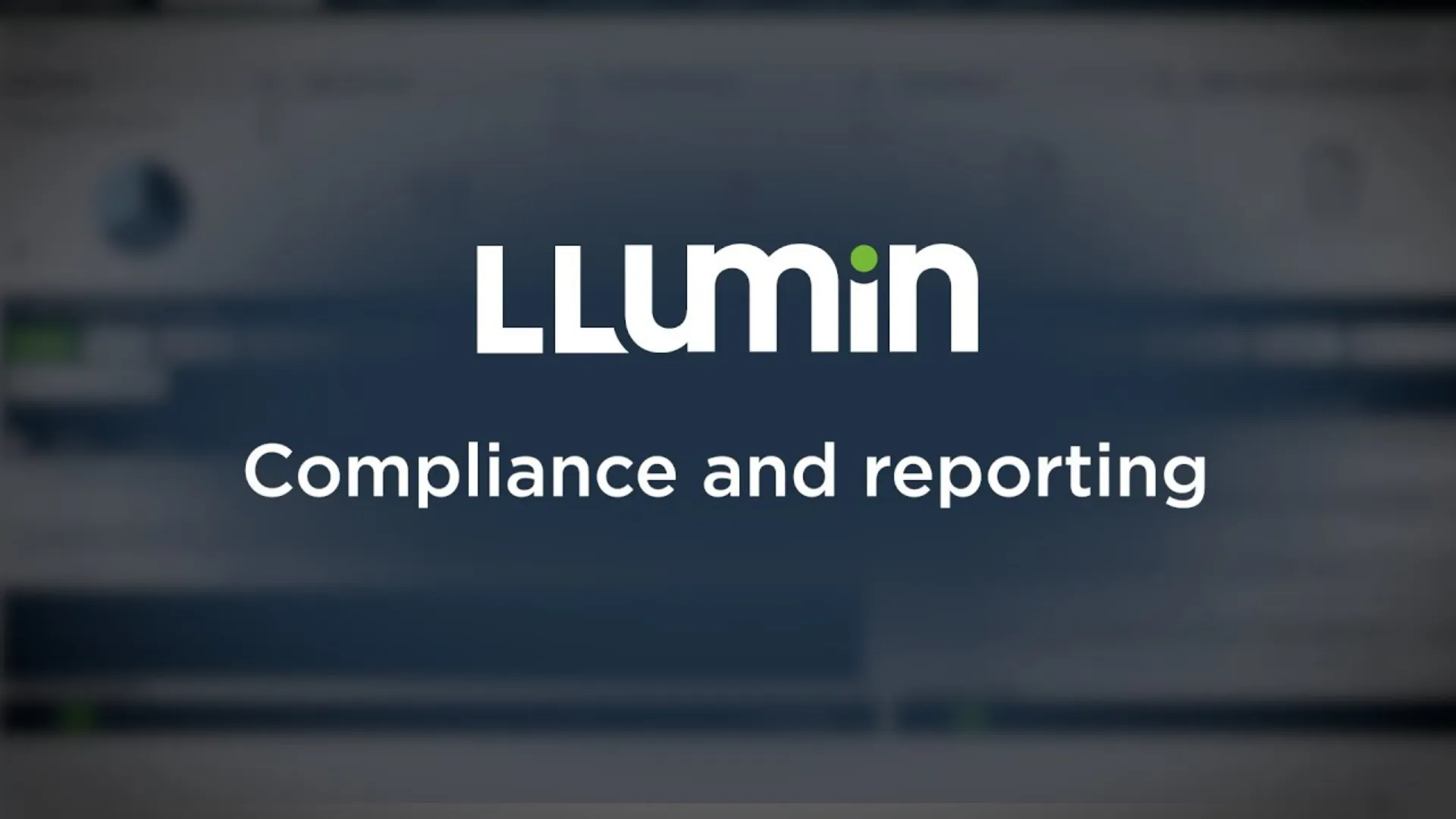
LLumin provides innovative CMMS+ (Computerized Maintenance Management Software) as well as EAM (Enterprise Asset Management) solutions.
LLumin's cloud-based, mobile-ready CMMS+ was developed to help enterprises manage assets and maintenance operations more effectively, with an emphasis on minimizing downtime and boosting productivity.
Manufacturing, utilities, higher education, municipalities, and the hospitality sectors are just a few of the industries addressed by LLumin's all-in-one solution.
Key Features
- Predictive Maintenance: The AI-driven predictive maintenance features of LLumin's CMMS+ set it apart. To predict equipment breakdowns, the program leverages real-time IoT data and machine learning techniques.
- Comprehensive Implementation Support: LLumin provides a white-glove installation service, supporting users through the process of incorporating CMMS+ into their facilities. This guarantees a seamless transition to the new system, which is handled by specialists who are familiar with the difficulties of the best predictive maintenance software implementation.
- User-Centric Design: The LLumin CMMS+ was created with the end user in mind. It is readily customized according to work position, enabling employees to operate the system intuitively and simply.
Pricing
- Professional: $45/mo Price per user
- Premium: $80/mo Price per user
- Enterprise: $110/mo Price per user
3. Uptake
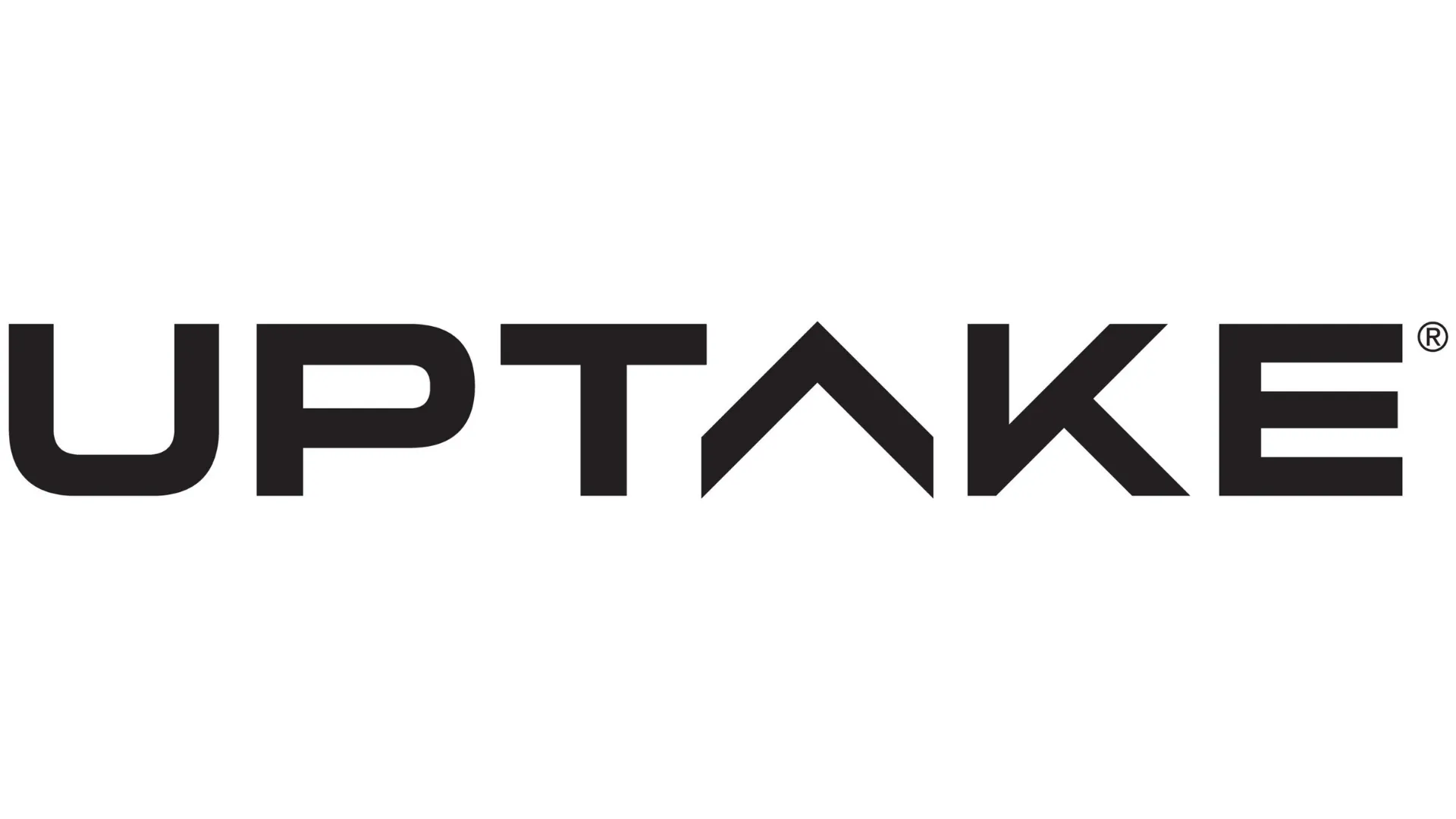
Uptake is an enterprise-grade predictive maintenance technology that leverages AI and machine learning to detect and prevent equipment breakdowns.
It has a broad variety of capabilities such as asset management, data collecting, data analysis, work order management, reporting, and dashboards.
They offer to provide real-time insights. Easily show streamlining findings in an ultra-simple UI, so you can make smarter business choices that equate to a healthier bottom line.
Key Features
- Precision Maintenance: Optimizing maintenance costs by minimizing unexpected expenses from unplanned outages and downtime.
- Rapid Insights: In the shortest amount of time, meaningful information can be retrieved from operational data and made accessible to a broad range of stakeholders.
- Enterprise-scale Impact: Simple connection with current data and procedures to immediately gain value via improved connectivity.
Pricing
- Contact vendor for information
4. eMaint
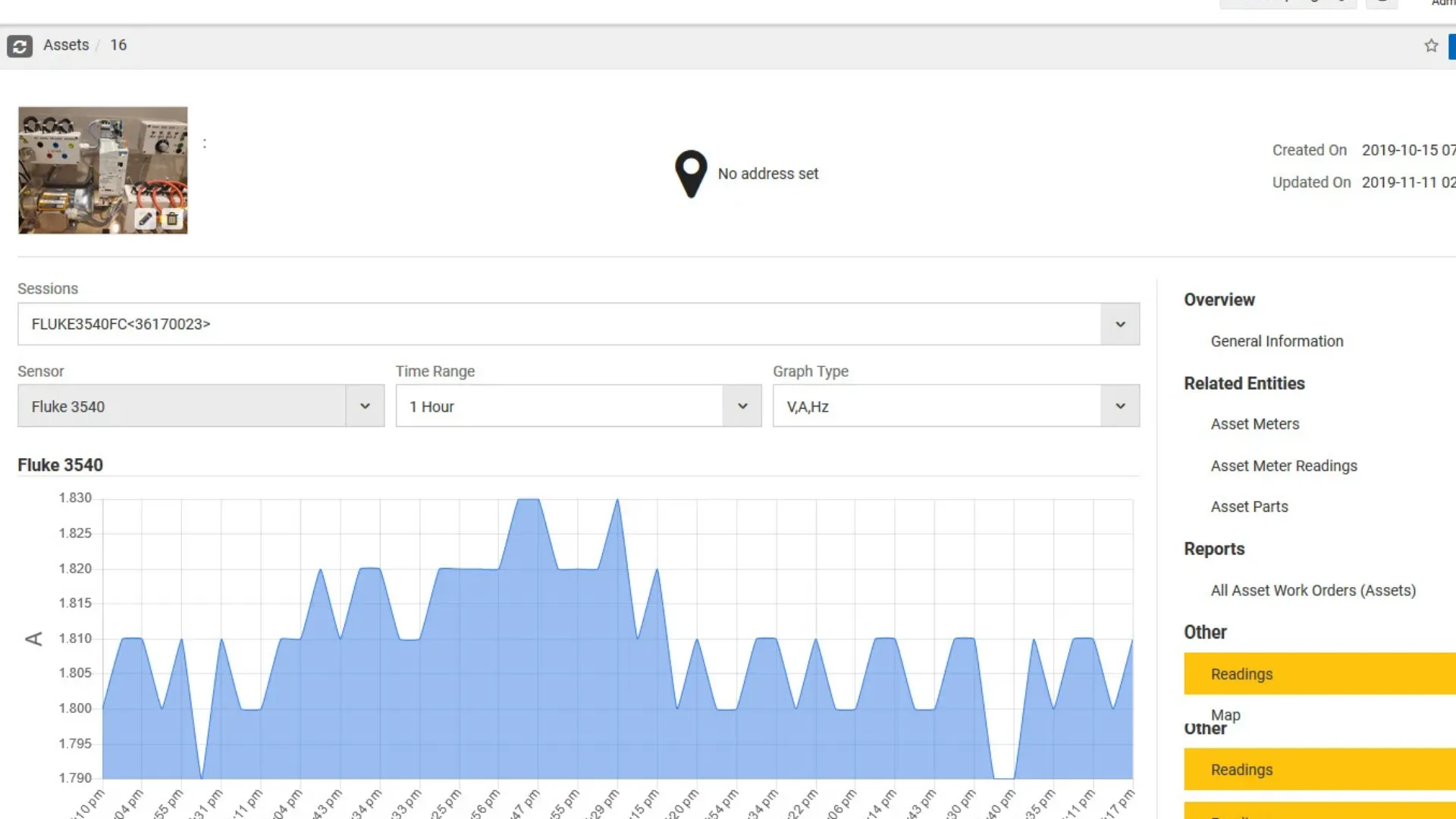
Predictive maintenance features are also available in eMaint, a Computerized Maintenance Management System (CMMS) software. It performs very well in predictive analytics, scheduling preventative maintenance, and asset status monitoring.
Utilization, condition monitoring, and maintenance data provide significant insights that help to prolong asset life. Investigate the history of maintenance. Manage the asset lifetime from purchase to end-of-life.
Key Features
- Asset Management: Find assets quickly in an ordered asset hierarchy, which simplifies management and extends asset longevity.
- Work orders: Embrace organized and easy-to-use work orders, a drag & drop PM calendar, and automated work orders based on asset data.
- Reporting: eMaint simplifies enterprise-level reporting, KPI tracking, audit dashboards, and more.
Pricing
- Team: Starting at USD - $69
- Professional: Starting at USD - $85
- Enterprise: Custom quote
5. PMXpert
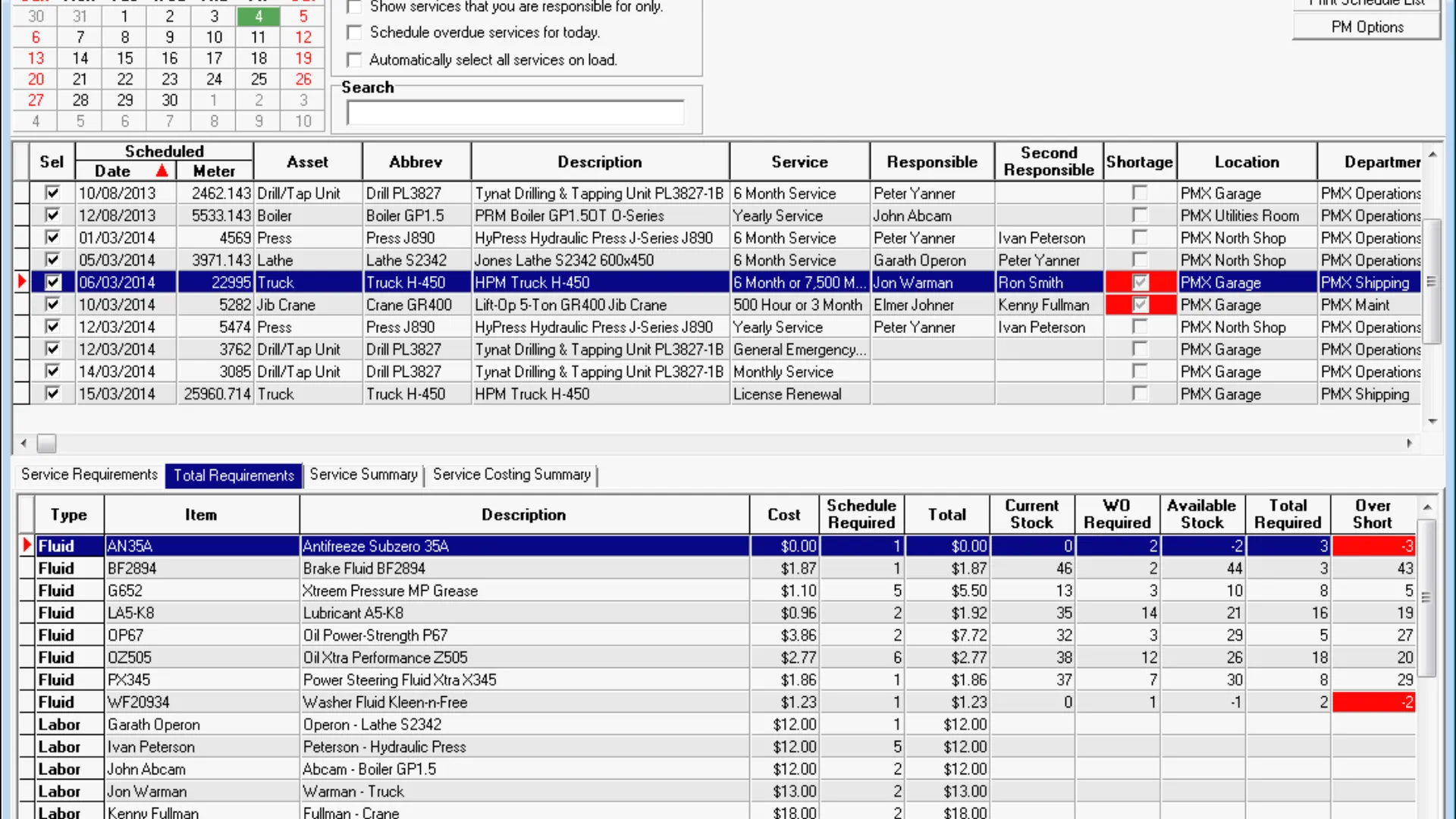
PMXpert is simple-to-use predictive maintenance software designed for small and medium-sized organizations.
In simple terms, it provides asset management, data collecting, data analysis, work order management, reporting, and dashboards.
PMXpert helps schedule services on time. Inspections and emergency repairs can be combined with planned maintenance to save downtime and boost productivity.
Key Features
- Work Orders: The Work Orders automatically pull in services, procedures, and required parts set up on the assets.
- Inventory Control: With PMXpert's precise inventory and automated purchase order system, you can keep your inventory organized, buy more effectively, and avoid waste.
- Maintenance Management: Reduce asset failures and prevent over-servicing by setting up maintenance services on your assets based on the usage calculation of your choice.
Pricing
- 30-day free trial
- Ask for a Custom Quote
6. Oracle
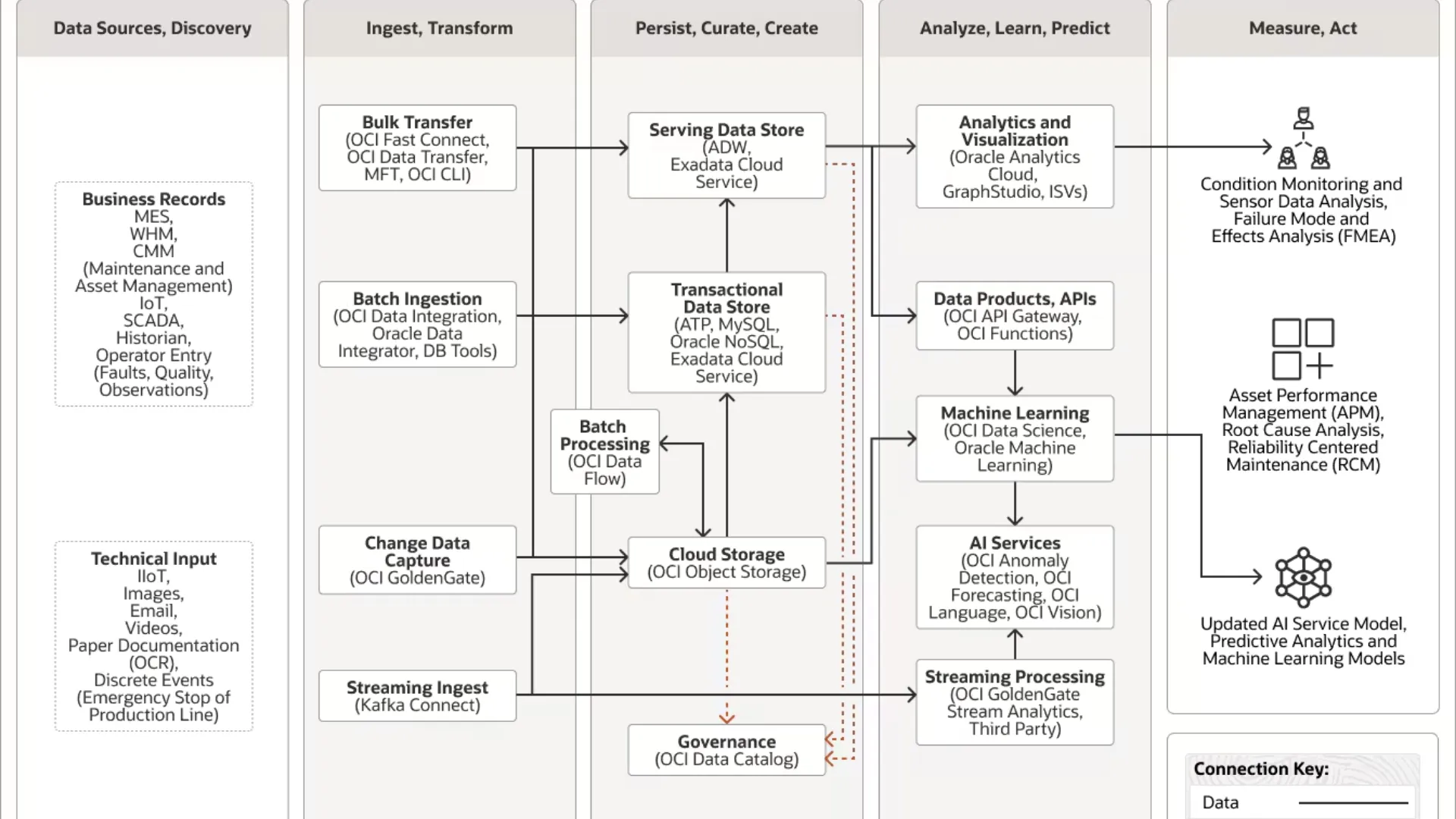
Up next on our best predictive maintenance software list, we've got Oracle.
Yes, it's more of a household name in the industry because Oracle has tons of different solutions for a multitude of businesses & use cases.
Speaking of predictive maintenance, this cloud-based system, which is part of the Oracle IoT Cloud portfolio, includes asset management, data collecting, data analysis, work order management, and reporting and dashboards.
Track the location, health, and use of your assets in real-time, lowering total maintenance expenditures. Contact center agents may monitor assets and data on their dashboards and then try to resolve issues as soon as possible.
Key Features
- Service Connected Assets: Connect every asset type or subcomponent across any network to provide insights to your contact center.
- Detect Abnormalities: Identify problematic components visually and automatically detect defects and irregularities to engage the right service resources and keep the asset functioning.
- Analytics with Machine Learning and AI: Create visual patterns and user-friendly interfaces for complex analytics aggregation.
Pricing
- Ask for a Custom Quote
7. Brightly Asset Essentials
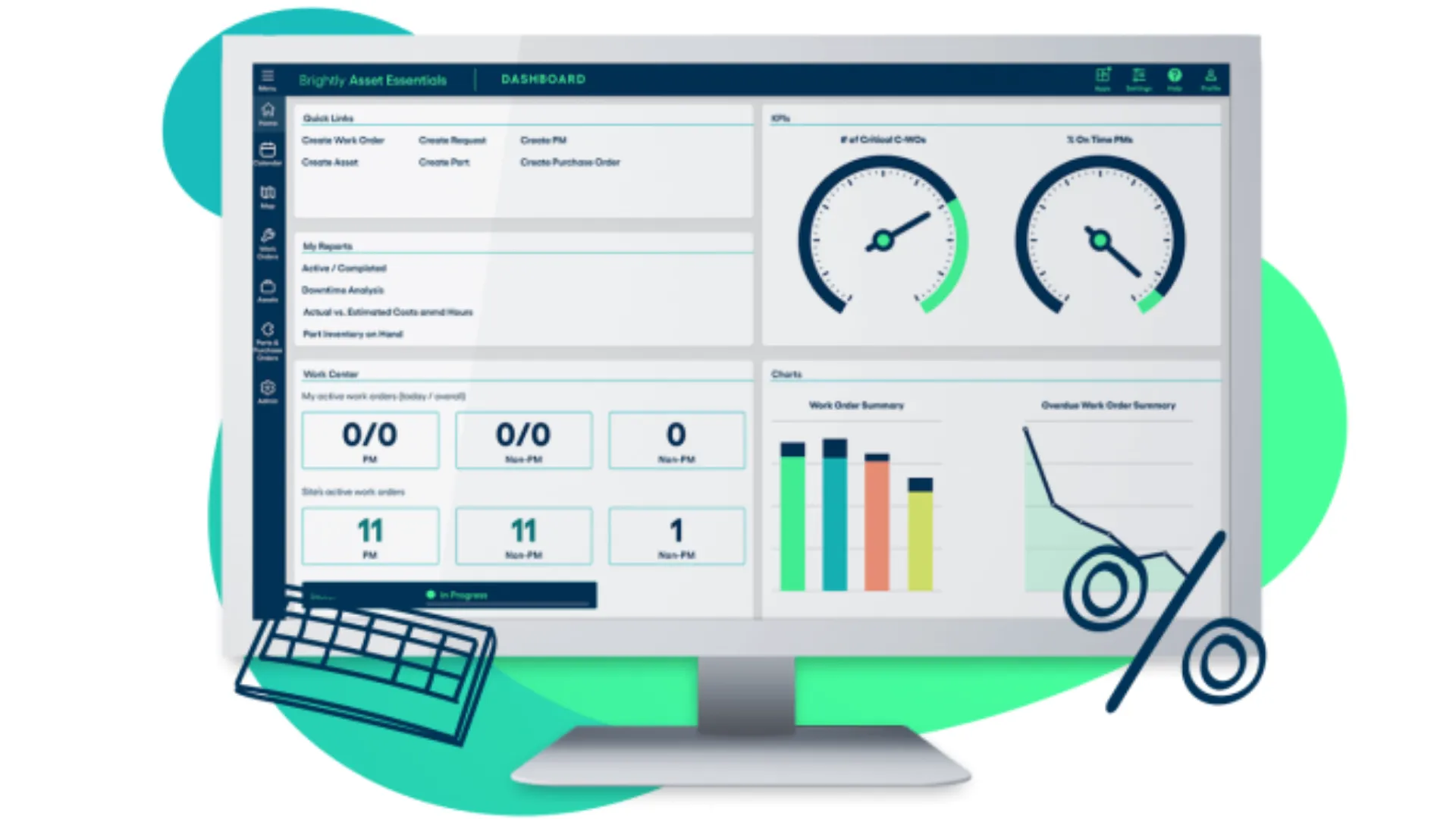
Brightly Software's (previously Dude Solutions') Asset Essentials is a next-generation work and one of the best predictive maintenance software built for smarter, more effective maintenance and operations.
Brightly, which is now part of Siemens, is the worldwide leader in intelligent asset management systems. Over 12,000 operations leaders use this system to handle over 49 million assets and 386 million work requests.
This user-friendly preventive maintenance program software enables businesses to reduce maintenance costs, increase productivity, and make better operational choices.
Key Features
- Mobile Work Order Software: With our cloud-based asset management software, you can enable your personnel to boost productivity while on the road. Reduce travels to the office for the next work to increase the efficiency of your team.
- IoT Remote Monitoring: Using up-to-date asset health information, you can quickly detect and maintain underperforming assets before they become a serious issue using IoT remote asset management.
- GIS Mapping Integration: Create a map of facilities and infrastructure assets to readily see where work needs to be done and compare asset status across several locations.
Pricing
- Ask for a Custom Quote
What is Maintenance Management?
Maintenance management, at its core, is a structured approach and practice focused on the planning, organization, execution, and monitoring of maintenance work. Everything from emergency repairs to full preventative and predictive maintenance plans is covered.
Maintenance management is especially important in industrial and manufacturing environments, where machinery and production-oriented equipment serve as the backbone of the operation, and downtime cannot be allowed.
Predictive Maintenance (PdM) Definition
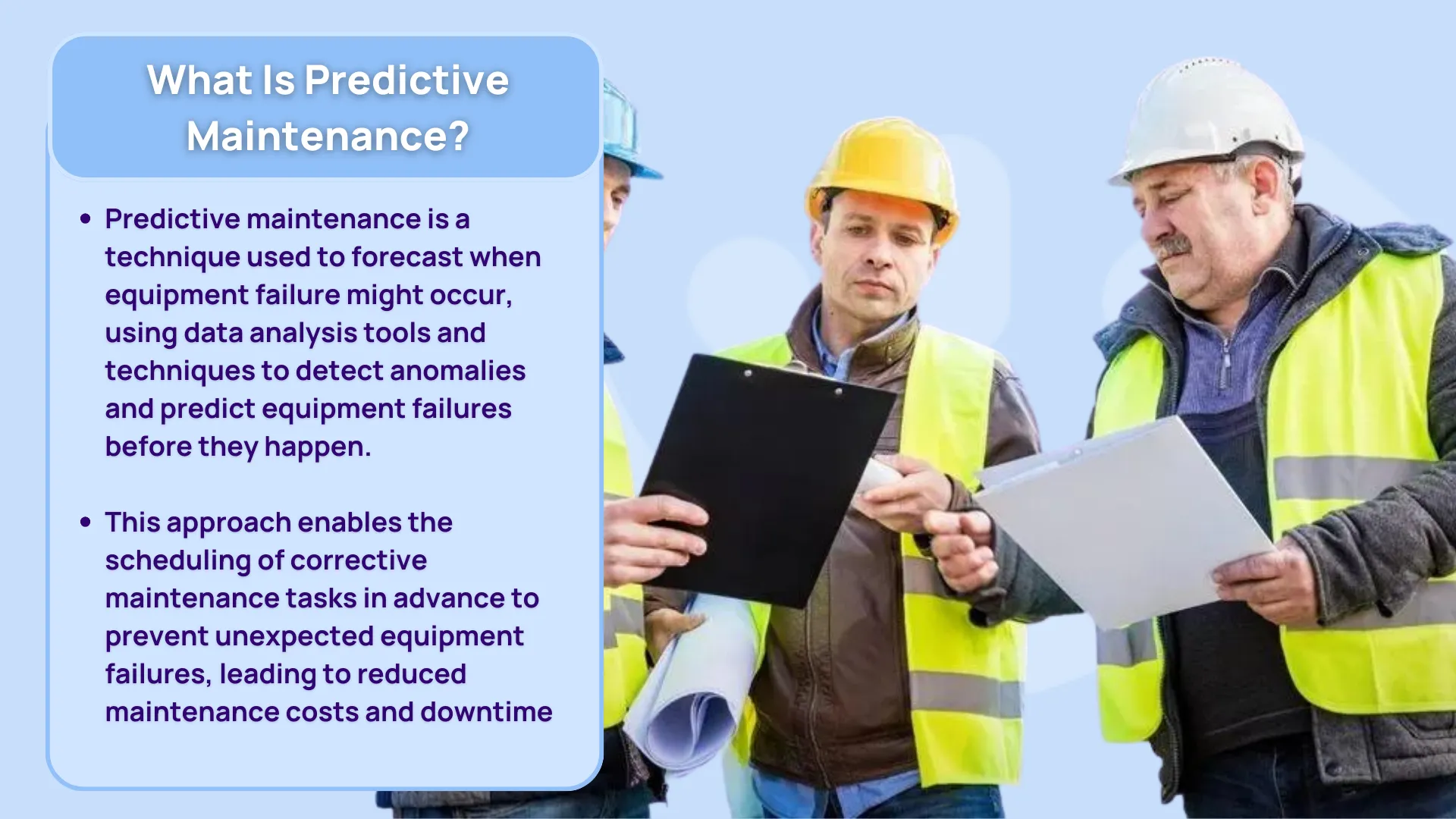
Predictive maintenance (PdM) uses data analysis to discover operating irregularities and probable equipment problems, allowing for prompt fixes before failures occur.
It seeks to reduce maintenance frequency, preventing unforeseen outages and excessive preventative maintenance expenses.
According to Deloitte, AI-powered anomaly detection and fault prediction in predictive maintenance could result in significant advantages such as:
- Increasing the runtime by 10 to 20%.
- Saving up to 10% on maintenance expenditures.
- Reducing the amount of time required for maintenance scheduling by up to 50%.
Predictive maintenance differs from preventive maintenance in that preventative maintenance often schedules maintenance actions based on operator and supervisor expertise.
How Does Predictive Maintenance Work?
Predictive maintenance activities help to predict issues by analyzing historical and real-time data from multiple areas of your business. Predictive maintenance affects three major aspects of your organization:
- Real-time monitoring of asset status and performance
- Work order data analysis
- MRO inventory utilization benchmarking
Predictive maintenance is strongly reliant on technology and software, notably the integration of IoT, AI, and integrated systems.
These systems link disparate assets, allowing for data exchange, analysis, and actionable insights.
Sensors, industrial controls, and simple preventive maintenance software such as EAM and ERP collect data. This data is then analyzed to identify problem regions using methods such as vibration analysis, oil analysis, thermal imaging, and equipment monitoring.
Why is Predictive Maintenance Essential?
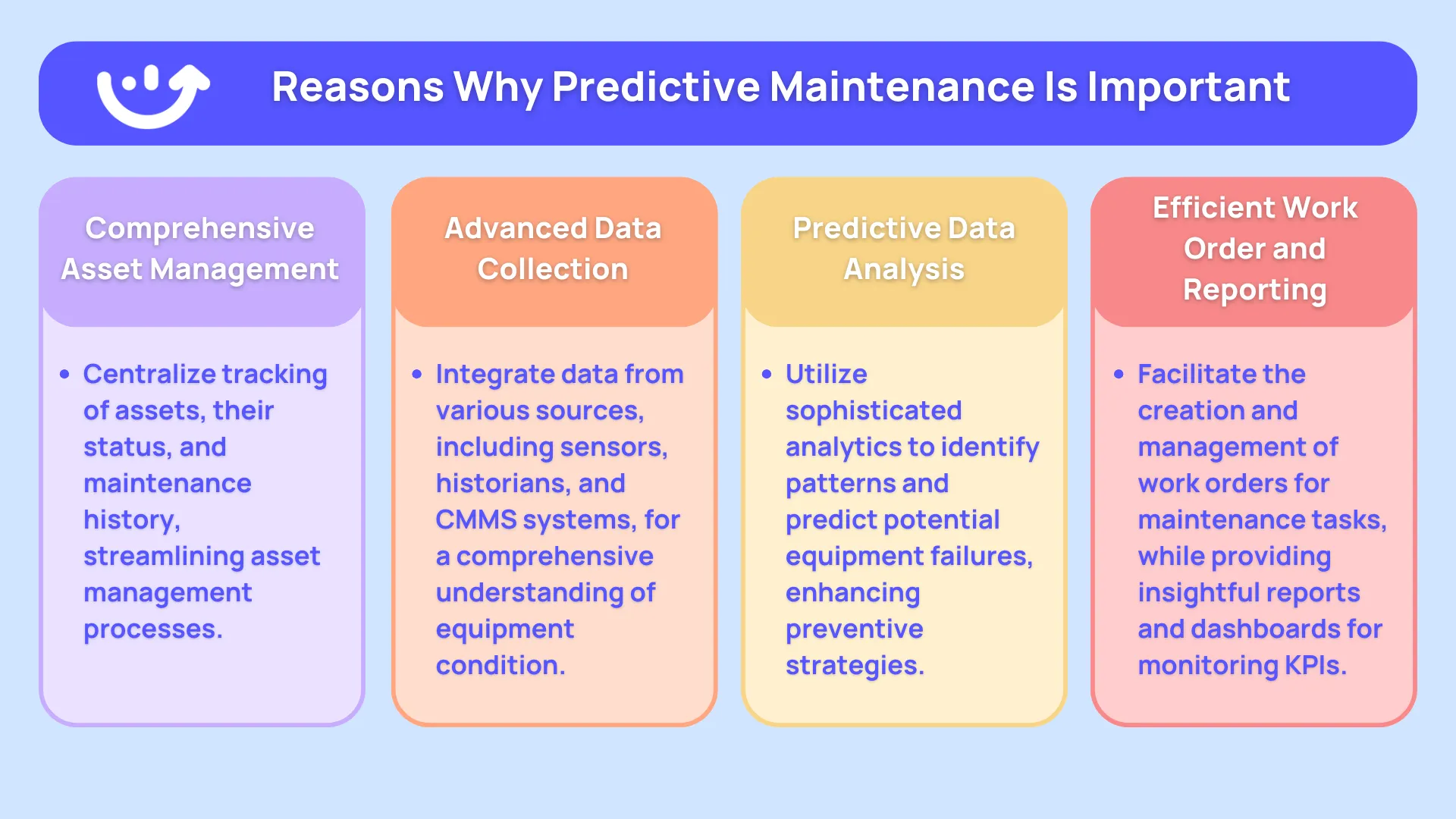
When it comes to asset management, preventive maintenance provides various benefits:
- Asset Management: Keep track of your assets, their status, and maintenance history in one place.
- Data Collection: Gather data from multiple sources, such as sensors, historians, and CMMS systems, to ensure you have a thorough understanding of your equipment.
- Data Analysis: It employs sophisticated analytics to uncover patterns and trends in your data, allowing you to forecast equipment breakdowns precisely.
- Work Order Management: Create and manage work orders for both preventative and corrective maintenance operations efficiently.
- Reporting and Dashboards: Create informative reports and dashboards to display data and track Key Performance Indicators (KPIs).
Impact of Predictive Maintenance on Different Industries
1. Manufacturing
Process digitalization and industrial automation, enabled by Industry 4.0, offer producers vast volumes of data as well as real-time monitoring capabilities.
Innovative vendors create manufacturing predictive maintenance software that works well with factory execution systems (MES) and other production tools by using real-time data from the Internet of Things (IoT) and advanced analytics.
According to McKinsey, machine breakdowns account for around 15% of all downtimes for pharmaceutical producers.
However, our client data reveals that equipment failures might account for up to 25% of downtime in the pharmaceutical business. In contrast, in some sectors, equipment failures may account for more than 25% of downtime.
As a result, floor supervisors can assess production machine performance and discover irregularities rapidly. This minimizes inefficiencies in the plant and allows for better maintenance planning.
Furthermore, PdM schedules maintenance tasks during non-working hours, which greatly reduces anticipated maintenance losses.
2. Automotive
Automotive manufacturers use condition-based maintenance in factories and after-sales cars.
PdM systems in manufacturing facilities aggregate data from several operations to give insights on asset lifespan and recommend maintenance tasks.
This significantly decreases planning delays and improves maintenance planning, resulting in fewer unplanned downtimes.
Furthermore, reliable asset defect prediction enables floor managers to avert safety events and guarantee worker safety.
3. Construction
Construction activities include the use of costly heavy equipment and the production of materials.
As a result, asset or production downtime results in substantial capital loss and postpones project completion. To identify issues, PdM continually monitors construction plant characteristics such as vibration and temperature.
This gives project managers the decision assistance they need to make alternate arrangements or better schedule maintenance tasks to prevent downtimes.
Furthermore, cement manufacturers and prefabricators use PdM to extend the life of their assets within manufacturing facilities.
4. Logistics
Unlike other businesses, the logistics industry has a considerable number of scattered assets, such as transportation trucks and distribution facilities in distant places.
This complicates asset health monitoring and maintenance. Integrating PdM and IoT across logistics assets, on the other hand, enables firms to manage their warehouses, fleets better, and material handling systems.
PdM-powered maintenance planning, for example, lowers downtimes of material handling equipment in the logistics value chain. It also assists fleet operators in recognizing vehicle faults and better planning vehicle maintenance. This helps drivers to schedule maintenance breaks rather than searching for repair shops when their cars break down.
FAQs
What is predictive maintenance software?
Predictive maintenance software is a program that predicts when machinery or equipment will fail, enabling businesses to repair them before issues arise. It's like knowing when your automobile needs to be serviced before it breaks down.
What are the three types of predictive maintenance?
Predictive maintenance is classified into three types:
- Vibration Analysis: It examines machine vibrations to find possible problems.
- Infrared Thermography: This technology utilizes heat to diagnose electrical system faults.
- Oil Analysis: It examines the state of oils and lubricants in order to detect machine problems.
What are the technologies used in predictive maintenance?
Predictive maintenance collects and interprets data from equipment using technologies such as sensors, data processing, and Artificial Intelligence (AI).
It's as if you have sophisticated sensors that warn you when anything is going to go awry.
Bottomline
In conclusion, the best predictive maintenance software is an essential instrument for businesses trying to improve their operations and decrease downtime.
You can make a smart decision and choose the best predictive maintenance software for your unique requirements by studying the features and comparing the leading solutions such as Xenia, Uptake, eMaint, PMXpert, and Oracle IoT Service Monitoring for Connected Assets Cloud.
Invest time in research; think about your specific needs, and keep in mind that the proper option may result in significant savings and better efficiency.
.webp)
%201%20(1).webp)