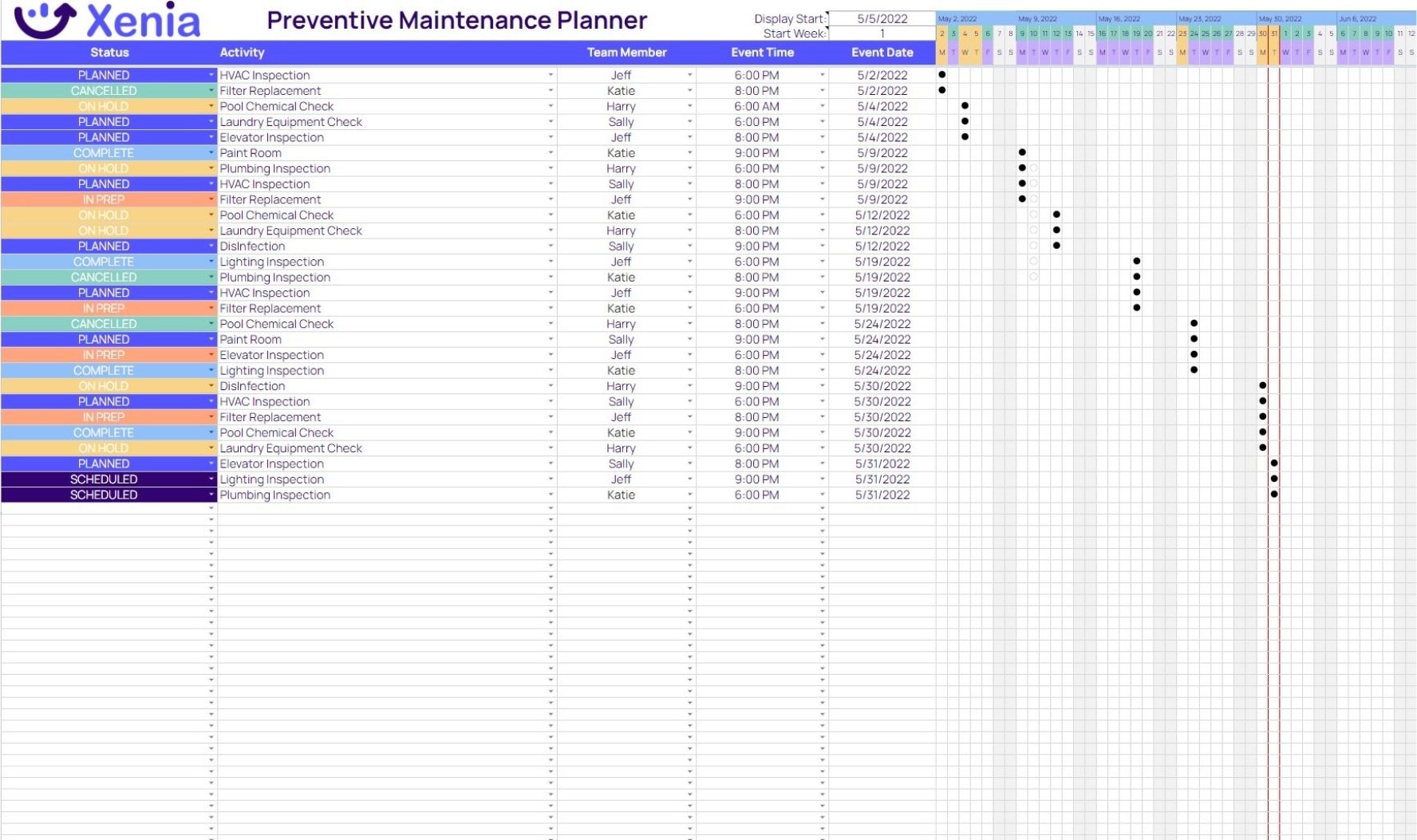
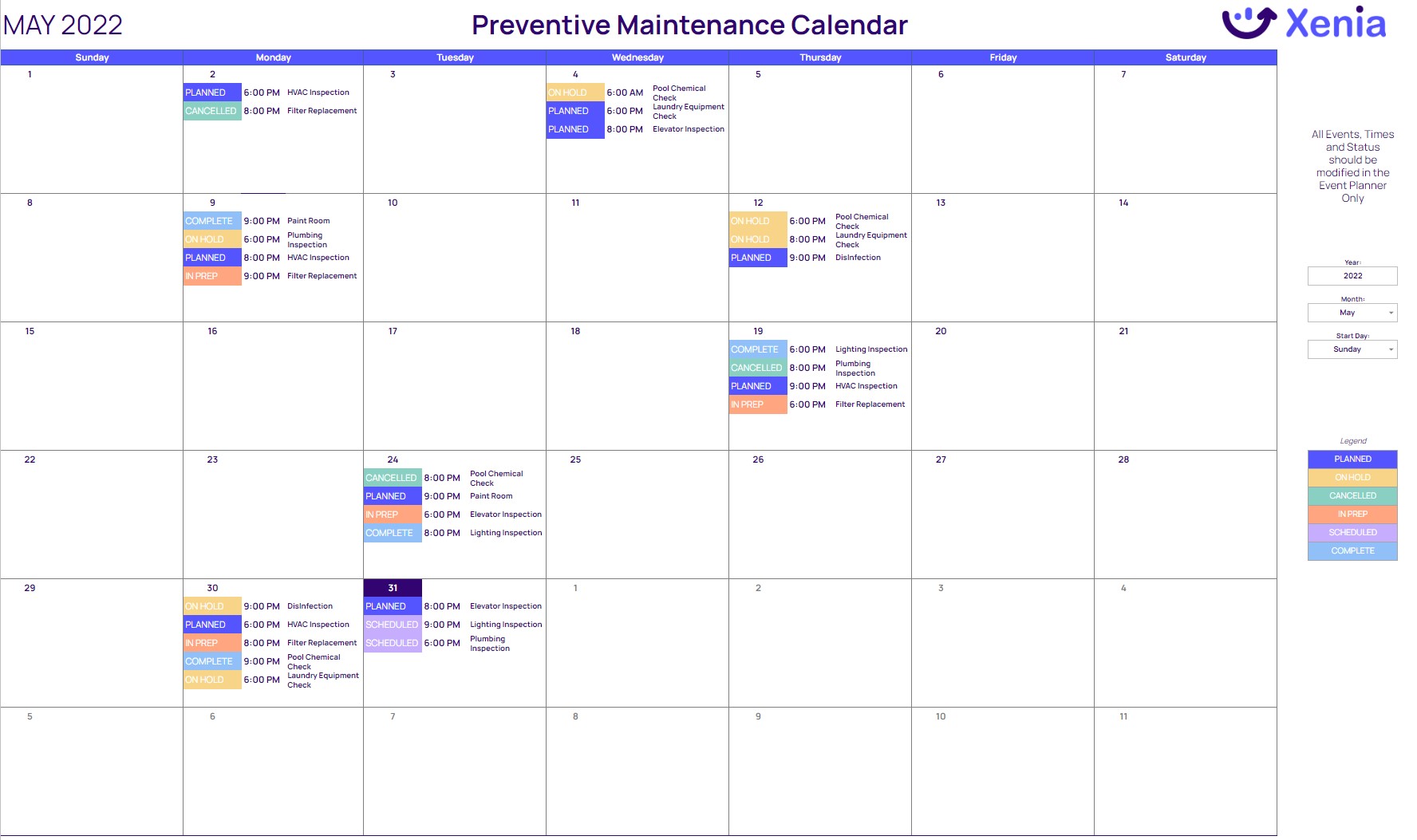
What is a preventive maintenance calendar?
A preventive maintenance calendar is a tool that allows you to keep track of when certain tasks need to be completed in order to prevent breakdowns and malfunctions. It's important, because if you don't have a calendar, you won't know when your car's oil needs changing or when your water heater stops working.
The best use for a preventive maintenance calendar is for businesses that need to regularly perform regular maintenance on their equipment. This includes restaurants, hotels, property managers, factories, and any other industry where there's a lot of equipment that needs regular upkeep to keep running smoothly.
To make preventive maintenance a breeze, Xenia provides a free Google Sheet based calendar tool to track operations. For a more comprehensive, mobile-friendly solution, start your free trial of Xenia today!
Recommended Resources:
- Best Facility Maintenance Software That Every Manager Should Try!
- Best Task Management Software For Optimal Team Performance
- Preventive Maintenance Software For Facilities & Businesses
- 8 Best Building Maintenance App(s) In 2024
What is a Preventive Maintenance Schedule?
A preventive maintenance schedule is a strategy for categorizing company resources to make sure that maintenance tasks are performed at specific times and usage. The main objective of preventive maintenance is to retain assets in the best working condition.
A preventive maintenance schedule includes material, equipment, and timeframes for finishing off tasks. It also ensures task order management which means who should perform which tasks and how they should do them.
Developing preventive maintenance is the responsibility of maintenance schedulers, maintenance supervisors, and maintenance planners.
People often confuse maintenance scheduling with maintenance planning. Although both processes support one another, they aren’t always completed by the same person.
Maintenance planning concentrates on what needs to be done and how. On the other hand, maintenance scheduling tells who will perform the required maintenance tasks and when.
How to Create Preventive Maintenance Schedule Format?
Below are some steps to follow if you want to create an accurate preventive maintenance schedule format.
Step 1: Prioritize assets based on criticality
You can start creating a preventive maintenance schedule for one or two assets, and then use the results to tell your strategy for others. Starting with multiple assets can be overwhelming, especially if your business contains thousands of assets.
Developing a PM schedule for just one or two assets is not only easy, but it will help you find out what is performing and what could be improved when you create PM schedules for other assets.
A critical asset should be prioritized and broken down as you come up with a preventive maintenance strategy.
Step 2: Gather information on critical assets to determine their maintenance needs
After selecting one or two critical assets in mind, collect information to specify their maintenance needs. Keep time-based and usage-based maintenance in mind when collecting assets.
A time-based PM schedule means scheduling maintenance tasks based on the time of their last occurrence. While usage-based preventive maintenance can also be known as predictive maintenance.
It involves scheduling maintenance tasks based on real-time usage data from gear sensors. You can measure usage in hours, kilometers, temperature, and flow.
If you’re confused about whether to choose a time- or usage-based PM schedule, start with time-based. And, if you feel like you’re over-maintaining, switch to usage-based.
Preventive maintenance software allows both types of schedules because you can set reminders to inform your team once an asset has reached a certain time or usage between maintenance tasks.
After determining your maintenance needs, as well as whether you need to make time-based or usage-based PM schedules, you can plan short-term and long-term tasks for each asset.
Step 3: Plan long-term tasks for each critical asset
Long-term preventive maintenance tasks consist of routine maintenance. It is necessary to perform sometimes in a week, but not every day. Long-term preventive maintenance will vary according to the needs of each asset, Below are some examples of long-term PM tasks;
- Inspections
- Oil and air filter changes
- Chain, and belt adjustments
- Greasing & lubrication
- Part replacement and/or repair
After narrowing down which maintenance tasks you’d like to schedule over the coming weeks, you can focus on more short-term tasks.
Step 4: Plan short-term tasks for each critical asset
Short-term preventive maintenance tasks are the ones your team will perform on a more regular basis such as every day or every week. They’re the ones that if you don't perform them on time they will have more severe consequences.
For example, a substantial change in temperature or air pressure should probably be dealt with urgently, while an oil or air filter change can wait unless there are clues of a huge problem.
Similarly, cleaning spare parts of tools becomes a huge task if it’s postponed, unlike an inspection, which takes the same amount of work no matter if it's performed.
Here are some examples of short-term preventive maintenance tasks:
- Cleaning
- Record measurements such as pressure and temperature
- Verify that parts are working properly
Step 5: Train workers on your preventive maintenance schedule to ensure a smooth transition
After planning maintenance tasks for your most critical assets, it’s important to teach your crew about their tasks and duties.
It's important to make sure that each team member understands what they’re accountable for and how to conduct each preventive maintenance task accurately.
Along with notifying your team when maintenance needs to be performed, preventive maintenance software like Xenia can help you schedule and assign preventive maintenance tasks, track asset versions, and submit a work order for equipment repair if any reactive maintenance is needed.
You can also get an accessible mobile version of your preventive maintenance checklist for each asset.
Along with training your squad on their maintenance duties, ensure they know how to use any software platform you select to improve your maintenance program.
Preventive Maintenance Schedule Examples
A maintenance team often applies preventive maintenance. The best maintenance programs endure a proactive approach in which 60% of all maintenance activity is preventive.
An excellent maintenance program shows your ambition towards planning, implementation, and evaluation of your business. It helps companies improve their quality and outcome, increase equipment uptime and Overall Equipment Effectiveness (OEE), reduce costs, and more.
- Tools & Kits Inspections:
Regular machine inspections are one of the most typical preventive maintenance examples. Maintenance teams often perform calendar-based examinations of critical machines. These frequent inspections secure the facility and keep it running.
- Equipment Cleaning:
Mechanical systems don’t do well due to dust and dirt accumulation. As pollutants build up, it creates friction and starts damaging machine components. Maintenance teams often clean these impurities to avoid any issues.
- Lubricate Parts:
Lubricants are crucial for keeping machine parts moving. Less or no lubrication can damage gear and lead to destruction. Making sure that regular lubrication is one of the best preventive maintenance examples for keeping machines in the right condition.
Preventive Maintenance Calendar Templates are also available online. At Xenia, you can find preventive maintenance checklists:
1- HVAC Preventive Maintenance Checklist
2- Cctv Preventive Maintenance Checklist
3- Sauna Preventive Maintenance Checklist
4- Boiler Preventive Maintenance Checklist
5- Chiller Preventive Maintenance Checklist
What is Preventive Maintenance Compliance?
Preventive maintenance compliance (PMC) is a maintenance metric and KPI that expresses how many scheduled preventive maintenance tasks have been completed over a certain period. It measures the usefulness of PM programs and demonstrates how well PM schedules are being followed. Thus, it is a very important metric in improving a factory’s maintenance practices.