When it comes to mastering maintenance, the key is to balance proactive maintenance budgets to minimize the financial impact, frequency and duration of reactive maintenance events.
In this post, we will discuss proactive maintenance, its types, examples, and tips for preparing a budget for your facility.
Priced on per user or per location basis
Available on iOS, Android and Web
If you are looking to learn more about maintenance management, visit our guide on Work Order Management.
What is proactive maintenance?
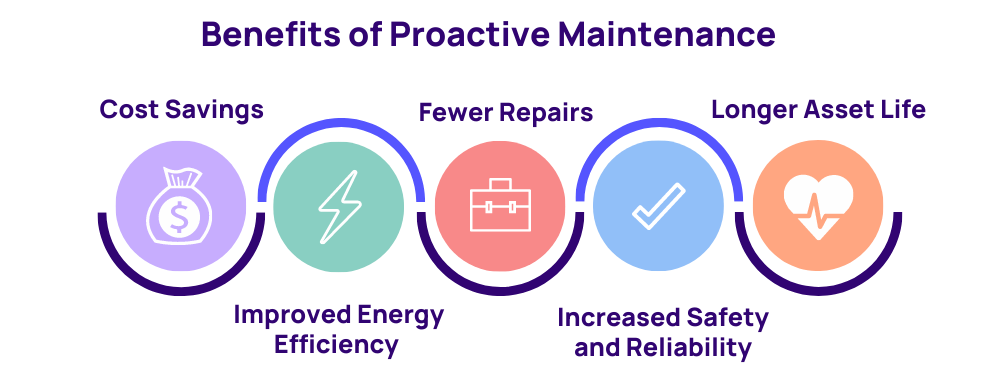
Proactive maintenance, also known as preventive maintenance, aims to recognize the fundamental cause of equipment failures and rectify them before they cause major issues.
For a comprehensive approach to this, exploring maintenance management software can provide the tools needed to effectively implement these strategies.
Proactive maintenance can be contrasted with reactive maintenance in that proactive occurs before a breakdown whereas reactive is to correct the cause of the breakdown. In most cases, reactive maintenance caries a higher cost and operational impact to facilities.
However, some proactive maintenance can be expensive, so managers need to find the balance between maintaining a healthy asset inventory and balancing the budget.
To accomplish this balance, managers should develop a proactive maintenance strategy, consisting of processes that will help you find any hidden inefficiencies, improve asset reliability and workplace safety. Let's look at a few different types of proactive maintenance.
Recommended Resources:
- Maintenance Management Software
- 10 Best CMMS Software For Small Business In 2024
- 8 Best Building Maintenance App(s) In 2024
- Preventive Maintenance Software
3 Types of Proactive Maintenance
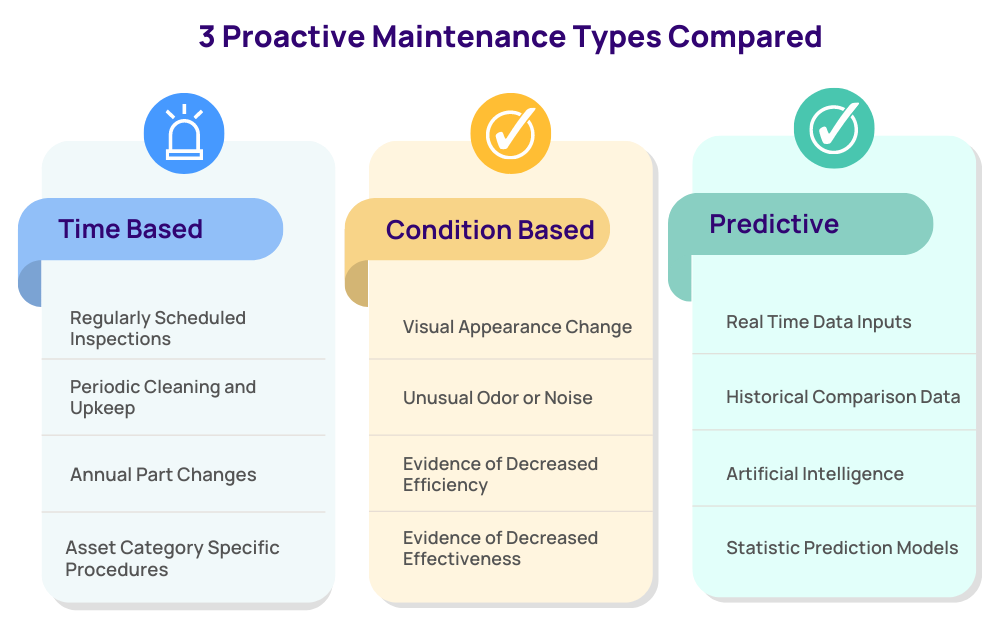
👷🏽 Time-Based Maintenance
Time Based maintenance is regularly scheduled maintenance to prevent unexpected failures in the future. Each asset type has distinct preventive maintenance protocol to be conducted at regularly scheduled time cadences.
For example, a boiler in a hotel may have monthly, quarterly and annual preventive maintenance processes to ensure reliable operations. Through time-based preventive maintenance, engineers can enhance the asset efficiency and decrease down-time risk for business operations.
Assets tend to become less efficient and effective over time, especially when they are not taken care of properly. For example, the engine health in a car is largely influenced by the frequency of oil changes.
Engines with proper lubrication deliver better fuel efficiency and are more reliable for the driver.
Just as with the car, performing preventive maintenance will help you save energy, increase the asset life, and reduce unplanned downtime.
🔧 Condition-based Maintenance
Condition-based maintenance (CBM) is when technicians monitor condition of equipment to decide what maintenance is needed. This can be done manually or through sensor devices to collect real-time measurements on equipment pieces. CBM data isn't necessarily predictive, but can be used to make value based decisions on maintenance needs.
In addition, condition based maintenance is used to correct issues that are not yet causing functional risk, but are aesthetically or otherwise unappealing. Examples such as dents and paint chipping can be corrected with condition-based maintenance.
Other examples of condition-based maintenance include:
- Vibration analysis
- Infrared thermography
- Oil analysis
- Ultrasonic analysis
- Pressure testing
📈 Predictive Maintenance
Predictive maintenance uses data analysis tools to detect irregularities in your operations and defects in your process so you can fix them before they become a problem. It uses real-time and historical data from various parts to predict any possible issues.
The overall goal of predictive maintenance is to minimize unnecessary upkeep so that budget can be focused on when downtime is imminent. Incorporating preventive maintenance software into this strategy can significantly enhance the effectiveness of your maintenance operations by using data analysis tools for early detection and action.
Predictive maintenance is difficult to achieve in the current environment due to lack of consistent data points. New equipment may come with built-in health monitoring that helps managers succeed in predictive maintenance.
With the emergence of Internet of Things (IOT) technology, predictive maintenance will become more implementable and relevant. By connecting hardware monitors to existing equipment, managers can collect regular performance readings and artificial intelligence can provide insights into when and where to conduct maintenance.
The future is bright for maintenance processes due to predictive technologies.
Proactive Maintenance vs Reactive Maintenance
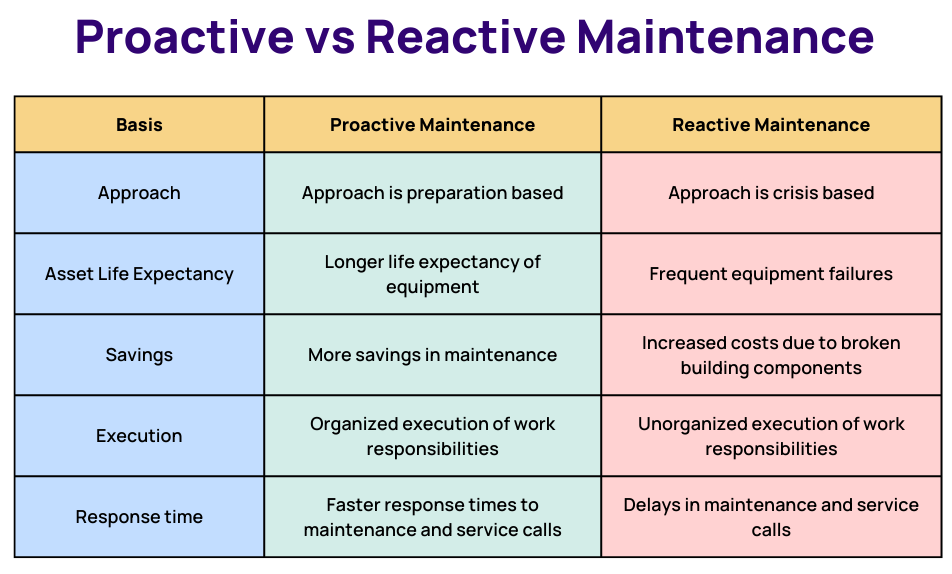
Predictive and Proactive Maintenance
Proactive Maintenance:
Proactive maintenance uses data, often operated on computerized maintenance management system (CMMS) software, to determine the hidden cause of faulty kits and tools.
Small and medium-sized businesses can benefit greatly from implementing CMMS for SMBs, which are designed to fit the unique needs and budget constraints of smaller operations.
Proactive maintenance helps to reduce your overall machine and repair costs and expand the life of your tools by addressing problems before they arise.
If proactive maintenance is done correctly, repairs can be limited. It happens when you aggressively track all key performance indicators (KPIs) at all times.
The proactive maintenance methodology assures that you’re conducting routine maintenance only when it’s necessary. This approach helps you collect data that can reveal trends and provide performance-based metrics on an ongoing basis through a web-based system, probably a CMMS that is available to your entire crew.
The main goal of proactive maintenance is to decrease downtime so you can avail the most out of your gear for as long as possible. Proactive maintenance eliminates the need for expensive and time-consuming restorations.
Predictive Maintenance
Predictive maintenance uses condition monitoring to examine the current shape of your tools and perform online maintenance before any problem arises in your machine.
Predicting the future seems like a fool’s chore, but in terms of facilities management, predictive maintenance makes your work easier and more effective than ever.
The goal is to reduce expenses and snuff out downtime caused by unforeseen machine maintenance. So instead of reacting to unexpected events, you’ll be able to maintain a proper plan, eliminating downtime costs. It will also help you in providing more data to your maintenance team, so they can prepare a diagnosis and begin addressing problems quickly.
One of the most remarkable aspects of predictive maintenance is its power to effectively pre-empt and avert potential issues, allowing crucial work to be performed on machines while you are still online, instead of when rendered inoperable.
Predictive and proactive maintenance seem alike, but the truth is they’re very much different.
While proactive maintenance tries to get to the root cause of a potential crisis, predictive maintenance compiles relevant data to appropriately plan daily fixes to make sure that equipment is operating correctly.
However, both are excellent processes in terms of cost, especially when something goes too bad. Gear and tools that tarnish over time not only cost you financially but also cause serious safety risks.
These techniques hold great importance, especially when you believe that maintenance and equipment deterioration are the main reasons for unplanned downtime, outages, and cybersecurity threats.
With the advancement in technology, various software can help you enhance efficiencies, save money, and improve safety in maintenance.
Work Orders in Proactive Maintenance
Using paper and pen is the oldest method for managing proactive or preventive maintenance work orders which is the least efficient and effective way. Hundreds of businesses are still relying on maintenance work order files, binders, and clipboards every day. Transitioning to digital means through work order software can revolutionize how these tasks are assigned, tracked, and managed, increasing efficiency and transparency across the board.
For “old school” maintenance supervisors, this may be the only way to assemble your maintenance data. But there are better ways like using work order management software.
We want to help out, that’s why Xenia is offering maintenance work order forms, that are efficient, detailed, and easy to use. Assigning work orders using software takes seconds and can be allocated based on category, location, priority level, start, and due times.
Work orders can be assigned as recurring tasks to enable quick preventive maintenance scheduling and regular safety inspections.
Proactive Order Status & Work Order Progress Tracking
Maintenance work order software enables managers to keep tight supervision of operations no matter where they are located. When work orders are assigned, the correct employee is notified via their mobile device. Once they start work, the manager can see the proactive order status and proactive track order.
The manager can monitor the checklist progress and view images from the frontline in real-time. If there are questions, the employee can chat with team members or management within the work order itself, providing an exceptional level of collaboration, detail, and transparency.
Example of Proactive Maintenance in the Hospitality Industry
Hotels constantly have guests checking in and out, and the buzzing lobby filled with guests also brings the responsibility of ensuring hotel maintenance meets guests' expectations.
Most think maintenance is expensive, but they can cut overall expenses by safeguarding hotel assets such as supplies and equipment. Here are the top areas to focus on for your hotel:
🌡️ Heating and cooling systems
Routine checks and maintenance of the hotel's chiller and boiler systems are essential for guests' comfort. Dirty or worn-out filters, HVAC leaks, and blocked heat ducts can mess up your hotel's budget with last-minute repairs.
💡Lighting and Electrical Systems
Electrical issues can cause sudden power outages causing inconvenience to your guests and staff. Consistently checking plugs, wires, and circuit breakers can prevent major last-minute electrical problems.
🪠Plumbing and water supply
Water issues can make a deep hole in your pocket. Avoid it by consistently checking rusty pipes, cracked tiles, toilet malfunctions, and water damage to ceilings and floors. Ensure there are unclogged drains, sinks and tubs are leak-free.
⏰Alarms and Safety Equipment
Guest safety should be your priority. Ensure everything works properly, including sprinkler systems, smoke detectors, and carbon monoxide detectors. Locks on the door to the washrooms, bedrooms, conference rooms, and other hotel areas.
4 Proactive Maintenance Budgeting Tips
The allocation of maintenance budget is not the same for every business and must be personalized to the condition of assets. When creating a maintenance budget for the first time, there are a few elements you need to consider.
🚨 Set aside the budget for emergencies
Proactive maintenance can help you avoid downtime and keep your assets healthy.
So you must allocate a considerable portion of your budget for proactive work. While it can look like a hefty expenditure for a moment, it will benefit you in the long run. But there will inevitably be instances where you'll need reactive maintenance, which tends to be more expensive and time-sensitive.
To avoid exceeding your budget, set aside a portion for such emergencies. A study by Stanford University found the cumulative cost of maintaining and operating its assets rose as the buildings aged.
For this reason, the reactive maintenance budget amount should depend upon your overall equipment age, usage and breakdown history. This amount should increase over time as the likelihood of failure increases.
📚 Analyze spending from last 3 years
The best way to understand future maintenance costs is to take a look back at your budgets from past 3 years. How much of the overall budget was allocated to maintenance? Was there any money left over at the end of the year? Were there issues that could have been prevented with a more comprehensive maintenance protocol? Answering questions like these will help you to anticipate your future expenses and learn from past mistakes.
❄️ Take seasonal maintenance needs into account
Each season comes with unique needs, so you must keep seasonal factors in mind while preparing the budget. If you are located in areas with harsh winters—you need to set aside a portion for snow and ice removal, heating system equipment, and any power losses. You also need to consider the risk of increased costs due to tightened technician and parts supply in high issue months.
Plan the required summer and winter measures before the seasons arrive. Use the mild spring and fall months to execute preventive maintenance. Make sure to plan for any emergencies during such extensive seasons.
💸 Identify and budget for hidden costs
Hidden or underground costs are easily overlooked, and you might not expect them. So if you ignore such costs you can expect your budget to fall off easily. For example, you may need to pay for software licenses, or the invoices can come with additional processing fees. Another example is supply chain bottlenecks and inflation costs. Without factoring this into your maintenance budget, you will likely be under predicting costs.
Free Checklists to Standardize Proactive Maintenance
Gone are the days when you used to keep a physical record of every process and update them from scratch now and then. With digital checklists, you can create your custom lists, record their usage and analytics across teams. Equipment failure can lead to unplanned downtime and affect your organization's productivity. Prevent this by creating a proactive maintenance checklist.
According to Plant Engineering 74% of CMMS users believe that this tool improves productivity, while 58% consider it cost-effective in general. Furthermore, 57% of users see its ease of use as an advantage.
Preventive Maintenance Checklists include all tasks your staff need to complete, so they know the exact process they need to follow regarding maintenance. Checklists make it easier for technicians to understand everything, and they complete tasks faster and track asset condition over time.
FAQs - Proactive Maintenance
What is the meaning of a proactive approach?
The proactive approach attempts to understand a system even before it fails (unacceptable quality) to identify how it could fail. Measures can then be put in place to prevent the failure or failures that have been anticipated.
What’s the definition of Proactive Maintenance?
Proactive maintenance is a maintenance strategy that aims to identify and fix the reasons for equipment failure before it happens. The goal of proactive maintenance is to increase asset reliability and reduce the risk of downtime.
Who is a proactive learner?
Proactive learners are like explorers on a quest for knowledge. A proactive learner in maintenance refers to a person who works hard for the upkeep of the proactive maintenance solution. The proactive learner approach indicates your loyalty and seriousness to the system.
What is a proactive maintenance solution?
Proactive maintenance solutions are software that can be used to predict potential issues and determine significant improvements that prevent a recurrence.
.webp)
%201%20(1).webp)