A facility condition assessment is a critical aspect of a preventive maintenance strategy. Not only is it essential to prepare a budget around facility costs, but facility codes and regulations must also be upheld.
According to a recent CBRE report, external factors are reshaping facilities management costs like never before. Inflation, rising energy costs, and a tight labor market are among these factors.
For many business owners, this is crunch time and neglecting your facility maintenance is not an option. When facilities are poorly maintained, it can affect the customer’s experience.
Priced on per user or per location basis
Available on iOS, Android and Web
If your facility is falling apart around you, or if it needs to be cleaner for your customers, you risk losing business. Even if you don't have any safety issues right now, remember that your equipment will only last so long before it needs to be replaced—and if maintenance is suffering due to budget concerns, new equipment is not an option.
Then there are all the compliance issues: if your equipment isn't up to code, it could cause problems with regulations and inspections. Ignoring this maintenance will make it challenging and expensive to comply with industry standards.
What is Facility Assessment or Facility Condition Assessment?
A facility condition assessment (FCA) is a checklist of items used to determine a facility's condition. It's a way to identify and address risks, which can help you prevent future problems.
FCAs can be used for preventive maintenance purposes or inspections after an incident has occurred. They can also be used as part of an environmental audit or a more effective risk management plan.
Professionals with experience in construction, facilities management, and maintenance of buildings will complete a facility condition assessment. They use their expertise to determine the condition of your building assets, including mechanical systems, electrical systems, plumbing systems, structural components, and more.
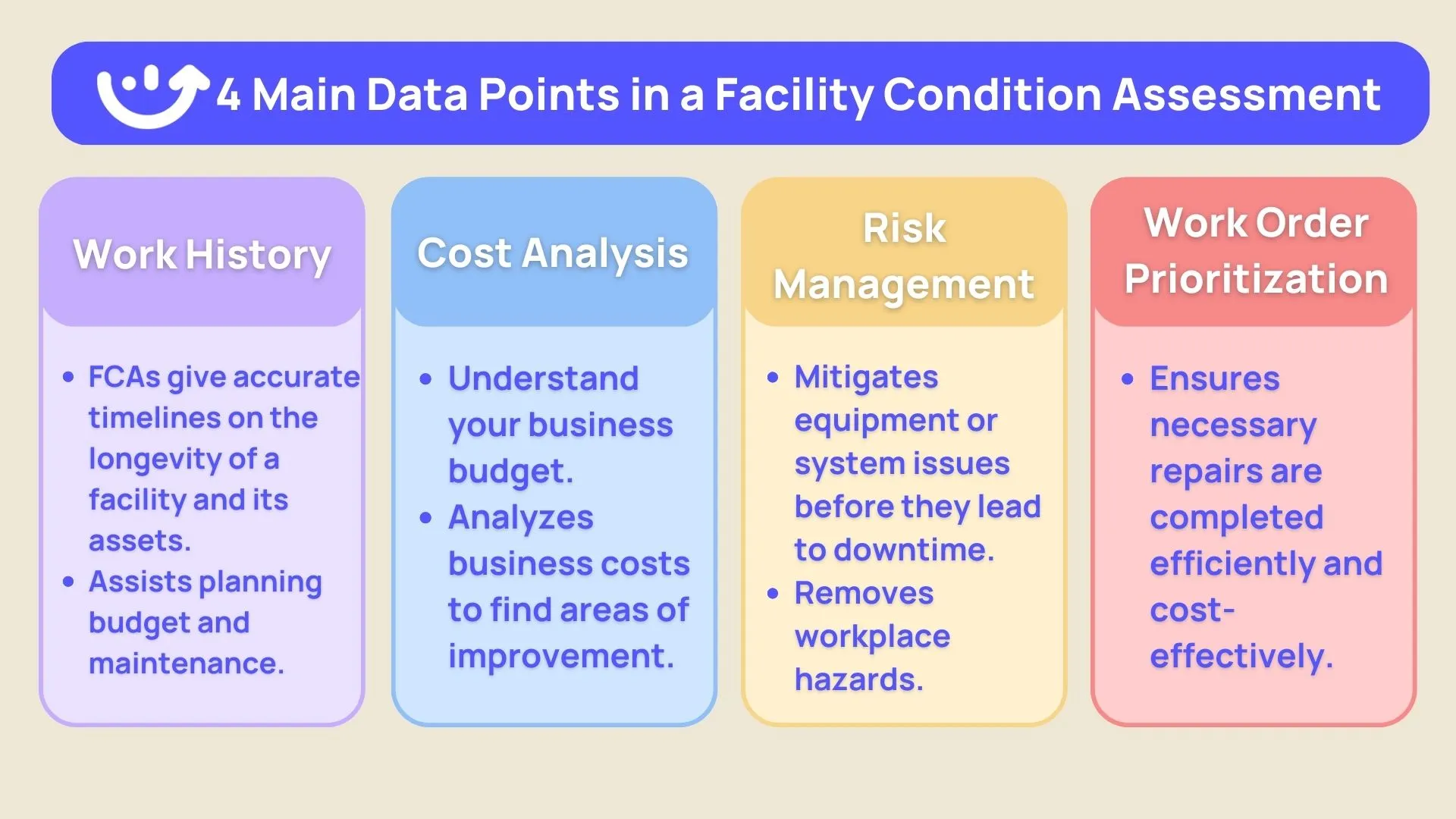
When taking a new maintenance management position, a facility condition assessment will establish a baseline and get a clear picture of the current state of your building. Streamline this process to your employee directory through Computerized Management Maintenance Systems (CMMS) software.
CMMS will provide them with the tools for facility managers to collect and monitor data on the facility's condition. Then you can use that data to make informed decisions about which repairs need to be made. CMMS can help facilities managers prioritize work orders, track their progress, and manage all relevant data in one place.
Recommended Resources:
- Facility Maintenance Software
- 5 Best Building Maintenance Management Software In 2024
- 8 Best Facility Inspection Software in 2024: Features & Pricing
- Preventive Maintenance Software
- 7 Best Document Management SOP Apps In 2024
Why Is Facility Condition Assessment Important?
Facilities are the backbone of your business. A facility condition assessment will help you maintain them, so they can continue to serve you well for years to come.
An FCA gives you accurate data about multiple pain points, including:
📜 Work History
You'll want to get information on the age and use of the facilities—and how much longer it could last before breaking down completely—and what kind of work needs to be done on those parts to keep them functioning at optimal levels.
This information will allow you to plan budgets more effectively and know exactly how much money should be allotted each year toward maintaining your building's health and longevity.
💰 Cost Analysis
An FCA is the first step to understanding your building facility costs. This involves looking at all the costs associated with running a facility over time and seeing where there might be areas for improvement.
📉 Risk Management
It helps prevent injury, illness, or other hazards in your workplace by reducing facility failure. Mitigate potential equipment or system issues before they lead to a shutdown.
🛠️ Work Order Prioritization
Ensures that necessary repairs are completed most efficiently and cost-effectively as possible. It helps prevent unnecessary delays in obtaining new equipment or systems Scheduled care keeps the facility compliant with safety regulations.
This information is essential for future budgeting. It also helps with facility or equipment issues likely to pop up and cause unexpected downtime.
Four P’s of Facility Condition Assessment for Frontline Managers
As a frontline manager, you have a lot on your plate. You must protect your employees and the facility, perform the daily tasks of running a business, plan for future growth, and prepare for any emergency situations.
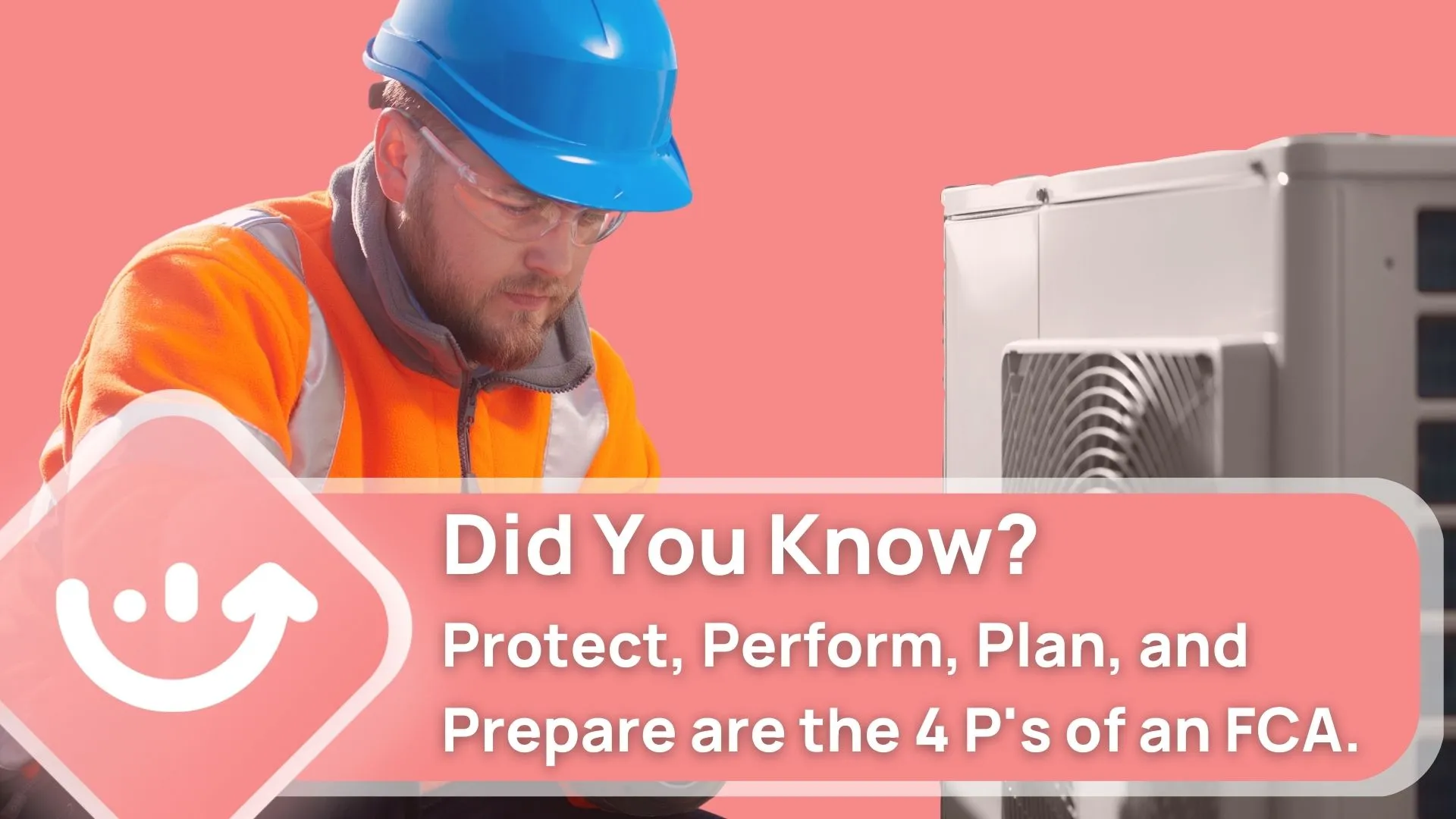
So how do you accomplish all of this? By following the four Ps of a facility condition assessment:
😷 Protect Staff and Customers
The first step in performing a facility condition assessment is identifying hazards and taking corrective action where needed. This will help protect your staff and customers from dangerous situations arising from poor building conditions.
Hazards might include:
- Ceiling leaks
- Cracked floors or walls
- Electrical problems
📅 Perform Preventive Maintenance
Performing regular maintenance checks on your equipment can help to improve its reliability and avoid problems before they happen. Utilize the FCA to create work orders for all of your facilities. This will help make more economical use of maintenance workers working on a schedule. It also reduces overtime costs.
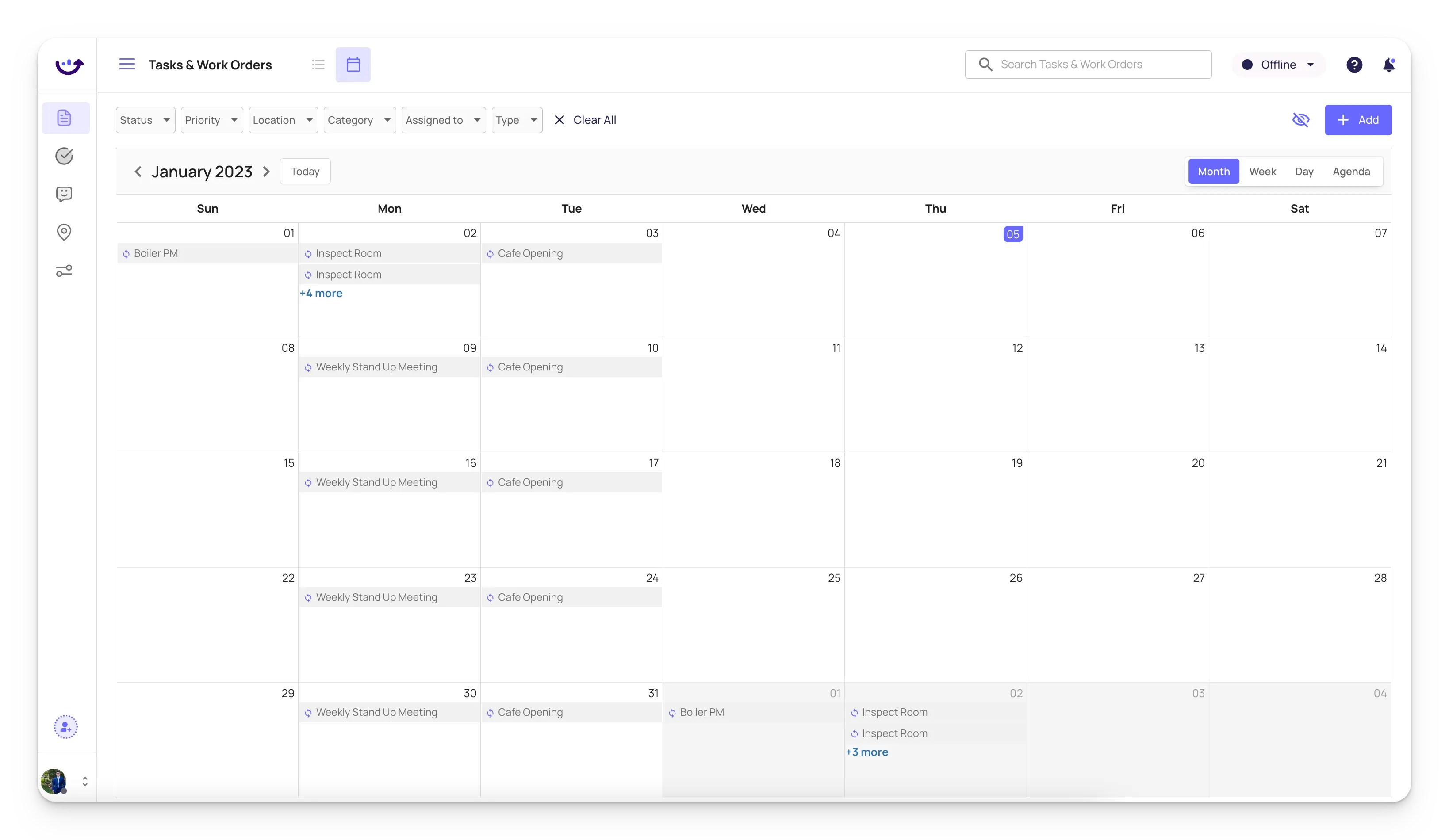
💵 Plan for Upcoming Expenses
An FCA helps prioritize repairs and maintenance based on their importance to safety, productivity, or regulatory compliance.
📊 Prepare Ongoing Maintenance Plan
Identify assets at the end of their life and create protocols for dealing with those assets. This is not just a one-time event—it's an ongoing process that allows you to maintain a state-of-the-art facility well-suited for your business.
How To Conduct Facility Condition Assessment?
When conducting a facility condition assessment, it's important to remember that there are many different types of facilities—from retail stores and restaurants to manufacturing plants and warehouses—and each type has its own unique needs. Each will also have its challenges regarding maintaining its structure and functionality.
As part of this process, it's essential to determine whether or not your building requires repairs or improvements in certain areas, such as upgrading electrical systems or replacing windows. This will focus your time and resources on improving things like energy efficiency or comfort levels in the workplace.
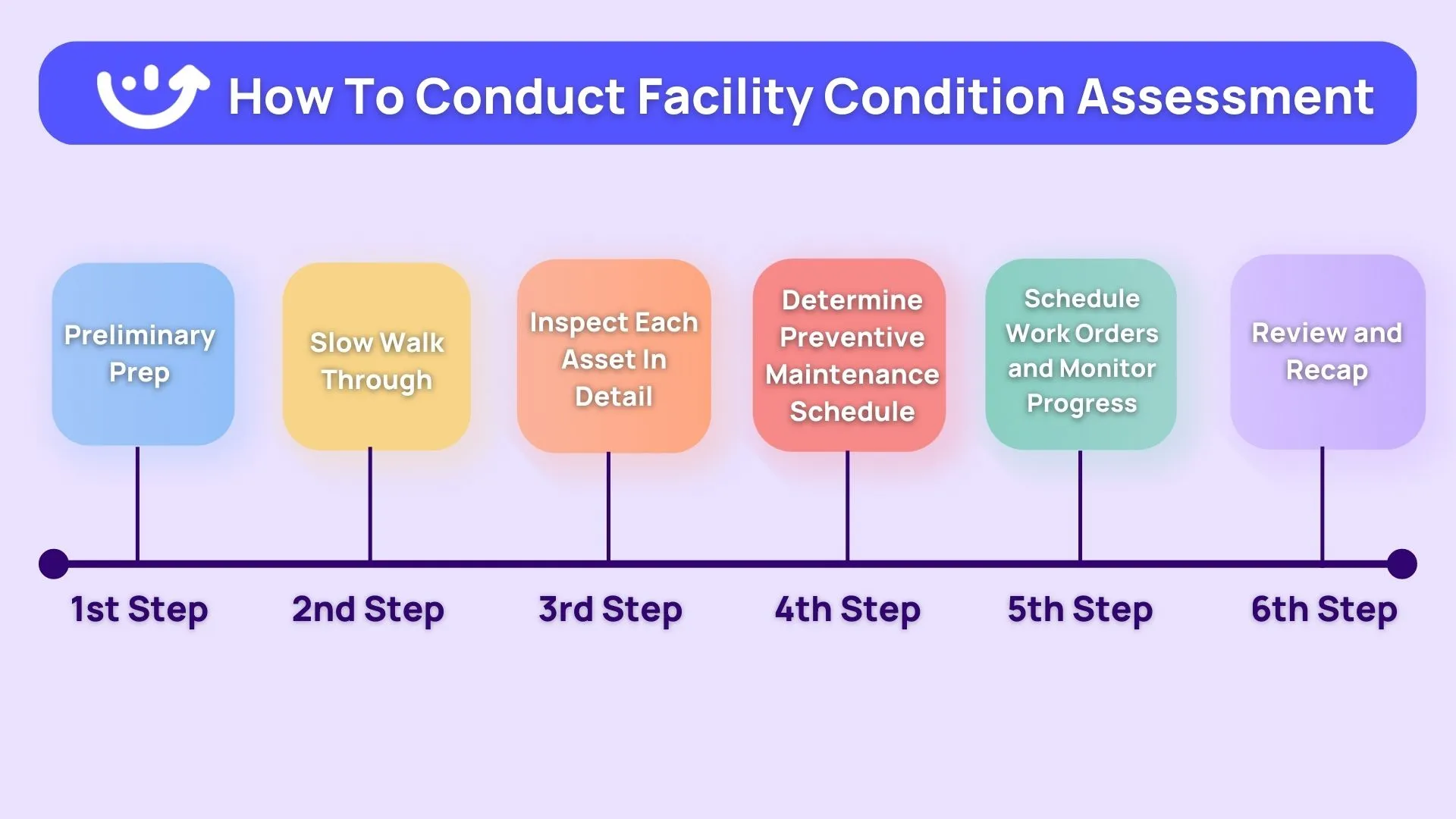
Keep that in mind when you follow these steps during a facility condition assessment:
🦺 Preliminary Prep
The first step to conducting a facility condition assessment is to get everything you need ready. To do this, you'll need the following:
- A map of the facility and its assets
- An inspection checklist shaped around your facility’s needs.
- A hazard log
👣 Slow Walk Through
- Once you have these materials, slowly walk through your facility, looking for hazards.
- Log your findings on a checklist. This will help ensure that when you create work orders for each hazard, it's all there in one place for easy reference later.
🤖 Inspect Each Asset in Detail
- Record images and notes on each asset. You want to remember all the details!
- Identify parts with wear or damage. If something needs replacing or repairs, you'll know exactly what it is.
- Estimate the remaining life for each asset so you can plan repair or replacement costs.
📅 Determine Preventive Maintenance Schedule
- An FCA will justify future capital expenditures and provide information necessary for effective long-term management decisions related to facility operations and maintenance policies.
💻 Schedule Work Orders and Monitor Progress
- Communicate with your employees by sending work orders, so we have all the information needed to complete your request as quickly and efficiently as possible.
- It will give you an overview of how your facilities are doing and help you identify areas where improvements could be made.
📊 Review and Recap
- Review data and make sure everything is up-to-date and ready for future use.
When To Perform a Facility Condition Assessment
It's easy to think of facility condition assessments as a necessary evil—you know you need one, but it feels like an enormous task and a waste of time. But the truth is that facility condition assessment are incredibly valuable for your business.
First, they can help you save money by allowing you to identify problems that need to be addressed before they become costly emergencies. Second, they will enable you to take proactive measures to keep your building in good shape.
Thirdly, facility condition assessments help ensure compliance with local codes and regulations.
If you're wondering when to perform a facility condition assessment, here are some answers:
When your building is new:
- Perform an FCA during the design phase of a new construction project. It helps ensure that the building will be built correctly, and it also gives you an opportunity to take into account any changes in your business or operations that might affect how you use the space.
When your building is old:
- If your building is at least ten years old—and perhaps even older than that – it's time for an FCA. You'll want to know what needs attention now to plan for those repairs in advance and avoid having them happen unexpectedly.
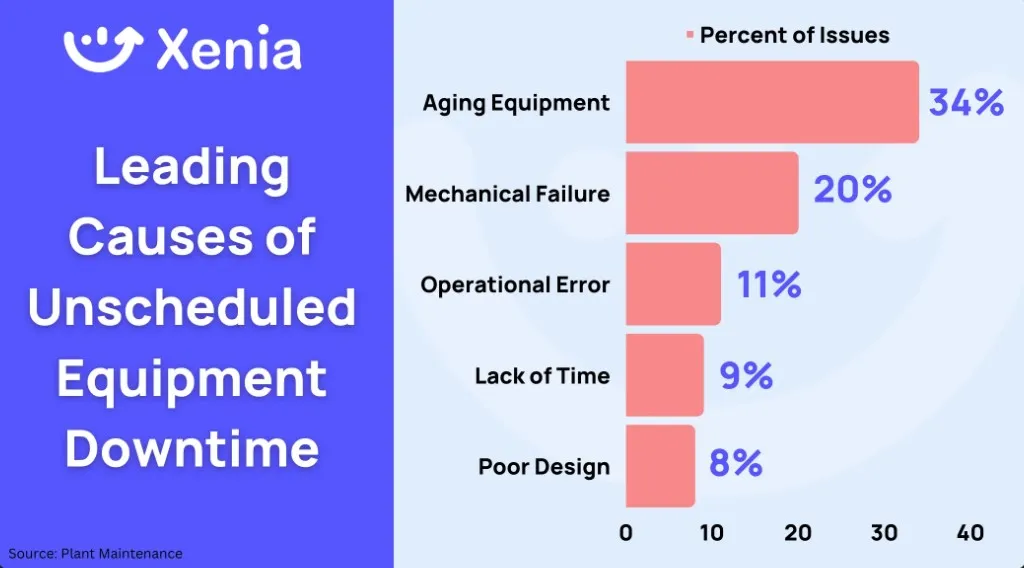
When you're ready to complete a facility condition assessment, it can take time to know where to start. But one way can make the whole process easier: using a CMMS.
A CMMS will help track all the equipment, machinery, facilities, and other assets your company owns or uses—and it'll do it in a way that makes sense for you and your team.
The beauty of using a CMMS is that it gives everyone involved in the maintenance process access to information about what's happening at any given time. It also helps eliminate some guesswork when it comes to making decisions about what needs fixing and why (or if).
.webp)
%201%20(1).webp)