The facility management industry is constantly developing, presenting several chances to improve the way we work and our businesses' bottom line. Facility managers play an important role in today's changing working environment since the most precious assets of an organization are the buildings, equipment, and people.
The job growth rate is expected to be around 10% between 2016 and 2026, according to the Bureau of Labor Statistics in the United States.
Professional facility management businesses operate in a variety of industries, including manufacturing, finance, technology, real estate, retail, and healthcare.
The noted upward trend of the job market reflects an increasing understanding of the practice’s importance in virtually any organization, as the need to optimally manage physical spaces, assets, and resources applies to all.
Facility management is the use of a set of procedures, rules, and services to coordinate the physical workplace with the people and work of the company it serves. This comprises asset management, operating norms and guidelines, maintenance, furniture provisioning, and other activities.
The notion of using facilities management software has gained popularity since it allows such companies to focus on their main strengths without having to worry about the management process.
Facility management is a demanding job that requires a variety of skills. Managers are in charge of a wide range of tasks at work and have different responsibilities to juggle. An FM's job description usually ranges from building maintenance, recruiting, and staff management, to data collection for decision-making purposes.
This guide is intended to simplify your job with the use of an integrated facility management system. It contains 17 best facility management software, 10 paid and 7 free.
We have researched, gathered, and analyzed procedures and techniques for managers looking to maximize their talent and reach their full potential.
Let’s start.
Priced on per user or per location basis
Available on iOS, Android and Web
Overview of Facility Management Solutions
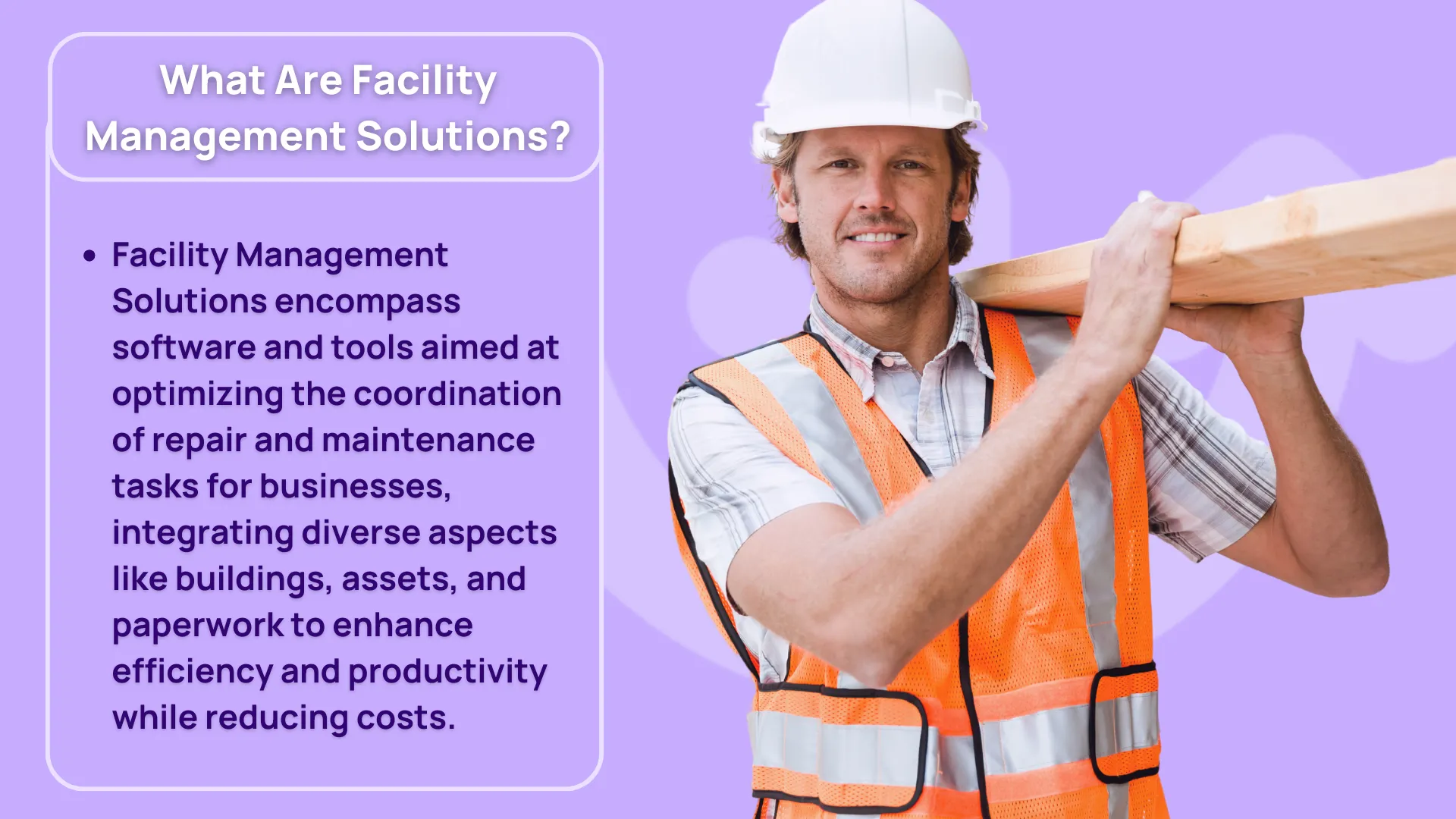
Companies utilize facility management tools to help streamline the coordination of all of their repair and maintenance activities.
This is where efficiency gets compounded and results get accelerated.
Facility management apps are also used to integrate various forms of facilities, such as buildings, spaces, assets, and all associated paperwork. The overall objective of this approach is that businesses want their facility management systems to reduce maintenance costs while improving revenue. This program also allows front offices to know when an apartment has been cleaned. On top of that, users can reserve items and create spaces all on the same platform.
How Facility Management Solutions Can Improve Operations
Asset management: By employing the right facility management platform, managers can ensure the systematic use of a company's assets to maximize value or return over time. This approach helps in optimal asset productivity, by doing more with the same asset base or achieving the same flow with fewer resources.
Compliance: Employing the right facility management strategies can be the most efficient and effective way to decrease the amount of time and effort spent identifying and hiring a contractor, as well as ensuring that the contractor complies with any regulatory requirements.
Work Order Management: Manage and handle your work order process efficiently so every managerial aspect is according to your line of thinking. This includes work order creation, planning, and assignment to meet the timely resolution of tasks.
Data Analysis: Utilize a data analytics tool to monitor space utilization, spending trends, and compliance, as well as uncover cost-cutting options. This approach cut out all the red tape from the process.
Communication Tools: Upgraded communication tools such as chatbots to communicate more effectively with service providers and internal stakeholders, resulting in more fruitful collaboration.
Types of Facility Management Software
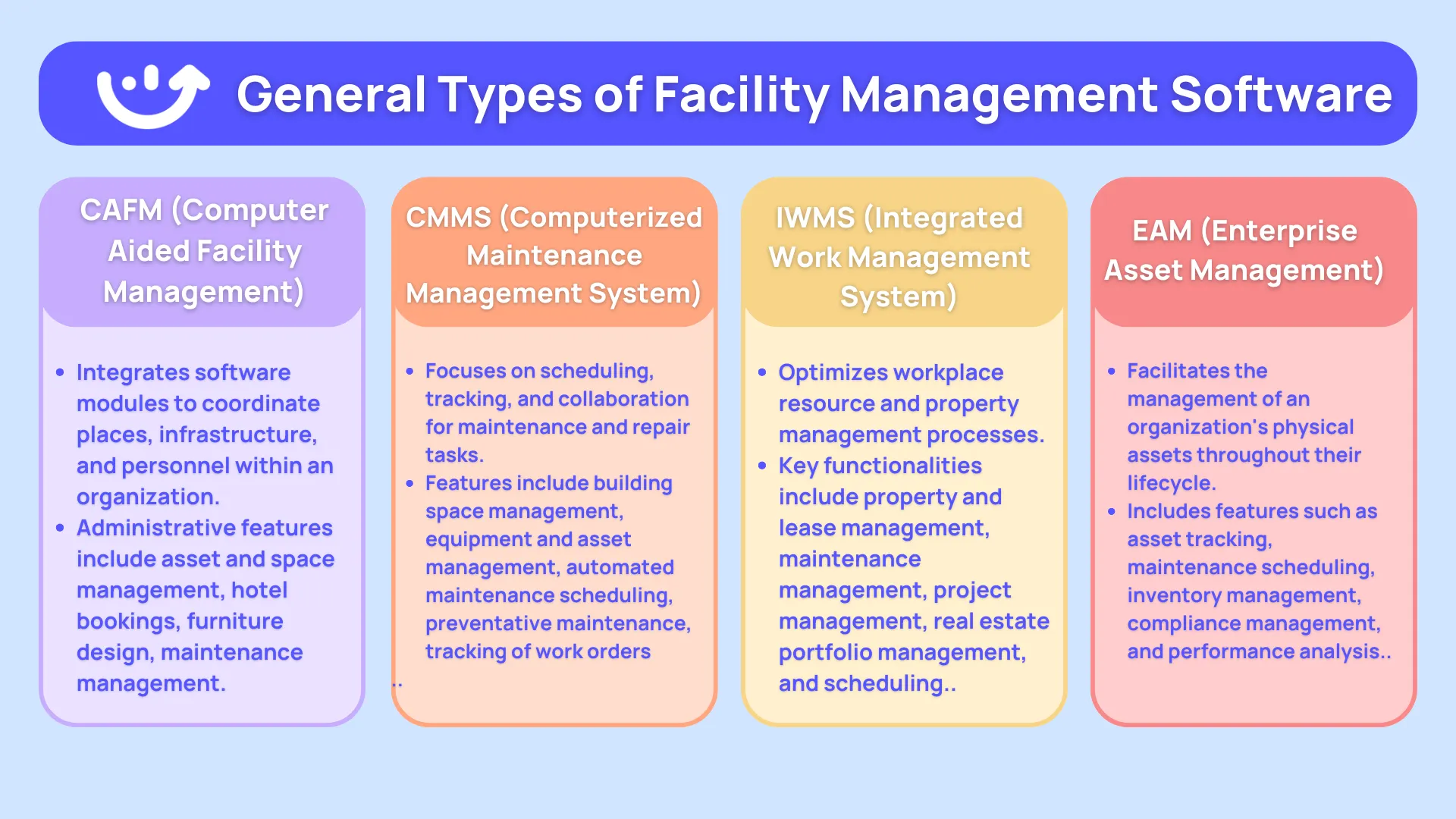
1. CAFM Computer Aided Facility Management)
This type of facility management solution coordinates places, infrastructure, and people using an enterprise-level suite of interconnected software modules. CAFM's administrative skillset comprises asset and space management, hotel bookings, furniture and layout design, and maintenance management.
A CAFM will also involve strategy planning, disaster preparedness, relocation planning, and staff scheduling.
2. CMMS (Computerized Maintenance Management System)
CMMS primarily focuses on three aspects of maintenance/repair: scheduling, tracking, and collaboration between staff responsible for maintenance/repair. It improves communication between managers and service providers by providing features such as Building Space Management, Equipment and Asset Management, automated maintenance scheduling, preventative maintenance (PM), tracking (work orders, etc.), reporting, and analysis.
3. IWMS (Integrated Work Management System)
Such facilities management software optimizes workplace resource and property management processes by including key functionalities such as property and lease management, scheduling maintenance management, asset, and maintenance management, project management, and real estate portfolio management, among others.
Building Management Software
After digging into the general notion of facility management, let's look at what a building management system performs and how it may improve the day-to-day operations of your facility/s.
The building management system (BMS) monitors your facility operations in your building to ensure maximum efficiency.
Integrated with advanced tools, building facility management software organizes data exchange across a large number of linked devices. This data offers analytics, allowing the present management of your property to make informed decisions.
Building management software helps managers regulate
- HVAC
- Lightning
- Electric
- Water Supply
- Piping
- Finances
- Emergency fire system
- Access control
Incorporating these features into a single unified BMS improves the effectiveness and efficiency of building operations.
Energy-efficiency upgrades can cut facility energy use by up to 40%. facility management solutions helps companies gather and analyze trends and data within a facility to identify areas of inefficiency and improvement.
How Facility Management Apps are Different from Traditional Methods?
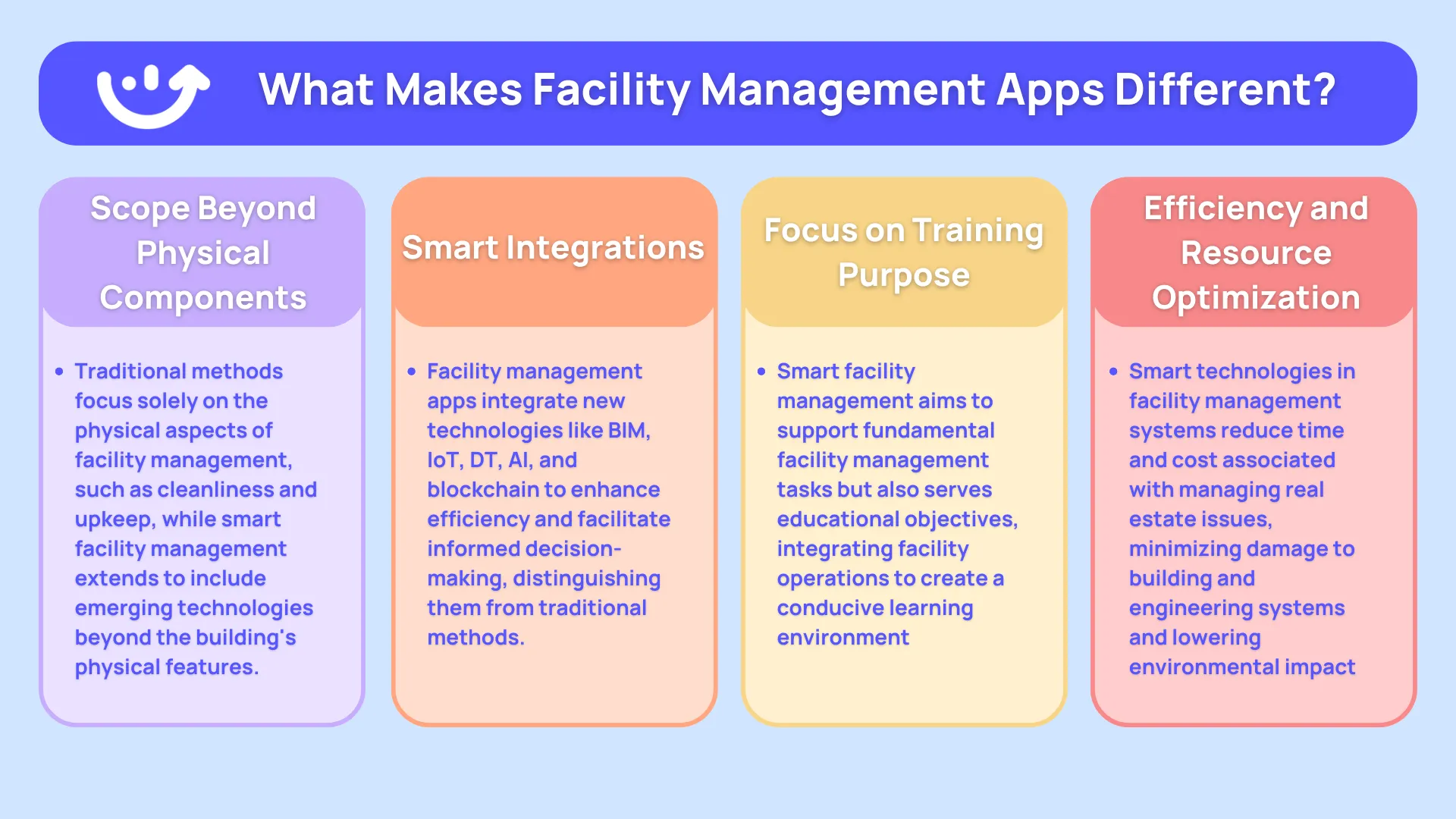
- Goes Beyond Physical Components
One of the primary differences between the two is that the conventional approach to facility management focuses solely on the physical components of a structure. It is largely concerned with the building's cleanliness and upkeep. In contrast, Smart facility management strives to cover emerging technologies that are not limited to the physical features of building management.
- Smart Integrations
Facility management apps integrate new technologies such as BIM (Building Information Modeling), IoT (Internet of Things), DT (Digital Twin), AI (Artificial Intelligence), and blockchain to increase overall facility management efficiency and enable more informed decision-making.
- Focus on Training Purpose
Intelligent facility management aims to assist fundamental tasks and is often viewed as independent from the core educational goals of teaching and learning. An integrated building management system aims to harness the facility's main operations to create a learning environment conducive to educational success.
- Efficiency and Resource Optimization
The advantage of smart technologies included in facility management systems is that they reduce the amount of time and money spent on managing real estate issues. By using these technologies, managers can minimize building and engineering system damage, hence lowering the environmental effect.
- Data-Driven Decisions
Data-driven decision-making supplements informed decision-making based on representational data and collaborative efforts. Smart facility management provides actionable insights by combining real-time data from on-site devices and the linking method with BIM.
- Advanced Integrations
Smart facility management offers more advanced and integrated solutions than traditional methods. By using technology, managers can streamline operations, improve service quality, and allow for a more flexible and responsive approach to building management.
Benefits of Integrated Management System
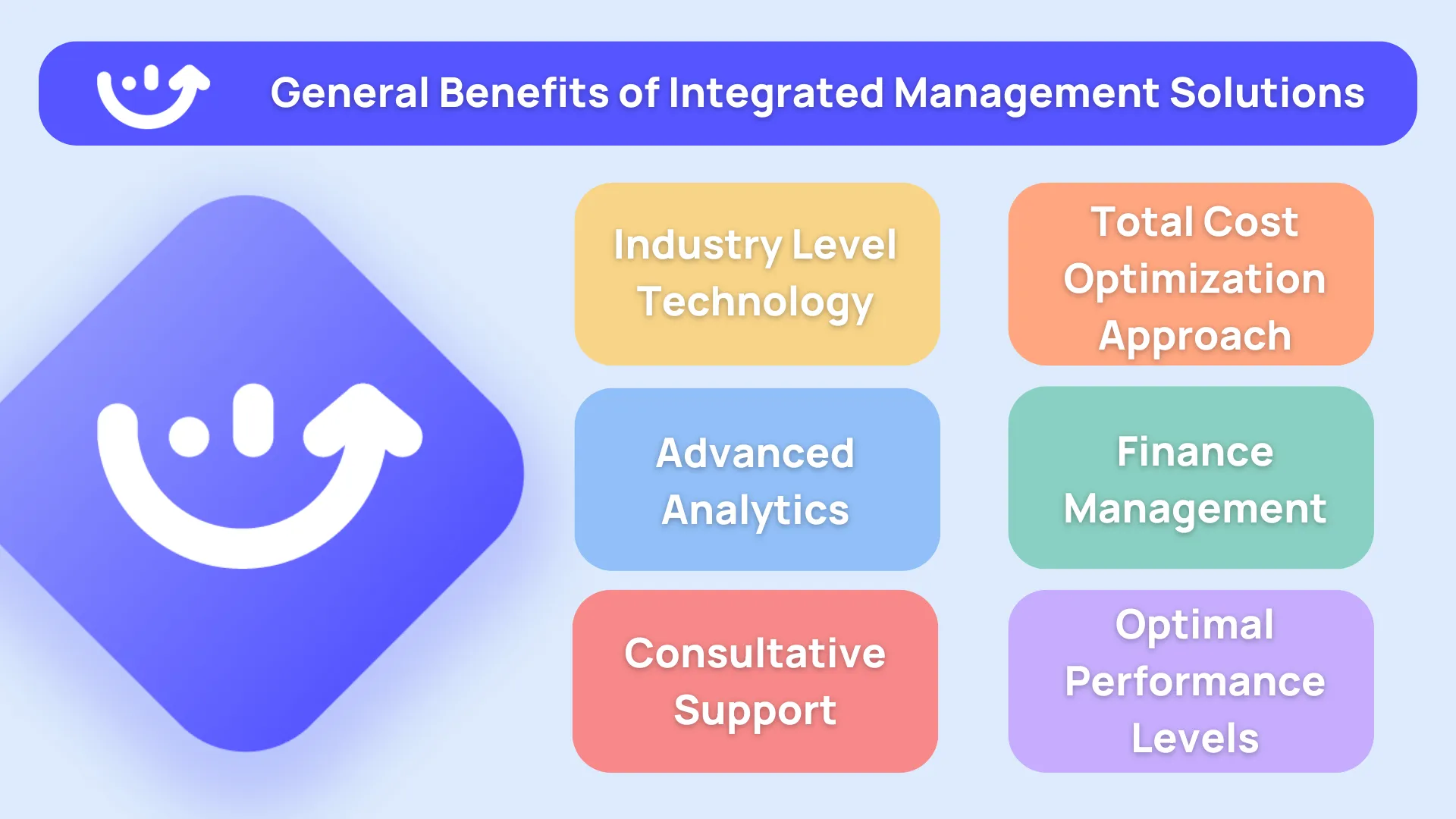
Shared data, irrespective of industry or operation, promotes enhanced efficiency, cost savings, and advancement. An integrated facilities management solution can help you achieve such advantages by providing the following features:
Industry-Leading Technology
The IFM technology platform includes industry-leading customized features for work order management and other functions.
Doing so enables total transparency in your facilities management program.
At the same time, it collects all relevant information, such as asset history, program activity, spending, and more. This enables you to gain useful information that can assist you in improving efficiency and making faster and better short- and long-term choices about your facilities management operations.
Using the IFM technology platform, you can share these insights in real time with your IT, procurement, budgeting, marketing, sales, and other departments across the company.
If you want contractors, IFM providers, or other vendors to have access to the platform, you can let them in.
When calamity hits, you will not have enough time to seek assistance. With an IFM solution, you'll have access to a nationwide network of reputable, licensed Independent Service Providers (ISPs) that will work for you. Your IFM solution provider will contact the relevant ISP, coordinate processes, and manage all interactions, allowing you to focus on what you need to do.
Total Cost Approach
IFM employs a whole cost approach, grouping FM activities and identifying the linkages between equipment, processes, and people that can drive productivity, workflows that can be simplified, and practices/materials that can be eliminated to ensure cost savings.
For example, negotiated pricing (not hourly) and service level agreements (SLAs) for service providers allow for coordination across various facilities, improved processes, and identifying and addressing operational inefficiencies in ad-hoc service provider management leading to significant program savings.
Depending on the strategies and billing models used, each FM business will guarantee varying degrees of savings. Best-value IFM system utilizes a comprehensive, cost-effective method.
Advanced Analytics
One of the most significant benefits of using the IFM is its superior analytical capabilities, which can help prevent highly costly or catastrophic problems before they occur. By efficiently tracking individual assets by model type, age, location, and other factors, you will gain incredible, accurate information about where your problem areas are and will be much better prepared to help reduce the need for emergency repairs by implementing preventative and predictive maintenance techniques.
Finance Management
The right integrated facility management application will fundamentally change the way you budget. Some can even create a spending strategy, utilizing previous program data to understand your stores' budget requirements, as well as an emergency plan for you so you'll know what to expect in the case of a significant disaster.
This is especially crucial if your stores' service requirements change rapidly. With the right FM tools, managers can identify any utility at a given time and, owing to their knowledge of store sales and occupancy rates.
Consultative Support
Software alone cannot provide true value to an FM program. It needs human intellect to convert data into action, and this is one area where an IFM solution may be really useful.
Moving from an isolated, historical paradigm to an integrated one enables facilities teams and senior leadership to collaborate more effectively to advance the business.
It's a facility management strategy that can have a huge influence on your company: well-informed data-driven decisions based on insights from a source that truly understands your industry.
The Rise of Facility Management Apps
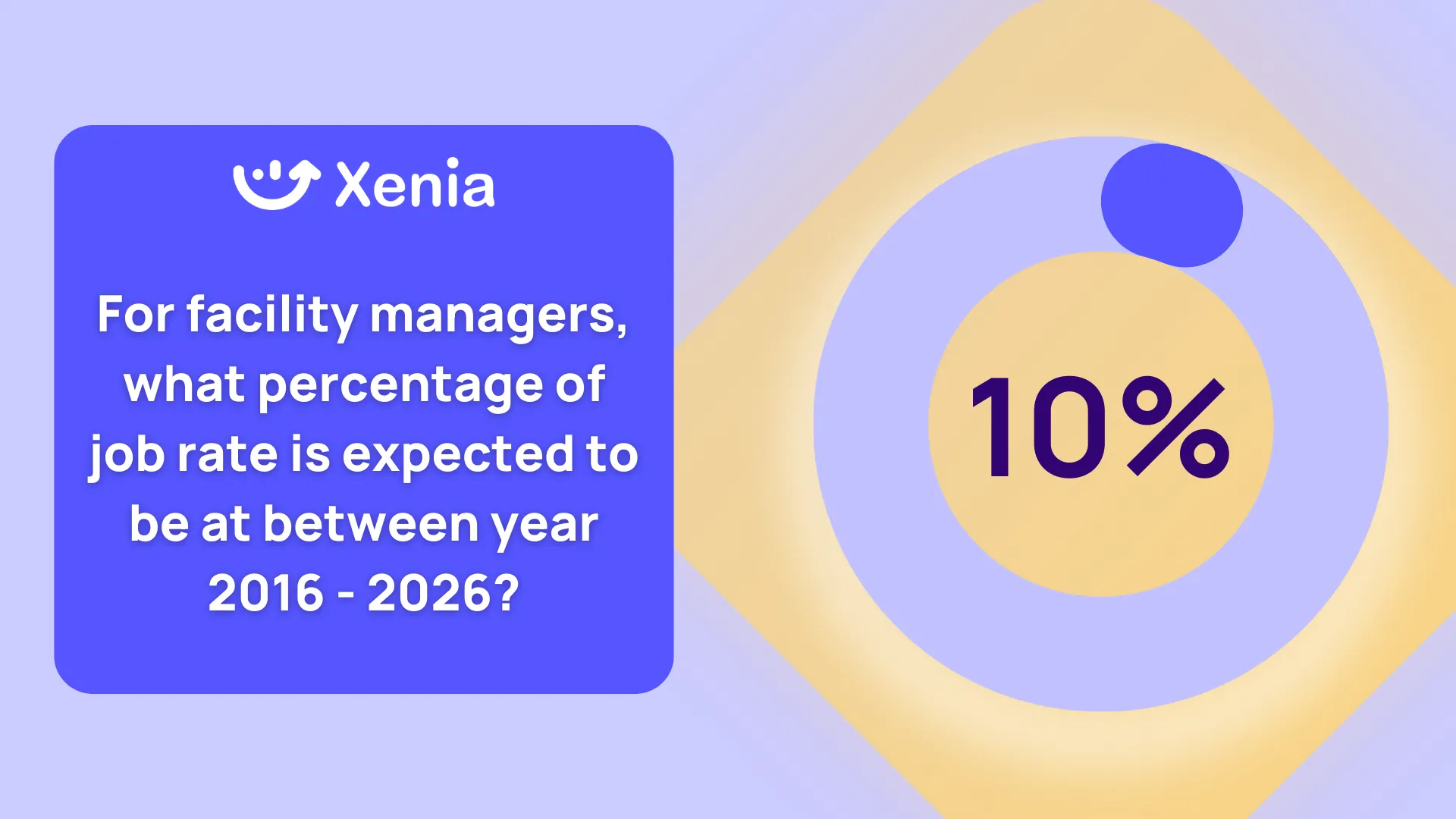
Mobile apps are critical in building on the integration principles laid out earlier bringing facilities management to your fingertips.
With facilities management apps, you are never limited to your physical workplace. These apps give important, actionable information whether you're in the field, at the office, or working remotely.
Moreover, a facility management app allows users to check in, receive notifications and updates, recognize when challenges arise, and what more is required to properly manage to complete tasks while on the go.
Maintenance workers can employ mobile technologies to easily produce, identify, record, and track tasks. With this in mind, a full work order and assignment can be easily completed without any issues. This essentially allows all maintenance professionals, from the team leader to the individual worker, to manage tasks seamlessly while increasing overall productivity.
Moving on, Facility Management Apps simplify asset tracking by allowing users to track asset condition, and maintenance history, and estimate future service and requirements.
Furthermore, managers can monitor and operate different building systems remotely and on their own time.
For example, building owners or facility managers can change HVAC schedule settings or ensure that the facility enters an unoccupied security mode when a mobile phone is no longer in use at the end of the day.
Advantages of On-the-Go Management
- Facility managers can tackle issues as they emerge, ensuring that operations operate smoothly.
- Managing tasks and gathering vital data via mobile devices is convenient and makes facility staff more productive.
- Facility management apps provide the ability to make proactive decisions since the operational manager has real-time information on the system's overall resilience and can use the data being entered to make timely decisions.
- Mobile solutions enable the connection between facility management teams, service suppliers, and stakeholders, which drives collaboration. They provide and support a smooth communication route, increasing collaboration among all stakeholders.
- On-the-go facility management enables agile resource allocation depending on current demand. This optimization ensures that resources are allocated to where they are most effective, resulting in cost savings.
10 Best Facility Management Applications
1. Xenia - Overall No.1 Facility Management App
.webp)
Xenia is an all-in-one maintenance and operations platform for teams to manage work orders, track preventative maintenance schedules, build simple checklists, and more.
This facility management free online tool has an Android app and is one of the easiest and most cost-effective solutions on the market.
Xenia's Key Features:
- Smart Maintenance & Inspections: Streamline inspections and automate corrective tasks.
- Digital Forms for Remote Data Collection: Create and submit mobile maintenance checklists & logs. Export as reports & receive email notifications for completed submissions.
- Geolocation: Required/optional geostamp responses for multi-site operators and employees.
- Scheduled Work: Improve productivity with clear task schedules and mobile notifications. Distribute daily responsibilities and task assignments automatically.
- Task & Cost Management: Ensure accountability with status-tracking, required images, responses, and templates. Add costs associated with tickets. Summarize, report, and export CSV/PDF.
- Work Requests and Approvals: Centralize request management, expedite approvals, and monitor resolution.
- Photo-Centric: Capture images when creating an issue and responding to checklist steps.
- Notifications & Reports: Optimize incident handling with mobile reporting and live progress tracking.
- Instant Messaging: Enhance teamwork with quick chats and announcements.
With plans built for everyone from small businesses to global enterprises, Xenia has the tools you need to succeed.
The program also offers team-based pricing with one flat monthly rate for the first 20 users. It has a free trial as well as a free forever plan to get started risk-free.
Pricing:
- Free Forever: Everything free with limited access to features for up to 5 users
- Starter: $99 / month for 15 users
- Premium(Best Value): $199 / month for 15 users, and access to advanced features
- Custom: Need something tailored to your organization?
2. LLumin
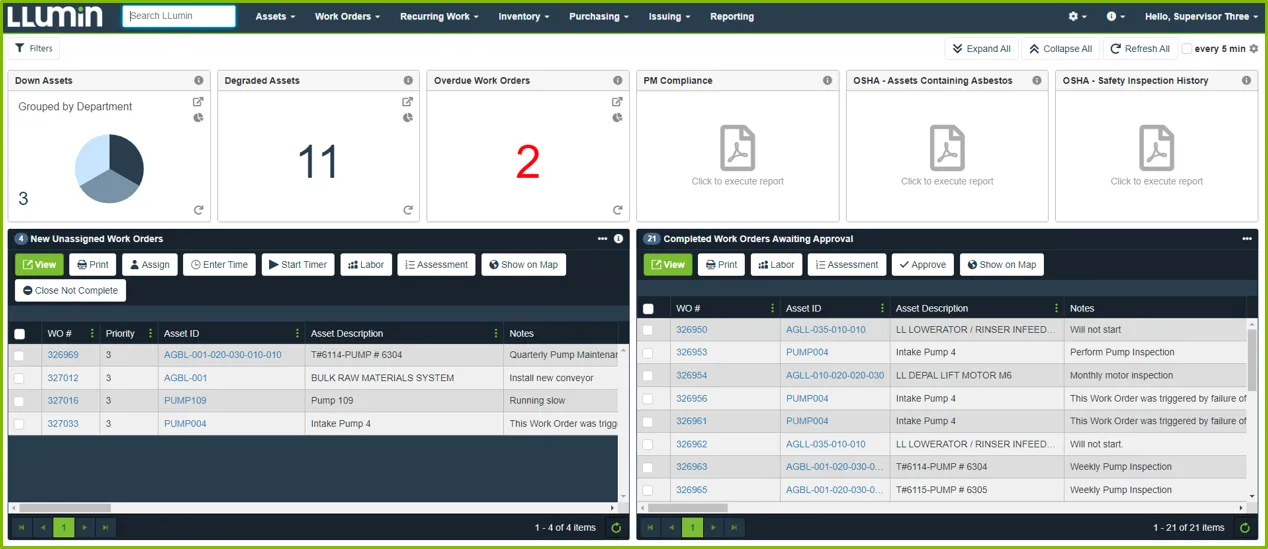
The LLumin Android app allows users to carry out various functions of the standard CMMS suite in an on-the-job setting. The app provides users the ability to open and view work order details, create new work orders, and enter parts, procedures, and inspections for those work orders. Open and view asset details, create new assets, and complete asset inspections all from your phone.
Key Features:
- Streamlines maintenance workflows, reducing downtime and increasing productivity.
- Optimizes maintenance operations, extending asset lifespan.
- Reduces maintenance costs, improves asset performance, and increases uptime.
- Facilitates informed decision-making, resource optimization, and enhanced efficiency.
- View work order details, create new work orders, and input parts, procedures, and inspections.
- Open and view asset details, create new assets, and complete asset inspections.
- Data input syncs seamlessly with the central system.
Llumin offers a starting pricing of $45 per user per month. With premium & enterprise plans at $80/user/month and $110/user/month.
Pricing:
- Professional: Starting at $45 per user per month
- Premium: Starting at $80 per user per month with automated maintenance and engineering procedures
- Enterprise: Starting at $110 per user per month
3. Yardi Facility Manager
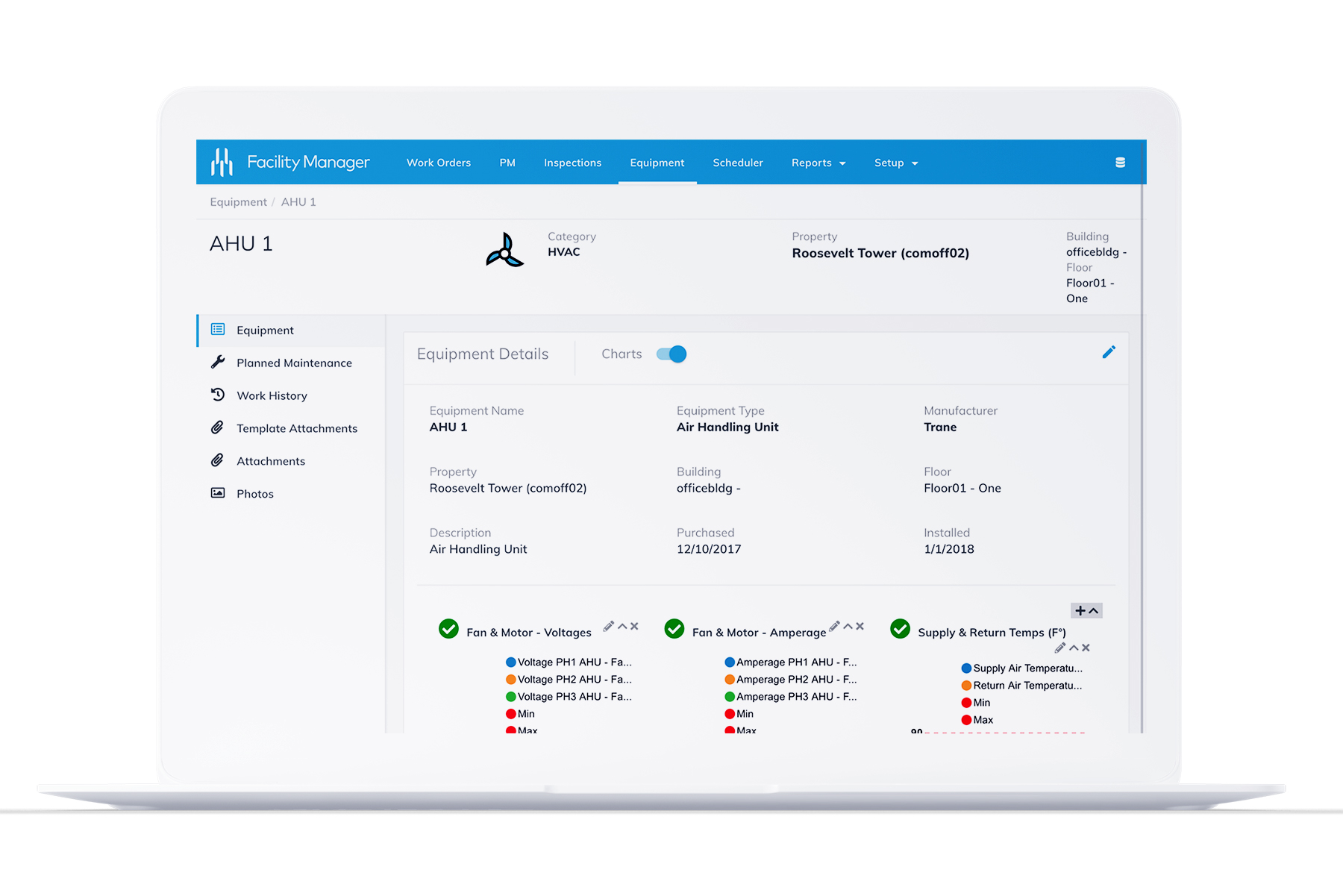
With the Yardi Facility Manager Android app, you can manage and complete work orders, inspections, and preventive maintenance checklists.
Yardi enables technicians to oversee all facilities management tasks while in the field through the Facility Manager mobile app. Automatic synchronization ensures real-time data access, facilitating confident decision-making, notifications, and information sharing among technicians, vendors, and tenants.
You can update work orders, and conduct preventive maintenance, and inspections on the go.
Key Features:
- Work Orders: Assignment of unclaimed work orders. Attachment of photos and notes.
- Assets: Asset management, creation of work orders, status and time tracking
- Checklists: Generation of inspections and submission reports
- Access: Vendor management for work orders
Yardi Facility Manager pricing is not publicly available. To learn more, check out the links below:
Pricing:
- Demo required.
Available on Android Mobile/Tablet
4. FacilityForce
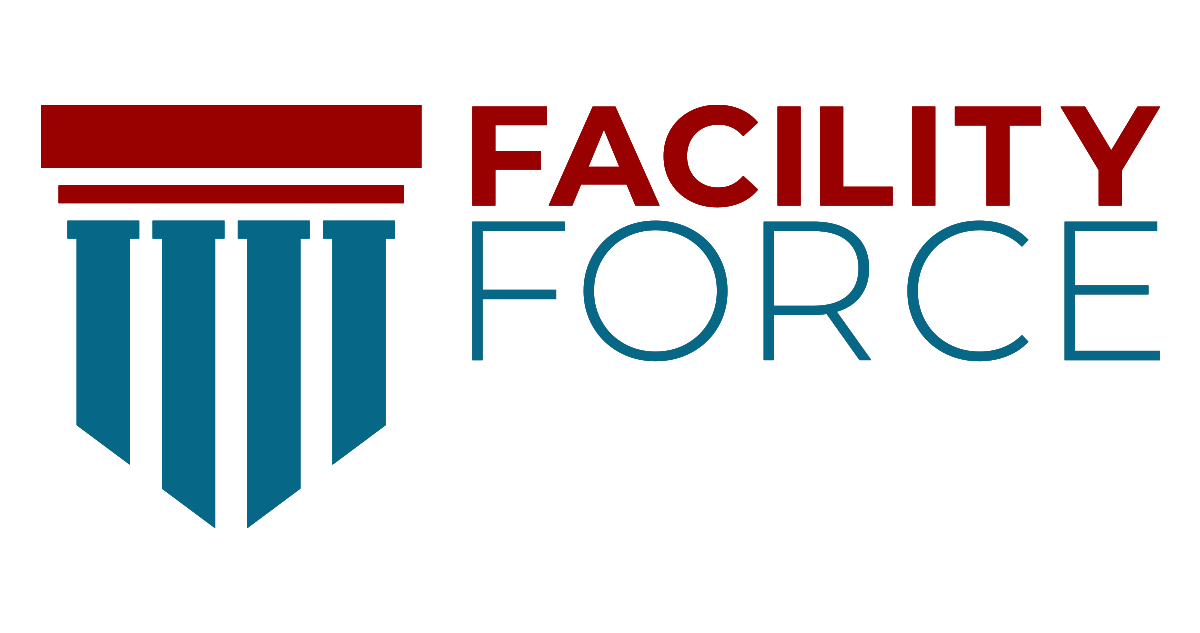
FacilityForce provides a comprehensive, end-to-end solution for facilities management. While focused on public sector facility management, this platform offers robust facility management software features across mobile, tablet, and Web apps.
Key Features:
- Request Management: Capture comprehensive details using a sophisticated online request engine.
- Geo-centric Asset Management: Facilitate map-centric asset tracking and management.
- Workflow Management: Efficiently route work orders based on business processes, including approval, scheduling, and resource allocation.
- Mobile Workforce Dispatch: Dispatch field personnel through mobile apps for job location, parts ordering, time tracking, and task completion.
- Financial Tracking: Monitor total costs and performance metrics organization-wide.
FacilityForce pricing is not publicly available. To learn more, check out the links below:
Pricing:
- Pricing: demo required.
Available on Android Mobile/Tablet
5. Snapfix
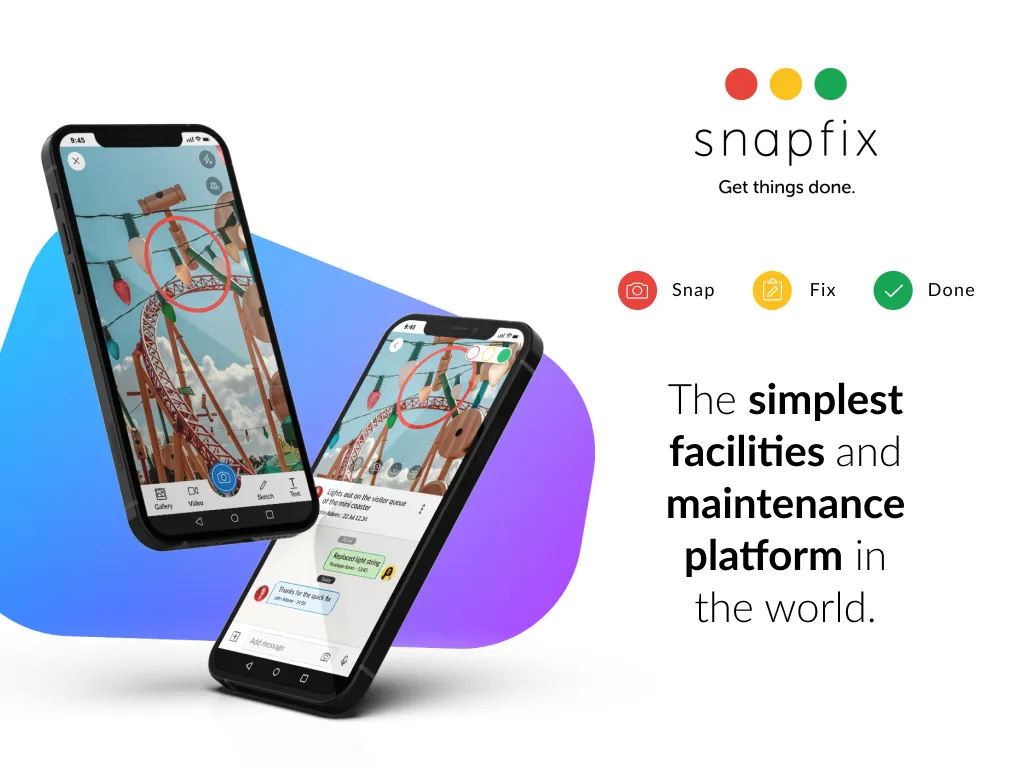
Snapfix is a digital solution for work orders, planned maintenance, and fire safety. It includes flexible checklist features that allow you to manage maintenance inspections and create work orders on the go.
Their software is photo-centric, making it easy to snap and fix anything anywhere.
Key Features:
- Work Order Management
- Planned Maintenance
- Asset Management
- Data Analytics
Snapfix’s solution is popular in the hospitality industry. Snapfix offers per user per month and unlimited user pricing plans. Snapfix starts at $9.99 per user per month and $99 per month for unlimited users.
Pricing:
- Free: 7 day trial of all Snapfix features
- Self Serve Per User: $9.99 per user/per month
- Snapfix Pro: $99 per month
- Enterprise: Starts from $199 per month
Available on Android Mobile/Tablet
6. ArcGIS
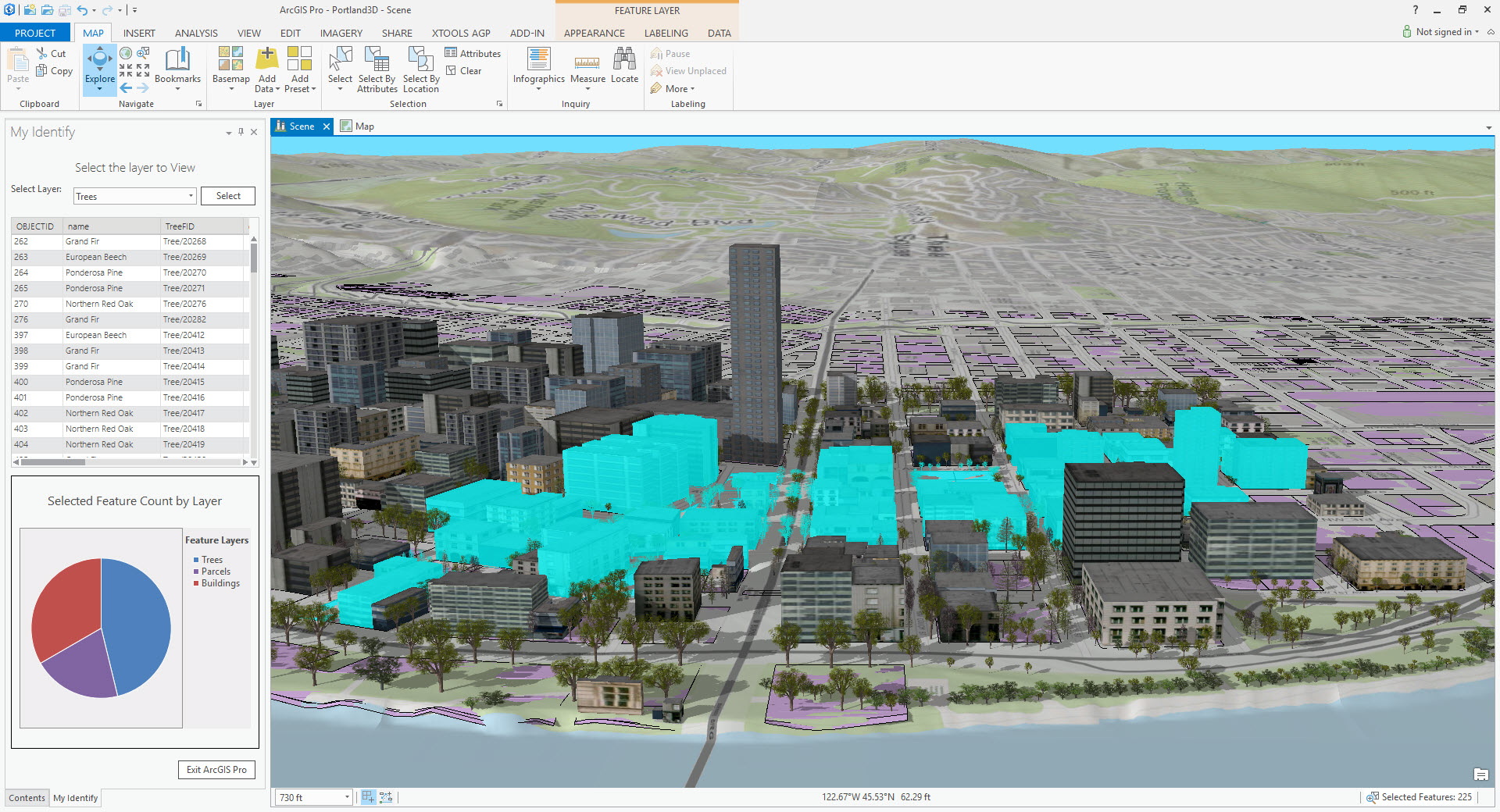
To help facility managers access and display critical data, ArcGIS provides a state-of-the-art location-based analytics solution.
It can be used by facility managers to see the whereabouts of their assets, employees, and facilities in real-time and to track their movements.
Key Features:
- Track and Manage Assets: Utilize location-based data to monitor the movement and status of assets across different sites or facilities.
- Predict Service Needs: Employ predictive analytics to anticipate maintenance requirements and optimize facility upkeep.
- Coordinate Quick and Appropriate Responses: Establish efficient communication channels and protocols to swiftly address emerging issues in real-time.
Pricing:
- Contact the vendor for pricing.
7. Maintenance Connection
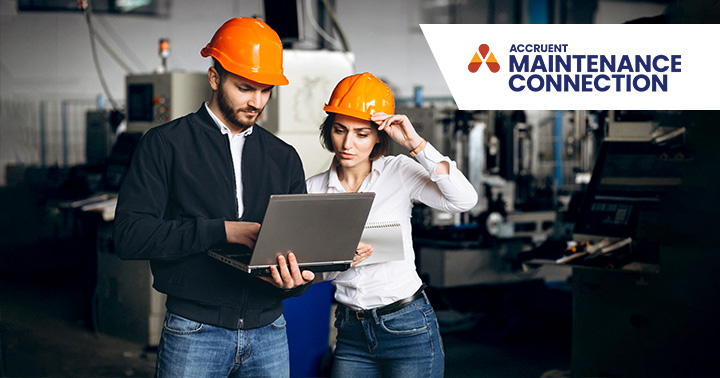
With Maintenance Connection's preventative maintenance module, site managers can extend the life of their equipment and decrease the frequency of emergency repair orders.
This software can help you save money on inventory and maintenance.
Key Features:
- Monitor all aspects of Facility Management with Ease: Utilize intuitive monitoring tools to oversee all aspects of facility management, including maintenance, operations, and resources.
- Organize Workforce for Higher Efficiency: Implement workforce organization tools to optimize staffing schedules and assignments, fostering greater efficiency and productivity.
- Schedule and Track Maintenance on Different Kinds of Assets: Utilize comprehensive scheduling and tracking systems to manage maintenance tasks across a variety of asset types, ensuring timely upkeep and prolonging asset lifespan.
Pricing:
- Professional: $110/month per Named User Subscription
- Add-On: $58/month per Professional
8. Fiix
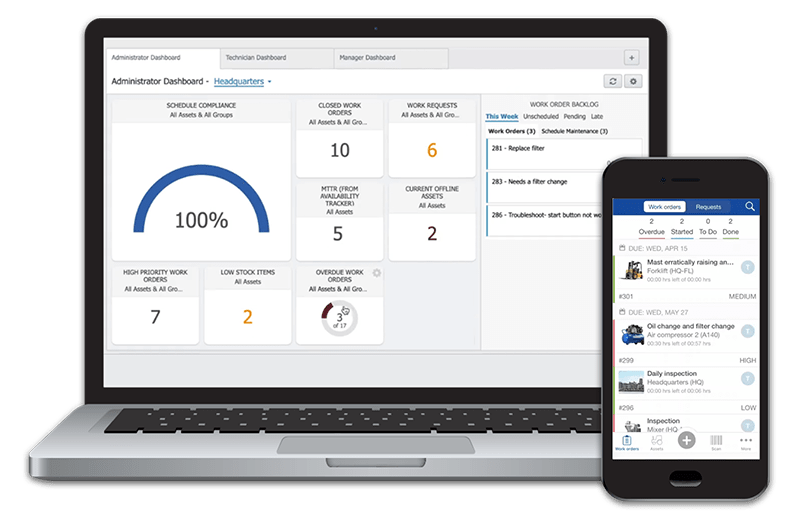
With Fiix's user-friendly reporting and analytics, facility managers can maximize asset performance.
Improve your maintenance processes with the help of Fiix Foresight, an AI engine that provides deeper insights and data-driven actions.
Key Features:
- Track Metrics with Multiple Dashboards: Utilize multiple dashboards to monitor and analyze key metrics across all facilities, providing a comprehensive overview of performance.
- Integrate Data from Production and Business Systems: Seamlessly integrate data from production and business systems into the CMMS platform for enhanced visibility and insights.
- Tag Assets and Parts using QR Codes and Barcodes: Efficiently manage assets and parts by tagging them with QR codes and barcodes, enabling easy identification and tracking.
Pricing:
- Free: $0
- Basic: $45 per user, per month
- Professional: $75 per user, per month
- Enterprise: Custom Pricing
9. Maxpanda
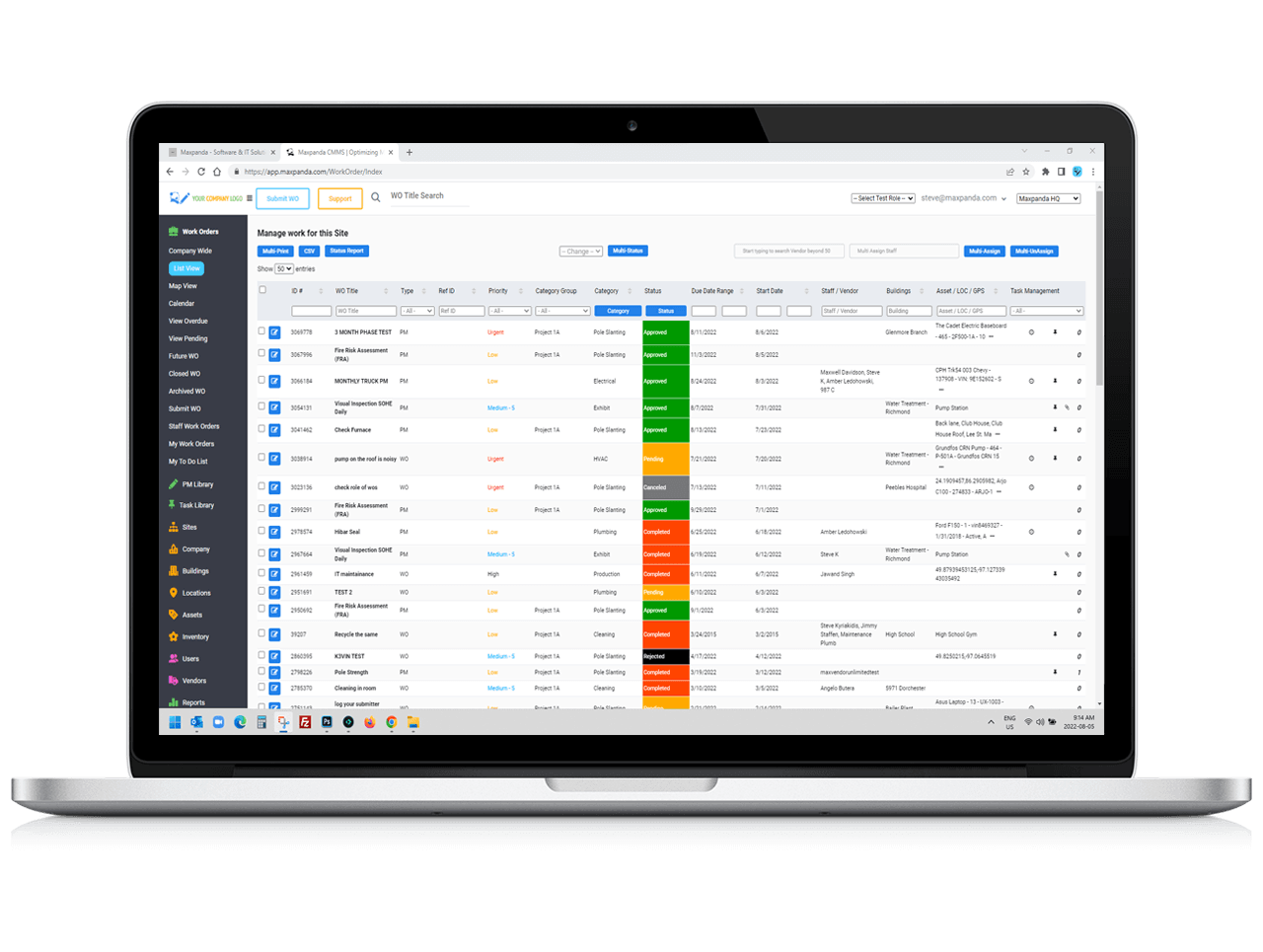
It is easy for facility managers to keep tabs on scheduled maintenance using Maxpanda, a CMMS that is both simple and efficient.
Work in sync with your team, suppliers, and clients by using Maxpanda.
Key Features:
- Scan QR Codes: Enable users to conveniently initiate work order requests by scanning QR codes associated with assets or equipment, facilitating efficient submission from the field.
- Manage Integrated Resource Library: Utilize an integrated resource library to effectively organize and maintain assets, providing a centralized repository for storing crucial asset information and documentation.
- Add Both Invoice Item and Tax Types to Invoices: Customize invoices by incorporating various item types to offer detailed breakdowns of charges and services, ensuring clarity and accuracy in billing.
Pricing:
- Contact the vendor for pricing.
10. Asset Essentials
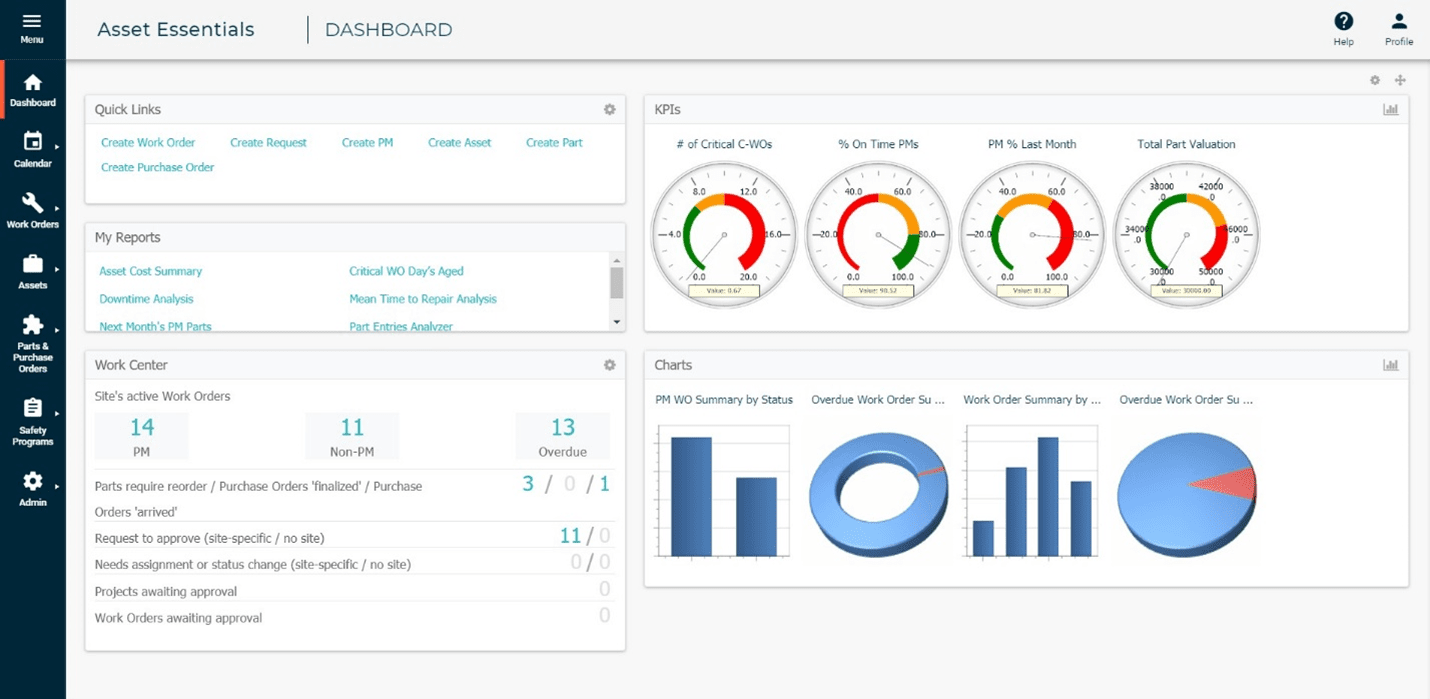
Apply Asset Essentials to a variety of maintenance tasks. Additionally, it allows facilities managers to control assets with facts rather than speculation. Asset Essentials makes it simple to measure the efficiency of maintenance and how well it aligns with company objectives.
Key Features:
- Monitor the Use of Parts and Equipment: Track the usage of parts and assess equipment reliability over time to optimize maintenance schedules and inventory levels.
- Capture Information and Add it to a Digital Database: Digitally capture relevant information about equipment, maintenance activities, and part usage to maintain accurate and accessible records.
- Integrate with ArcGIS: Integrate with ArcGIS for spatial analysis and mapping, enabling visualization of asset locations and facilitating informed decision-making based on geographical insights.
Pricing:
- Contact the vendor for pricing.
8 Free Facility Management Solutions
1. MaintenanceCare
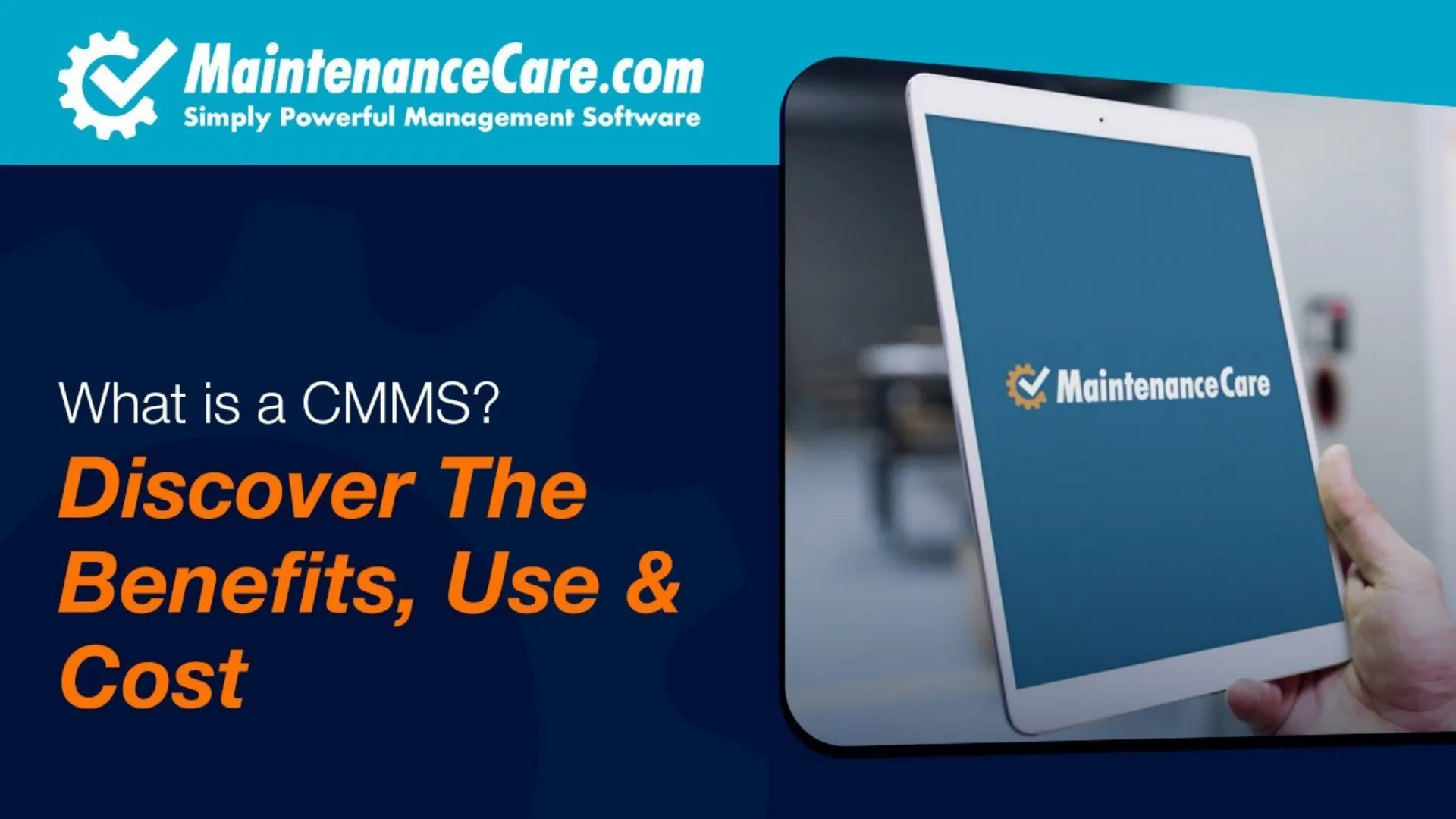
Ideal for healthcare, hospitality, and many other sectors, Maintenance Care is a CMMS (Computerized Maintenance Management System) another best and free maintenance program that offers unrivaled usability.
Its user-friendly design and intuitive interface mean that users require no special training and can effectively navigate the software easily. In addition to this, Maintenance Care offers exceptional customer support.
This, coupled with its feature-rich and specifically designed interface accommodates various facility management initiatives.
Key Features
- Preventive maintenance management enables routine maintenance to avert breakdowns and extend equipment life.
- Work order management simplifies the process of creating, assigning, and tracking work orders for maintenance activities.
- Asset monitoring allows clients to keep track of the status and location of assets in their facilities.
- Parts and inventory management allows for the efficient administration of spare parts and supplies, decreasing downtime.
- Document storage enables users to conveniently organize and retrieve important documents, instructions, and processes.
- Reporting and analytics solutions provide insights into maintenance performance and asset health, allowing for data-driven decision-making.
Pricing
- Free Edition
- Enterprise Edition -$200/month
- WorkOrder Edition -$100/month
2. ARC Facilities
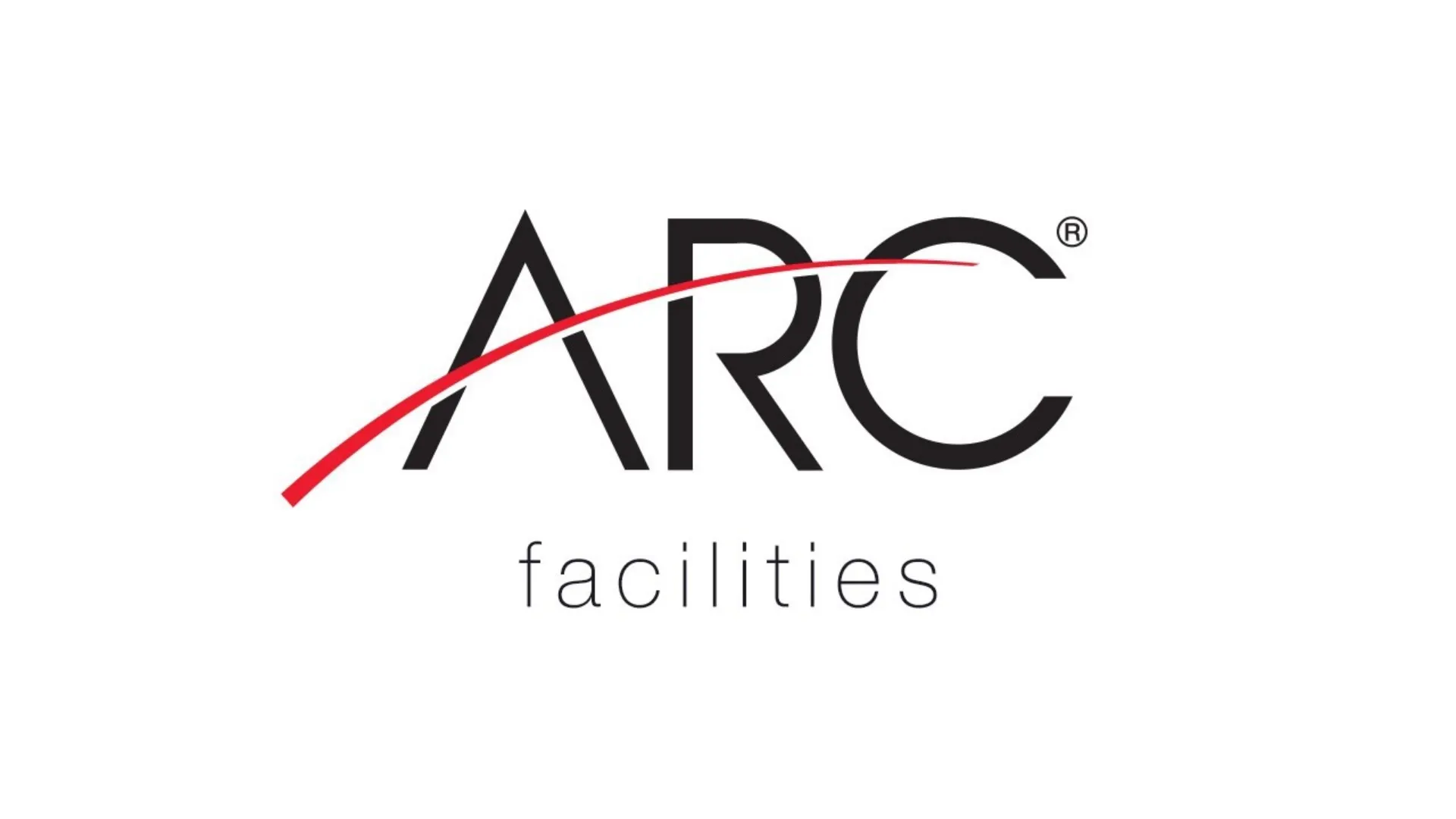
Next on our list of best and free maintenance programs is ARC Facilities. ARC Facilities sets itself apart as one of the top companies in the industry through its ability to cater to a wide range of market segments. Some of these include schools, colleges and universities, healthcare and hospitals, government buildings, office buildings, and many more.
Two integral aspects of this leading free facility management software provider are the quick setup process with no contract involved and top-of-the-line customer support.
Moreover, The software with the secure database can be customized to your specific needs.
Key Features
- Facility and equipment maps provide users with a visual representation of their facilities and assets, allowing them to navigate and allocate resources more effectively.
- Floor and emergency plans offer detailed building layouts, enabling more efficient catastrophe response and evacuation.
- Preventive maintenance management enables firms to plan and track maintenance activities ahead of time, reducing the likelihood of unexpected breakdowns.
- Mobile access enables users to manage facility and maintenance tasks remotely, increasing flexibility and responsiveness.
- Contact management simplifies communication by centralizing contact information for stakeholders, vendors, and service providers.
- Data import and export features enable users to transfer data between ARC facilities and external sources while maintaining data integrity and accessibility.
Data visualization technologies give insights into facility performance and maintenance patterns, allowing for more informed decisions and resource efficiency.
Pricing
- For paid version contact the vendor
3. ServiceChannel
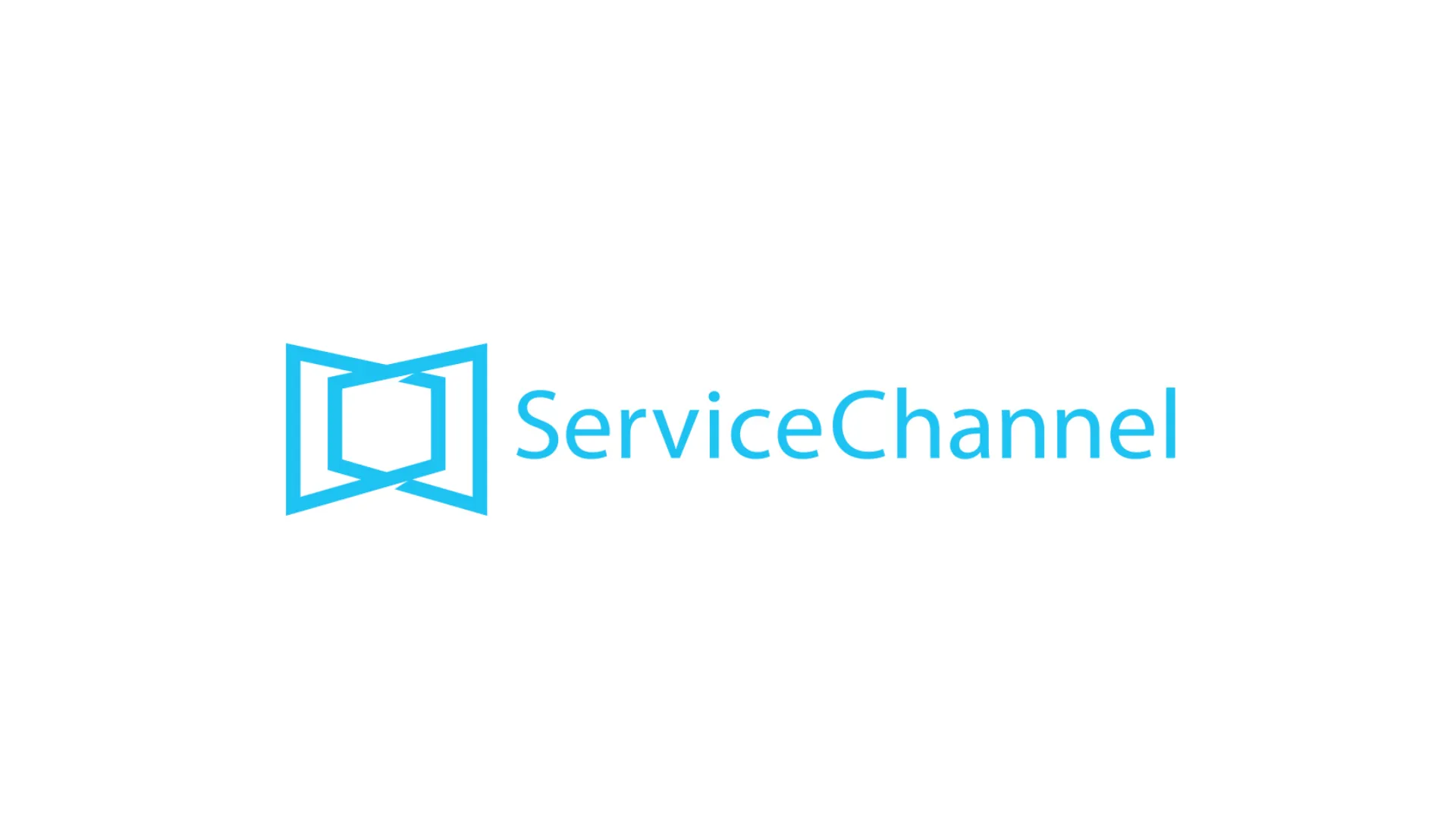
ServiceChannel Service Automation is an integrated suite of web- and mobile-based solutions that automates the entire process of facilities management.
Whether you need help sourcing qualified contractors, getting new assets into a CMMS, or benchmarking how your locations are performing against their peers, ServiceChannel has the technology and analytics you need to more effectively manage your business.
Backed by this unprecedented facilities management platform, several experienced professionals apply best practices to help them identify savings, reduce spending, and gain efficiencies across entire maintenance operations.
ServiceChannel recognizes the value of tracking data and performs analytics from the service suite to evaluate quality across all trades, locations, and contractors.
ServiceChannel maintains that informed decisions and instigating improvements within maintenance operations are produced when customers can view provider performance and service quality data.
Key Features
- ServiceChannel's work order software makes it easy to create, assign, and track work orders for maintenance jobs, ensuring that issues are resolved on time.
- The system provides asset manage
- 30ment capability, which allows customers to track and manage asset maintenance across many facilities.
- Offer the scheduling and control of preventative maintenance jobs, allowing you to handle possible issues and reduce downtime.
- This facility management software allows facilities managers to efficiently manage parts and supplies inventories, assuring availability for maintenance jobs.
- The platform delivers information on provider performance, allowing facility managers to evaluate the level of service given by contractors and suppliers.
Pricing
- For the paid version contact the vendor
4. FMX
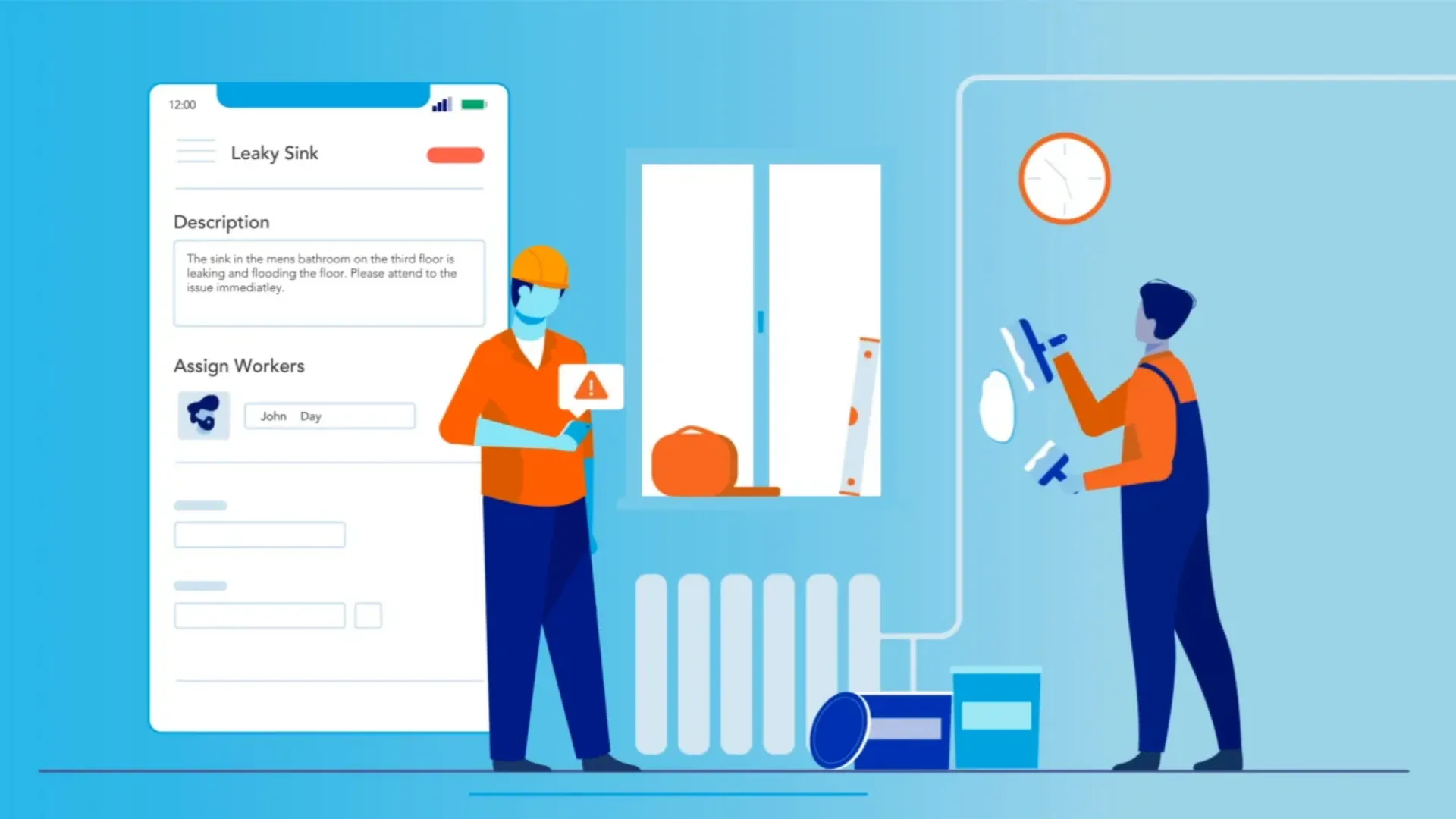
FMX is a leading provider of configurable maintenance and facilities management Software, with the tools necessary to ensure accurate and robust asset management in supporting all processes within the organization including maximizing data integrity, maximizing employee effectiveness, and minimizing operating costs for your facility.
This one of the best and free maintenance programs enables organizations to better manage their maintenance operations and personnel by combining robust Work Orders, preventive maintenance scheduling, asset management, and inventory controls into a single, easy-to-use system.
One more important feature of FMX is its accessibility, it can be accessed on any web browser, even on mobile devices. It also gives you unlimited requesting users at no extra cost, meaning you can always involve or keep your employees or all the people who need to be in the loop of what is going on with maintenance or facility.
Key Features
- FMX makes it easier to manage equipment maintenance chores, ensuring that assets are in good working order and reducing downtime.
- Preventive maintenance tasks may be scheduled and tracked using the program, allowing companies to handle any issues before they worsen.
- The software offers powerful reporting and analytics capabilities, enabling customers to obtain insights into maintenance performance and make data-driven choices.
- This best and free maintenance program allows businesses to successfully plan and prioritize capital projects, ensuring that resources are allocated optimally.
- FMX contains capabilities for monitoring components inventory, which ensures that essential supplies are accessible for maintenance tasks.
- FMX automates task assignment procedures to ensure that work orders are assigned to the relevant people efficiently.
Pricing
- For paid version info, please contact vendor
5. eSpace
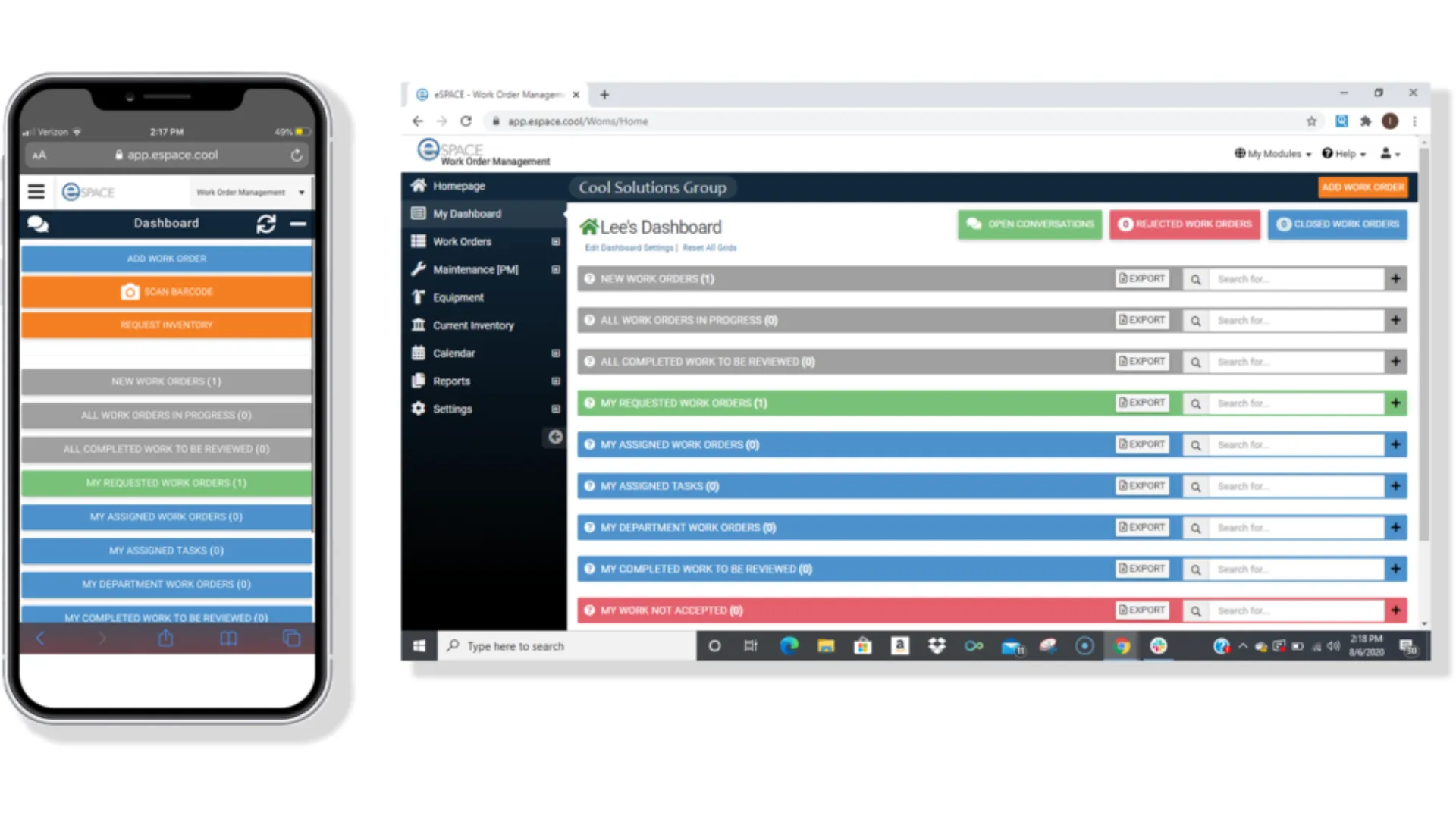
eSpace is a facility management system package that is created for institutions such as churches and schools.
Tailored with precision, eSpace is built and designed for simplicity and can be used for all functionalities.
The program's been built to be very user-friendly, with navigation that makes sense and is accessible to all levels of users. It’s an excellent tool for any organization wanting a quick and easy solution that performs all the required functions for managing facilities and events.
eSpace’s functionality is boosted by a series of advanced features, all aimed at improving efficiency and productivity. This includes event scheduling, work order management, and preventative maintenance, all saving time and resources.
Key Features
- eSpace guarantees that facilities are always in top shape by managing repair orders and scheduling preventative maintenance tasks.
- Users may manage maintenance operations, monitor equipment health, and produce informative reports to help them make more educated decisions.
- eSpace streamlines the process of creating, allocating, and tracking work orders.
- provides full facility management features, allowing customers to manage all elements of their facilities easily.
- eSpace's asset monitoring technology allows users to easily monitor the status and placement of assets throughout their lifespan.
Pricing
- Deluxe (Event schedule)-$50
- Premium-$100
- Ultimate-$150
- Deluxe(Work order management)-$50
6. Fiix CMMS
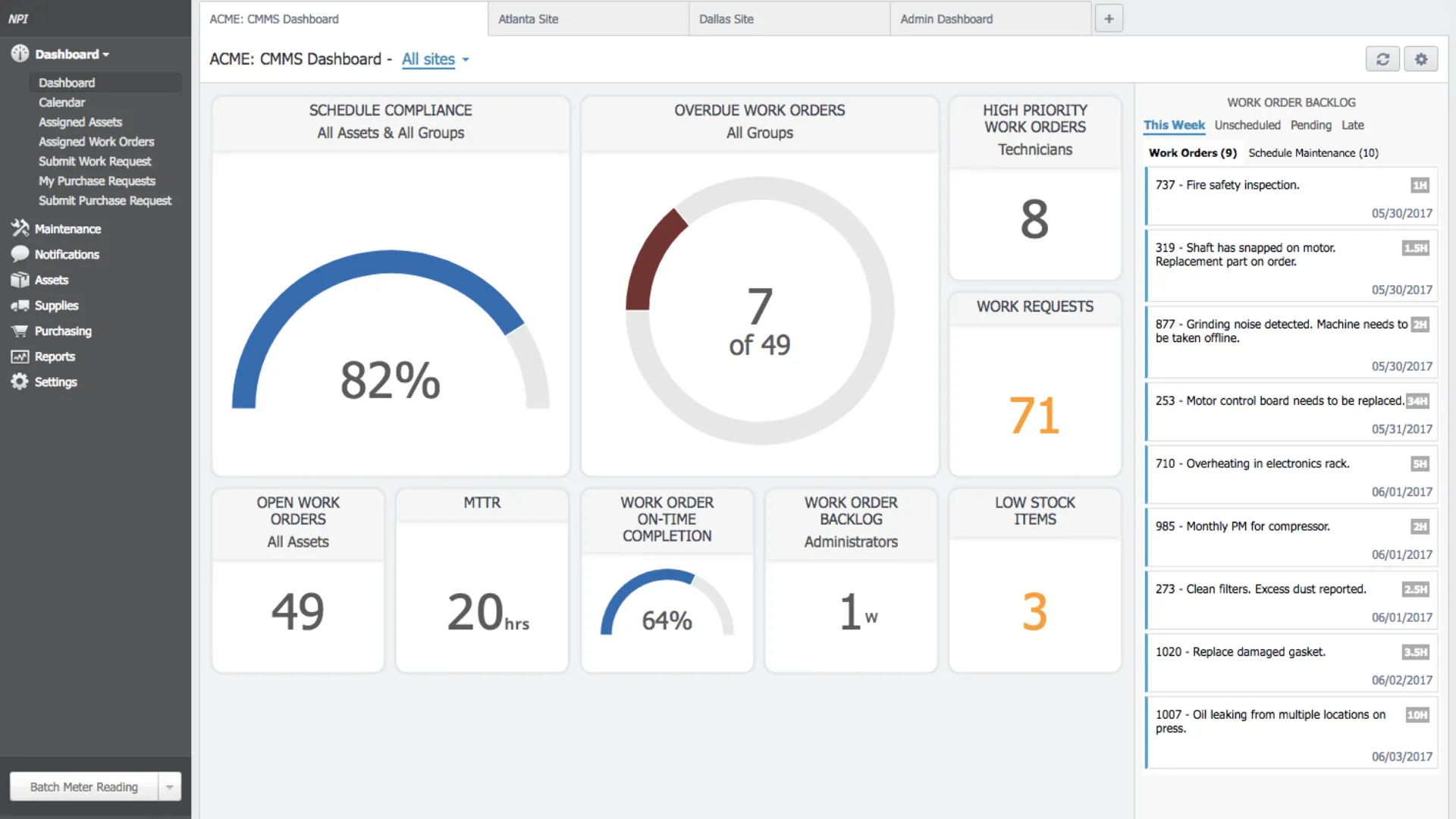
Fiix is one of the top maintenance software choices for a computerized maintenance management system (CMMS), providing comprehensive tools that streamline work order submission, tracking, and analysis through an intuitive work request portal.
With Fiix you can manage work orders with ease, Fiix allows you to make detailed to-do lists, you can set standard operating procedures (SOPs), and due dates and you can add attachments e.g. photos. it also gives you multiple pre-built report templates to give you a range of reports to choose from.
Managers have the choice to build custom reports, some reports include completion rates, repair times, total costs, follow-up tasks, and failed inspections, and then through AI capability analyze the reports in detail and notify you of any anomalies to improve operational efficiencies.
Fiix’s greatest strength is a free plan that offers the ability to track unlimited work order requests, inventory parts, assets, and task lists as well as schedule up to 25 active preventive maintenance requests. Of all the CMMS systems we reviewed, Fiix was the only one that offered a free product with these features.
Key Features
- Routine maintenance procedures may be seamlessly planned and scheduled based on predefined intervals or specified triggers, allowing for proactive maintenance management.
- Log the length, reason, and impact of downtime for building assets such as HVAC systems and elevators. This tool assists in recognizing reoccurring problems and arranging preventive maintenance to avoid possible breakdowns.
- Use a simple analytics dashboard to track critical parameters like equipment failure rates, time to repair, total downtime, work order completion rates, and preventive maintenance compliance, allowing for data-driven decision-making and performance improvement.
Pricing
- Contact Vendor
7. ManWinWin
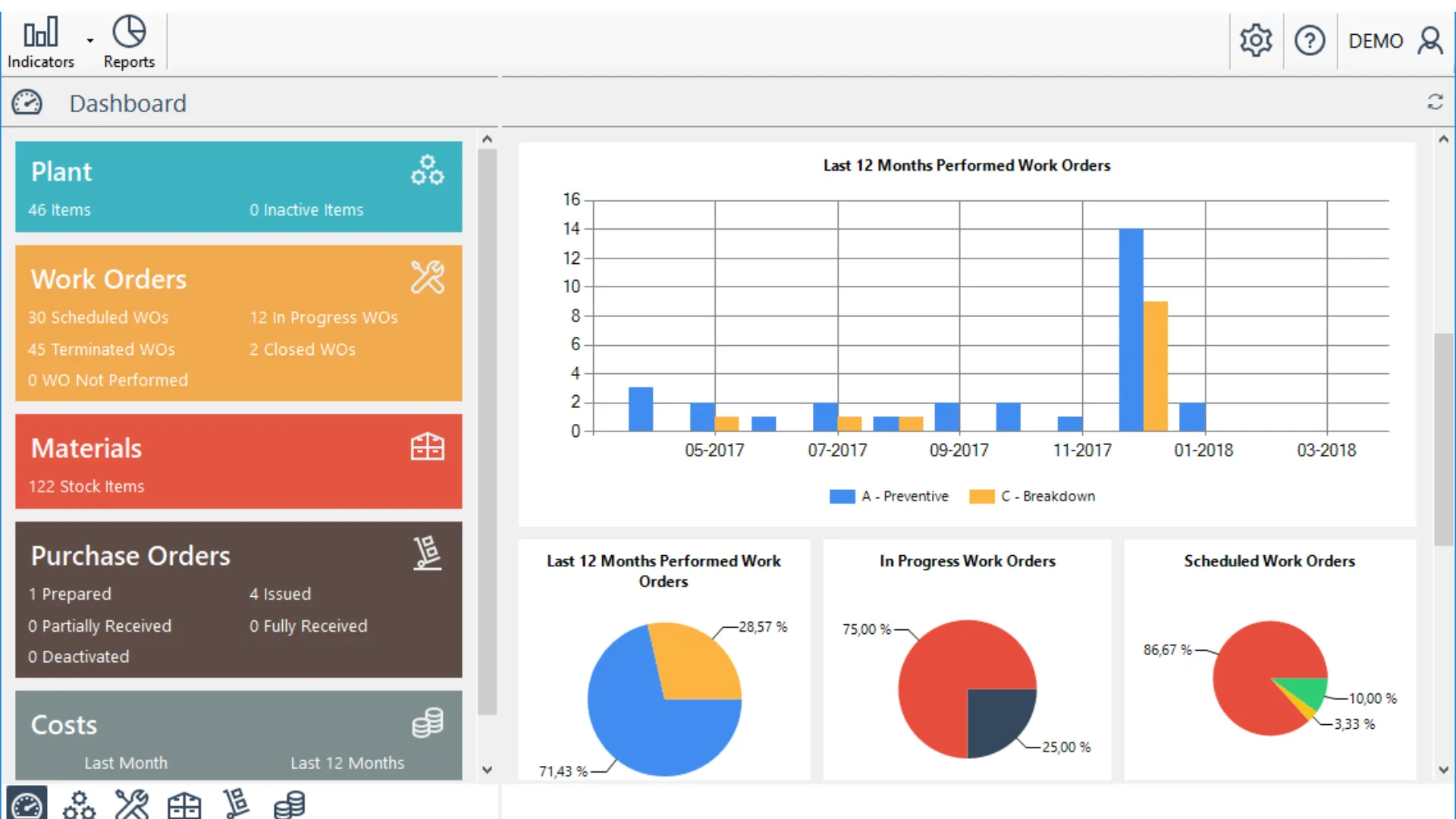
ManWinWin CMMS is one of the best maintenance management software on the market and for good reason. Its user-friendly platform only makes maintenance management easier.
It comes with a vast array of features that allow you to generate, distribute and track work orders, and manage all aspects of maintenance repair.
A key highlight of the ManWinWin Suite is the ability to prioritize work orders based on the criticality and urgency of maintenance tasks, enabling managers to optimally allocate resources and resolve urgent and important tasks immediately.
Additionally, the tool enables users to easily create their dashboards with key maintenance performance indicators such as the average time between failures, average time to repair, total downtime, work order completion rate, and preventive maintenance compliance.
Key Features
- Utilize the power of an AI assistant to get real-time alerts for possible difficulties, gain insights into equipment performance and historical data, and benefit from predictive projections regarding resource requirements and future failures.
- Streamline approval procedures by digitally signing maintenance papers, which allows stakeholders to approve work orders, service contracts, material requisitions, and other critical activities more efficiently and securely.
- Effectively monitor and control the expenses of maintenance operations, such as labor, materials, and external services, while maintaining openness and responsibility in spending management.
Pricing
- Contact Vendor
8. WatchWire
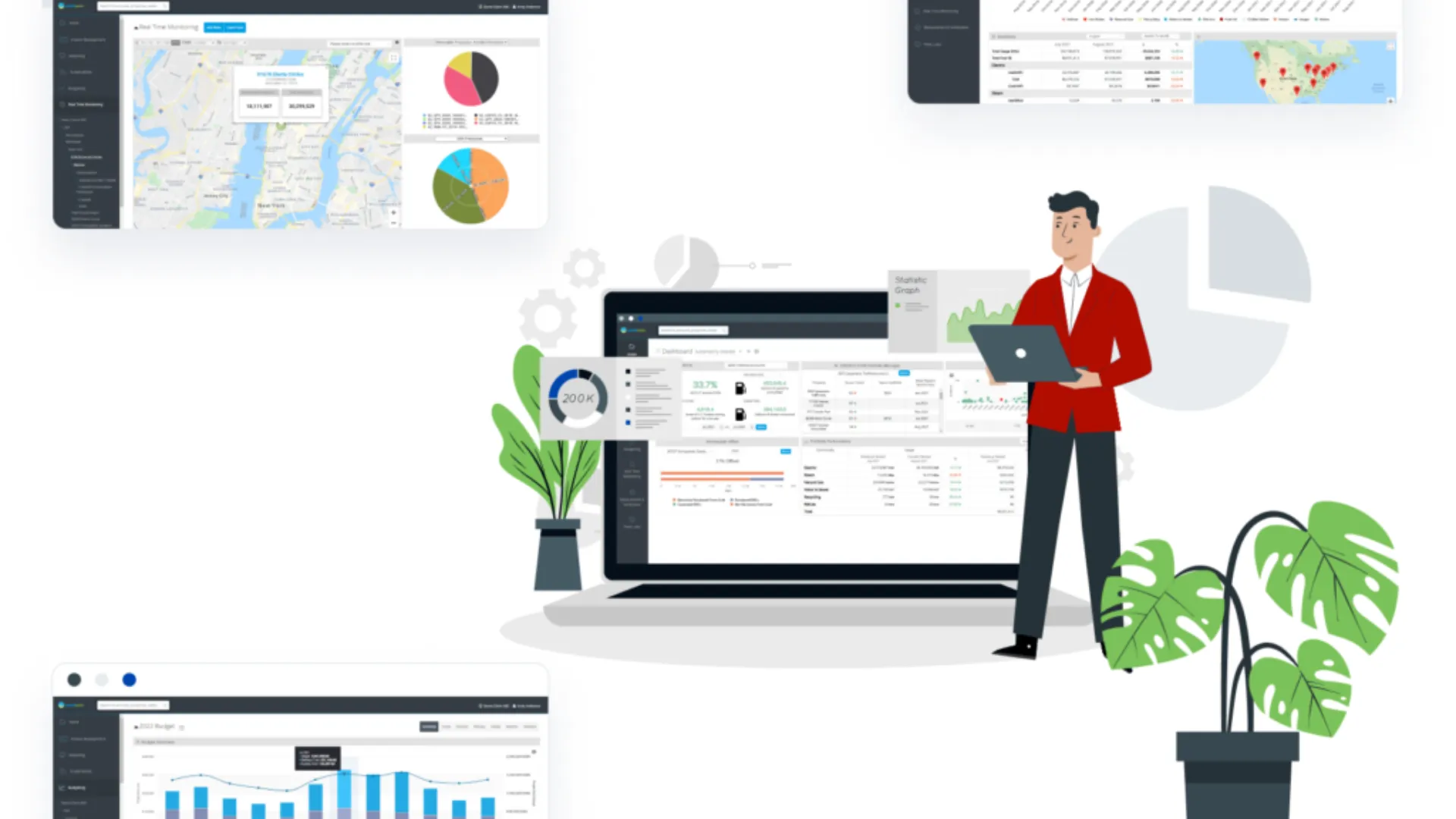
Our next best maintenance software solution, WatchWire focuses on energy and sustainability management as an offering within the domain of facility management.
Designed to target organizations who are striving to contain energy costs and contribute towards carbon reduction campaigns, WatchWire offers comprehensive solutions to address this important aspect of facility operation.
In short, at its core, WatchWire is an analytics tool crafted specifically for managing utility budgets and consumption. With this tool, customers can gain deep insights into their consumption patterns and identify opportunities for optimization. By leveraging advanced analytics tools, customers can effectively monitor and analyze usage trends, identify inefficiencies in these trends, and develop targeted strategies to not only optimize energy but to drive down costs.
In addition, WatchWire provides excellent sustainability reporting. Customers can track and report their environmental performance metrics with pinpoint accuracy as well as transparency. Customers can generate reports, which are customized to their specific requirements, that demonstrate their activities in decreasing their greenhouse gas emissions, conserving resources, and promoting sustainability.
Key Features
- Gain a thorough understanding of energy consumption trends, uncover inefficiencies, and apply targeted measures to optimize energy usage and decrease expenses.
- Create configurable reports that emphasize environmental performance measures such as greenhouse gas emissions, resource conservation efforts, and adherence to sustainable practices, allowing for more transparent communication about sustainability activities.
- Efficient utility bill management capabilities make it easier to manage utility bills, analyze expenses, and uncover cost-cutting options.
Pricing
- Contact Vendor
How to Choose the Best Facility Management Tool?
To choose the best facility management solution, facility managers must first assess several factors.
- Features and Functionalities
Assess the software's basic features. These should encompass a wide variety of facility management features, from asset management to preventative maintenance, and should be tailored to the facility's particular requirements.
- Easy-to-Use
The program must have a user-friendly interface. Anyone on the facilities management team can simply learn how to utilize this program on their own.
- Scalability
As the facility grows or changes, the software should be able to grow to meet the new demands and requirements without losing data or disrupting the software's operation and reporting.
- Integrations
Look for software solutions that work seamlessly with other tools and systems. Having an integrated application allows you to operate more efficiently by allowing data to flow across different areas of facility management, resulting in a unified facility management system.
- Customization
Having control over the software is essential since each facility has unique requirements. As a facility manager, you want a versatile platform that can be tailored to your operations and processes.
- Mobile-Accessibility
The program must have a mobile-friendly interface or, better yet, a mobile app. In this manner, if you have a day off and don't want to travel to your workplace, you can oversee operations from anywhere.
- Cost-Effectiveness
Cost-effectiveness is measured by the total cost of ownership, which includes initial setup costs, licensing, and any additional fees.
- Security Measures
With security as a top priority, the software should follow industry-standard security measures to secure sensitive facility management data from unwanted access and breaches.
Future Trends in Facility Management
The landscape of building management is changing rapidly and the future will be shaped by advanced technological innovations. Several key emerging trends in the market will drive smarter and more effective facility management. 45.1% of workforce managers indicated they want to increase total worker productivity. Managers can enhance their facility management operations by concentrating on IoT integration and facility automation technologies.
- IOT Integration
In facilities management, the integration of "Smart" technology and the Internet of Things (IoT) has transformed this industry. With IoT integration, all assets, building systems, and gadgets can linked to exchange data via the Internet. All networked data is transferred to the cloud for analysis, which aids in the automation of operations and the proactive planning of maintenance activities. It allows your maintenance staff to stay connected to the field in real-time.
- AI Automation
Facilities management is the next commercial frontier, and automated solutions are likely to make rapid advances. work expenses can be reduced and technology enhances efficiency and complements human work rather than replacing it. Meanwhile, as AI becomes more integrated, FMs will be able to utilize predictive analytics to anticipate maintenance and hence plan more successfully in advance.
- Increased Mobility
The increased ability to achieve worldwide data and transmission gives Facility Managers (FMs) more mobility than ever before. These mobile apps enable technicians to submit work orders, consult user manuals, and retrieve equipment maintenance history from anywhere in the field. This aspect results in more efficient follow-up on work orders and more responsive facility operations.
All of these trends are linked. For example, the Internet of Things provides greater data-driven decision-making while also increasing mobility.
Facility equipment and processes communicate data via the Internet, which may be accessed from anywhere via mobile applications. This connection enables a constant flow of information, allowing FM teams to make data-driven choices on the go.
Facility Management Software- FAQs
How does facility management software increase operational efficiency?
Facility management software improves operational efficiency by automating procedures, enabling real-time asset monitoring, offering data-driven decision-making insights, and allowing stakeholders to communicate seamlessly.
As a result, it leads to more efficient resource allocation and overall enhanced facility performance.
What are the most important things to look for in facilities management software?
Comprehensive asset management, preventative maintenance scheduling, integration capabilities, mobile accessibility, and configurable checklists are the key things to look for in facilities management software.
Why do we need Internet of Things (IoT) facilities management software?
The Internet of Things in facility management software enables managers to link assets, building systems, and devices over the Internet.
This allows to automate processes, schedule maintenance with assurance, and transmission of information in real-time. In this manner, anyone can connect each system directly, making facility management more interactive.
The Bottom Line
Data integration throughout your organization is vital to being agile, competitive, and productive in today's corporate environment. Facility management software has taken on an essential role in assuring efficiency, accuracy, and deliberate decision-making.
In this guide, we have thoroughly studied facility management software, beginning with the many types of software on the market and progressing to the importance of installing an integrated solution, followed by the influence of mobile technology.
In light of this, Xenia represents the future of facility management technology. The mobile-first service, adaptability, and capacity for customization all combine to make it the best choice for those looking for an all-in-one app that gives the facility manager total control.
Explore all of the top-notch features of Xenia, to see how this advanced facility management app streamlines your operating efficiency.
.webp)
%201%20(1).webp)