Vending machine maintenance is essential for ensuring optimal performance and customer satisfaction.
In today's fast-paced world, vending machines have become integral to our lives, providing convenient access to snacks and beverages. It's essential to prioritize proper vending machine maintenance to deliver uninterrupted service and ensure continuous availability to customers.
Effective vending machine maintenance involves preventive tasks, inspections, cleaning, and inventory management. By implementing these practices, maintenance managers can minimize downtime, optimize revenue, and deliver high-quality service.
Yet, maintenance managers often face challenges in vending machine maintenance, including machine malfunctions, inventory management, and compliance with safety regulations. Overcoming these hurdles requires efficient maintenance management strategies and the use of advanced digital tools.
In this guide, we will delve into the best practices for the future of vending machine maintenance, address common challenges, and highlight the benefits of using Xenia for maintenance management.
Our goal is to equip maintenance managers with the knowledge and tools needed to elevate their vending machine maintenance practices, optimize operations, and deliver exceptional service to customers.
Priced on per user or per location basis
Available on iOS, Android and Web
What is Vending Machine Maintenance?
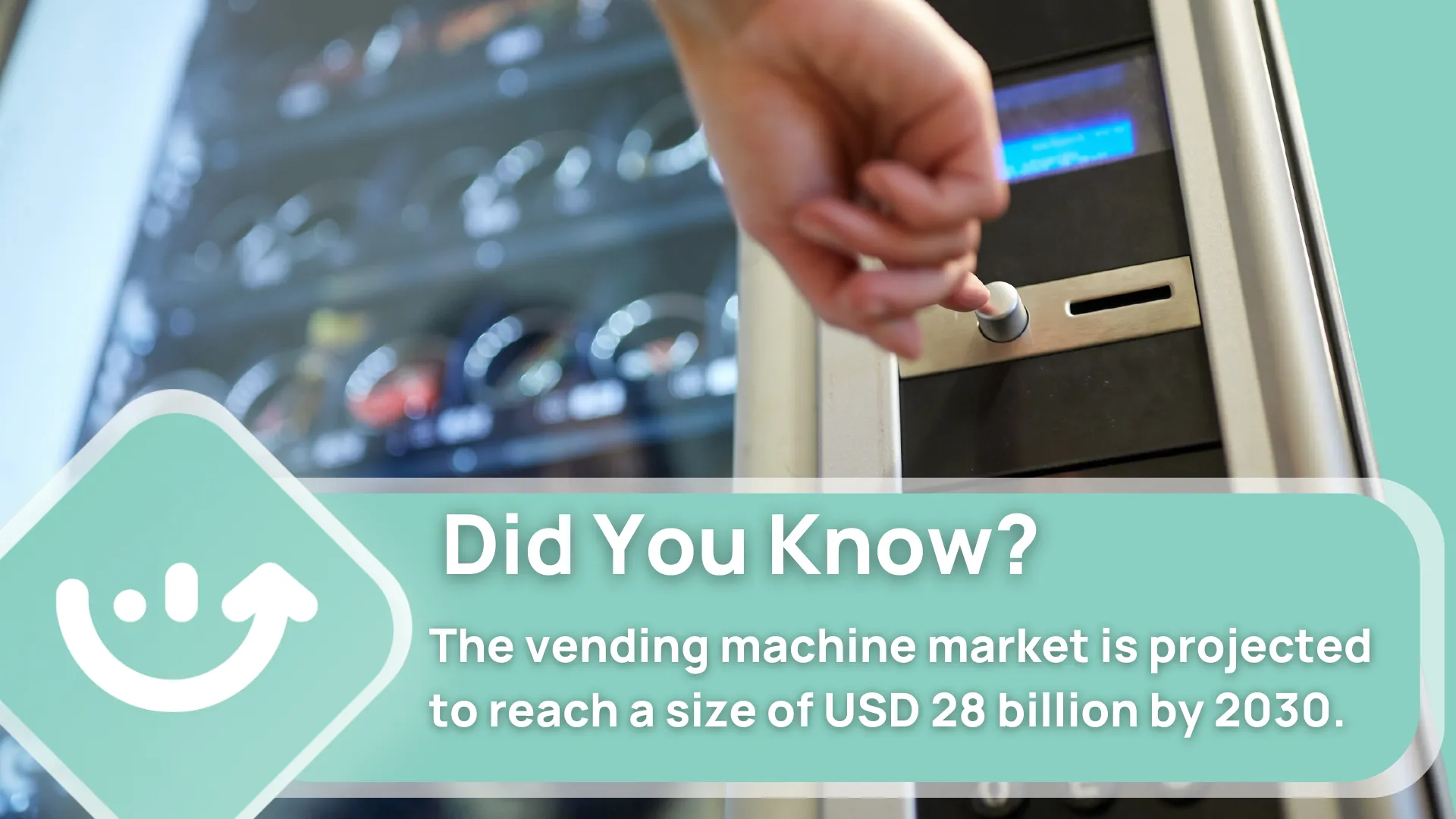
Vending machines are automated self-service units that dispense products such as snacks, beverages, toiletries, and more. According to the report by Custom Market Insights, the vending machine market is projected to reach a size of USD 28 billion by 2030.
Vending machine maintenance involves proactive practices such as preventive maintenance tasks, inspections, cleaning, inventory management, and addressing technical issues. By implementing these practices, maintenance managers can minimize downtime, optimize revenue generation, and enhance customer satisfaction.
Preventive maintenance tasks, including routine inspections and cleaning, help identify and address potential issues before they escalate. This proactive approach reduces the risk of breakdowns, extends the lifespan of vending machines, and lowers repair costs.
Proper inventory management ensures that vending machines are always stocked with popular items. Monitoring sales trends, restocking regularly, and rotating perishable items minimize customer disappointment and maximize sales opportunities.
Benefits of Vending Machine Maintenance
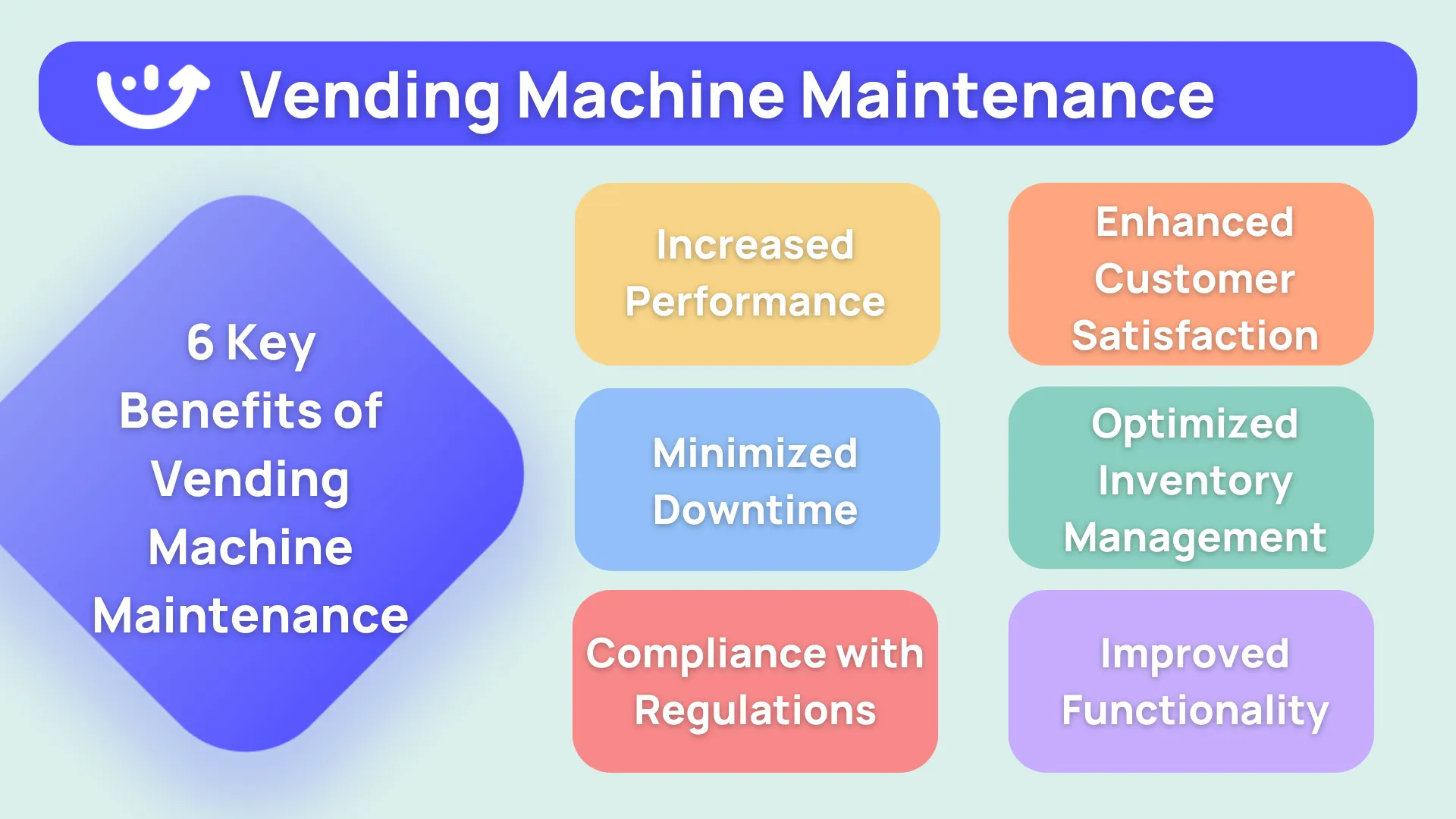
Vending machine maintenance maximizes revenue potential and fosters a positive customer experience, making it a valuable investment for maintenance managers. Implementing a robust vending machine maintenance program offers several other key benefits for maintenance managers:
Increased Machine Reliability and Performance
Regular maintenance ensures that vending machines operate at their full potential, minimizing the risk of breakdowns, malfunctions, and customer dissatisfaction. Well-maintained machines deliver consistent performance, enhancing customer experience and loyalty.
Minimized Downtime and Revenue Loss
By proactively addressing maintenance needs, maintenance managers can minimize downtime caused by unexpected breakdowns or malfunctions. Reduced downtime translates into uninterrupted service and maximized revenue potential.
Enhanced Customer Satisfaction and Experience
Maintained vending machines offer reliable and convenient service, meeting customer expectations. Smooth transactions, well-stocked inventory, and functional cash and coin mechanisms contribute to positive customer experiences and repeat business.
Optimized Inventory Management
Regular maintenance activities, including inventory checks and stock replenishment, ensure that vending machines are always adequately stocked. This avoids customer disappointment due to out-of-stock items and maximizes sales opportunities.
Improved Cash and Coin Mechanism Functionality
Maintenance tasks, such as cleaning and lubrication of cash and coin mechanisms, contribute to their smooth operation. This reduces the risk of transaction errors, jams, or other issues that could hinder revenue collection.
Compliance with Safety and Health Regulations
Vending machines must adhere to safety and health regulations to protect both customers and operators. Regular maintenance helps identify and address potential safety hazards, ensuring compliance with relevant standards and regulations.
Why is Vending Machine Maintenance Important?
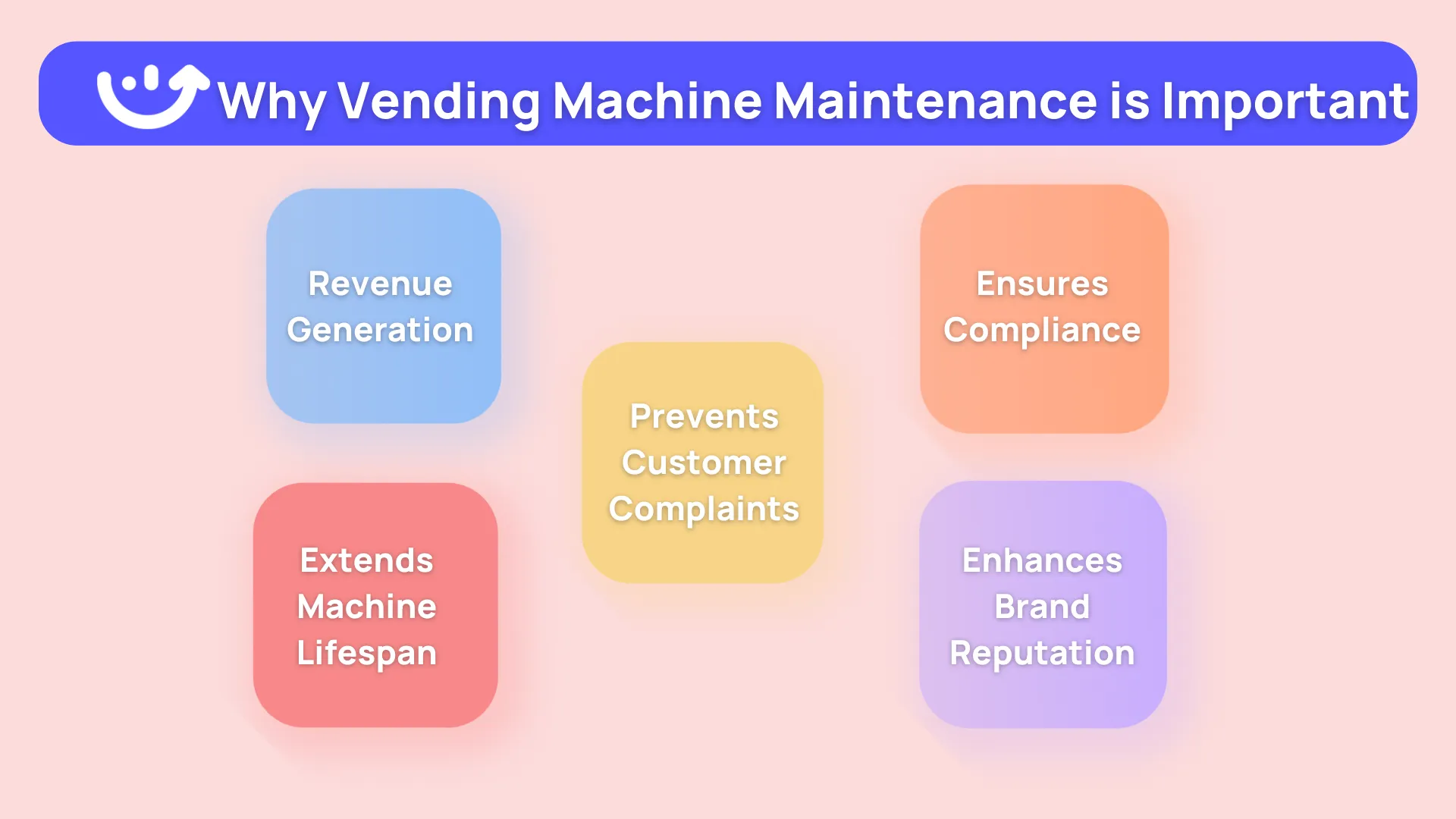
Vending machine maintenance is crucial for ensuring that vending machines operate at their best, delivering optimal performance and satisfying customers. By implementing regular maintenance practices, maintenance managers can unlock a variety of benefits that have a direct impact on the success of their business.
Let's explore why vending machine maintenance is so important:
Maximizes Machine Uptime and Revenue Generation
Well-maintained machines are less prone to breakdowns, ensuring consistent service and revenue generation. Unplanned downtime can lead to missed sales opportunities and customer dissatisfaction.
Prevents Customer Complaints
Functional vending machines with well-stocked inventory create a positive customer experience. On the other hand, malfunctioning machines or out-of-stock items can frustrate customers and damage the brand's reputation.
Ensures Compliance with Safety Regulations and Standards
Compliance with safety regulations is crucial to safeguard customers and maintain a secure operating environment. Regular maintenance helps identify potential safety hazards, allowing prompt corrective actions.
Reduces Repair Costs and Extends Machine Lifespan
Proactive maintenance practices can identify minor issues before they escalate into major problems. Addressing maintenance needs promptly reduces the risk of costly repairs and extends the lifespan of vending machines.
Enhances Brand Reputation
Maintaining well-functioning vending machines reinforces positive customer experiences, fosters brand loyalty, and contributes to a favorable reputation in the market.
Common Challenges in Vending Machine Maintenance
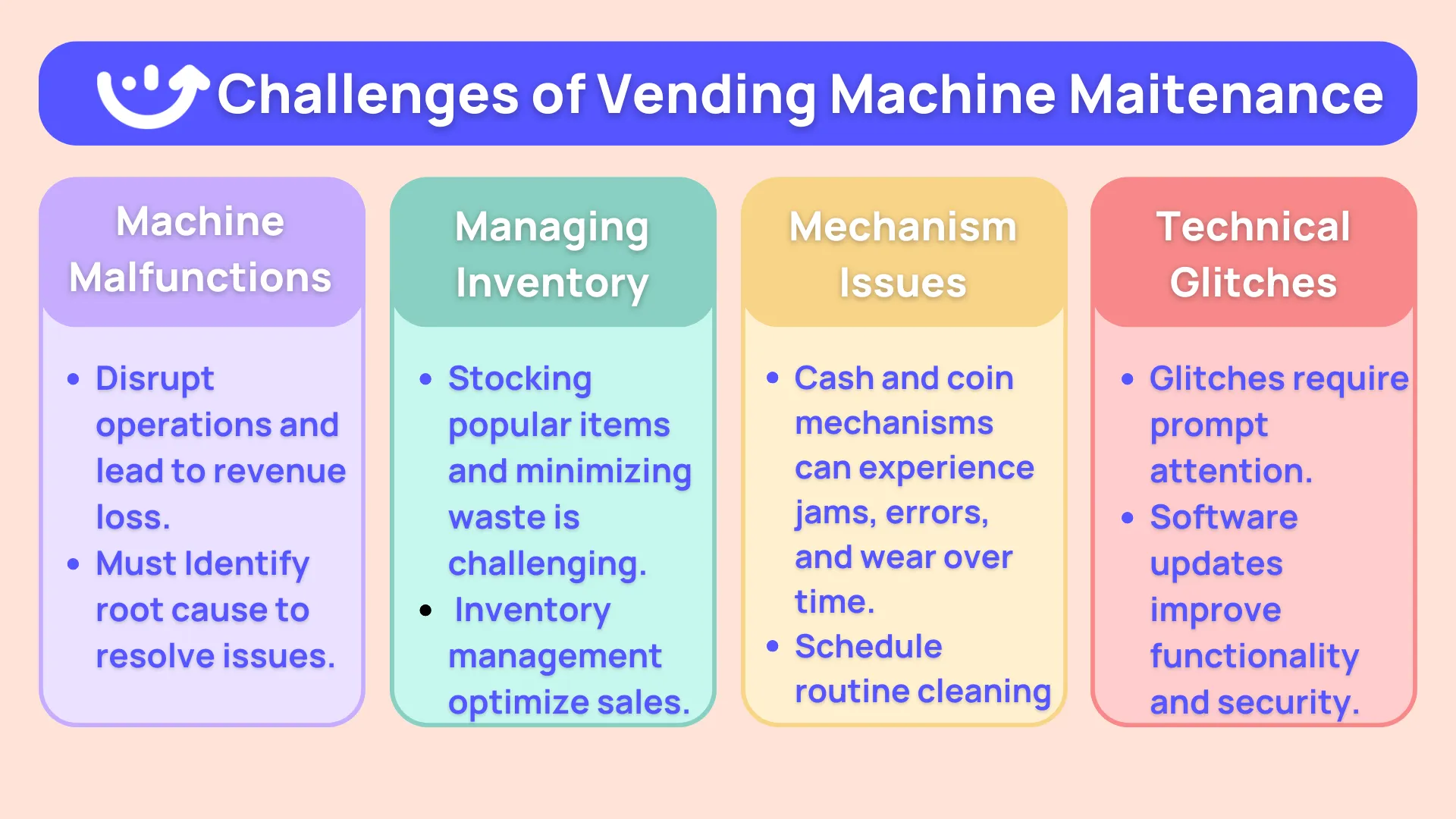
Maintenance managers often encounter specific challenges when it comes to vending machine maintenance.
These challenges can disrupt operations and lead to revenue loss. It is crucial for managers to identify the root causes of these issues and implement preventive maintenance measures to minimize their impact.
Some common challenges include:
Machine Malfunctions and Downtime
Unexpected breakdowns and malfunctions can disrupt operations and result in revenue loss. Identifying the root causes of these issues and implementing preventive maintenance measures is crucial.
Managing Inventory and Stock Levels
Ensuring that vending machines are well-stocked with popular items while minimizing waste and spoilage can be challenging. Effective inventory management practices are essential to optimize sales and reduce costs.
Cash and Coin Mechanism Issues
Cash and coin mechanisms are susceptible to jams, transaction errors, and wear over time. Regular maintenance and cleaning are necessary to keep these mechanisms in optimal condition.
Technical Glitches and Software Updates
Vending machines may encounter technical glitches or require software updates for improved functionality and security. Staying on top of software updates and addressing technical issues promptly is crucial for maintaining smooth operations.
How to Implement Effective Vending Machine Maintenance
Implementing an effective vending machine maintenance program involves several key steps to ensure the smooth operation, reliability, and longevity of the machines.
By following these steps, maintenance managers can minimize downtime, optimize revenue generation, and provide exceptional service to customers.
Let's explore the essential steps for implementing an effective vending machine maintenance program and reaping the benefits it brings to your business:
Develop a Preventive Maintenance Program
Create a comprehensive preventive maintenance plan that includes regular inspections, cleaning schedules, lubrication of moving parts, and calibration of sensors. Define maintenance tasks, frequencies, and responsibilities. Train your maintenance personnel on proper vending machine maintenance procedures, safety protocols, and troubleshooting techniques. Offer ongoing support and training to your staff.
Conduct Regular Inspections
Perform routine inspections to identify potential issues, such as damaged components, loose connections, or signs of wear. Address these issues promptly to prevent further damage and avoid breakdowns.
Establish Cleaning and Sanitization Guidelines
Develop cleaning and sanitization procedures tailored to your vending machines. Regularly clean surfaces, buttons, coin slots, and bill acceptors. Use appropriate sanitizing agents to maintain a hygienic environment.
Optimize Inventory Management
Implement inventory management practices to ensure that vending machines are consistently stocked with popular items. Monitor sales trends, restock inventory regularly, and rotate perishable items to minimize waste.
Maintain Cash and Coin Mechanisms
Regularly inspect and clean cash and coin mechanisms to prevent jams and ensure accurate transactions. Follow manufacturer guidelines for lubrication and maintenance of these components.
Ensure Software Updates and Technical Support
Stay up-to-date with vending machine software updates provided by the manufacturer. Regularly check for firmware updates, security patches, and bug fixes. Establish a relationship with technical support to address any issues promptly.
How Digital Tools Optimize Vending Machine Maintenance
The evolution of digital tools has brought significant advancements in vending machine maintenance management. These tools have transformed maintenance operations by streamlining processes, enhancing efficiency, and providing valuable insights. Let's explore how these digital tools optimize vending machine maintenance:
Streamlining Maintenance Operations
Digital tools provide a centralized platform for managing maintenance tasks, schedules, and documentation. This streamlines workflows and ensures that maintenance activities are completed efficiently and on time.
Centralized Asset Management
With digital tools, maintenance managers can keep track of their vending machine fleet, including locations, specifications, and maintenance history. This centralized view enhances visibility and simplifies asset management.
Preventive Maintenance Scheduling
Digital tools automate preventive maintenance scheduling, ensuring that tasks are assigned and completed as planned. They send reminders and notifications to maintenance personnel, reducing the risk of missed maintenance activities.
Real-time Monitoring and Alerts
Digital tools offer real-time monitoring capabilities, allowing maintenance managers to track vending machine health, performance, and inventory levels. They send alerts and notifications for proactive maintenance interventions, enabling timely actions.
Inventory Tracking and Reordering
Digital tools facilitate inventory management by tracking inventory levels in real-time. They generate automated alerts when stock levels reach a predefined threshold, streamlining the reordering process and ensuring optimal inventory management.
Why Use Xenia for Vending Machine Maintenance Management?
.webp)
Xenia, a powerful maintenance software, leverages various tools across desktop and mobile platforms to optimize vending machine maintenance. Here are the key features that make Xenia an exceptional choice for managing vending machine maintenance:
Operations Template Library and Builder
Xenia provides an Operations Template Builder that allows users to create customized checklists, forms, logs, SOPs, inspections, meeting agendas, and more. It offers different response types, including checkboxes, pass/fail, text input, number input, temperature, length, weight, and multiple choice.
The Operations Template Library consists of a wide range of ready-to-use templates, enabling users to save time and easily customize inspections, SOPs, checklists, and logs to suit their specific needs. These templates can be completed as stand-alone or attached to tasks or work orders, providing guidance and data collection.
Task and Work Order Management
Xenia's task and work order management feature allows users to assign tasks to teams or individuals quickly. Users can categorize tasks based on cleaning, repair, inspection, work order, and more, specify task locations, and associate assets related to the task. Additional details such as priority, start date, due date, and recurring tasks can be set.
Task and Work Order Scheduling
With Xenia, users can effortlessly create recurring tasks and work orders, all within minutes. These scheduled items can be unified into a single digital calendar, providing a filtered view based on a detailed task category. Users can assign these tasks to teams or individuals, attach templates and additional details, and require images for accountability.
Messaging & Chats
Users can send company-wide announcements, messages to teams or individuals, and even communicate within specific tasks to collaborate or seek assistance. Additionally, Xenia offers an employee directory that provides comprehensive data on every staff member, enhancing internal communication and collaboration.
Reports and Analytics
Xenia offers a cloud-based record archive that serves as a valuable resource for audits, compliance, and management reports. Users can easily organize and export reports based on various details such as priority, location, category, status, and assignee. Reports can be exported as PDF or CSV files, allowing for further analysis and presentation.
.webp)
%201%20(1).webp)