A Six Sigma root cause analysis is the long-term solution your business needs for quality management. Statistics and data analytics drive the methodology behind this approach that will get to the root of the problem.
Frontline workers and business owners alike strive for increased quality production. Of course, without defects or faulty products, profit is bound to increase. This means a better product for sales and less overhead spent on repairing, remaking, or returning products.
Priced on per user or per location basis
Available on iOS, Android and Web
However, this process isn’t always easy. Not being able to get to the core of an issue can frustrate anyone, especially when customer service’s telephone is ringing off the hook. Finding a quick fix might sound like the best option, but riddling workers with the anxiety of another subsequent collapse will not fare well with staff.
A Six Sigma root cause analysis will give your business the organizational tools to identify the cause of the problem and prevent it from ever happening again.
Recommended Resources:
- 5 Best Quality Control Checklist Apps For Businesses In 2024
- 10 Best ISO 9001 QMS Software in 2024
- Maintenance Management Software
- 10 Best Software For Writing Procedures
What is Six Sigma?
Developed in the 80s to improve machinery processes, Six Sigma quickly became the new corporate fad. According to Forbes magazine, more than half of all Fortune 500 companies have adopted six sigma practices within the past twenty years. This investment saved these businesses a whopping $427 billion.
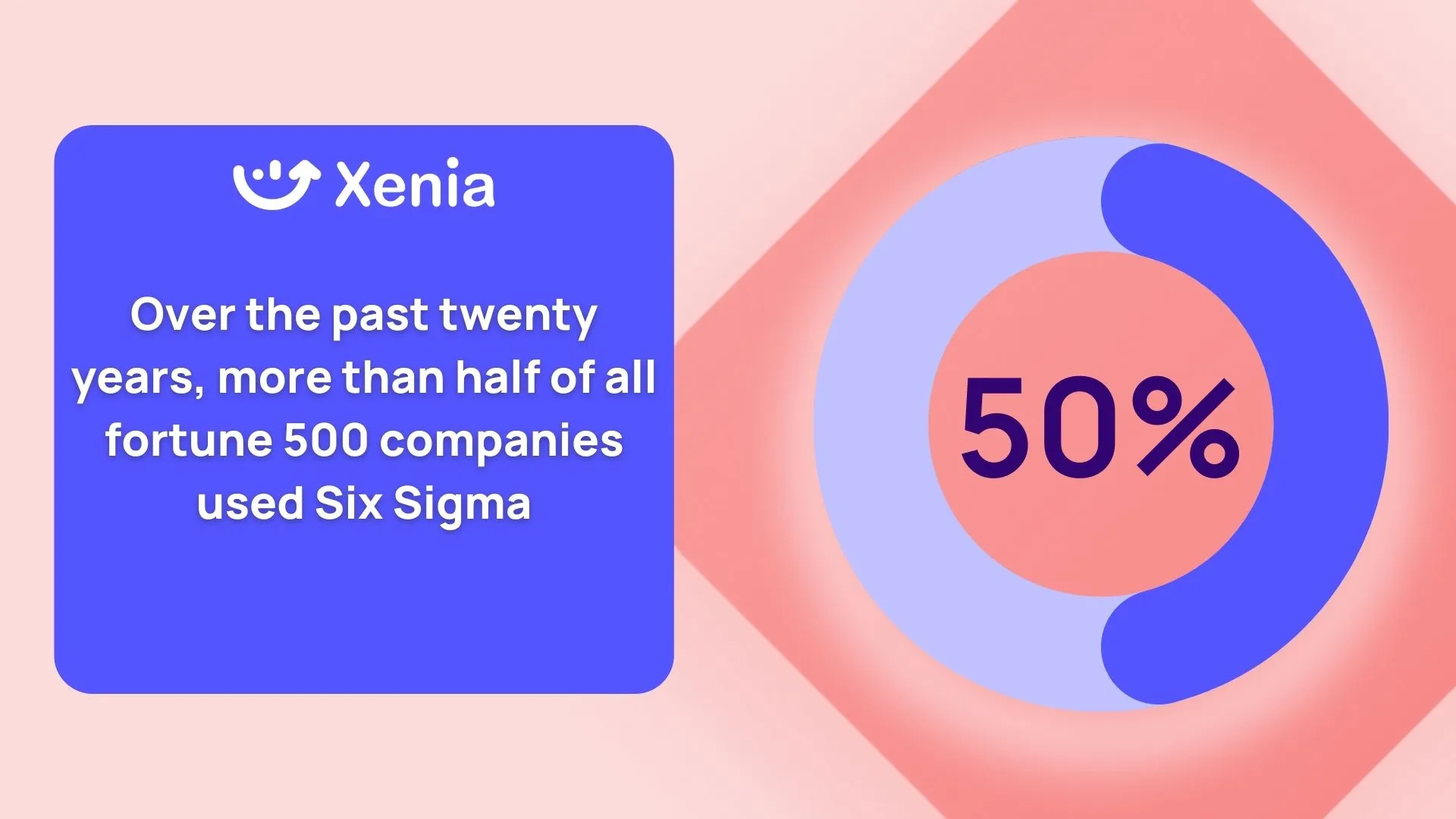
So then, what is with all the hype?
Six Sigma is a managerial-driven scientific approach to reducing defects and waste while increasing high-quality output. This profit-driven methodological undertaking provides verified certifications through a belt system similar to karate.
Six Sigma Belt Levels Explained
Six Sigma is an advanced method of analyzing business processes to reach the desired outcome. Understandably, a significant corporation would want to work with someone proficient in statistics and problem-solving.
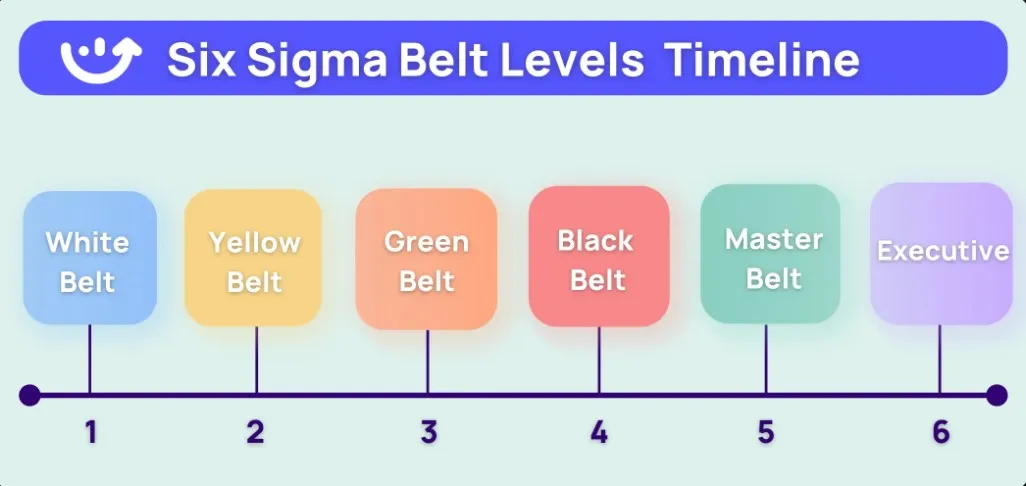
It’s easy to understand why universities around the globe began providing accredited courses on six sigma training. Such as Purdue University offering six-week online courses to achieve individual belt rankings. The jobs are out there.
Let’s review each belt and what they represent professionally.
◻️ White Belt
This is the entry-level Six Sigma belt. White belts are typically team members who are not directly involved in the implementation of Six Sigma, but who need to understand the methodology and how it is used in their organization. A white belt in Six Sigma training represents no formal training or certification. However, this belt provides a project framework for quality control and waste management. A Six Sigma White Belt should take on the following responsibilities:
- Understand the basic principles and concepts of Six Sigma, including the DMAIC (Define, Measure, Analyze, Improve, Control) methodology and the use of statistical analysis to identify and eliminate defects
- Participate in Six Sigma training and development programs as needed
- Support Six Sigma projects and initiatives by providing data, assisting with process mapping, and participating in process improvement activities
- Understand the role of Six Sigma in the organization and how it fits into the overall business strategy
- Understand the role of other Six Sigma belt levels and how they contribute to the implementation and success of Six Sigma projects
- Be able to communicate effectively with team members and stakeholders about Six Sigma concepts and practices
- Continuously improve personal skills and knowledge related to Six Sigma and process improvement.
🟨 Yellow Belt
Six Sigma yellow belts have professional training through working with managers with higher belts. Yellow belts are typically team members who are responsible for identifying and supporting the implementation of Six Sigma projects. They may also be responsible for collecting and analyzing data, identifying improvement opportunities, and participating in Six Sigma training. A Six Sigma Yellow Belt should take on the following responsibilities:
- Use Six Sigma tools and techniques, such as process mapping, root cause analysis, and data collection and analysis, to identify and prioritize improvement opportunities
- Participate in problem-solving teams and contribute to the development of solutions to improve business processes
- Support the implementation of Six Sigma projects by providing data, assisting with process mapping, and participating in process improvement activities
- Contribute to the development of performance metrics and monitoring systems to track progress and measure the success of Six Sigma projects
- Understand and adhere to the Six Sigma methodology and project management principles, including the use of project charters and other project management tools
- Support the development and implementation of Six Sigma training programs and materials within the organization.
🟩 Green Belt
Green belts are responsible for leading and managing Six Sigma projects. They work closely with black belts to identify and prioritize improvement opportunities, collect and analyze data, and implement solutions. Green belts also play a key role in coaching and mentoring other team members in the use of Six Sigma tools and techniques. When you achieve a green belt in Six Sigma training, your professional rap sheet showcases that you have completed accredited training for techniques around process improvements.
- Identifying and prioritizing process improvement opportunities within the organization.
- Leading process improvement teams and facilitating the use of Six Sigma tools and techniques to analyze and optimize processes.
- Collecting and analyzing data to identify root causes of problems and develop solutions.
- Implementing and monitoring process changes to ensure that they are effective and sustainable.
- Communicating the results and benefits of process improvement efforts to stakeholders.
- Providing training and support to team members in the use of Six Sigma tools and techniques.
- Participating in the development of Six Sigma strategies and initiatives within the organization.
⬛ Black Belt
Six Sigma Black Belts are individuals who have advanced training and expertise in the Six Sigma methodologies and tools, and are responsible for leading and managing Six Sigma improvement projects within their organization. They are typically experienced Six Sigma practitioners who have demonstrated a strong understanding of the Six Sigma principles and have successfully completed a number of improvement projects.
The time it takes to become a Six Sigma Black Belt can vary depending on the specific training program and the individual's prior experience and knowledge. Some Six Sigma Black Belt training programs can take as little as four weeks to complete, while others may take several months or longer. In addition to formal training, Six Sigma Black Belts typically have a significant amount of practical experience applying Six Sigma principles and tools to real-world situations, and may have completed a number of improvement projects before being certified as a Black Belt.
As a Six Sigma Black Belt, some specific responsibilities may include:
- Leading and managing Six Sigma improvement projects from start to finish.
- Mentoring and coaching Six Sigma Green Belts and other team members.
- Collaborating with senior leadership to develop and implement Six Sigma strategies and initiatives.
- Facilitating the use of Six Sigma tools and techniques to identify and prioritize process improvement opportunities, collect and analyze data, and develop and implement solutions.
- Communicating the results and benefits of Six Sigma improvement efforts to stakeholders.
- Providing training and support to team members in the use of Six Sigma tools and techniques.
- Participating in the continuous improvement of Six Sigma processes and practices within the organization.
🏆 Master Belt
Six Sigma Master Black Belts are highly skilled professionals who have undergone advanced training in Six Sigma methodologies and tools. They lead and manage complex improvement projects within their organization, utilizing Six Sigma principles to identify and prioritize process improvement opportunities, collect and analyze data, and develop and implement effective solutions. Master belt holders are considered experts in Six Sigma. Typically, these individuals have been practicing Six Sigma for years and are the go to people for operational wisdom.
In addition to their project management responsibilities, Six Sigma Master Black Belts also serve as mentors and coaches for Black Belts and other team members, providing guidance and support in the use of Six Sigma tools and techniques. They work closely with senior leadership to develop and implement Six Sigma strategies and initiatives, and contribute to the continuous improvement of processes and practices within the organization.
For example, a Six Sigma Master Black Belt may lead a team to identify and resolve bottlenecks in a manufacturing process, resulting in increased efficiency and reduced waste. They may also provide training to Black Belts and other team members on how to use Six Sigma tools such as process maps and root cause analysis to identify and address problems within their own processes. Overall, Six Sigma Master Black Belts play a critical role in driving process improvement and driving organizational success.
Final Note on Six Sigma Belts
It is worth noting that the Six Sigma belt levels are not universally recognized or standardized, and the specific roles and responsibilities associated with each belt may vary from one organization to another. It is difficult to determine exactly how many Six Sigma Belts there are globally, as there are many different organizations and training programs that offer Six Sigma certification. However, Six Sigma is a widely recognized and respected methodology for improving business processes, and it is likely that there are many thousands of Six Sigma Black Belts globally.
Each of these belt certifications will utilize the same Six Sigma methodology. This methodology theorizes that, within every business, there is a predictable process to achieve success.
For this to be true, these procedures must be data-driven. Six Sigma’s data-driven strategy is known as DMAIC. Additionally, integrating ISO 9001 software into your quality management system can complement Six Sigma practices, aligning with the DMAIC framework for enhanced quality and efficiency. Let’s dive into the meaning of this acronym.
The Six Sigma DMAIC Process
DMAIC is a Six Sigma methodology that stands for Define, Measure, Analyze, Improve, and Control. It is a structured approach for improving processes and is designed to help organizations identify and solve problems, reduce variability, and increase efficiency. Every letter in DMAIC represents a phase of Six Sigma. Each stage is integral to the quality management process and will be explored in the earliest belt certification.
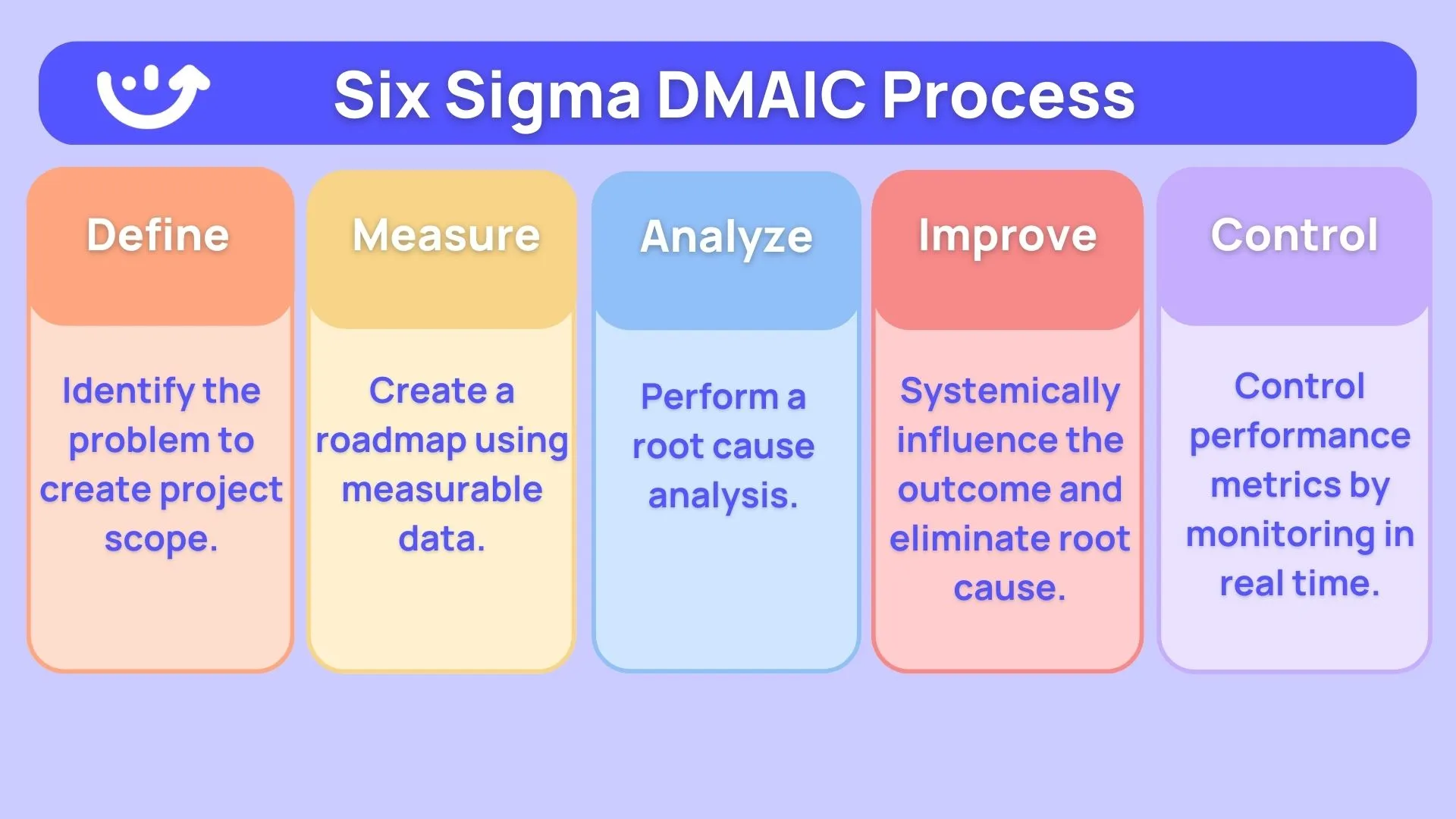
📖 Define
The Define phase of the DMAIC process is the first phase of the Six Sigma methodology and is focused on clearly defining the problem or opportunity to be addressed, as well as the goals and objectives for the improvement project.
During the Define phase, it is important to clearly understand the current state of the process and the specific problems or issues that need to be addressed. This may involve collecting and analyzing data to understand the current performance of the process and identifying areas for improvement.
🔑 Define the problem, but spend more time defining the goals and objectives for correcting the problem
In addition to defining the problem or opportunity, the Define phase also involves setting clear goals and objectives for the improvement project. This may include defining specific performance targets or metrics that will be used to measure the success of the project.
It is also important to identify the stakeholders who will be impacted by the improvement project and to ensure that their needs and concerns are taken into account. This may involve engaging with stakeholders to understand their perspectives and to gather input and feedback on the improvement project.
Overall, the Define phase is critical for establishing a clear direction for the improvement project and for ensuring that the project is aligned with the broader goals and objectives of the organization.
📐 Measure
The Measure phase of the DMAIC process is the second phase of the Six Sigma methodology and is focused on collecting and analyzing data to understand the current state of the process and identify areas for improvement.
During the Measure phase, it is important to gather data that accurately reflects the performance of the process and to ensure that the data is properly collected and analyzed. This may involve using tools such as process maps and flowcharts to understand the steps and inputs involved in the process, as well as using statistical analysis techniques to identify patterns and trends in the data.
🔑 All measurements should be compared to a baseline measurement for context
It is also important to establish baseline measures of process performance and to define specific performance targets or metrics that will be used to assess the success of the improvement project. This may involve setting targets for process performance indicators such as cycle time, defects, and customer satisfaction.
Overall, the Measure phase is critical for providing a clear understanding of the current state of the process and for identifying areas for improvement. By collecting and analyzing data in a structured and systematic way, organizations can gain insights into the root causes of problems and identify opportunities for improvement.
🔎 Analyze
The Analyze phase of the DMAIC process is the third phase of the Six Sigma methodology and is focused on identifying the root causes of problems or opportunities for improvement through the use of tools such as root cause analysis and process mapping.
During the Analyze phase, it is important to carefully review the data collected in the Measure phase and to use a variety of tools and techniques to identify the root causes of problems or opportunities for improvement. This may involve using statistical analysis techniques to identify patterns and trends in the data, or using process mapping techniques to understand the flow of the process and identify bottlenecks or points of variability.
🔑 Gather insight from different perspectives gain a wholistic view of the problem
It is also important to engage with stakeholders and subject matter experts to gather additional insights and perspectives on the root causes of problems or opportunities for improvement. By gathering a diverse range of inputs, organizations can gain a more complete understanding of the underlying issues and can develop more effective solutions.
Overall, the Analyze phase is critical for identifying the root causes of problems and for developing a clear understanding of the underlying issues that need to be addressed. By using a structured and systematic approach to identify root causes, organizations can develop targeted and effective solutions that address the root causes of problems rather than just the symptoms.
📈 Improve
The Improve phase of the DMAIC process is the fourth phase of the Six Sigma methodology and is focused on developing and implementing solutions to address the problems or opportunities for improvement identified in the Analyze phase.
During the Improve phase, it is important to develop a range of potential solutions and to carefully evaluate the pros and cons of each option. This may involve using tools such as design of experiments to test and validate different solutions, or engaging with stakeholders and subject matter experts to gather additional insights and perspectives.
🔑 Iteration is essential for continuous improvement, build systems to test and learn
Once a solution has been selected, it is important to carefully plan and execute the implementation of the solution. This may involve developing implementation plans, training team members, and establishing controls to ensure that the solution is effective and sustainable.
It is also important to monitor the results of the improvement efforts and to make adjustments as needed to ensure that the solution is meeting the desired performance targets. By continuously monitoring and adjusting the solution, organizations can ensure that the improvements are effective and sustainable.
Overall, the Improve phase is critical for developing and implementing solutions to address the root causes of problems and for driving continuous improvement within the organization. By using a structured and systematic approach to identify and implement solutions, organizations can drive meaningful and lasting improvements in their processes and performance.
🤖 Control
The Control phase of the DMAIC process is the fifth and final phase of the Six Sigma methodology and is focused on ensuring that the improvements made during the Improve phase are sustainable and effective.
During the Control phase, it is important to establish controls to ensure that the improvements are maintained over time. This may involve implementing process controls, such as checklists or standard operating procedures, to ensure that the improvements are consistently applied.
🔑 Controlling variables is the only way to know if your intervention is the cause of improvement
It is also important to continuously monitor the results of the improvement efforts and to make adjustments as needed to ensure that the improvements are meeting the desired performance targets. This may involve collecting and analyzing data to understand the ongoing performance of the process and identifying any areas for further improvement.
By continuously monitoring and adjusting the improvements, organizations can ensure that the benefits of the improvement project are sustained over time.
Overall, the Control phase is critical for ensuring that the improvements made during the DMAIC process are sustainable and effective. By establishing controls and continuously monitoring and adjusting the improvements, organizations can drive continuous improvement and ensure that the benefits of the DMAIC process are sustained over time.
Final Note on DMAIC
The analytical phase is often the most critical and time-consuming phase of a Six Sigma root cause analysis. This can take many forms within a team structure. Many teams prefer discussion, while others prefer diagram-making. In the context of maintaining operational efficiency, adopting maintenance management software can play a crucial role in ensuring equipment and processes are functioning optimally, thereby supporting Six Sigma objectives.
Let’s look at how a root cause analysis (RCA) can function within the analysis phase of Six Sigma. To enhance the effectiveness of this phase, employing quality control apps can offer structured and efficient ways to document, track, and analyze quality issues.
What Is Six Sigma Root Cause Analysis?
A Six Sigma root cause analysis is a crucial element of the problem-solving process. Most problems in life are just like the structure of a plant. If you don’t pull out the entire root, you can expect the weeds to keep growing.
This is the same for a Six Sigma root cause analysis. If a proposed solution does not go through a hypothesis test, you’re just putting a Band-Aid on a wound. Luckily, there are tools to make this technique easier.
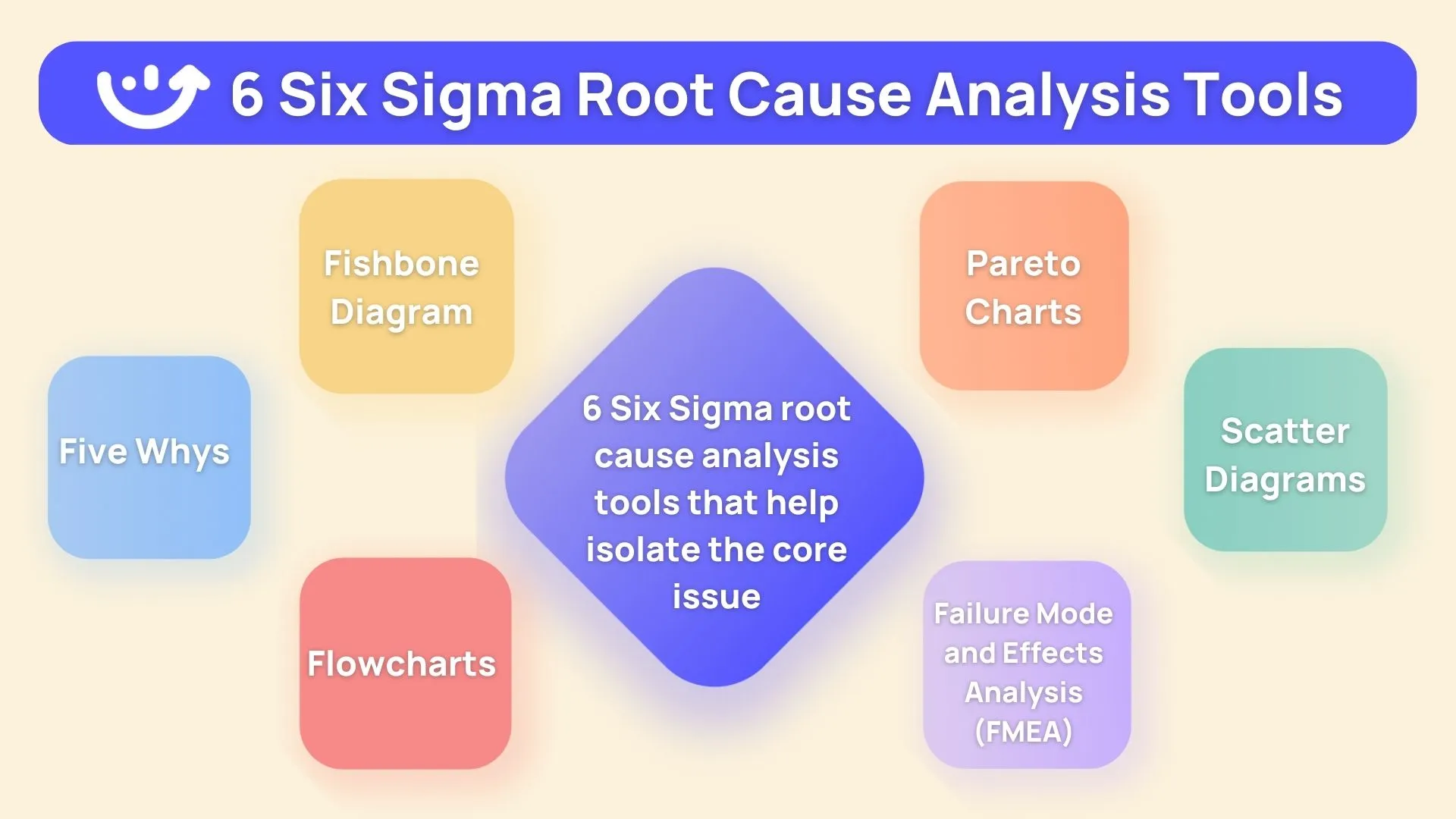
6 Tools for Six Sigma Root Cause Analysis
Here are 6 Six Sigma root cause analysis tools that help isolate the core issue.
🐟 Fishbone Diagram
Fishbone diagrams, also known as cause and effect diagrams or Ishikawa diagrams, are a tool used in Six Sigma and other process improvement methodologies to identify the root causes of problems. To document and refine these analyses, leveraging procedure software can help in creating detailed procedures and ensuring that improvements are accurately captured and implemented.
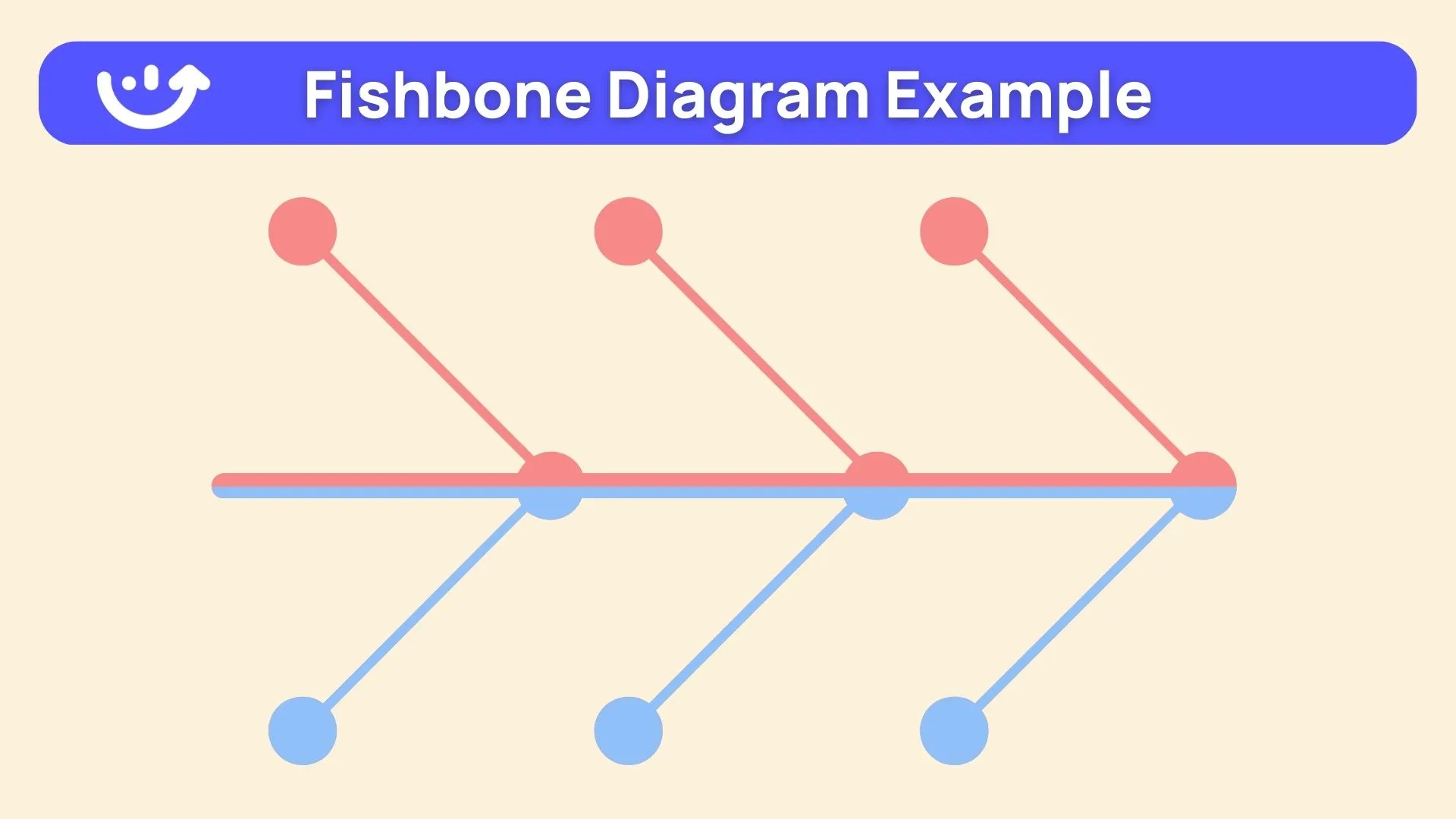
Some reasons why fishbone diagrams are effective at root cause analysis include:
- They help to identify all possible contributing factors: Fishbone diagrams allow organizations to identify and consider all possible contributing factors to a problem, rather than just focusing on the most obvious or immediate causes. This helps to identify more complex or underlying causes that may not be immediately apparent.
- They help to organize and structure the analysis: Fishbone diagrams provide a structured and systematic approach to root cause analysis, helping organizations to clearly organize and understand the various contributing factors to a problem.
- They help to facilitate team involvement: Fishbone diagrams can be used in team-based problem-solving efforts, allowing all team members to contribute their ideas and insights to the root cause analysis process.
- They can be used to identify patterns and trends: By organizing and analyzing data in a fishbone diagram, organizations can identify patterns and trends that may not be immediately apparent in raw data, helping to identify root causes more effectively.
Overall, fishbone diagrams are a useful tool for identifying the root causes of problems and for driving continuous improvement within an organization.
❓ Five Whys
Five Whys analysis is a tool used in Six Sigma and other process improvement methodologies to identify the root causes of problems by repeatedly asking "why" a problem occurred.
Some reasons why Five Whys analysis is effective at root cause analysis include:
- It helps to identify underlying causes: By repeatedly asking "why," Five Whys analysis helps organizations to dig deeper and identify the root causes of problems, rather than just focusing on the most obvious or immediate causes.
- It helps to facilitate team involvement: Five Whys analysis can be used in team-based problem-solving efforts, allowing all team members to contribute their ideas and insights to the root cause analysis process.
- It can be used to identify patterns and trends: By repeatedly asking "why" and organizing and analyzing data, organizations can identify patterns and trends that may not be immediately apparent in raw data, helping to identify root causes more effectively.
- It is simple and straightforward: Five Whys analysis is a simple and straightforward approach to root cause analysis that can be easily understood and applied by team members with a wide range of backgrounds and expertise.
Overall, Five Whys analysis is a useful tool for identifying the root causes of problems and for driving continuous improvement within an organization. By repeatedly asking "why," organizations can gain a deeper understanding of the underlying causes of problems and develop targeted and effective solutions.
↔️ Flow Charts
Flow charts are diagrams that show the flow of processes or systems, and are often used in Six Sigma and other process improvement methodologies to understand and improve processes.
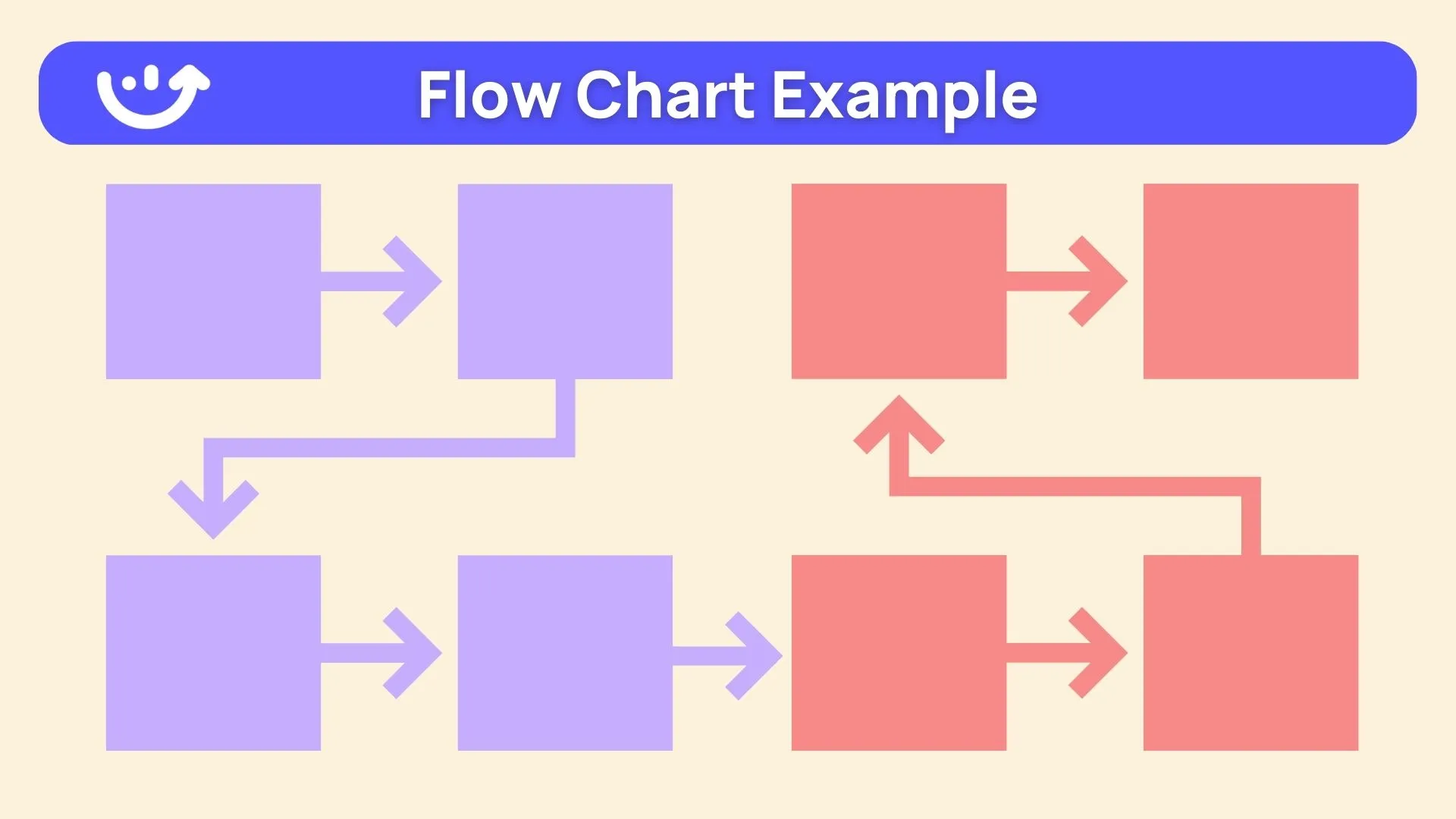
Some reasons why flow charts are effective in process improvement include:
- They help to visualize the process: Flow charts provide a visual representation of the steps and inputs involved in a process, making it easier for organizations to understand and analyze the process.
- They help to identify bottlenecks and points of variability: By visualizing the flow of the process, flow charts can help organizations to identify bottlenecks and points of variability that may be impacting the efficiency and effectiveness of the process.
- They can be used to facilitate team involvement: Flow charts can be used in team-based problem-solving efforts, allowing all team members to contribute their ideas and insights to the process improvement process.
- They can be used to document and communicate process improvements: Flow charts can be used to document and communicate process improvements, helping to ensure that the improvements are understood and consistently applied.
Overall, flow charts are a useful tool for understanding and improving processes, and can help organizations to drive continuous improvement and increase efficiency and effectiveness.
🥅 Pareto Charts
A Pareto chart is a graphical tool that allows for the visualization and analysis of data in order to identify the most significant factors contributing to a particular problem or situation. It is often used in the field of quality control and continuous improvement to identify the root causes of problems and to prioritize actions based on their potential impact.
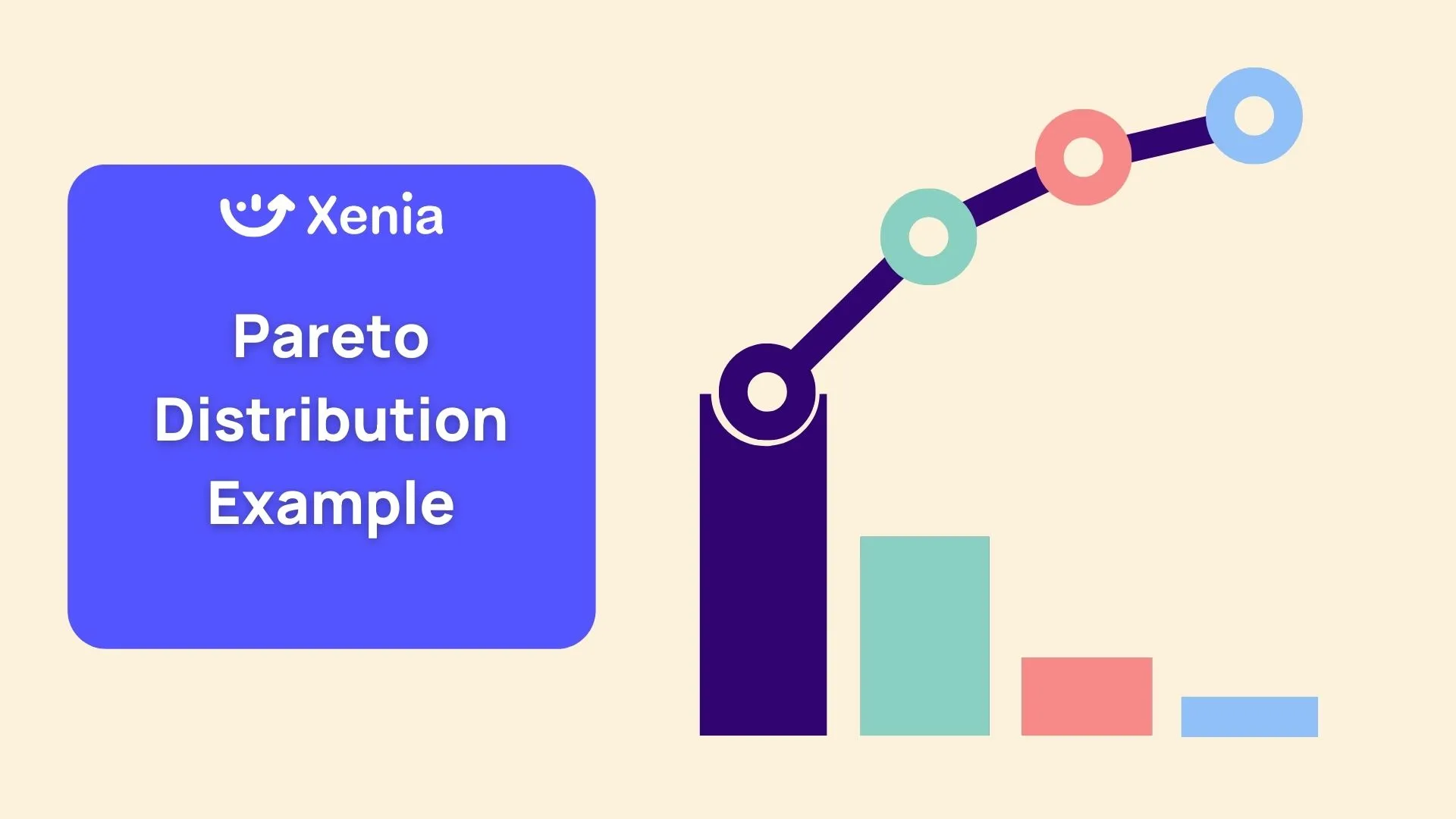
Here are some key points about Pareto charts and their use in root cause analysis:
- A Pareto chart consists of a bar graph that displays the frequency or occurrence of different factors (called "causes") on the y-axis, and the cumulative percentage of the total occurrence on the x-axis.
- The factors are typically arranged in descending order, so that the most significant factors are displayed at the left of the chart.
- The Pareto principle states that a small number of causes (often referred to as the "vital few") tend to contribute significantly to the overall problem or situation, while a larger number of causes (the "trivial many") contribute relatively little.
- By identifying the vital few causes, a Pareto chart can help to focus attention and resources on the most impactful areas, rather than addressing a large number of minor issues.
- Pareto charts can be used in a variety of situations, including identifying the most common defects in a manufacturing process, determining the most frequent causes of customer complaints, or identifying the most significant factors contributing to a business problem.
- To use a Pareto chart effectively, it is important to ensure that the data being analyzed is accurate and representative of the problem or situation being addressed. It is also important to take into account any potential biases or limitations in the data collection process.
📄 Scatter Diagrams
A scatter chart, also known as a scatter plot or scattergram, is a graphical tool that allows for the visualization and analysis of data in order to identify patterns and relationships between variables. It is often used in the field of statistical analysis and data visualization to understand the underlying causes of a particular phenomenon or problem.
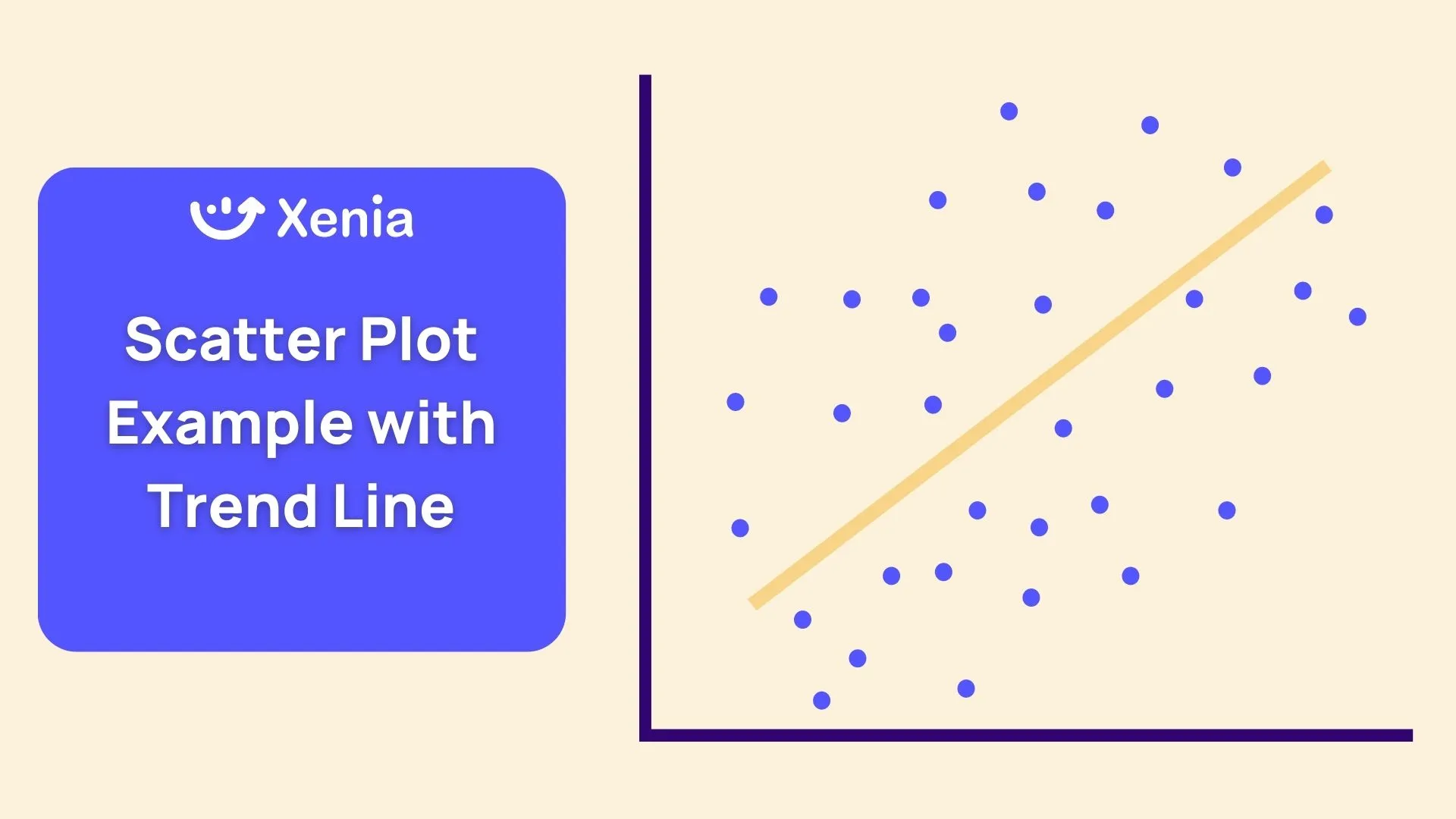
Here are some key points about scatter charts and their use in root cause analysis:
- Scatter charts are a visual tool that can be used in root cause analysis to identify the relationship between two variables.
- They can help to identify any trends or patterns in the data that could be contributing to the issue.
- Scatter charts can be used to determine if there is a correlation between two variables, or if there is a cause and effect relationship.
- When using scatter charts for root cause analysis, it is important to ensure that the data is accurate and complete.
- Scatter charts can be created using a variety of software tools, including Microsoft Excel and Minitab.
- In addition to identifying the root cause of a problem, scatter charts can also be used to monitor progress and evaluate the effectiveness of any corrective actions taken.
- It is important to interpret the data on a scatter chart correctly, as misinterpretation can lead to incorrect conclusions and ineffective solutions.
Operational software for a Six Sigma root cause analysis is the perfect response to anyone that doubts this process! Digital tools will only enhance your confidence in this comprehensive approach to quality management. You’ll s
.webp)
%201%20(1).webp)