Today's facilities managers need a vision for the future. How will things unfold in a few days or weeks? Can your maintenance process help you stay afloat?
Most of the time, facilities managers are reactive instead of proactive. They wait for a calamity to fall upon them rather than preparing for it beforehand. With a proper planned maintenance program in place, managers can have confidence that their business will run without costly interruption.
Priced on per user or per location basis
Available on iOS, Android and Web
What is Planned Maintenance?
The concept of planned maintenance is a part of an overall proactive maintenance strategy that a company needs to employ to reduce the likelihood of any downtime that can disrupt its general work operations.
A planned maintenance strategy is a broad category that encompasses all the different types of maintenance activities that can be done to prevent breakdowns. A planned maintenance strategy shows how and what will be done over time to maximize performance while ensuring that the machine is kept in good working order.
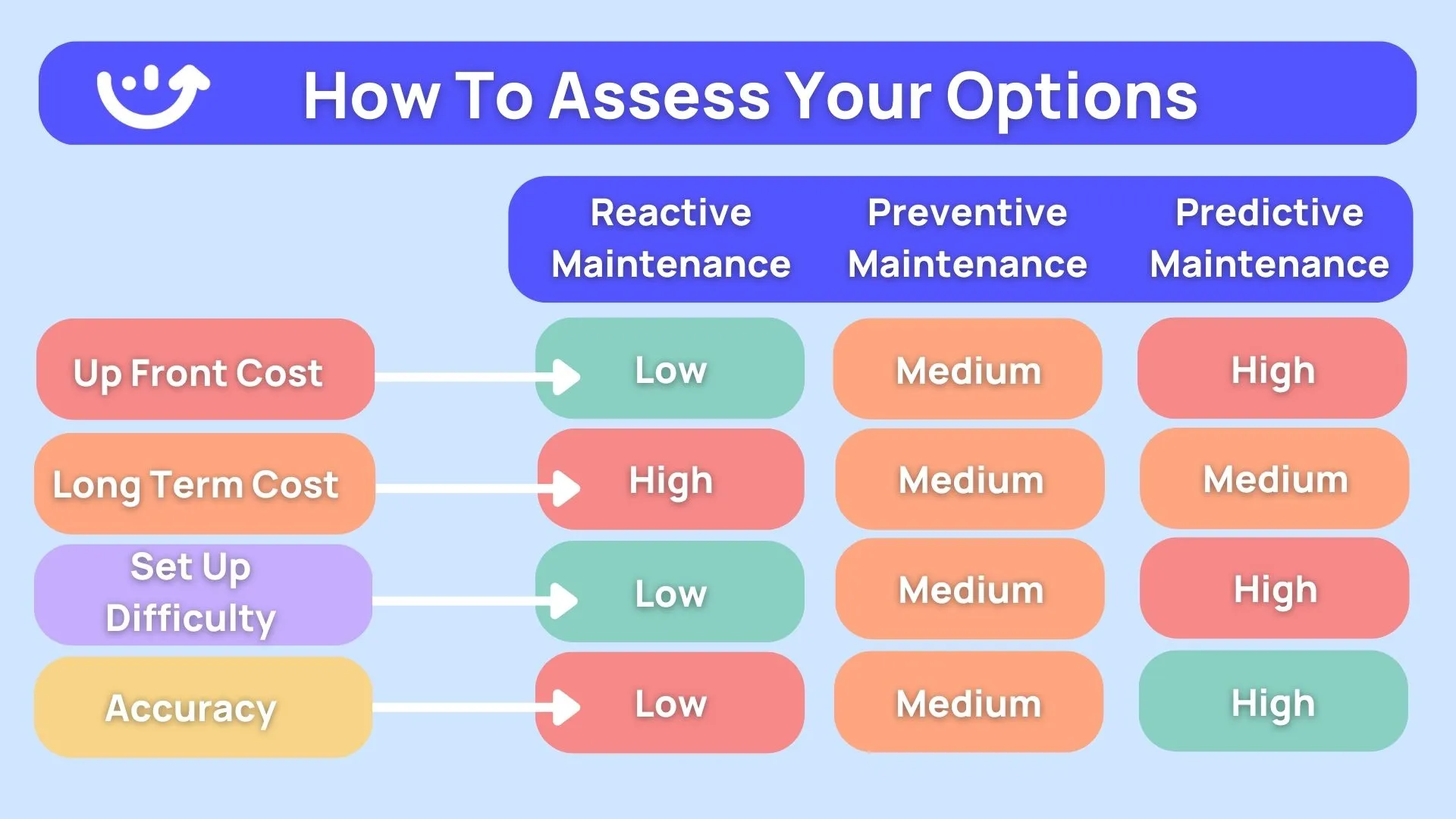
Preventive maintenance is a common type of planned maintenance, where each asset has regular inspections and upkeep such as lubrication or tightening of bolts.
If you have trouble understanding planned maintenance, think of it this way. When you buy a car from a dealership, they always give you suggestions and helpful recommendations about when or where you should get your car serviced. These are typically based on time in operation and the miles it has taken. This would be your preventive maintenance schedule for your car. However, there are many other reasons why you may plan maintenance on your vehicle. Maybe you regularly check your car's fluids and tire treads to ensure that it is in tip-top condition. Possibly you have regular car washes to provide protection to your paint. You may even schedule an extra check up before a road trip or take it in when you hear an odd noise from under the hood. This is all planned maintenance.
Importance of Planned Maintenance
Planned maintenance is critical to the health of your business assets. It provides opportunities to identify and correct signs of deterioration, damage or wear and tear that could cause equipment failure. This helps ensure that your equipment is functioning properly and optimally in the present and extend asset life beyond the predicted replacement date.
When mechanical breakdowns and unplanned outages occur in the middle of essential work processes, a company or organization can be affected in many ways. Loss of revenue, increased risk of injury, and unhappy customers are a few negative impacts that affect your bottom line. But in the end, downtime isn't the only indicator of lost productivity that can be prevented with proper maintenance.
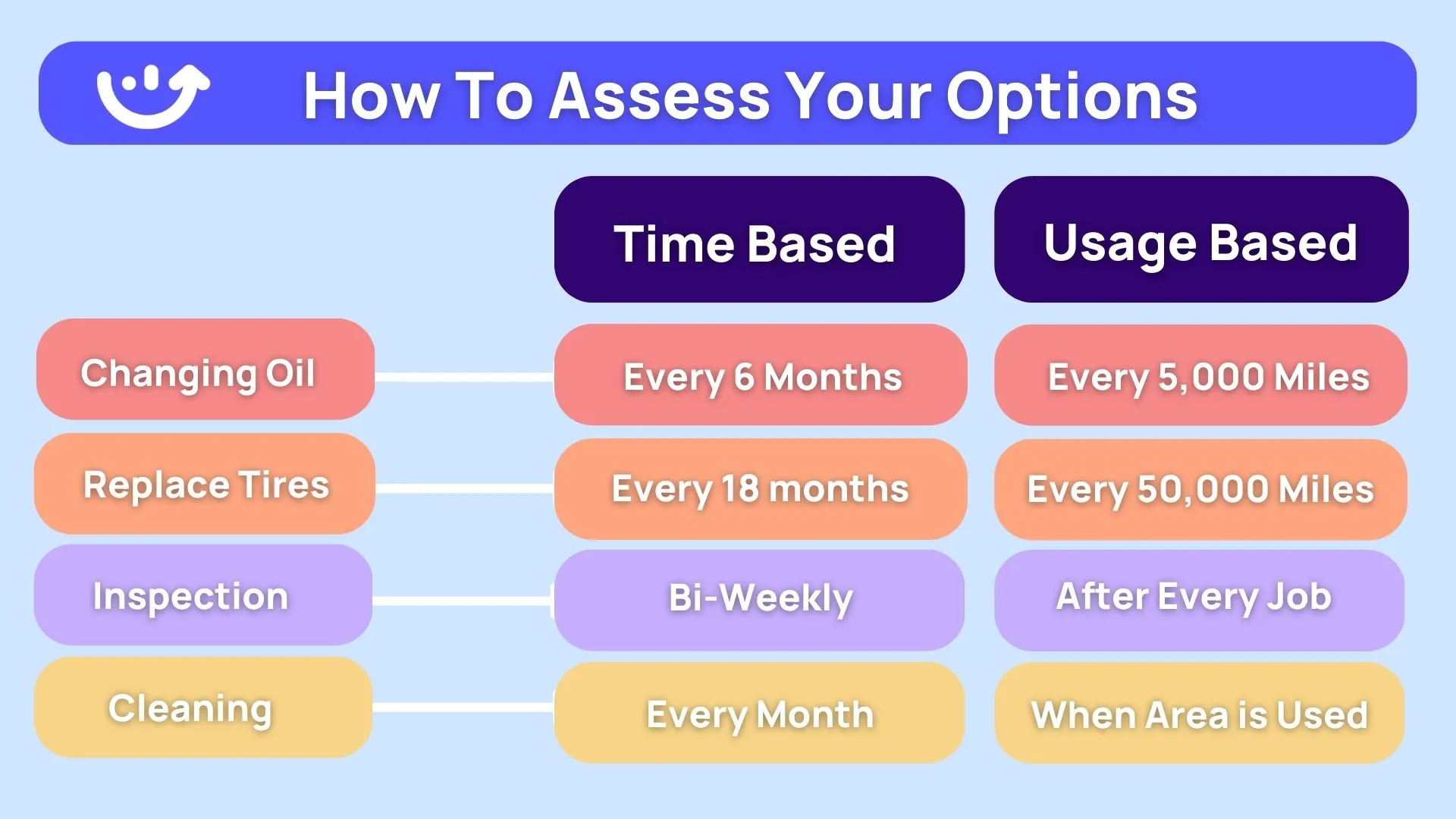
Equipment that is not properly maintained does not function at the highest possible level of efficiency. This inefficiency is compiled with assets that require human interaction to run. For example, a hotel laundry operation with old, poorly maintained driers will have longer run times in drying linens. Since laundry is loaded and removed by humans, their time spent on each load also rises. With 50% of hotel laundry costs coming from labor, inefficient machinery can directly threaten your bottom line.
Facilities managers worldwide need to employ a planned maintenance mindset to ensure that their workforce and the company have better productivity, increased morale, and reduced costs.
Dealing with down equipment is stressful on staff, damaging to reputation, and unreasonably costly. Service providers may be booked or parts may be unavailable causing prolonged downtime. These same pressures are likely to drive up prices due to increased demand and limited supply.
Let's now look at some of the benefits of planned maintenance that companies can enjoy If they employ this strategy.
3 Benefits of Planned Maintenance
1. Reduce Repair Costs
When a machine is not maintained regularly, the performance of the machine will deteriorate over time. This can result in more frequent breakdowns, longer downtimes and higher repair costs.
Repairs are expensive, and they can take your business down for days or weeks. Planned maintenance is a way of taking care of the problems that crop up in your equipment before they become big issues. By doing this, you can avoid needing to pay thousands of dollars to fix something that you could have fixed with a few hundred dollars' worth of parts.
2. Increase Asset Life
Regularly scheduled inspections and preventative maintenance are essential for ensuring that your equipment continues to function at its best throughout its lifetime. Greasing bearings, tightening bolts, and replacing damaged parts benefit the entire asset system, reducing risk of collateral damage from a part failure which contributes to an extension of asset life. By implementing planned maintenance, you can ensure that your assets are in good working order and able to perform their job as efficiently as possible.
Planned maintenance is a critical part of any organization's asset life management strategy. With the right asset data, managers can uncover which maintenance processes drive improvement in productivity and asset life.
3. Reduce Asset Downtime
When you don't plan for the future, you run the risk of having your assets break down when you need them most. This can be especially problematic if you're trying to generate revenue at a certain time of year, or if your business relies on a specific piece of equipment to function properly. Planning ahead will allow you to schedule maintenance at times when it won't affect your operations or revenue streams. This means that you won't find yourself in a position where an unexpected breakdown causes downtime that costs money or damages your reputation with customers.
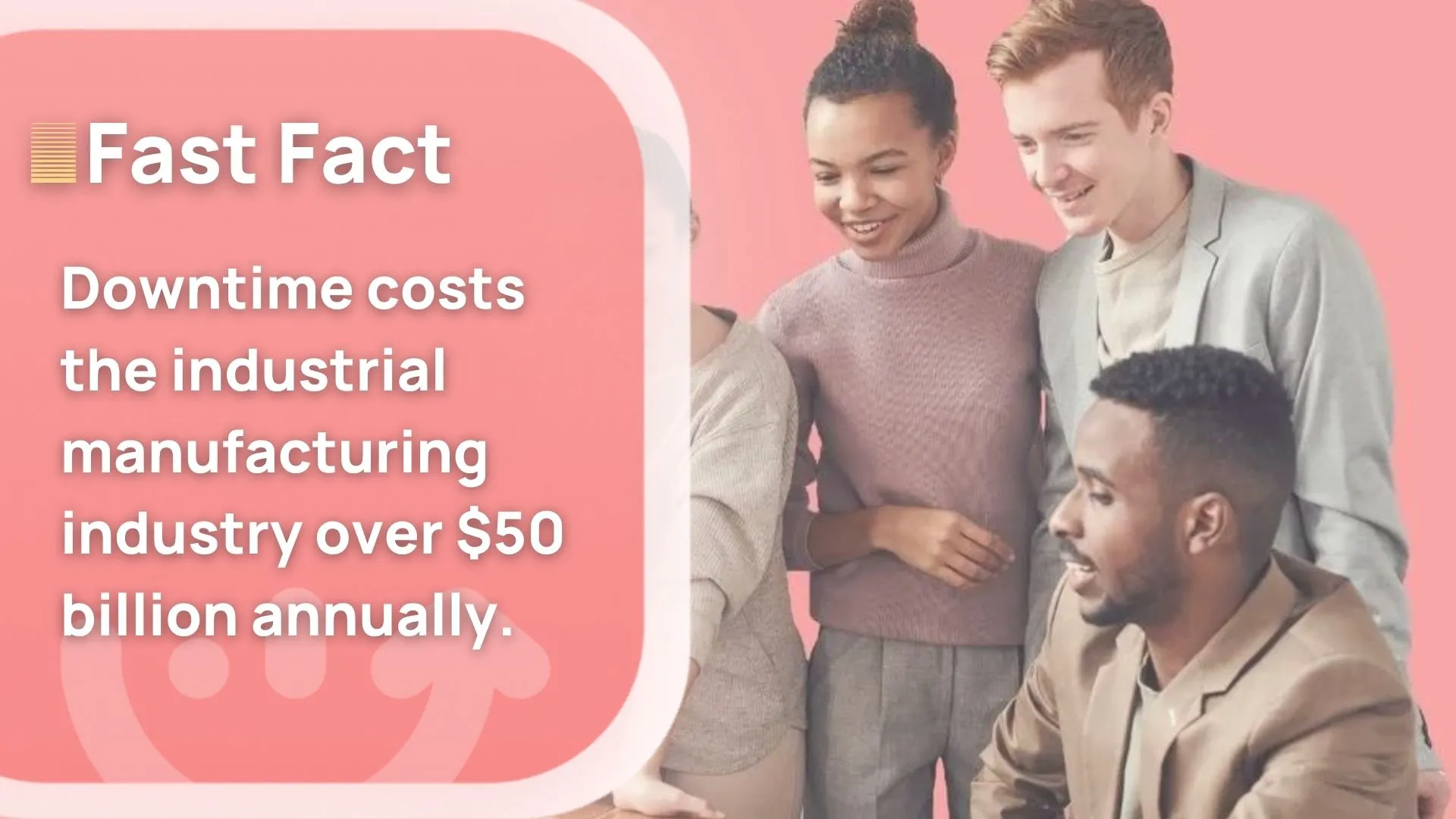
Moreover, unexpected breakdowns necessitate:
- a thorough analysis to find the root cause of the problem
- assessment of necessary replacement parts to get back up in running
- analysis of additional risks in the same asset that could cause future breakdowns
Once the analysis is complete, the parts still have to be ordered and installed. Depending on the asset, this could disrupt or even eliminate your ability to serve your customers. These downtimes could potentially last for a couple of hours to a couple of weeks, depending on the severity of the breakdown.
Planned maintenance allows you to make sure that critical parts are replaced before they fail completely or are at least in inventory as a precautionary measure
Xenia Empowers Managers to Succeed with Planned Maintenance
Xenia is an integrated workplace management platform that unites all of your facilities operations and maintenance management tools. Xenia features a robust, out-of-the-box checklist library to power any task from cleaning and quality inspections, to equipment maintenance and compliance audits. These checklists can have photo attachments and you can even build your own from scratch.
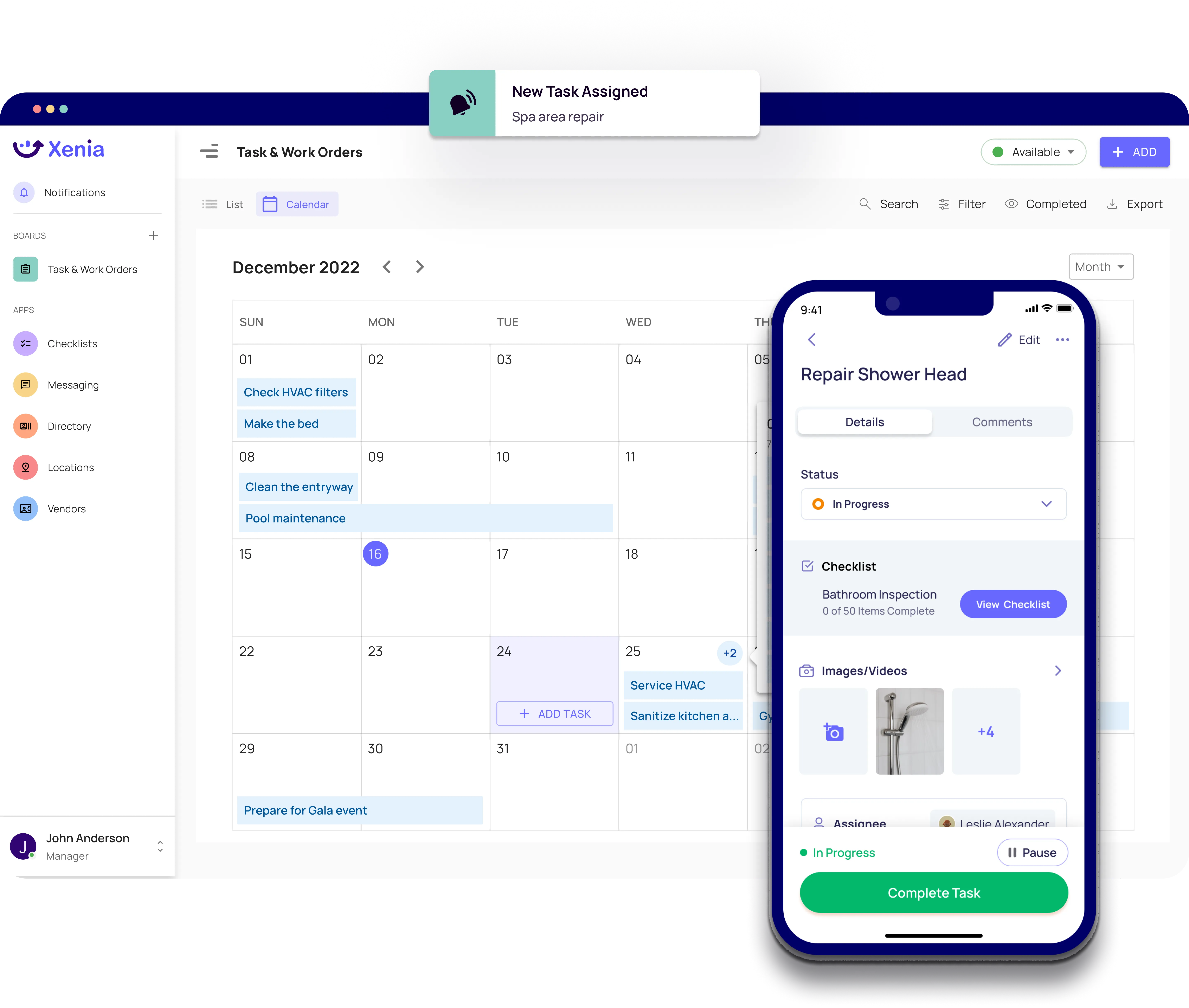
This allows managers to quickly standardize procedures and use them in the work assigned to teams. Xenia seamlessly integrates internal chats, directories and other tools such as logs and schedules to power a diverse array of use cases including:
- safety inspections
- work order management
- preventive maintenance
- facility audits
- quality assurance
- standardized operating procedures
Using Xenia allows managers to learn from previous experience, collecting data to make informed decisions that improve efficiency and effectiveness of deskless teams. Start your free trial of Xenia today, or check out our free checklist library for resources to improve your business.
.webp)
%201%20(1).webp)