When it comes to risk-based inspection, there are two things that keep managers up at night: the lack of knowledge of potential threats and the need to make difficult decisions.
A risk-based inspection can help you avoid these feelings, costly downtime and improve safety, quality, and efficiency.
Priced on per user or per location basis
Available on iOS, Android and Web
This approach helps organizations improve their inspection processes by focusing on areas of the facility or system that are most likely to cause harm to people or equipment.
You can use a risk-based inspection to help determine what areas of your facility need the most attention. Then use this information to get the biggest bang for your buck with your safety improvements.
What is a Risk-Based Inspection?
A risk-based inspection (RBI) is an approach to maintenance management that focuses on prioritizing activities based on their predicted impact on equipment and processes. According to a study, It is based on the notion that 20% of a facility’s components will yield 80% of the risks.
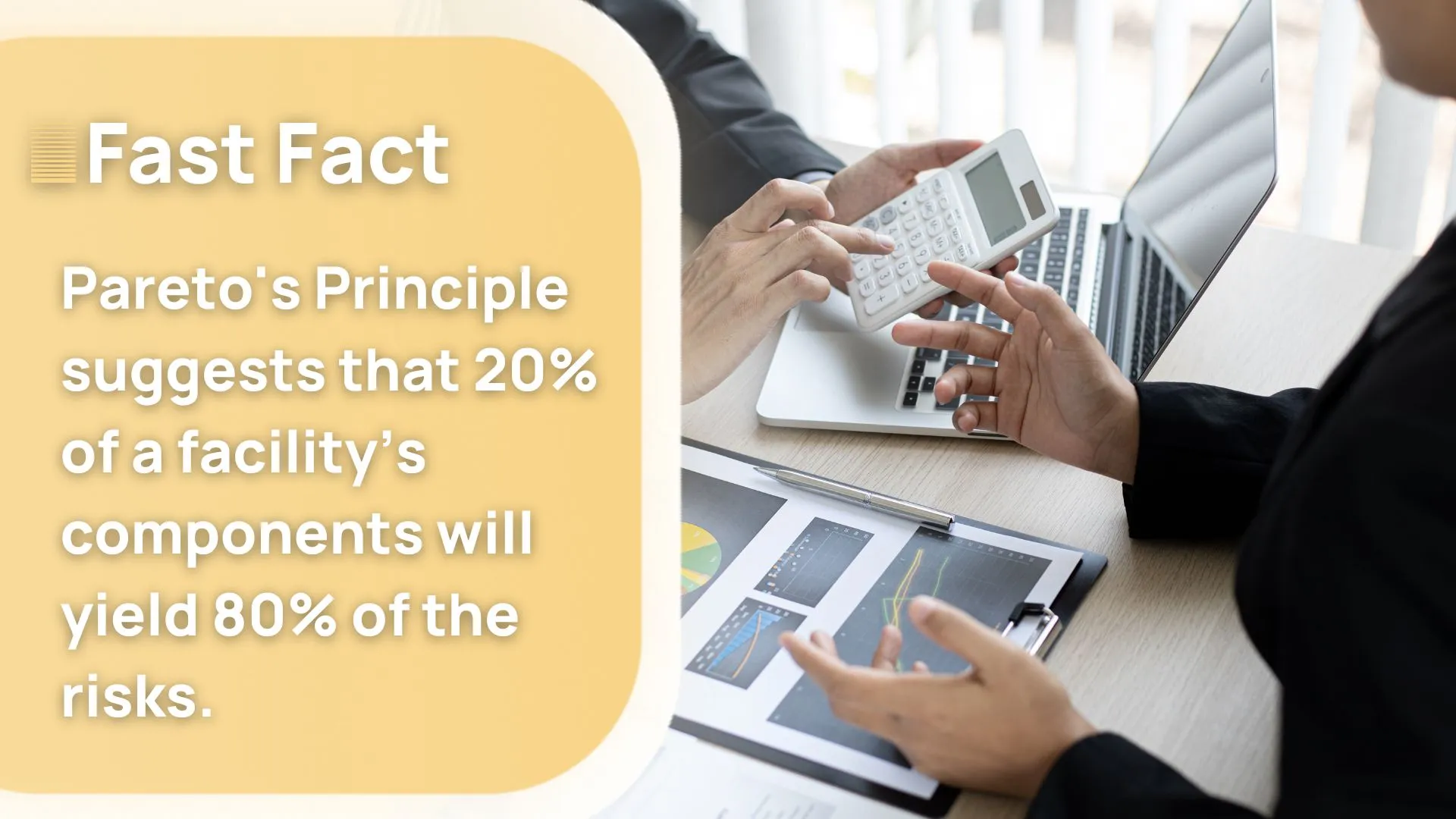
A risk-based inspection will utilize data to identify the most critical issues that need to be addressed. This allows you to make decisions based on actual data instead of assumptions or guesses.
🔎 Identify the higher-risk components
Identifying high-risk items and planning for replacements or repairs can reduce your facility's downtime and save money.
🤑 Perform cost-saving reviews
Analyzing safety, environmental, and health related risk through an economic lens will cut workforce time and reduce downtime.
🦺 Reduce the likelihood of risk recurrence
The purpose of an RBI is to correct or eliminate hazards at the core issue so that they will not happen again. This is also known as a “root cause analysis” or a “failure mode analysis.”
In short, you should inspect some parts of your equipment at different frequencies. This way, you'll pay more attention to those parts with higher probabilities of failure and less to those with lower chances. This allows you to focus your resources where they're most needed and avoid unnecessary work.
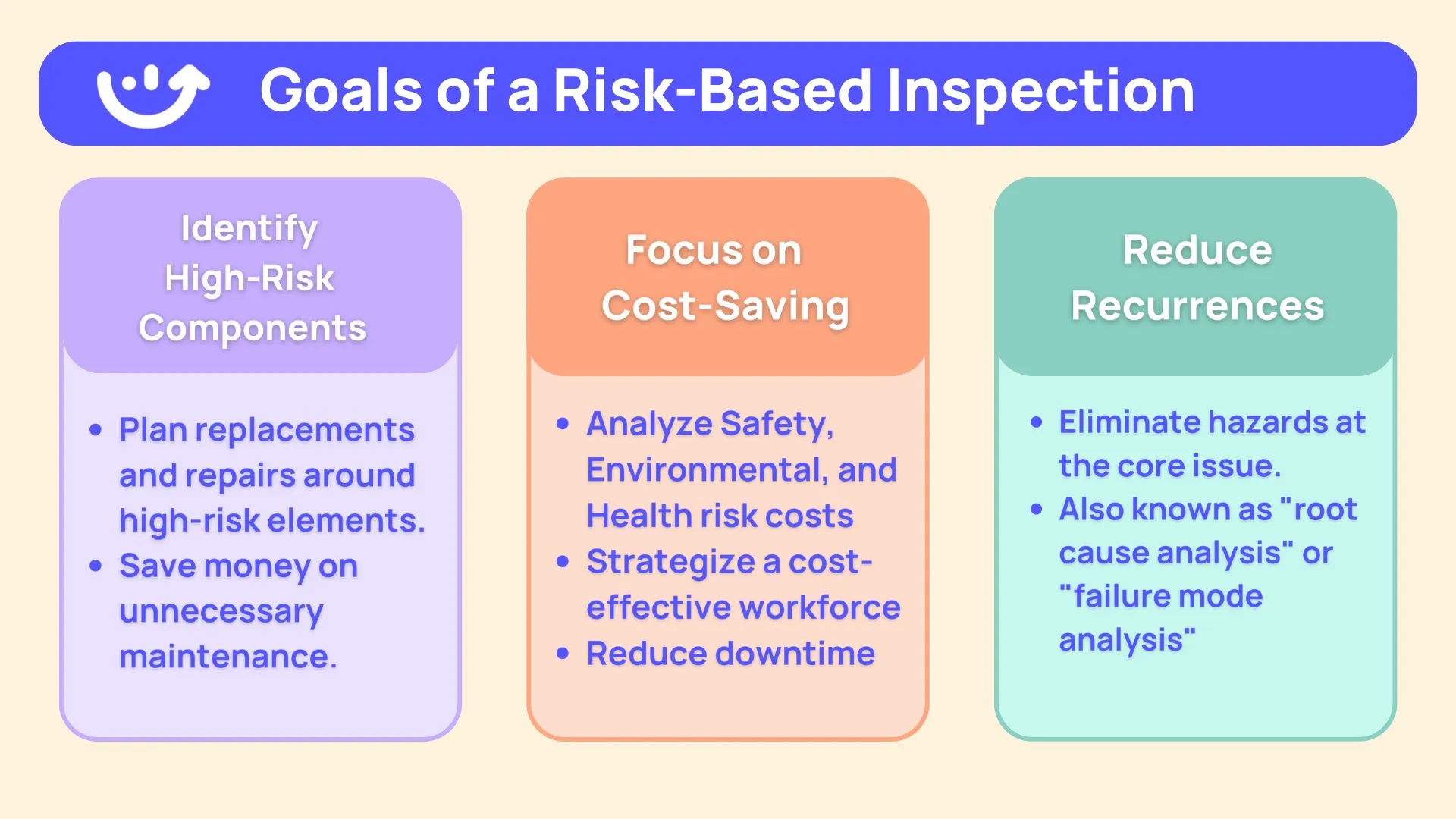
Risk Based Inspection Codes to Review
Many resources are available to guide how to use a risk-based inspection to determine the frequency and extent of analysis. They also include information on how to make failure mode and effect analyses (FMEAs) a part of your risk management strategy.
🌎 International Risk-Based Analysis Resource Code
- EN 16991: Risk-based inspection framework as per European standards
- API 580: Risk-Based Inspection - Recommended Practice created by the American Petroleum Institute.
- API 581: Risk Based Inspection Methodology - Recommended Practice (Third edition, April 2016)
- ASME PCC-3: Inspection Planning Using Risk-Based Methods written by the American Society of Mechanical Engineers (ASME).
- DNV-RP G101: Risk-Based Inspection Of Offshore Topsides Static Mechanical Equipment
- EEMUA 159: Chapter 17 - RBI methodology for aboveground storage tanks.
With this resource analysis information, you must collect data points regarding your facilities. It’s critical to examine each machinery’s error frequency rate, what potential consequences might arise from an error, and where exactly the failure occurs.
Inspectors collect this data utilizing these three main methods:
- Qualitative: First-hand observation.
- Quantitative: Utilize statistical models and data history.
- Semi-Quantitative: This is a combination of qualitative and quantitative. You can use a single point of reference to assume probability.
A risk-based inspection goes further into a mathematical equation using two main components.
What Are The Two Critical Components of Risk-Based Inspection?
The two critical components of risk-based inspection are point of failure (POF) and consequence of failure (COF).
👉 Point of Failure
POF estimates the chance that an asset or piece of equipment will fail over a predicted timeline. It's calculated using historical data, such as how often the piece of equipment has failed in the past, how long it typically lasts before failing, and so on. For example, if an asset (like a piece of machinery) has a 50% chance of failing in one year, the POF would be 0.50.
🧲 Consequence of Failure
COF estimates what happens if a critical asset or piece of equipment fails—in other words, what are the consequences? This includes safety hazards and financial losses.
The POF and COF components are combined to determine which assets or equipment need an inspection. If your POF is high, but your COF is low (or vice versa), then focusing on mitigating that issue isn't worth your time. This information helps prioritize corrective action.
4 Benefits of Risk-Based Inspections
As a general manager or frontline worker, you know how important it is to keep your business running smoothly. You want to reduce the risk of failures and increase the reliability of your equipment, but you also want to use inspection resources more cost-effectively.
Inspection resources are costly, so they must be used in ways that will improve your operations. A risk-based inspection is one way to do that: it allows you to use your existing inspection tools more strategically and ensure they align with your organization's priorities.
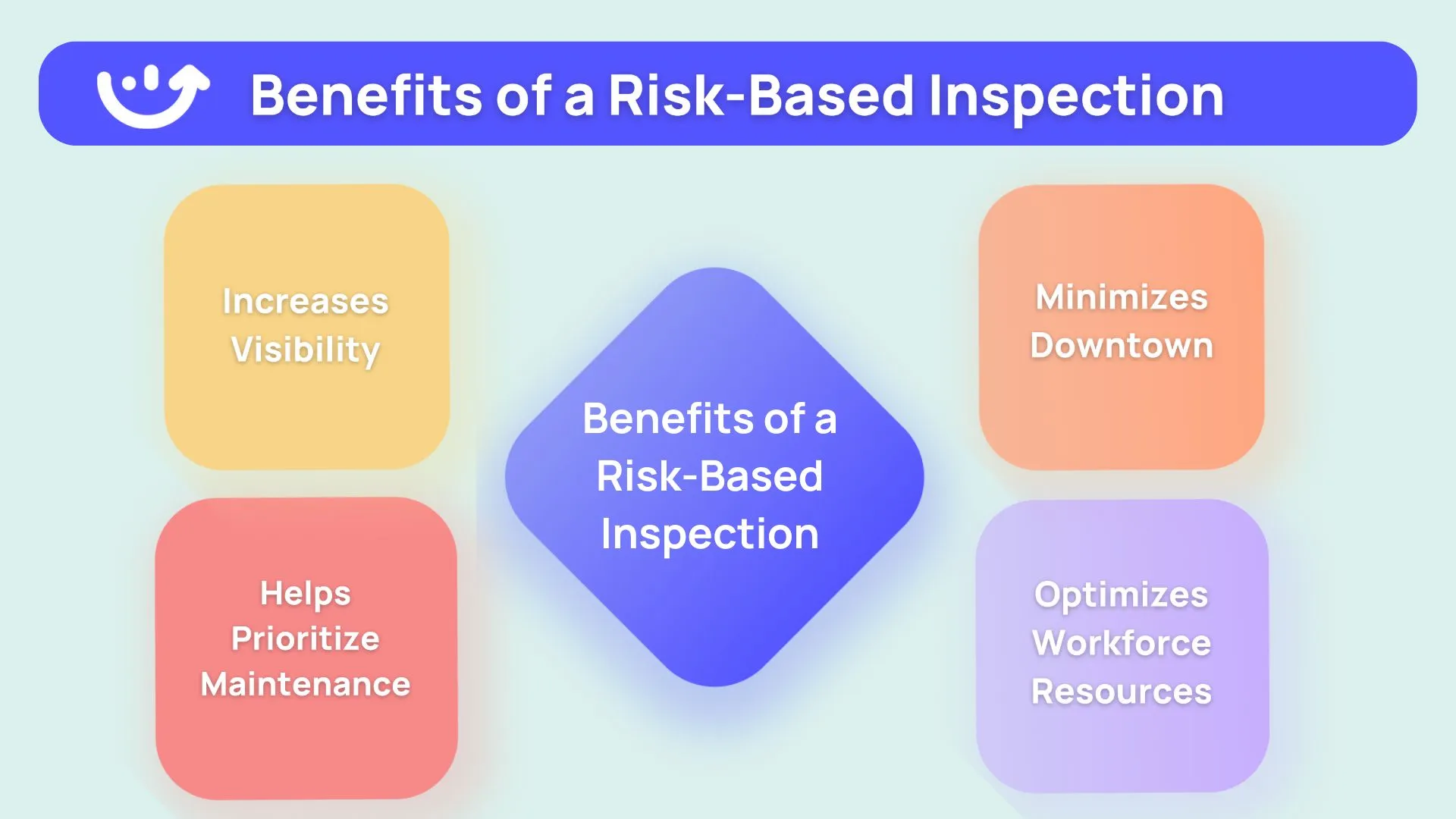
👀 Improve visibility
You'll get a clearer picture of your critical assets' health and more insight into the cause of any problems.
📅 Prioritize upcoming maintenance
When conducting an audit of the machinery, assets, and facilities to determine which items are most likely to break down or require repairs, utilize this information to create a priority list for upcoming maintenance activities. The goal is to identify potential issues before they occur and address them quickly before they become more significant problems.
🦾 Minimize downtime
By preventing critical malfunctions, you can reduce the need for major maintenance and repairs—and avoid the costly downtime that comes with them.
🎉 Optimize workforce resources
By eliminating unnecessary actions, employees can focus on the most critical aspects of their job without worrying about doing something irrelevant or unnecessary. The result is an optimized workforce that doesn't waste time doing busy work—and isn't bogged down by having too many boxes to check on a single checklist!
Why Use CMMS Software for Risk-Based Inspections?
Computerized Maintenance Management Software (CMMS) is the perfect methodology for risk-based inspections. It focuses on the use of automated analysis, data collection, and reporting to facilitate continuous improvement in safety, quality, productivity, and cost control.
CMMS’ goal is to implement an evidence-based approach to safety and quality management that all members of the organization can use. The methodology involves identifying hazards through root cause analysis, implementing corrective action plans, and ensuring that they are followed up with regular audits. Then use the audit results to identify areas where improvements can be made and implemented quickly.
.webp)
This means that:
- All members of the organization are aware of potential hazards within their area of work and take steps to avoid them or mitigate against them if they do occur;
- Corrective action plans are put in place when problems arise;
- Managers carry out regular audits to ensure that these plans are being followed up on effectively;
- Any issues arising during audits can be addressed immediately so as not to affect other work areas (e.g., an accident caused by lack of training).
Risk-based inspections are part of CMMS software that helps you track your manufacturing processes and ensure they're as efficient as possible. It helps you manage your workflow, keep track of inventory, and set up alerts so that you'll know about it immediately when something goes wrong.
That's why we recommend using CMMS software like Xenia!
.webp)
%201%20(1).webp)