Construction projects require careful planning, coordination, and attention to detail to ensure that they are completed on time, on budget, and to the highest standards of quality and safety.
One critical aspect of construction projects is pre-drywall inspections, which help identify potential problems before they become costly issues that can delay construction, put workers at risk, or result in subpar construction quality.
Priced on per user or per location basis
Available on iOS, Android and Web
In this post, we will explore the benefits of pre-drywall inspections, the types of inspections conducted during the pre-drywall phase, and best practices for conducting thorough pre-drywall inspections.
We will also introduce Xenia, a cloud-based construction management software platform designed to help contractors streamline and automate their day-to-day operations, including pre-drywall inspections.
6 Benefits of Pre-Drywall Inspections
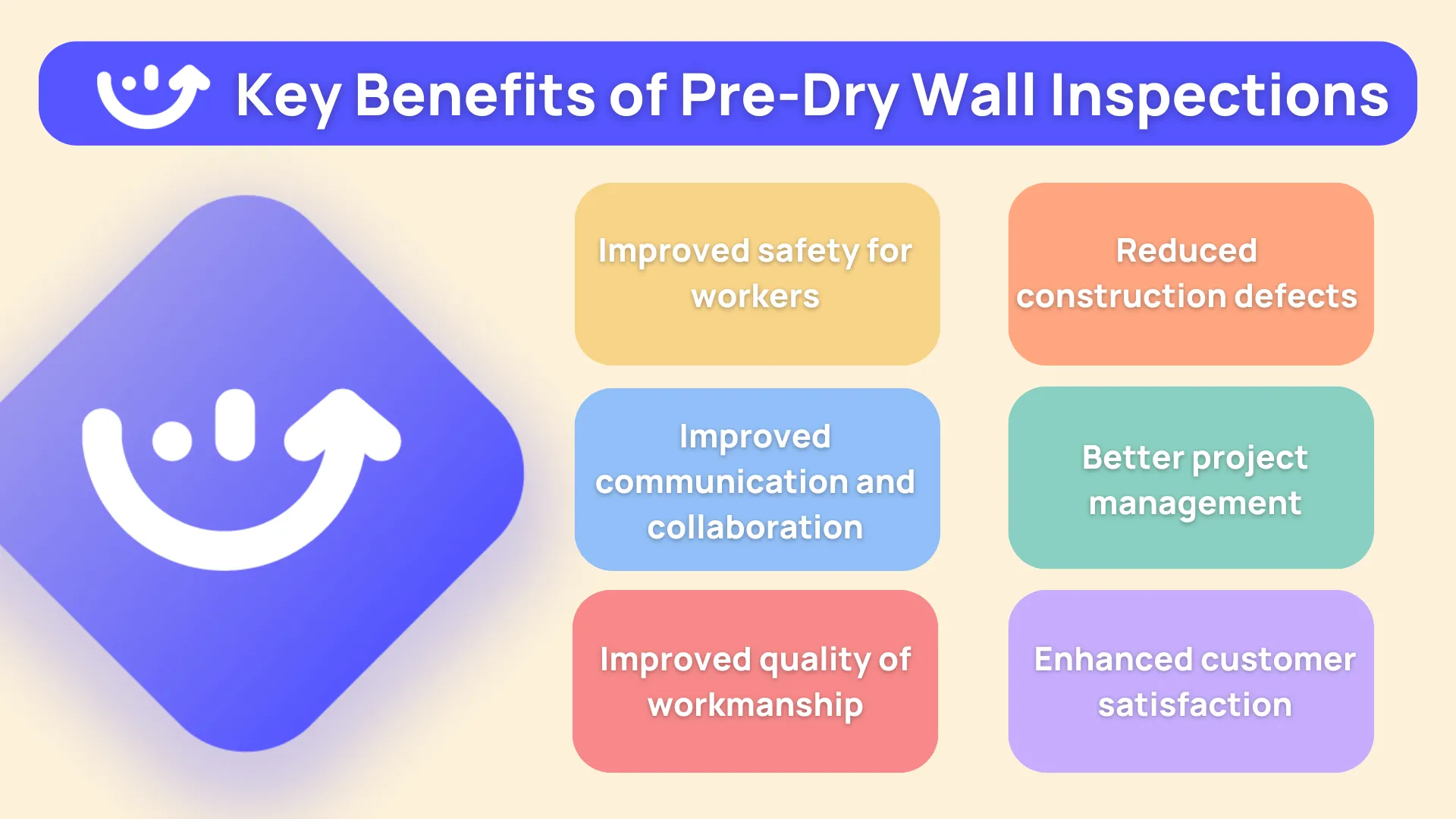
Pre-drywall inspections are a critical part of the construction process.
These inspections ensure that everything is up to code, installed correctly, and functioning as intended. This helps identify potential issues that could cause problems down the road, giving you the opportunity to address them before they become more significant problems. Pre-drywall inspections ensure that construction projects are safe, built to a high standard, and meet building codes and regulations.
Some of the benefits of pre-drywall inspections include:
1. Improved safety for workers
The safety of construction workers should always be a top priority. Pre-drywall inspections help to identify safety hazards that might be hidden behind walls or other structures, such as exposed wiring or improperly installed plumbing. By identifying and correcting safety issues during pre-drywall inspections, construction teams can reduce the risk of accidents, injuries, and even fatalities on the job site.
2. Reduced construction defects and deficiencies
Pre-drywall inspections can help to identify construction defects and deficiencies before they become major problems. Catching these issues early on can save construction teams time and money by reducing the need for expensive and time-consuming repairs later on. By addressing construction defects during the pre-drywall phase, construction teams can ensure that the final product meets high standards for quality and workmanship.
3. Improved communication and collaboration among team members
Pre-drywall inspections involve multiple team members, including general contractors, subcontractors, and inspectors. By bringing these team members together to conduct pre-drywall inspections, construction teams can improve communication and collaboration among all parties involved in the project. This can help to prevent misunderstandings and ensure that everyone is working towards the same goal.
4. Better project management and cost control
Pre-drywall inspections can help construction teams to manage projects more effectively and keep costs under control. By identifying potential issues early on, construction teams can make informed decisions about how to allocate resources and make necessary adjustments to the project plan. This can help to avoid costly delays and keep projects on track.
5. Improved quality of workmanship
Pre-drywall inspections can help to ensure that construction work meets high standards for quality and workmanship. By catching potential issues during the pre-drywall phase, construction teams can take corrective action to ensure that the final product meets these high standards. This can help to improve the reputation of the construction team and lead to greater customer satisfaction.
6. Enhanced customer satisfaction
Pre-drywall inspections can help to ensure that the final product meets the expectations of customers.
By catching potential issues early on and addressing them during the pre-drywall phase, construction teams can ensure that the final product meets high standards for quality and workmanship. This can lead to greater customer satisfaction and positive word-of-mouth marketing for the construction team.
Common Issues Found in Pre-Drywall Inspections
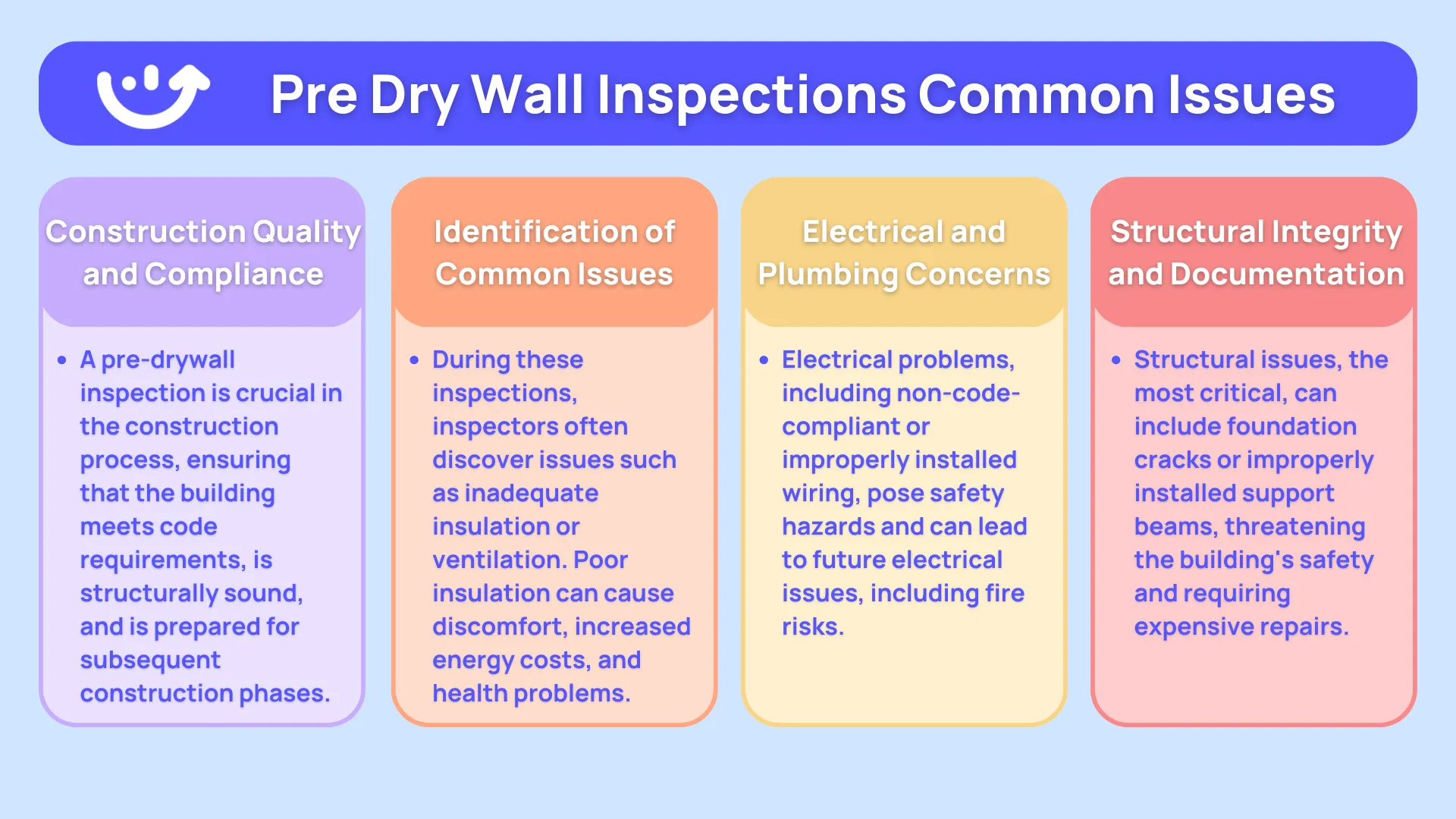
A pre-drywall inspection is an important step in the construction process that ensures that a building is up to code, structurally sound, and ready for the next phase of construction. The inspection takes place before the drywall is installed and provides an opportunity for the inspector to assess the quality of the work done by contractors and subcontractors.
During pre-drywall inspections, inspectors often find a range of issues that need to be addressed before the project can move forward. Inadequate insulation or ventilation is a common issue that can have serious consequences. Poor insulation can lead to uncomfortable living conditions, higher energy bills, and even health issues. Inadequate ventilation can lead to poor indoor air quality, which can cause respiratory problems and other health issues.
Electrical Issues
Electrical issues are also common during pre-drywall inspections. Wiring that is not up to code or improperly installed can be a safety hazard and cause electrical problems in the future. These issues can range from minor issues like loose connections to more serious problems like overloaded circuits or electrical fires.
Plumbing Issues
Plumbing issues are also frequently found during pre-drywall inspections. Leaks or improperly installed plumbing can cause water damage, mold growth, and other problems down the line. These issues can be difficult and expensive to repair, and can cause significant damage to the building if left unchecked.
Structural Issues
Structural issues are perhaps the most serious issues that can be uncovered during pre-drywall inspections. Problems with the frame or foundation of a home can lead to serious safety concerns and expensive repairs. These issues can include cracks in the foundation, poorly installed support beams, or other problems that compromise the structural integrity of the building.
It is important for inspectors to thoroughly document any issues they find during pre-drywall inspections. This documentation can help contractors and subcontractors understand the scope of the problem and the steps needed to address it. Documentation can also be used as evidence in the event of legal disputes or other issues that may arise during construction.
How to Conduct a Pre-Drywall Inspection
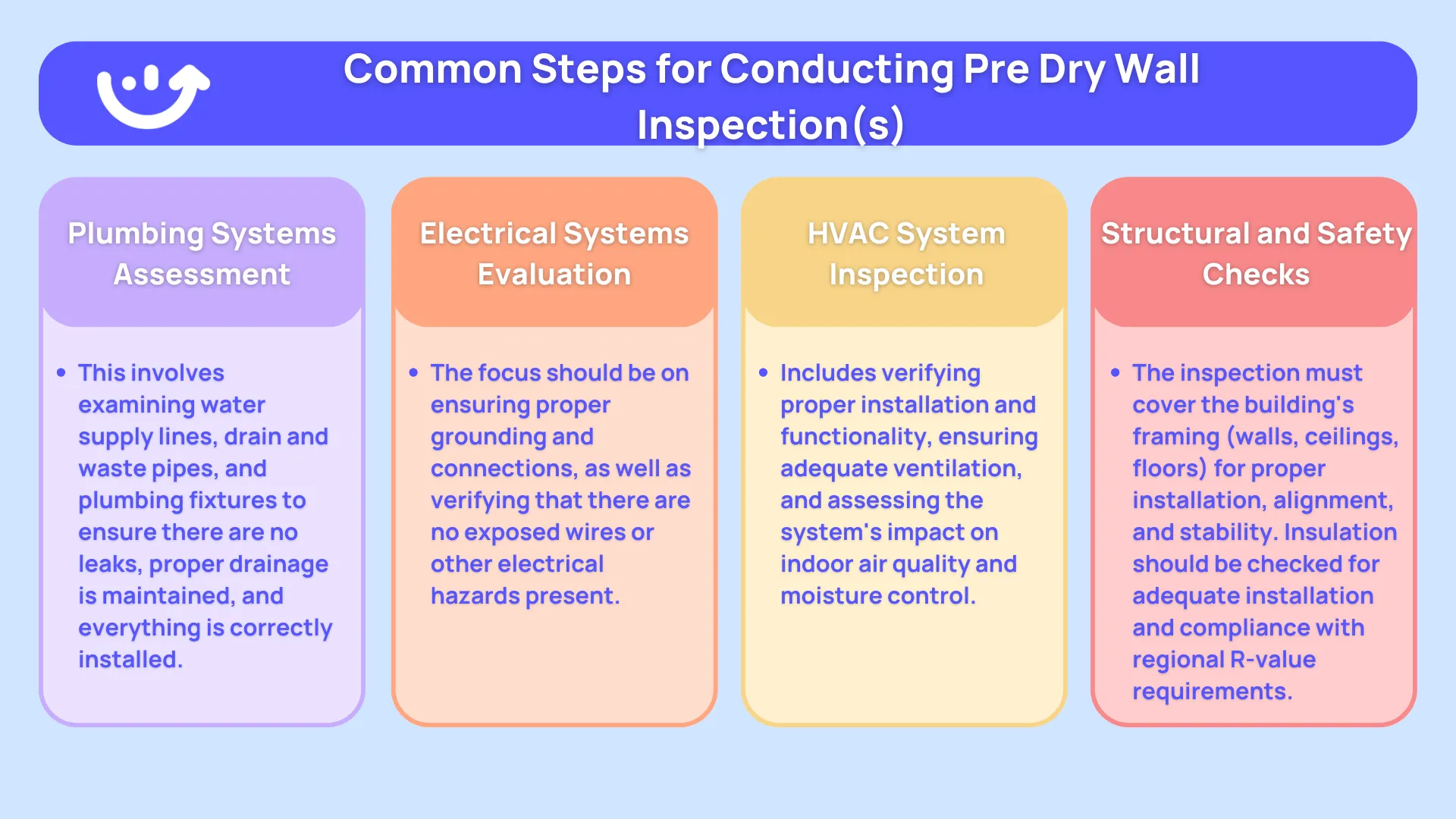
To conduct a thorough pre-drywall inspection, it's important to follow a checklist that covers all the essential areas. The checklist should include the following:
- Plumbing: Inspect all plumbing systems, including water supply lines, drain and waste pipes, and plumbing fixtures. Check for leaks, proper drainage, and proper installation.
- Electrical: Inspect all electrical systems, including wiring, switches, and outlets. Ensure that everything is properly grounded and connected, and that there are no exposed wires or other hazards.
- HVAC: Inspect the heating, ventilation, and air conditioning (HVAC) systems. Check for proper installation, functionality, and ventilation. This is particularly important for ensuring indoor air quality and preventing moisture problems.
- Framing: Inspect the framing of the building, including walls, ceilings, and floors. Check for proper installation, alignment, and stability.
- Insulation: Inspect the insulation in the walls, ceilings, and floors. Ensure that it is properly installed and meets the required R-value for the region.
- Fire safety systems: Inspect all fire safety systems, including smoke detectors, fire alarms, and fire suppression systems. Ensure that they are properly installed and functioning.
- Roofing: Inspect the roofing system, including shingles, flashing, and gutters. Check for leaks, damage, and proper installation.
In addition to following the checklist, it's important to conduct the inspection in a thorough and systematic manner.
This includes:
- Using the right tools and equipment to inspect each system and component.
- Taking detailed notes and photographs to document any issues or deficiencies.
- Communicating any issues to the project team, including the general contractor, subcontractors, and the owner.
- Following up on any corrective actions that need to be taken.
By following these best practices and using a comprehensive checklist, construction managers and owners can ensure that their pre-drywall inspections are effective and efficient. This can help to prevent costly delays and repairs, improve safety and quality, and enhance customer satisfaction.
Why Pen and Paper Inspections Must be Digitized
Pen and paper have been a long-standing method of conducting inspections. However, with the rise of technology, digital inspection tools are becoming more popular for their efficiency and effectiveness. Here are some reasons why:
Efficiency and speed
Conducting inspections with pen and paper is a time-consuming process. Inspectors have to write down the findings and then transcribe them into a digital format for record-keeping. This process is not only slow, but it is also prone to errors. With digital inspection tools, inspectors can record their findings directly on a mobile device or tablet, saving time and reducing the risk of errors.
Improved accuracy
With pen and paper, it's easy to make mistakes, such as writing down incorrect numbers or illegible handwriting. These mistakes can lead to inaccurate data and potentially costly errors. Digital inspection tools eliminate these mistakes by providing automatic calculations and data validation, ensuring accurate data collection.
Better organization and record-keeping: Keeping track of paper inspection forms can be a nightmare. Papers can get lost or damaged, and organizing them can be time-consuming. With digital inspection tools, all data is stored securely in the cloud, making it easily accessible for analysis and reporting. This also helps with compliance and regulatory requirements.
Real-time data and insights
With digital inspection tools, data is captured in real-time. This means that issues can be identified and addressed immediately, leading to quicker resolution times and preventing further problems from occurring. The real-time nature of digital inspection tools also allows for instant data analysis and reporting, providing actionable insights for improvement.
Mobility and accessibility
Digital inspection tools allow inspectors to conduct inspections on-the-go. With a mobile device or tablet, inspectors can easily access inspection checklists, capture photos, and record findings, no matter where they are. This mobility allows for more efficient and effective inspections, reducing the time and cost associated with traditional pen-and-paper methods.
Using pen and paper for inspections is outdated and inefficient. Digital inspection tools provide many advantages, including speed, accuracy, organization, real-time insights, and mobility. With the rise of technology, it's time to leave pen and paper behind and embrace digital inspection tools for better and more effective inspections.
Use Xenia for Construction Inspections and Team Management
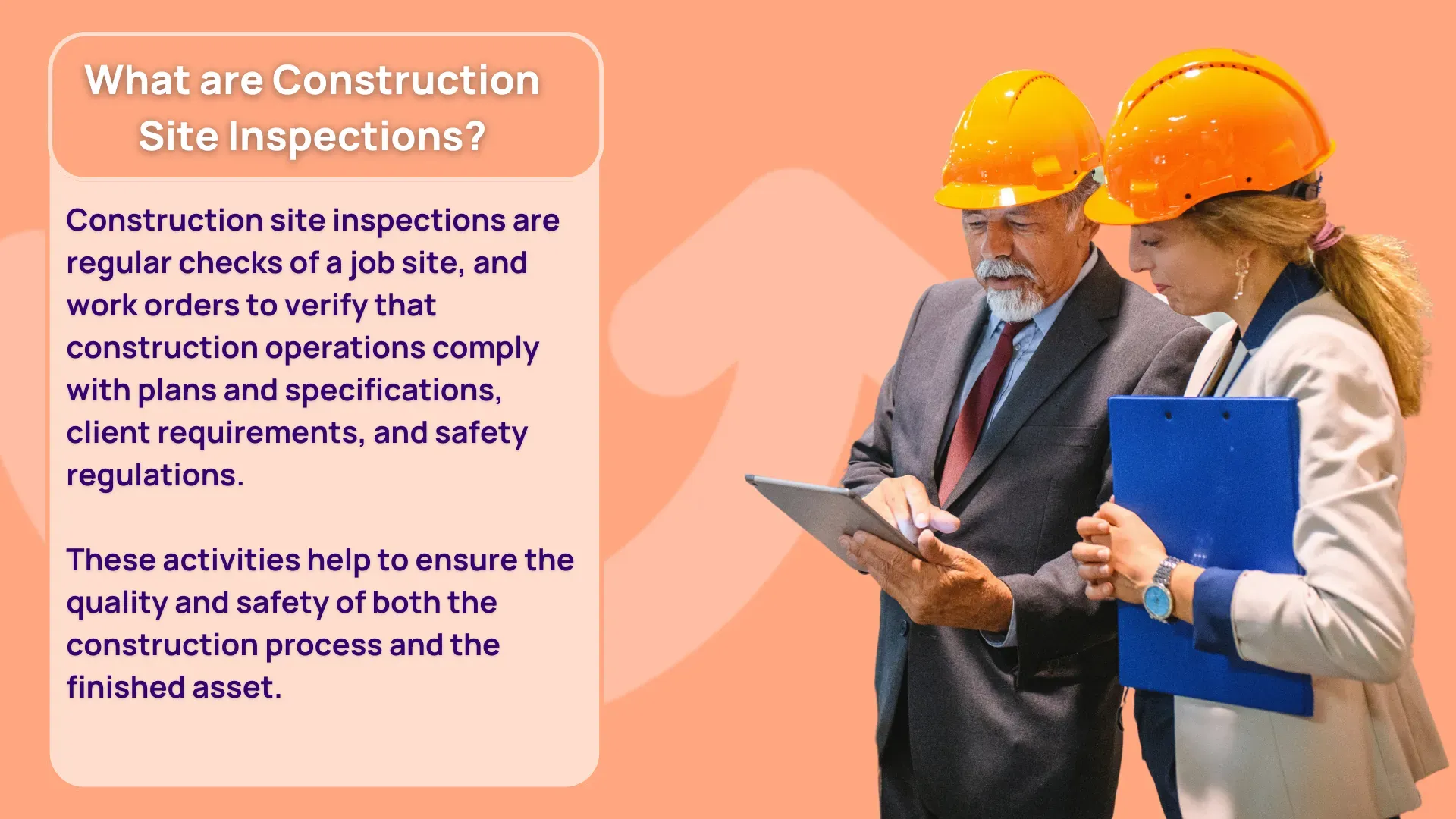
Now that we've covered the essentials of pre-drywall inspections, let's take a look at how Xenia can help streamline the process and improve your construction projects.
When it comes to managing pre-drywall inspections, Xenia is the ultimate tool for the job. Here are just a few reasons why:
Customizable Checklists
Xenia's customizable checklists and templates make it easy to create standardized procedures, daily logs, and inspections for any scenario, including pre-drywall inspections. With Xenia, you can create checklists that are specific to your project needs and ensure that all necessary inspections are completed before the drywall is installed.
Work Order Management
Xenia's Work Order Management feature allows you to assign work to teams or subcontractors with full clarity of location, category, due date, and template attachments. This means that you can easily assign pre-drywall inspections to the appropriate team members and track their progress to ensure that all inspections are completed on time.
Site Safety Management
Pre-drywall inspections are an important part of site safety management. With Xenia's Site Safety Management tools, you can conduct site inspections, report hazards and near misses, and ensure that all safety protocols are being followed. This helps to reduce the risk of workplace accidents and injuries.
Real Time Collaboration
Using Xenia for pre-drywall inspections can also improve communication and collaboration among team members. Xenia's real-time collaboration features allow team members to communicate effectively and share information about the project. This helps to prevent misunderstandings and ensures that everyone is working towards the same goal. By providing a central platform for communication and collaboration, Xenia can help to ensure that all team members are on the same page and working together effectively.
Equipment Maintenance
In order to perform pre-drywall inspections effectively, it is important to have well-maintained equipment. Xenia's Equipment Maintenance features allow you to schedule maintenance tasks, monitor equipment usage, and keep everything running smoothly on your job sites.
Detailed Reports
Xenia provides detailed reports on the work completed, including the time spent on each task and the live status of every job. This allows you to easily track the progress of pre-drywall inspections and identify any areas that may need additional attention.
.webp)
%201%20(1).webp)