Construction equipment management, much like the steel girders that form the backbone of your builds, is the underpinning of every successful construction project. This critical cog in the construction wheel influences everything from on-site safety and work efficiency, to project timelines and, ultimately, your bottom line.
Yet, navigating the rugged terrain of construction equipment management is no easy task; it’s riddled with unique challenges requiring a blend of industry expertise, management skill, and innovative tools.
Priced on per user or per location basis
Available on iOS, Android and Web
As a seasoned or budding construction manager, becoming proficient in the art of construction equipment management can turbocharge your operations, pushing the throttle on efficiency, productivity, and profit margins.
In this comprehensive guide, we’re not just scratching the surface; we’re excavating the foundations of construction equipment management. We’ll shed light on its integral role, highlight the pivotal elements you should be aware of, and offer strategies to conquer common obstacles.
What is Construction Equipment Management?
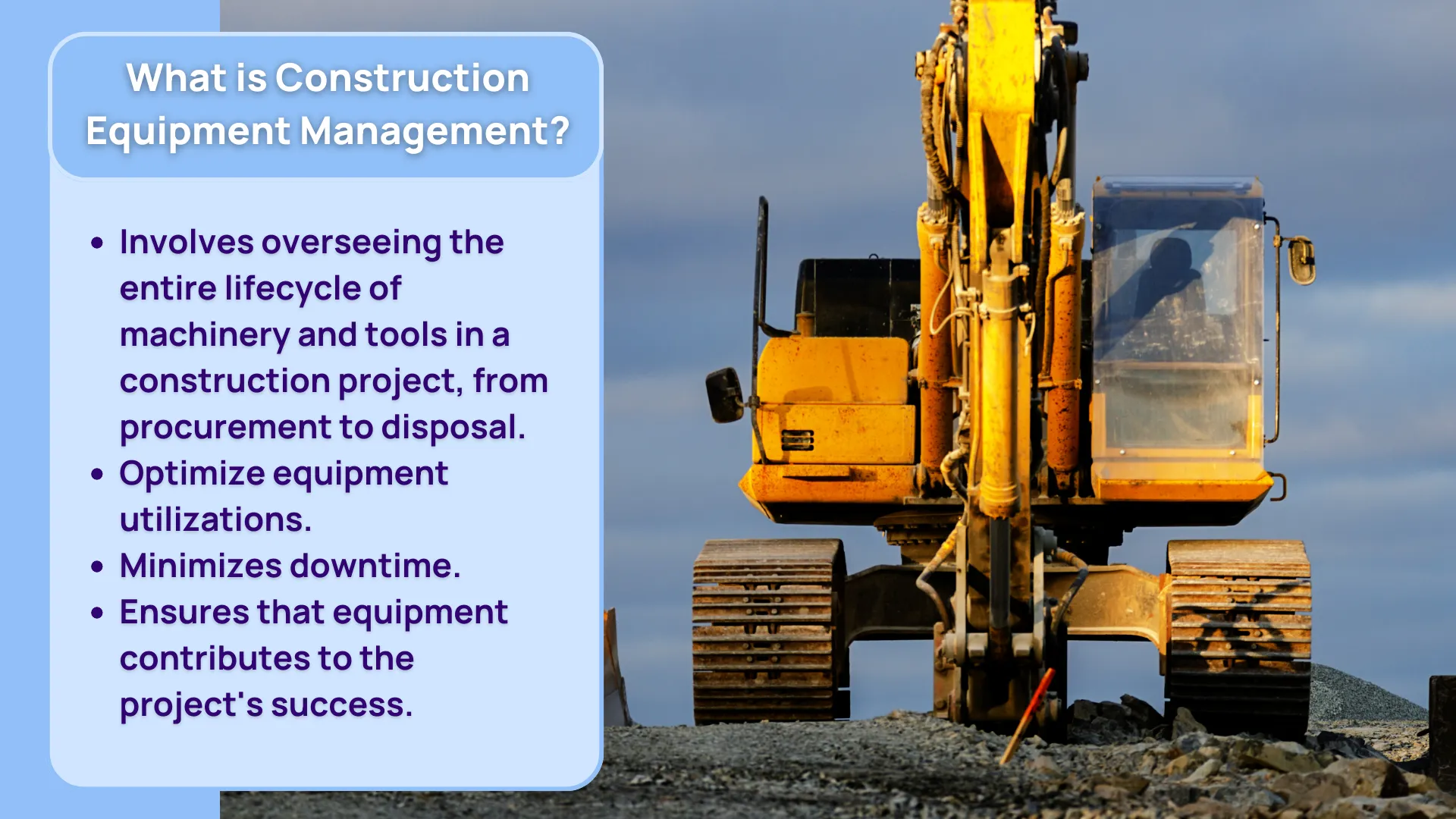
Construction equipment management refers to the strategies and practices used to manage machinery and equipment in a construction project. It involves overseeing the entire lifecycle of the equipment, from procurement, maintenance, and utilization, to eventual disposal or replacement.
Effective equipment management aims to ensure that every piece of equipment is used to its maximum potential, minimizing downtime and costs while maximizing productivity and longevity.
Equipment can range from large machinery like cranes, bulldozers, and excavators, to smaller tools like drills and jackhammers. Regardless of size, each piece of equipment plays a critical role in the successful completion of a construction project.
Construction equipment management includes aspects such as equipment selection and procurement, maintenance scheduling, safety compliance, tracking equipment utilization, managing breakdowns, and planning for replacement or disposal. Each of these elements plays a vital role in ensuring that equipment contributes to the project's success rather than becoming a source of delays or inflated costs.
Why is Construction Equipment Management Important?
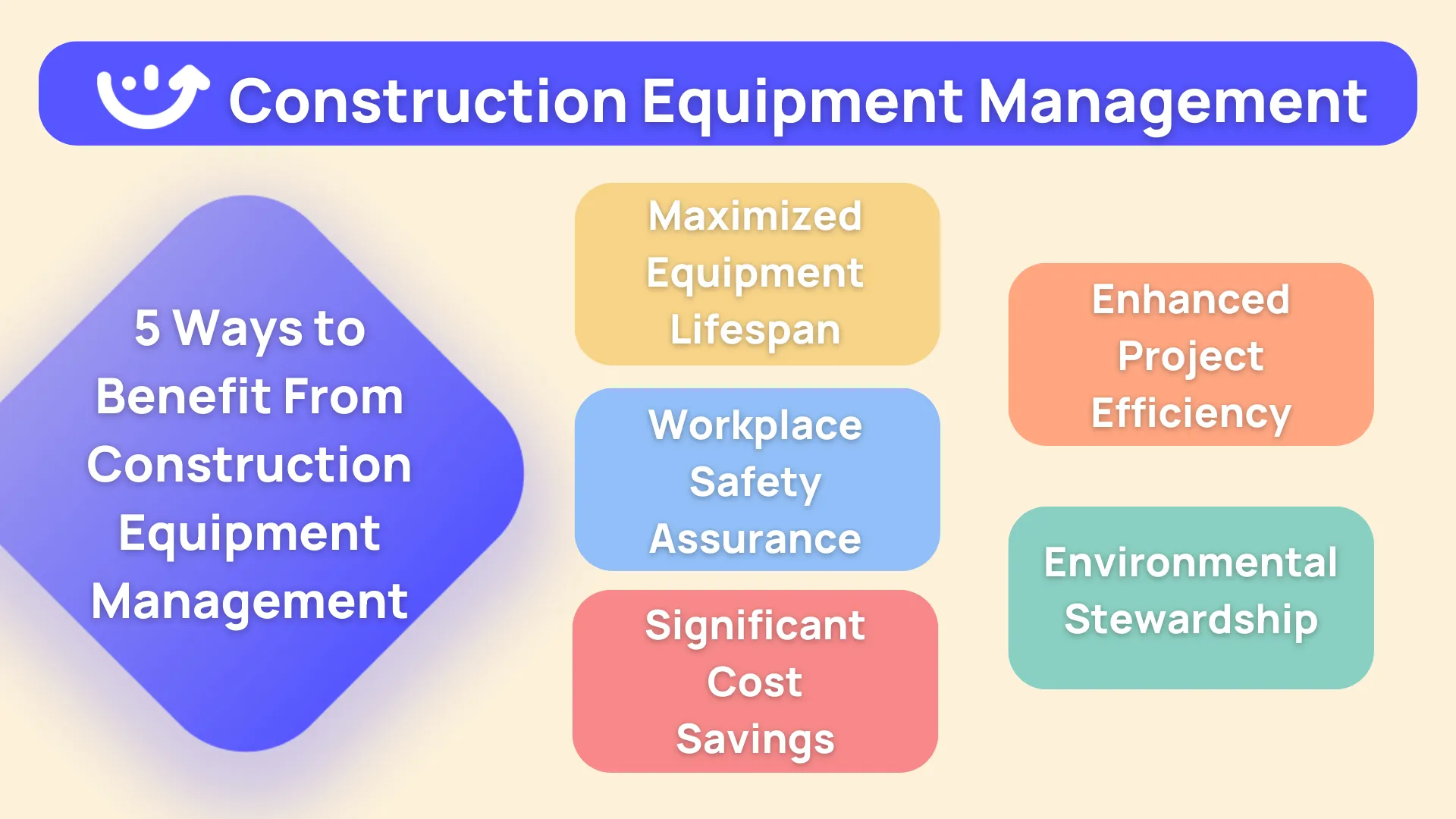
The importance of proficient construction equipment management cannot be overstated. Like the silent gears of a well-oiled machine, it has far-reaching implications for the smooth running of your construction projects. Here's why construction equipment management should top your priority list:
Maximized Equipment Lifespan and Efficiency
Through regular maintenance checks, strategic utilization, and diligent upkeep, you can stave off premature wear and tear. This approach not only saves you the hefty costs of premature replacements but also guarantees your equipment always operates at its peak potential.
Workplace Safety Assurance
Well-maintained and appropriately used equipment is less likely to malfunction, dramatically reducing the risk of on-site accidents and injuries. Construction equipment management, therefore, serves as your first line of defense against safety hazards, fostering a safer working environment for your team.
Significant Cost Savings
Effective equipment management is synonymous with substantial cost savings. By avoiding unnecessary equipment purchases, reducing maintenance and repair expenditures, and circumventing costly project delays caused by equipment failures, you can keep your budget in check. Construction equipment management is not just an operational consideration; it’s a savvy financial strategy.
Enhanced Project Efficiency
With your equipment fleet running like a well-tuned engine, your projects can proceed without disruptions. Efficient construction equipment management means fewer unexpected breakdowns, more predictable timelines, and improved overall productivity. This reliability translates into on-time project completion and highly satisfied clients who are more likely to entrust you with future contracts.
Environmental Stewardship
By optimizing the usage of construction equipment and ensuring regular maintenance, you minimize excessive fuel consumption and harmful emissions. This practice aligns with the global shift towards sustainable construction practices and green building certifications.
Common Challenges in Construction Equipment Management and How to Overcome Them
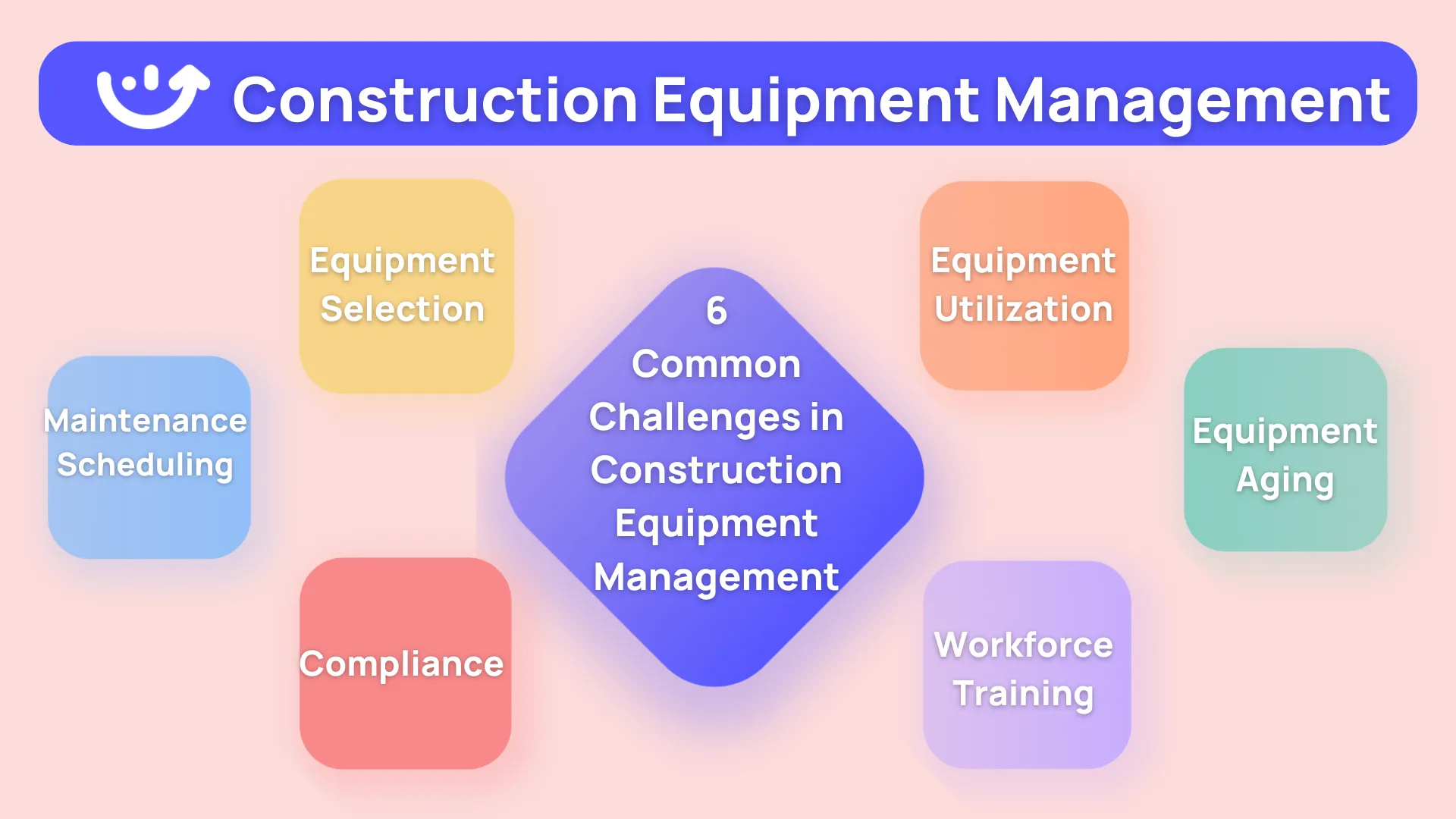
Navigating the realm of construction equipment management is no simple feat. It's a balancing act, involving the careful manipulation of multiple variables. Let's dissect six common challenges construction managers often grapple with, and explore viable solutions:
Equipment Selection
A mismatch can lead to operational inefficiencies, delays, and spiraling costs. A keen understanding of the task at hand, coupled with thorough knowledge of your equipment's capabilities, is fundamental to making the right selection. Investing time in training your team to accurately assess job requirements can go a long way in overcoming this challenge.
Maintenance Scheduling
Scheduling checks without hampering your operations can be quite the puzzle. This is where technology steps in. By adopting a robust construction equipment management software, you can streamline maintenance scheduling. Such software can alert you when maintenance is due, allowing you to plan operations around it, thereby reducing downtime.
Compliance
Ensuring all your equipment complies with safety and regulatory standards is paramount but challenging. Regular inspections, coupled with meticulous record-keeping, can help you stay on top of this task. Integrating a robust compliance management system into your operations can also automate and simplify compliance monitoring, reducing the likelihood of oversights.
Equipment Utilization
Getting the most out of every piece of equipment is vital for efficiency and cost-effectiveness. However, tracking equipment utilization manually can be a Herculean task. Here again, technology provides a solution. Equipment management software can offer real-time data on equipment usage, helping you make data-driven decisions to optimize utilization and minimize idle time.
Equipment Aging
As equipment ages, its performance may deteriorate, and maintenance costs can increase, affecting your bottom line. A well-planned replacement strategy, based on a comprehensive understanding of your equipment’s life cycle, can help you anticipate when equipment will start becoming a liability and plan for timely replacements or upgrades.
Workforce Training
Lack of proper training can lead to equipment misuse, which may cause premature wear and tear, increase safety risks, and lower productivity. Regular, up-to-date training programs can ensure your team has the knowledge and skills to use the equipment effectively and safely.
Leveraging Digital Solutions to Optimize Construction Equipment Management
.webp)
The dawn of the digital age has revolutionized the construction industry. By leveraging innovative digital tools, construction managers can now elevate their equipment management strategies to unprecedented levels of efficiency and effectiveness.
These tools include advanced construction management software, Internet of Things (IoT) devices, and user-friendly mobile apps, each offering a suite of features designed to streamline construction equipment management. Let's delve deeper into how these digital solutions can revolutionize your construction equipment management practices:
Real-Time Equipment Tracking
With multiple pieces of equipment in use across different job sites, losing track is a real risk. Enter digital solutions, which offer real-time tracking capabilities. These tools can provide live updates on each piece of equipment’s location, thereby preventing loss and theft.
Automated Maintenance Scheduling
Maintenance is a critical part of equipment management, but it's also a time-consuming one. Digital solutions can automate this process, offering features like automated reminders when maintenance is due. This reduces the likelihood of missed maintenance checks, extending the lifespan of your equipment, and maximizing ROI.
Compliance Management
Compliance is another area where digital tools shine. They can automate compliance checks, ensuring that your equipment meets all necessary safety and regulatory standards. This not only reduces the risk of non-compliance penalties but also contributes to a safer workplace.
Data-Driven Decision Making
The use of digital tools in equipment management can offer a goldmine of data. This data, when analyzed, can provide valuable insights into equipment performance, usage patterns, and maintenance needs. These insights can aid in strategic decision-making, helping you optimize your equipment management practices for improved efficiency and cost-effectiveness.
Remote Access
Digital solutions often offer mobile compatibility, allowing managers to access and manage their equipment data from anywhere, anytime. This flexibility can be a game-changer in swiftly responding to equipment issues, thereby reducing downtime.
Streamlining Workflows
By automating routine processes, digital tools can free up time for managers to focus on more strategic tasks. These solutions can handle everything from scheduling maintenance checks to tracking equipment usage, taking a significant load off the manager's shoulders.
Empowering Construction Equipment Management with Xenia
In the world of construction, Xenia stands out as a powerful ally that can revolutionize your construction equipment management. This robust software solution is packed with a plethora of features specifically designed to meet the unique needs of the construction industry. Let's delve deeper into how Xenia can transform your equipment management practices:
Real-Time Equipment Tracking
Xenia's sophisticated tracking system gives you real-time visibility of your entire equipment fleet. This includes live updates on location, status, and usage of each piece of equipment. This real-time information can help you prevent equipment loss or theft, optimize utilization, and swiftly address any equipment-related issues.
Automated Maintenance Scheduling
With Xenia, you no longer need to keep manual track of maintenance schedules. Xenia's automated system sends timely reminders when maintenance is due, ensuring that no maintenance task falls through the cracks. This not only prolongs the lifespan of your equipment but also ensures that they are always operating at peak efficiency.
Compliance Management
Compliance is a breeze with Xenia. The software conducts automated compliance checks, ensuring that each piece of equipment adheres to the required safety and regulatory standards. This reduces the risk of non-compliance penalties and contributes to a safer job site.
Data-Driven Insights
Xenia does more than just collect data; it helps you make sense of it. The software offers powerful analytics capabilities that can analyze your equipment data and provide valuable insights. These insights can inform your decision-making, helping you identify inefficiencies, anticipate equipment needs, and make strategic decisions that boost productivity and cost-effectiveness.
Remote Access
Xenia's mobile compatibility means you can manage your equipment from anywhere, anytime. This flexibility allows you to swiftly address equipment issues, manage your equipment inventory, and make critical decisions on the go, reducing equipment downtime.
Streamlined Workflows
Xenia automates routine equipment management tasks, freeing up time for you to focus on strategic planning and decision-making. From scheduling maintenance checks to tracking equipment usage, Xenia handles it all, allowing you to manage your equipment more efficiently and effectively.
Customizable Dashboards
Xenia understands that each construction operation is unique, which is why it offers customizable dashboards. You can tailor your dashboard to highlight the information that matters most to you, providing a quick and comprehensive view of your equipment management status at a glance.
User-Friendly Interface
Despite its powerful capabilities, Xenia is incredibly user-friendly. Its intuitive interface makes it easy for anyone on your team to navigate, reducing the learning curve and ensuring that you can hit the ground running with your improved equipment management practices.
.webp)
%201%20(1).webp)