If you’re here, chances are you might already know that Computerized Maintenance Management Systems (CMMS) make overall work easier and add up to optimal performance levels for any type of facility.
However, in actuality, these antique software are too often inaccessible and costly for use and deployment. They are difficult to install, many months of team training are required, and the user interface is not user-friendly or ergonomic. In an age of smartphones and ultra-intuitive mobile applications, the contrast is unlimited.
Lack of motivation and involvement from maintenance teams and machine operators results from these defects and the implication and use of these tools, which must nevertheless simplify their tasks but which, in practice, can complicate them.
There are many examples of companies that have wanted to implement software dedicated to industrial maintenance but have faced major difficulties on their own. The adoption of such a solution raises both technical and practical problems indeed dragging teams unable to appropriate this potentially very useful and in reality very unergonomic tool.
More than 2.25% of firms with at least 30% of their operating budget to preventive maintenance is spent on preventive maintenance exceeding 80% of the maintenance budget, communicating the urgent need to have efficient and cost-effective maintenance management in place. It simplifies maintenance operations allowing your company to reduce downtime while increasing the overall efficiency of your maintenance practices
Mobile CMMS are software applications that allow access to CMMS capabilities from a smartphone or tablet. That means you and your team can stay up-to-date no matter where you are. It is this “mobile” functionality that sets it apart from normal, traditional software, which also handles all those maintenance management tasks.
This permits management of the firm’s asset data from anywhere, at any moment. They can be accessed from any device that is connected to the internet and has a web browser. The software works excellently when the mobile device is disconnected. When back online, the data syncs automatically.
To benefit the most from mobile CMMS, one must comprehend and execute optimum practices. In this article, we have discussed selecting CMMS and highlight critical guidelines to boost your CMMS experience.
Priced on per user or per location basis
Available on iOS, Android and Web
What Is a CMMS?
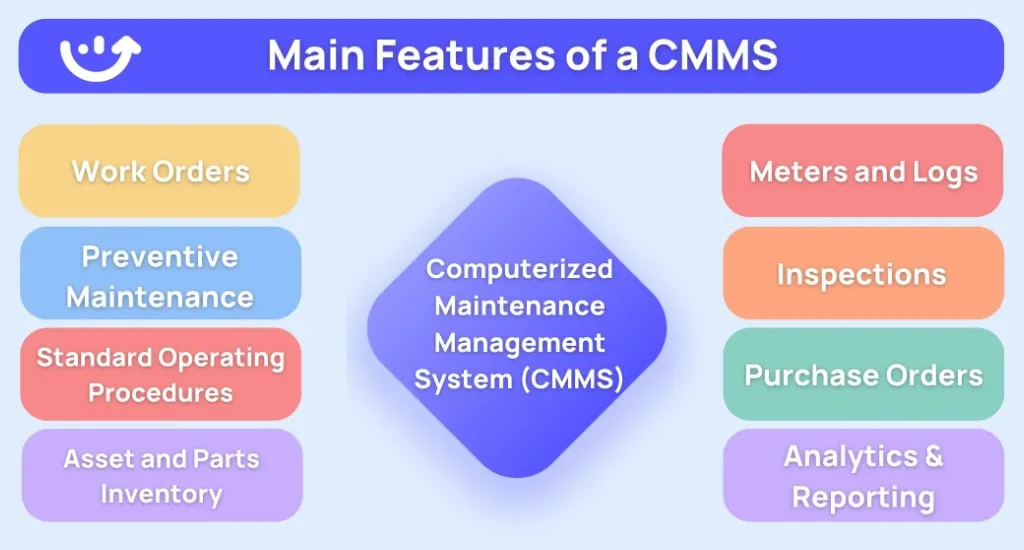
A CMMS, or computerized maintenance management system, is a software program that is used to help businesses manage their maintenance operations more effectively.
It allows users to track and manage work orders, schedule and assign maintenance tasks, and keep records of equipment and inventory.
This can help businesses save time and money by ensuring that their equipment is properly maintained and by reducing downtime due to equipment failures. A CMMS streamlines and simplifies many of the tasks involved in maintaining your facility including:
- Work order management
- Preventive maintenance scheduling
- Safety and quality inspections
- Process standardization and accountability
- Asset and parts management
- Analytics for decision making
- Reports for compliance
CMMS is used in 59% of those cases followed by predictive maintenance and reliability centered maintenance with 48% and 29% respectively.
That being said, CMMS programs aren’t all the same, because of the wide array of industries that have maintenance programs.
Maintenance in a hotel or school looks very different from an oil refinery or manufacturing plant. For this reason, CMMS platforms differentiate from each other in a few key areas:
- Feature set breadth
- Granularity of data collection
- Customizability of reporting
- Cost and pricing model
- Design, ease of use and implementation
What are Different Types of Mobile CMMS?
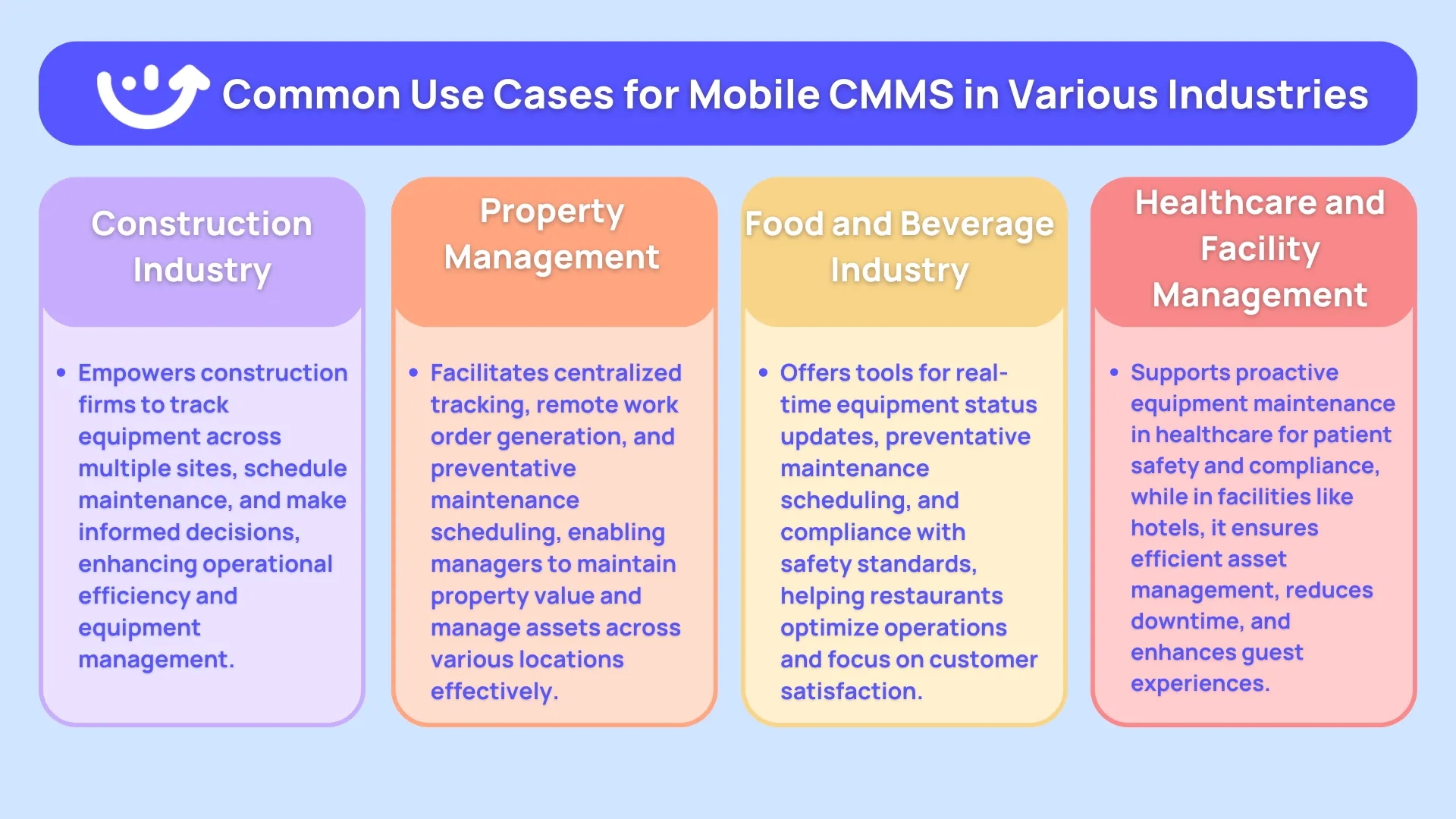
Several types of mobile CMMS (Computerized Maintenance Management System) software solutions are available to meet the unique demands and preferences of different enterprises. Organizations can choose the best mobile CMMS software for their specific needs because there are so many options available.
- Cloud-Based CMMS
Web-based systems can be accessible from any device with an internet connection. This implies that users can profit from CMMS by logging in and using WiFi or data.
Most web/mobile systems provide real-time updates as data is deployed, entered in the field, and sent back to the centralized CMMS.
Because web-based solutions are cloud-based, and most have their own unique servers and data centers, they make use of cloud technology with servers located all over the world.
- Native Mobile App
Native mobile CMMS is designed for certain mobile operating systems, such as iOS or Android. These apps can fully utilize the smartphone's abilities operate entirely on the device, and give excellent performance. Native applications for CMMS are often downloaded and installed from an app store.
- Open-Source CMMS
Open-source means the source code is available for anyone to use. While open-source often results in free CMMS, this is not always the case.
There is a difference between open (as inaccessible) source software and free software. Because the source code can be accessed, open-source ensures you are getting what you need – be it a basic CMMS package, or a robust enterprise-level system.
- On-Primise CMMS
Selecting this CMMS means the organization has to run its server, always connected to the internet, and available to the entire facility network.
This means the customer is responsible for having the correct IT infrastructure available, issuing internet user credentials for their network, releasing updates and security patches, no trial runs while installing new features, implementing security practices, installing and updating equipment, licensing, connectivity becoming a major project and ongoing high retainers for assistance.
- Industry Specific Mobile CMMS
Some mobile CMMS solutions are specifically designed for certain industries. This includes CMMS for manufacturing, healthcare, transportation, and facilities management for example. Many of these industry-specific mobile CMMS have specific features and functionalities built into them that are designed to specifically address the challenges associated with that industry.
Roles and Use Cases for Mobile CMMS App in Various Industries
- Construction Industry
Every day, construction organizations face a variety of challenges, including timely delivery, perfect equipment, employee overtime, and so on. Using a manual procedure to repair its equipment does not fully satisfy its challenges.
Spare parts and equipment are dispersed throughout the construction site and across multiple construction sites, which makes you wonder how you will maintain them from a single location, and the cost of maintaining those construction equipment cannot be properly managed using a paper-based system.
By implementing Mobile CMMS App, construction firms can enhance their operations and address all of their issues.
- Track all equipment properly and effectively.
- Schedule the maintenance work.
- Send an alert so that no maintenance tasks are left unfinished.
- Optimize the usage of building supplies.
- Provides equipment usage and historical data to support effective and informed decision-making.
- CMMS enables construction industry managers to monitor several sites' performance from a single location.
- Mobile CMMS produces relevant data and insights that help in decision-making.
- Property Management
Maintenance is an ongoing process in property management. After all, the primary difficulty for property management businesses is to maintain the property value. The more deteriorated the property, the lower the value of the physical asset.
As the number of assets and locations grows, it becomes increasingly difficult to maintain them manually.
Mobile CMMS app enables managers to physically monitor all of the apartments spread over several places. Moreover, using CMMS during the maintenance process makes tasks easier and faster. A CMMS assists property management organizations
- Keep track of maintenance from a central location.
- Generate work orders from a remote location.
- Schedule work orders and assign maintenance personnel from remote locations.
- Send out notifications for preventative maintenance
- Maintenance staff may submit photographs and concerns to the facility management without visiting the spot.
- The facility manager can deal with emergency circumstances.
- Provide insights and trustworthy facts to help with decision-making
- Food and Beverage
Following the pandemic, 26% of food firms consider themselves "tech-forward". This figure suggests that a significant proportion of food businesses have actively and consciously chosen to adopt more digital solutions, such as digital tools for ordering, contactless payment processing, inventory tracking, data analytics, and even mobile-based maintenance management systems.
Operating a restaurant is a challenging and logistical job that requires several departments to collaborate to ensure efficiency.
Sewer gas is an example of neglected, non-working restaurant equipment that can cause deadly explosions in huge restaurant buildings around the city. Equipment faults and accidents are unavoidable, so restaurants employ at least two Professional Maintenance Staff at each level.
Incorporating a mobile CMMS into the equation enables restaurants to optimize their in-house maintenance operations, free up time for in-house staff to focus on guest care, and seamlessly integrate repair work orders.
It enables restaurant workers to prioritize the all-important critical path, putting customer satisfaction at the top of the performance matrix.
- From equipment repairs to facility maintenance, CMMS for mobile devices guarantees efficient work order management.
- Technicians may utilize mobile devices to deliver real-time information on the state of kitchen equipment, allowing them to resolve issues more quickly and save downtime.
- Restaurants may use mobile devices to plan preventative maintenance work and comply with hygiene and safety laws.
- Ensuring compliance with food safety requirements and arranging recalls if needed.
- Remotely monitor equipment status and performance with mobile CMMS.
- Healthcare Industry
Patient safety is a major concern for healthcare organizations, and faulty equipment poses a threat to the quality of care provided. When healthcare providers use manual, paper-based maintenance processes, equipment is more likely to be overlooked, which increases the chances of unprecedented breakdowns and interruptions to critical care units.
In addition to patient safety, organizations must adhere to strict operating standards and guidelines to deliver a reputation-worthy healthcare service to many patients each year.
- Mobile CMMS allows for proactive scheduling of equipment maintenance, lowering the risk of unexpected failures.
- help to keep compliance with safety rules and care standards.
- The visual monitoring features of mobile CMMS enable hospital management to track equipment problems in real-time.
- Facilitates transaction-based recordkeeping, ensuring that all maintenance activities are correctly documented.
- ensures precise management of essential medical equipment such as computers, defibrillators, ECG machines, surgical units, patient monitors, sterilizers, and others.
- Contributes to providing the best possible patient care by ensuring that diagnostic, therapeutic, and monitoring equipment is reliable and in working condition.
- Facility Industry
Tenant and guest satisfaction can be difficult for facility managers to achieve based on the diverse needs and often conflicting requirements of the individuals.
Besides the volume of participants, employees, and guests, the management of facilities operations is extremely important to provide a positive experience for all.
Across a hotel’s infrastructure, from boiler rooms to computer networks, keeping assets running at the highest level is crucial to minimize costly downtime and maximize efficiency.
- Mobile CMMS designed specifically for hotels allows managers to efficiently organize work orders while addressing the diverse maintenance needs of critical assets such as circuit breakers, computer networks, HVAC equipment, parking structures, cameras, and more.
- Schedule preventative repair tasks to improve asset management, reduce downtime, prevent service disruptions, and provide a smooth visitor experience.
- The implementation of CMMS leads to a better customer experience by ensuring that facilities and amenities run efficiently and fulfill the
- Mobile CMMS allows hotel managers to efficiently manage a wide range of systems, ensuring that each component performs properly.
Why is Mobility in Maintenance Important?
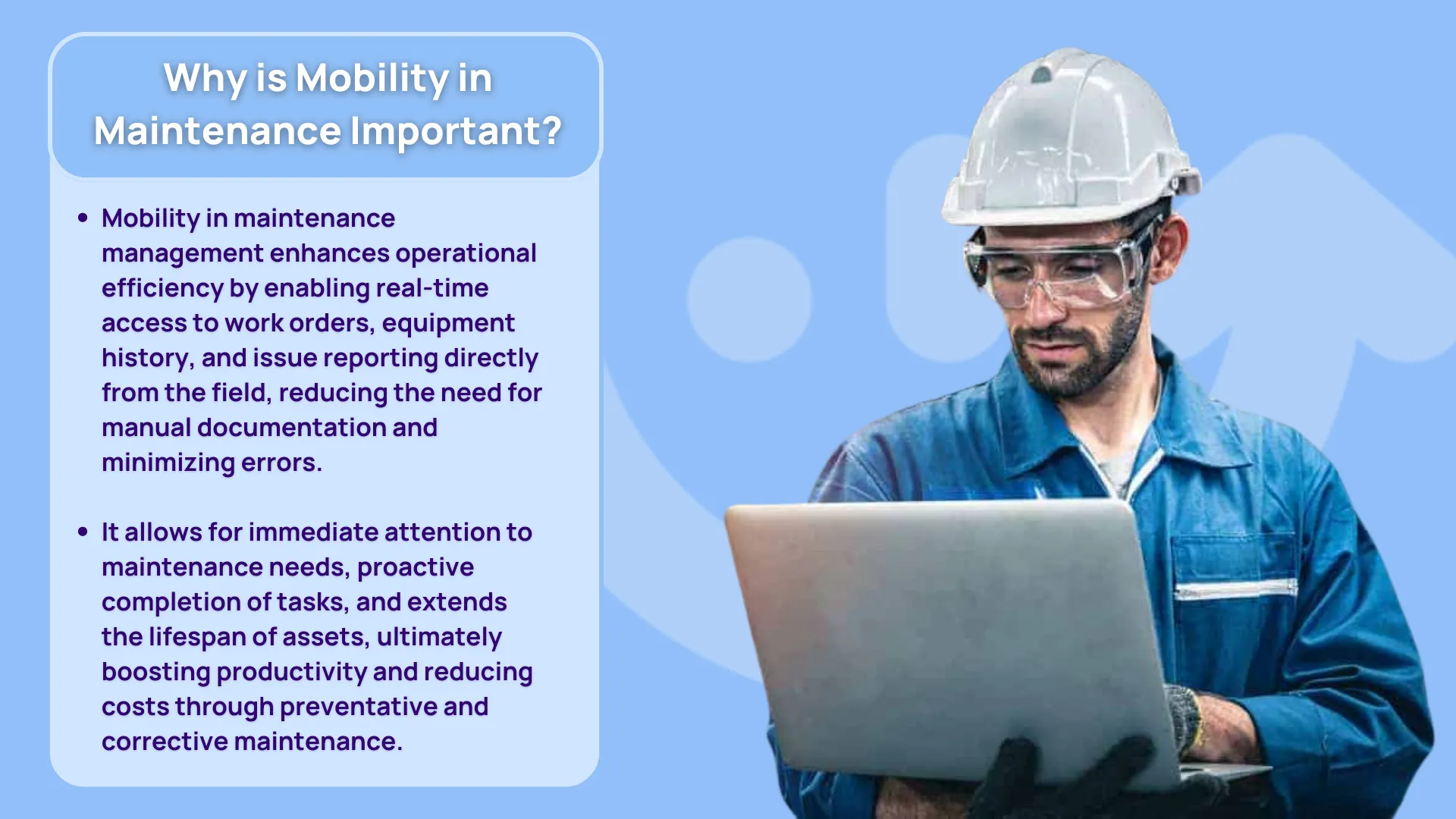
A key advantage of mobility in maintenance management is the accessibility to information; mobile devices and applications make it possible for technicians to receive work orders, access equipment history, and report issues, all from wherever they are located.
Technicians can create work orders using real-time, up-to-the-minute equipment data using their mobile devices, which speeds up the maintenance process and ensures that information is always up to date.
Technicians can also provide accurate equipment readings and inspection results, so there is no need for manual documentation where errors can be made.
Maintenance teams are no longer constrained by the limitations of the desk nor the bond of the location; mobile users can be anywhere and service any task.
Service technicians equipped with mobile devices can attend to maintenance needs immediately – as in yet still, before issues escalate – optimizing overall operational efficiency whether they are grouped on a manufacturing shop floor, standing along the infinite pipeline of a virtual construction site, or spread out across remote facilities.
Mobile apps also allow for scheduled and unscheduled preventive maintenance tasks.
This means that your company now has a proactive way to complete tasks to extend the lifespan of your asset. Preventive maintenance minimizes unexpected breakdowns, saving on downtime and in turn, costs money.
So, what's the business case for mobility? A mobile CMMS app allows you to...
- boost employee productivity, reduce maintenance costs via preventative and corrective maintenance, and protect company data with security policies and encryption.
- Distribute and manage internal and external apps on end devices.
- Using a remote control tool, you can solve the difficulties of your end customers in real time.
- With indicators and reports, you can monitor the functioning of your device and application.
The Significance of Going Digital with CMMS
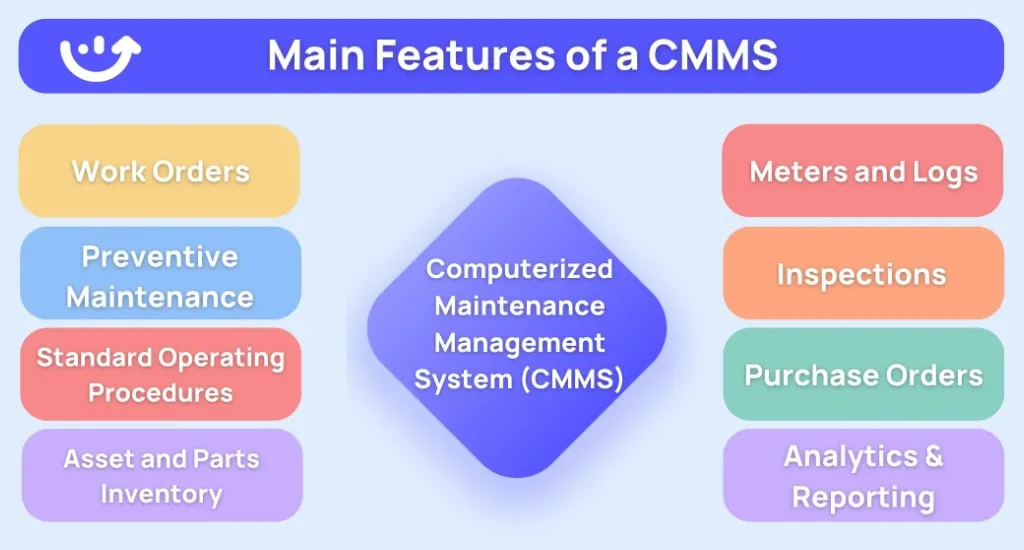
The digital transformation of maintenance management is more than just adopting technology. It’s a complete shift in how organizations approach and execute their maintenance strategies.
This digital transformation changes several key factors that are needed, focusing on efficiency, agility, and proactive decisions. Here’s a closer look at how digitization is transforming maintenance management.
- Real-Time Visibility
With real-time visibility and accessibility, digital maintenance management gives teams, knowledge of the status of assets, work requests, and tasks is always at their fingertips.
Teams can respond quickly to issues anywhere making downtime a thing of the past and making overall operational efficiency soar.
- Agile Work-Order Management
Digital platforms simplify the management of work orders, enabling tasks to be quickly created, assigned, and tracked. This eliminates the need for manual steps, greatly reducing the chance for error and ensuring that maintenance work is done on time and to specification.
- Data-Driven Decesion
CMMS mobile application generates detailed reports and analysis, enabling companies to make data-driven, educated decisions. Maintenance plans can be transformed based on previous performance data, resulting in increased operational efficiency and resource effectiveness.
- Automation Efficiency
Embedded automation features in CMMS mobile application automate routine tasks such as preventive maintenance scheduling to report generation. This reduces manual workload and guarantees consistency and accuracy in maintenance processes.
- Integrations
IT integration with other business systems like ERP and inventory management. The integrated approach toward a holistic view of organizational processes ensures the creation of synergy as well as enhancing operational overall efficacy.
- Improved Collaboration
Maintenance teams benefit from enhanced collaboration facilitated by digital platforms; maintenance environments are more coherent and responsive thanks to immediate updates, information sharing, and real-time communication.
- Cost-optimization and Resource Allocation
Digitization enables organizations to reduce costs by finding inefficiencies and implementing targeted improvements. Better resource allocation, led by data insights, means that maintenance activities are prioritized according to strategic objectives.
- Cultural Shift towards Preventive Maintenance
Most significantly, digitization leads to a cultural shift within organizations. The transition from reactive to proactive maintenance becomes a part of the organizational psyche, fostering a culture of continuous improvement that permeates all levels of maintenance management.
Selecting Mobile CMMS App– Pros vs. Cons
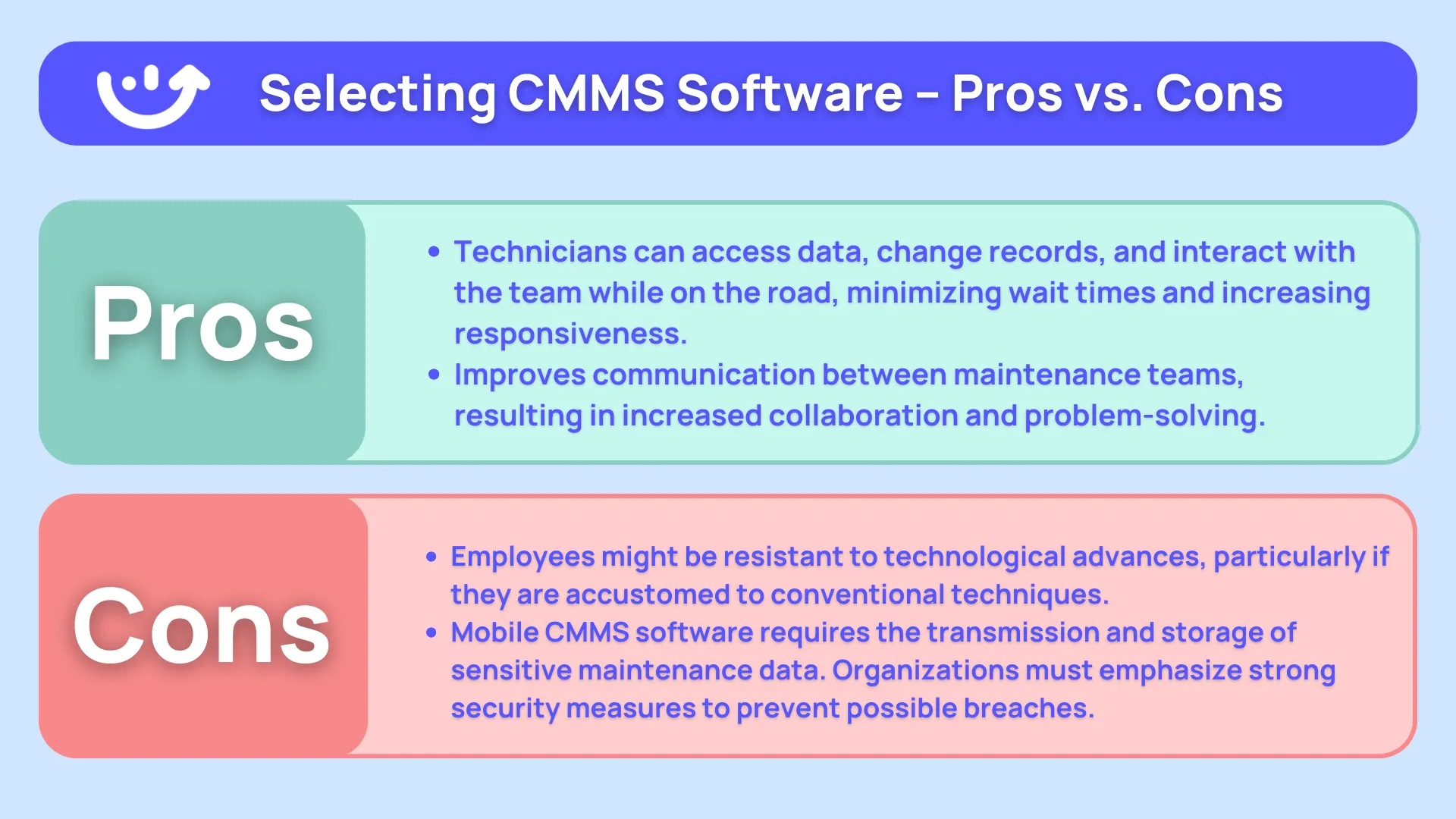
The initial step in determining the overall success and applicability of any system or technology is to balance its advantages and disadvantages.
Pros
- Technicians can access data, change records, and interact with the team while on the road, minimizing wait times and increasing responsiveness.
- Improves communication between maintenance teams, resulting in increased collaboration and problem-solving.
- The utilization of real-time data decreases the possibility of documentation mistakes and gives decision-makers with current information to have a better understanding of maintenance efforts.
- Mobile CMMS enables proactive maintenance planning, allowing firms to schedule preventive work to save downtime, increase asset lifespan, and reduce the chance of unexpected breakdowns.
Cons
- Deploying a mobile CMMS system might require initial investments in software, gear, and training.
- Employees might be resistant to technological advances, particularly if they are accustomed to conventional techniques.
- Mobile CMMS requires the transmission and storage of sensitive maintenance data. Organizations must emphasize strong security measures to prevent possible breaches or unauthorized access.
- Technical concerns with mobile devices might include compatibility issues, software flaws, and connectivity issues. These issues can disturb the smooth running of a mobile CMMS and must be addressed promptly.
What are the Challenges Regarding Mobile CMMS Implementation and How to OverCome?
Adopting a digital maintenance management system (CMMS) might add a layer of complexity. Aspire that the difficulties will differ by industry since each sector has its own unique technological and business operations.
- Accurate Data Transfer
Sharing information around to ensure exact recordkeeping and planning might be difficult. There is a lot of information to consider while transferring, such as asset descriptions, maintenance history, and work order timelines.
For example, in the manufacturing business, transitioning from paper records or an older maintenance system to a CMMS mobile application that integrates with an ERP system necessitates careful data conversion.
To effectively handle the issues of converting from an outdated maintenance system or paper records to a CMMS connected with an ERP system, a well-planned and methodical data conversion strategy is required.
Begin by doing an audit of the available data to determine which information is most significant, such as asset descriptions, maintenance histories, and repair order time frames. Create a thorough data map that specifies how each information type will be transferred and integrated into the new system.
- Integrations
To prevent CMMS from failing to capture data from processes, stakeholders need to achieve CMMS compatibility with other business systems or IoT devices.
Especially in industries like property management, where the CMMS integration with Building Management Systems (BMS) or IoT components is essential in maintaining a smart, interconnected building. If even one sensor or controller malfunctions then CMMS integration with the existing process will be incomplete.
Plant Engineering reports that 25% of those surveyed said they recognize the impact IoT will have on how maintenance personnel interact. In other words, one in four believes the IoT’s integration into maintenance will not only enhance efficiencies but also change how communication takes place within organizations.
Securing seamless integration between CMMS and other enterprise applications or IoT units is a crucial element in obtaining holistic data and retaining process efficiency, especially in industries like property management.
Among other planning activities, stakeholders must give priority to CMMS compatibility with Building Management Systems (BMS) and IoT initiatives to realize a smart and connected building.
- Workflow Redesignation
To incorporate a CMMS into the existing workflows, existing maintenance activities need to be reassessment, redesigned, and modification likely.
Adaptation must not conflict with ongoing operations, it has to coordinate CMMS testing and implementation and it has to walk through together.
For example, it is necessary to reform existing production lines in manufacturing industries when CMMS is integrated to accommodate both maintenance jobs and production scheduling simultaneously.
When implementing a Computerized Maintenance Management System (CMMS) to existing procedures, managers must employ a methodical and gradual approach to reassess, revamp, and modify maintenance tasks while preserving the business’s daily routine.
The coordination involved in the testing of the CMMS to its implementation and subsequently to its daily operations is of utmost concern.
- Adherence to Regulatory Compliance
Ignoring the requirement to adhere to business-specific regulations and move the integrated CMMS into compliance status may result in serious repercussions. In the energy and utilities space, for example, an implementation of the CMMS mobile application that does not meet NERC criteria for electric utilities may result in grid quality issues and regulatory fines.
Mitigating these risks requires conducting a thorough regulatory assessment at the onset of CMMS integration. Identify and comprehend the applicable regulations for your particular industry and make certain that the CMMS can be configured to satisfy those particular requirements.
This might mean adding the necessary features, protocols, and reporting mechanisms to ensure compliance.
- Inaccurate Asset Classifications
Incorrect classification of your assets within your CMMS can lead to inefficient allocation of resources. Within the utilities and energy sector, the failure to rank the criticality of your assets will lead to improper planning of maintenance on essential infrastructure and can result in expensive breakdowns.
Begin by performing an extensive evaluation of all assets and classify them according to their significance to operations. Determine key performance indicators and variables such as dependability, consequences of failure or malfunction on safety, and supports on overall system performance.
Consult with stakeholders being representatives of maintenance teams and experts to garner opinions on asset criticality.
- Incorporating Complex Mobile CMMS
Incorporating overly complex features or functionalities that may not be needed will result in unnecessary complexity-- that is, new problems.
This will confuse users and may lead to underutilization of the CMMS mobile application, thus undermining its core idea, and integration into the existing process.
To prevent unnecessary complexity in a computerized Maintenance Management System (CMMS), opt for a user-centered design approach.
Focus on the features that are most important to the users and the core CMMS objectives. Ensure that the functions fit smoothly into the existing processes.
Why Your Business Needs a CMMS in 2025
This has led to a need for management systems that are not only easy to use but also provide accurate data collection. Computerized maintenance management systems offer this functionality and more.
A computerized maintenance management system allows you to create standardized processes that can be easily replicated across multiple facilities while also providing detailed information on each individual operation within your facility.
This type of system will allow you to track all aspects of each operation and quickly identify areas where improvements can be made or issues need to be addressed.
This will help you meet customer expectations as well as improve overall operational efficiency which can save money in the long run by reducing downtime caused by equipment failure or other issues related directly with poor quality control procedures.
What Makes a Good CMMS Implementation?
You must know what you want to achieve before using a CMMS. Knowing what you're shooting for and why it's important will significantly help. While every company has its own specific CMMS implementation goals, there are a few universal targets that every maintenance team should aim for.
1. Are You Exceeding Your Performance Targets?
Whether it's lowering expenses, increasing safety, or decreasing downtime, every maintenance department has aims. No matter what your objectives are, a well-executed CMMS rollout will get you there.
Nothing will happen overnight; you'll have to put in some time and effort beforehand, including figuring out what you want to accomplish and whether or not a CMMS can assist you in doing it. You can get the outcomes you want from a CMMS if you design and execute it correctly.
2. Ensure Company-Wide Alignment
Disarray and confusion ensue when there are a lot of systems or procedures to keep track of. By centralizing all maintenance operations and information, a well-implemented CMMS can avert this worst-case situation.
A set of guidelines for system use and maintenance should be established. Connecting your CMMS to other operational systems and implementing the system and its procedures at every location are also components of uniformity.
3. Is Everyone Using The System?
The right individuals must routinely and correctly utilize CMMS for it to be effective. Users' buy-in is vital for this reason. The user adoption rate quantifies the proportion of individuals who use the technology in accordance with its intended purpose.
As an example, if 20% of technicians just use the systems for some jobs or do not use them at all, it indicates that your user adoption rate is 80%. In order to ensure accurate data collection, efficient work, and no tasks are skipped, user adoption should be 100%.
You might be wondering, "Is it really that significant to implement a CMMS?" Most definitely. Moving from an outdated system to a new way of doing things requires a significant cultural transformation in addition to a large financial and time commitment on the part of your business.
4. Is the CMMS Propelling Organizational Advancement?
Your maintenance team's digital transformation shouldn't begin with implementing a CMMS. If your CMMS implementation isn't up to par, all your operation will see are superficial adjustments to the current state of affairs.
A company gains momentum, resources, and inspiration to continue growing after an effective implementation. The maintenance department and beyond can gain from an environment that encourages creative problem-solving and development if the implementation is done correctly.
CMMS Implementation Requires The Right Fit Software
Given this landscape of CMMS options, it is essential to pair the right technology with the skills and abilities of the frontline that will be using them. For highly technical professionals or complex mechanical systems, a heavier weight, more powerful CMMS may be warranted.
But more powerful is not always better. For many industries, the added features confuse and distract the workforce leading to poor data collection and low adoption rates.
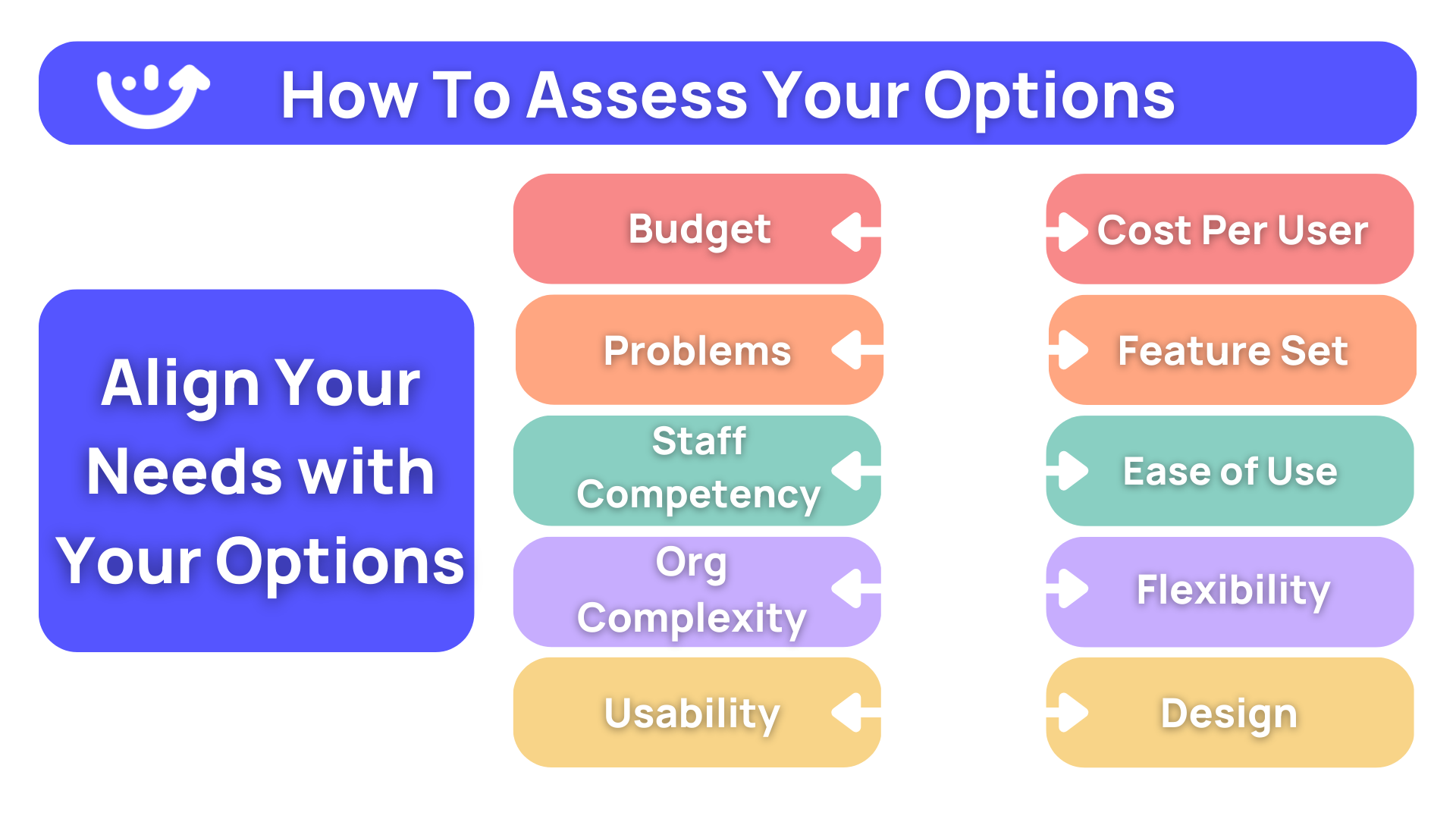
👥 Start with a Staff Assessment
To be successful in implementing software, managers must have a firm understanding of their employee skill sets and the training that will be needed to maximize success. Overlooking the risk of failed adoption is a huge mistake and it is better to overtrain than leave stones unturned.
Before you begin shopping for software, create an assessment of your staff that will be using the program. Note their technical skills and speed to learn new systems. Identify likely early adopters, and those that may need more support. Use this information to decide the level of complexity that can be onboarded effectively.
💯 Determine the Scope and Set Priorities
After you have assessed your staff, move on to listing out the assets in your facility along with details such as replacement cost, repair frequency and cost, impact of downtime, and complexity of maintenance. This will help you to understand the maintenance processes that will drive the most value in protecting your assets.
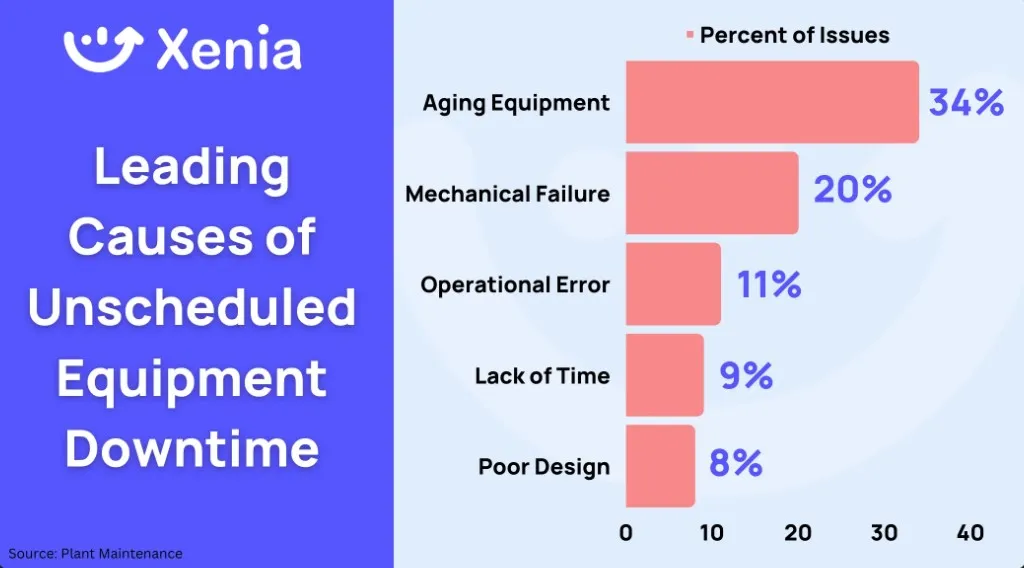
A big risk of shopping for software is getting too caught up in side by side comparisons of features. Features are important, but typically 20% of the features drive over 80% of the usage of software.
It is better to begin with the problems that your business needs to solve, prioritize them and then seek out software that solves those problems in the easiest (or cheapest) way possible. Use this list as your starting point and then look at the differentiating features to determine your final choice.
💰 Understand Your Budget and Downside Risk
How much should you be willing to pay for a CMMS? This question is best answered by quantifying the asset assessment completed in the previous step. By understanding the scope of assets and the cost of repair, replacement and downtime impact, you can estimate the risk posed to your bottom line.
Then, as a manager, you need to decide how much of that risk is preventable and how much is inevitable.
You should also consider the impacts of improving process efficiency on these values as even inevitable downtime impact can be greatly reduced with improved communication processes.
Once you have an understanding of the cost of maintenance on your facility, and the amount that can be prevented or improved, you should have an idea as to the marginal return on investment of implementing a solution. If the marginal ROI is low, you should look for a less expensive solution.
If the marginal ROI is very high, you may want to consider a more comprehensive approach (as long as your team can handle it).
🆓 Use Your Free Trials to Test Software
The final piece of pre-purchase advice is to try a few of your software options and determine what you like or dislike about each one. Select a small set of employees to participate in the trial period and gather their feedback regularly. Perhaps you were overestimating their ability to make use of the app. Or maybe the complex feature you thought you needed doesn’t live up to your expectations. The only way to know these things is to test and learn.
Post Purchase CMMS Implementation Steps
Now that you have selected the right CMMS for your business, it is time for the most crucial step in the process: implementation. It is critical to not underestimate or overlook this step in the process. In order to ensure successful implementation, follow the following steps.
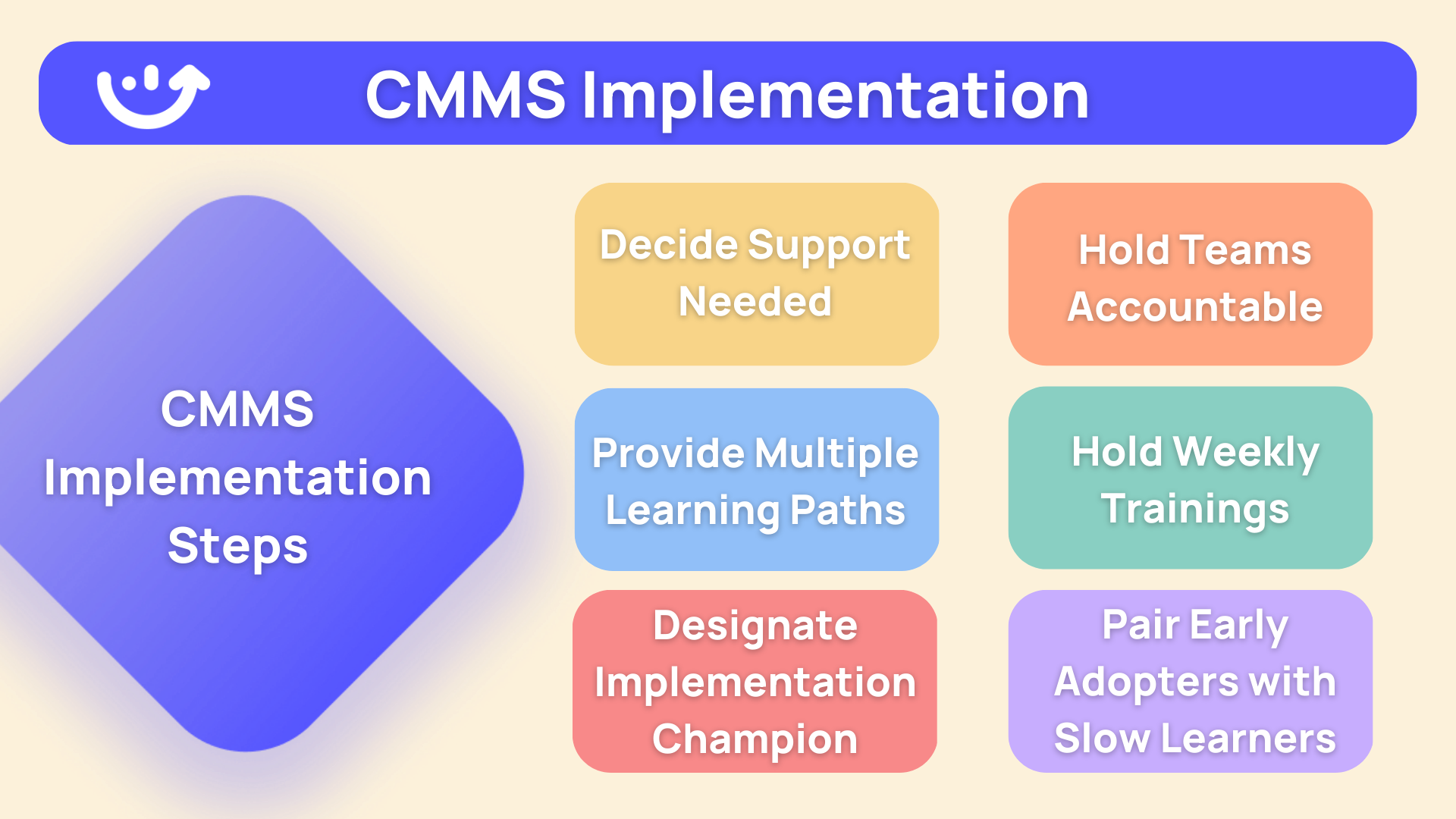
💲 Choose Between Paid or Self-Guided Implementation
Many CMMS platforms offer a paid implementation support period where one of their software experts will lead discussions and tutorials for how to best use the product. Since assets are different and CMMS platforms are highly customizable, this may be the best way to get started.
However, paid implementation can cost thousands of dollars and provide little value if your team is not paying attention and taking it seriously. Likely, you will still need self-guided implementation to subsidize the formal training.
📲 Provide Multiple Pathways for Learning
For self-guided implementation learning, it is important to leverage multiple mediums to provide different learning experiences for staff.
While some team members may learn best by reading a manual, others need a video explanation to gain understanding. Furthermore, some employees may learn by doing, thus requiring a “sandbox” environment to play around with the new tool. Other employees may learn by discussing with team members or being shown in person.
The best implementation teams leverage all of these options simultaneously.
💪 Designate an Implementation Champion
As a manager, you should have a good understanding of your star performers. Select one of these individuals to lead and own the implementation effort. Provide them a small incentive to ensure that everyone is aligned on the goal and benefits of software support in daily operations.
Provide the CMMS implementation champion with performance metrics to determine their impact on the program and have regular meetings with them to understand their perspective.
🙅 Communicate that Usage is NOT optional
A CMMS is only helpful when used consistently and correctly. This ensures that complete and accurate data is collected from the front line to be analyzed to drive better decision making.
A manager must not allow employees to say, “I like the old way better” or “this will slow me down”.
Any new process is likely to be met with opposition by some individuals. To respond to these statements, you should compare the benefits and risks of using software vs a paper or Excel based system.
You need to show how their actions directly impact the ability for the business to operate successfully. Another tactic is to explain how once trained, the time savings to the employee will start to become clear and the ability to measure work effort is greatly improved.
This ensures that no employee is overlooked or ill equipped with the necessary data to seek a raise or promotion.
🏋️ Hold Weekly Trainings with Open Feedback
Training should be held regularly and frequently, especially in the initial phases of implementation. Ease into usage by focusing on one use case at a time.
We recommend giving employees homework to begin using the CMMS to solve each use case, and then preparing questions and comments for the next training session. Allow for both public and private questions to ensure every employee is heard and no one feels outed or shy.
Once your team begins to understand and adopt the technology, managers can scale back the meetings from weekly to monthly. They can also move from formal training to office hours type sessions for questions.
👬 Pair Early Adopters with Usage Laggers
Once the training is underway and teams are using the software, it is important to identify early adopters and usage laggers within your organization. The purpose of this is to leverage your staff to free up training hours for management.
You can do this by pairing early adopters with usage laggers and incentivizing the early adopters to help train their teammate.
Often, this is a great opportunity to drive team collaboration and cohesion, which improves efficiency and retention across the department. It also provides another opportunity for shy or discouraged employees to get answers to questions without feeling embarrassed in front of management.
👿 Hold Teams and Individuals Accountable
The final advice that we have for CMMS implementation is to hold teams and individuals accountable for success.
This may look different depending on the role and individual, but is essential for ensuring success.
We recommend to use positive reinforcement of successful implementers as opposed to negative consequences for those lagging behind. This helps to drive a positive, growth mindset that is productive and supportive of all skill levels and team members.
Why Do CMMS Implementations Fail?
Hiring, onboarding, retaining staff (48%), optimizing procedures (27%), and effective technology adoption (25%) are the most prevalent problems faced by maintenance teams.
The sad reality is that between 60% and 80%of CMMS deployments are unsuccessful. The majority of these failures are caused by a few of critical errors.
Lack Of Support From Management
Companies often fail in their attempts to install a CMMS because they lack the necessary resources, such as time or money. However, this kind of failure is often caused by a lack of backing from higher-ups.
Project funding and support often come from upper-level executives. Lack of buy-in from decision-makers during implementation raises the risk of budget cuts or the project being repeatedly pushed to the bottom of the to-do list.
Unclear Goals, Roles, And Responsibilities
Without a predetermined objective, it is hard to tell if a CMMS installation was effective. Companies will not achieve their aims and users will not be motivated to utilize the system if there is no clear purpose.
When people aren't sure of their place in the company, they're more likely to make mistakes or forget important duties, which has far-reaching consequences. Both during and after setup, this can happen for activities like monitoring inventory and making sure PM triggers are triggered.
Poor User Engagement And Training
User reluctance or ignorance about the CMMS's functionality is a common cause of failed installations.
That is why it is crucial to include everyone who can be affected by the new software.
When evaluating suppliers and buying software, users should be consulted. Choosing a solution that isn't needed, is difficult to use, and is undesirable is a common result of skipping this phase.
Performance will decrease when software is selected due to insufficient training on how to properly utilize the CMMS.
Initiating CMMS Implementation: Shortcut to Operational Excellence
While CMMS software won't magically improve maintenance, it can have a significant role in getting improved outcomes.
A CMMS is just another tool that the maintenance staff should have on hand.
A CMMS, when used correctly, can function like a hammer: it makes work easier. If carried out correctly, a CMMS can evolve into a repository of maintenance-related data that can be mined for insights into how to optimize processes and spot areas for potential efficiency gains.
While it may not be an immediate solution, investing in high-quality software can significantly improve your organization's performance both now and in the future by serving as an integral part of your dependability and maintenance plan.
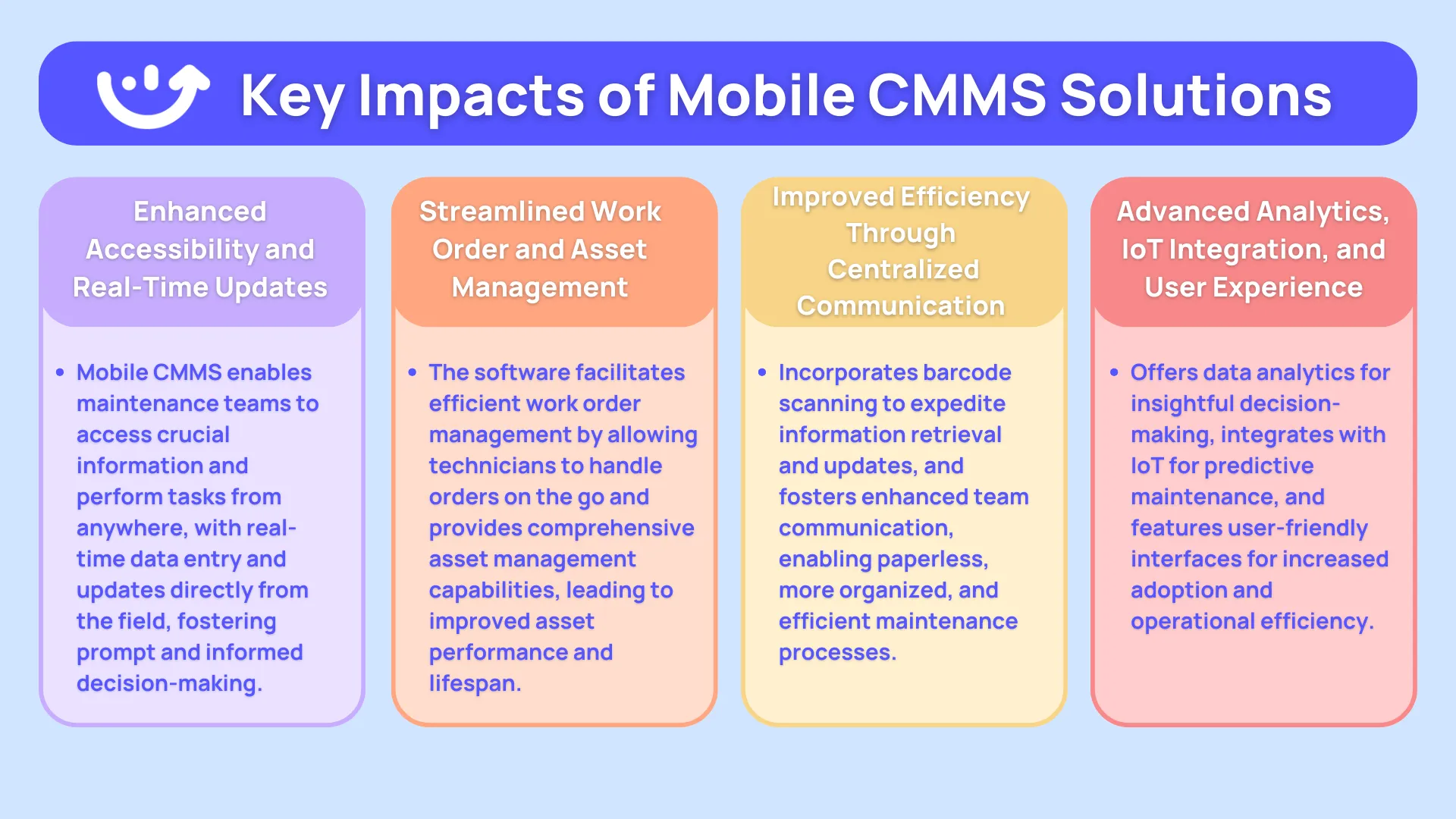
Xenia-The Best CMMS for Mobile Devices
A CMMS helps to plan and manage facility maintenance, but it will only be effective if implemented correctly. Take the time to identify all the facility and equipment types you manage, identify the ones most critical, classify assets correctly, and track those assets.
If not, you might end up wasting money on the tools you use to run your business, a very costly mistake.
On that note, Xenia is a hybrid mobile CMMS for frontline workforce management with a dedicated desktop and mobile application that can solve a variety of use cases across maintenance, operations, and people management.
The CMMS platform supports your daily operation processes like process standardization, work order management, preventive maintenance, inspections, meter logs, basic asset management, and more with a seamless mobile experience.
Also, integrated chat and flexible tools can be used for other frontline team like housekeeping, sales, customer service, security, and more.
Even though, with a core CMMS functionality, Xenia is a light version with very low set-up costs and monthly fees that are more than 50% less than the famous CMMS service.. on Focus Solutions has always delivered a high-driven return on your IT investment.
Why Xenia is the best mobile CMMS?
- A public template library with hundreds of checklists, logs, inspections, and SOPs
- A template builder for inspections for process modification and continuous improvement.
- Add unlimited photographs to work orders for transparency.
- Monitor detailed data and categorize reports for easy export.
- Integrate internal discussions with work orders for accountability and teamwork.
- Use the locations tool to specify and monitor work across the site.
- Simple to use, with low implementation risk.
.webp)
%201%20(1).webp)