Have you ever gotten a defective or otherwise disappointing product? Perhaps a piece of furniture that quickly fell apart after being put together or a gadget that failed to function properly after just a few uses?
Nothing frustrates customers more than no bang for the buck. Meanwhile, those of us who work in manufacturing are well aware of the reality that low-quality goods can have an even greater negative impact on companies.
Poor quality control is costing businesses an estimated $14.2 million a year, according to a new study. Companies can't thrive without quality control procedures.
That's where quality control software for manufacturing comes into play. From lowering production error rates to guaranteeing conformity with regulatory requirements, these software for quality control in manufacturing have addressed a wide variety of industrial challenges.
Best Quality Control Software for Manufacturing Businesses
Here's a quick run down of the best quality control software that you can potentially use to scale your business's end to end operations.
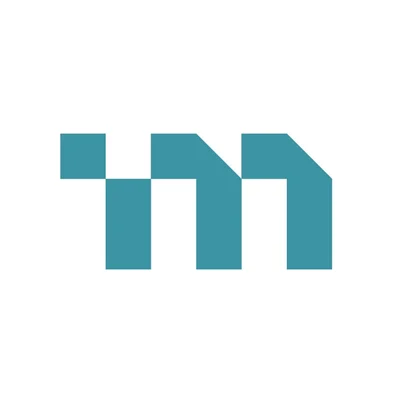
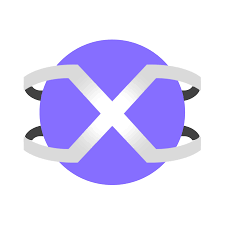
1. Xenia - Overall No.1 Manufacturing Quality Control Software
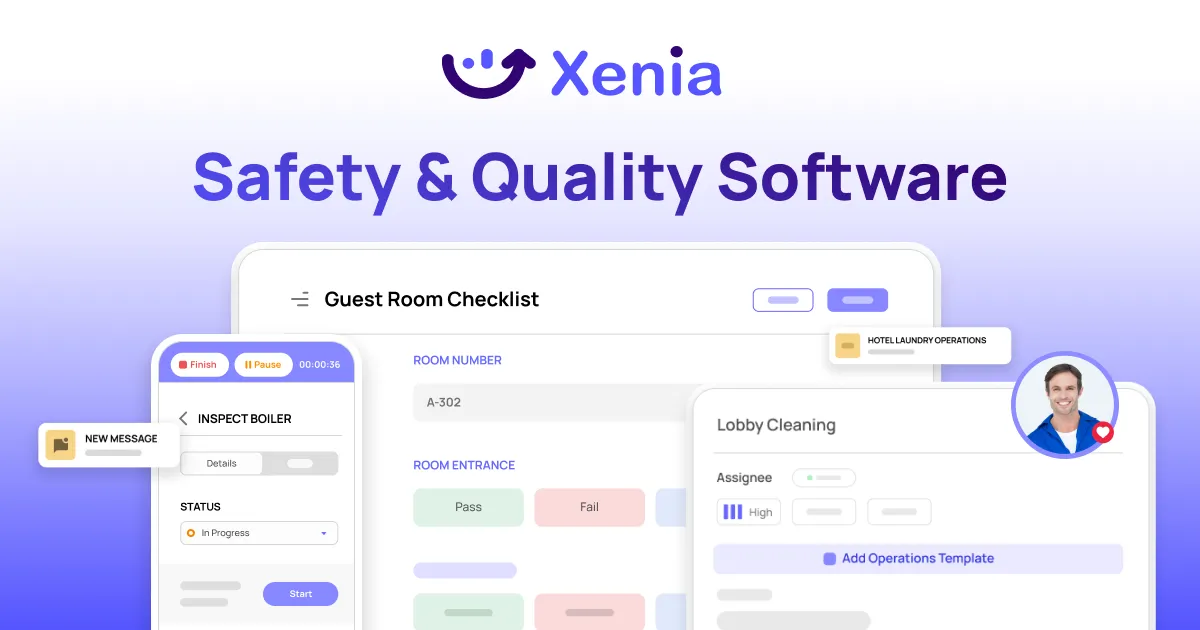
With Xenia's dynamic quality control software for manufacturing, you can increase safety, improve quality assurance, streamline asset inspections, and achieve regulatory compliance.
Remove the possibility of human mistakes associated with out-of-date systems. Digital workflows from Xenia provide correct data input, tracking, and reporting, avoiding expensive errors and assuring accuracy throughout your production processes.
It's an easy-to-use platform that allows users to schedule and execute regular manufacturing plant inspections easily, build customizable checklists, monitor outcomes, and produce thorough reports on both desktop and mobile devices.
To further your audits, use the in-app share option to share SOPs with team members, produce a downloadable PDF file for printing, and vice versa.
Get a checklist for quality control software for manufacturing free download
Key Features
- Compliance Tracking: Stay proactive with automated compliance tracking. Assign tasks, set schedules, and ensure adherence to safety standards. Enhance understanding by attaching instructional images, videos, or notes to maintain high safety standards.
- Incident Reporting: Report safety incidents swiftly using Xenia's mobile app. Capture photos and notes for each incident, ensuring accountability with time and geo-stamping.
- Corrective Actions: Optimize safety inspections with instant tasks generated from safety violations. View corrective action data in inspection reports for easy auditing and accountability.
- SOP & Document Management: Effortlessly create new SOPs and safety policies with Xenia's AI assistant. Store policies, along with videos, photos, or files, securely in a cloud-based data center accessible anywhere, anytime.
- Analytics & Reporting: To focus on certain sections of the overall project, create comprehensive reports with several charts that show the areas that are functioning well and those that need process improvement.
Pricing
- Free Forever: Free for up to 5 users with unlimited access to all the basic features.
- Starter: $99 / month for 15 users, alongside access to core features & functionalities.
- Premium: $99 / month for 15 users with access to all the core and advanced features altogether!
- Custom: Need something tailored to your organization?
Priced on per user or per location basis
Available on iOS, Android and Web
2. MasterControl
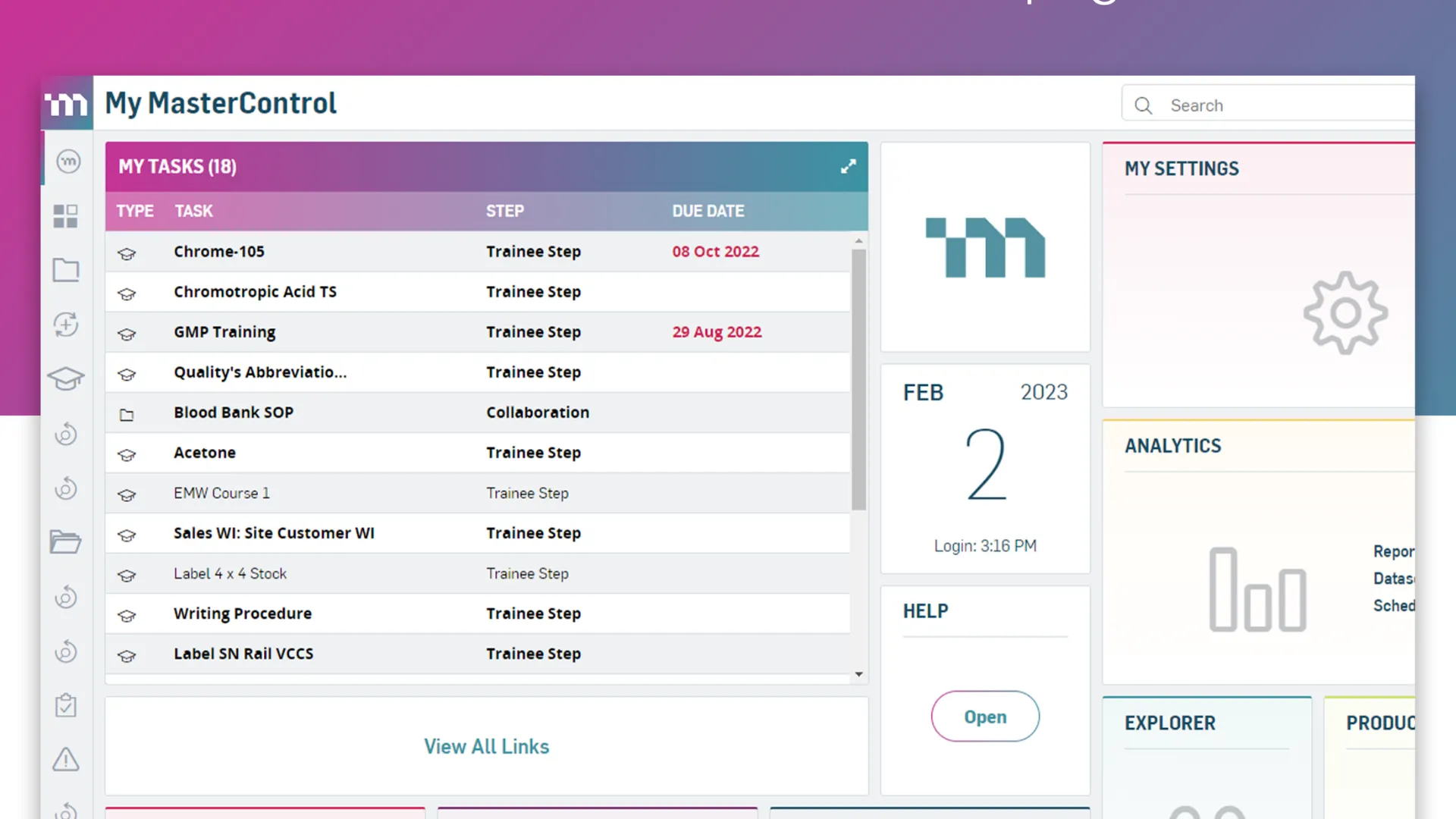
It is an automated quality control software for manufacturing that simplifies and streamlines quality control for production settings.
It is web-based. It offers a full suite of tools for quality management, such as document control, CAPA, training management, audit management, and non-conformance monitoring capabilities.
Key Features
- Quality in the Cloud: The cloud QMS software completely digitizes and consolidates formerly paper-based data and documentation, allowing for ongoing improvement of quality and compliance procedures via more regular software upgrades.
- Automated Regulatory Compliance: By automating important quality processes such as document, training, quality event, supplier, and quality audit management in a single end-to-end system, you can reduce compliance costs while improving product quality.
- Connected QMS Platform: Quality data can influence change and improvement across the whole product life cycle when it is digitalized, gathered, and integrated. This makes quality data a commodity that any firm of any size can use.
Pricing
- Contact the vendor to get a Quote-based Plan
3. Axonator
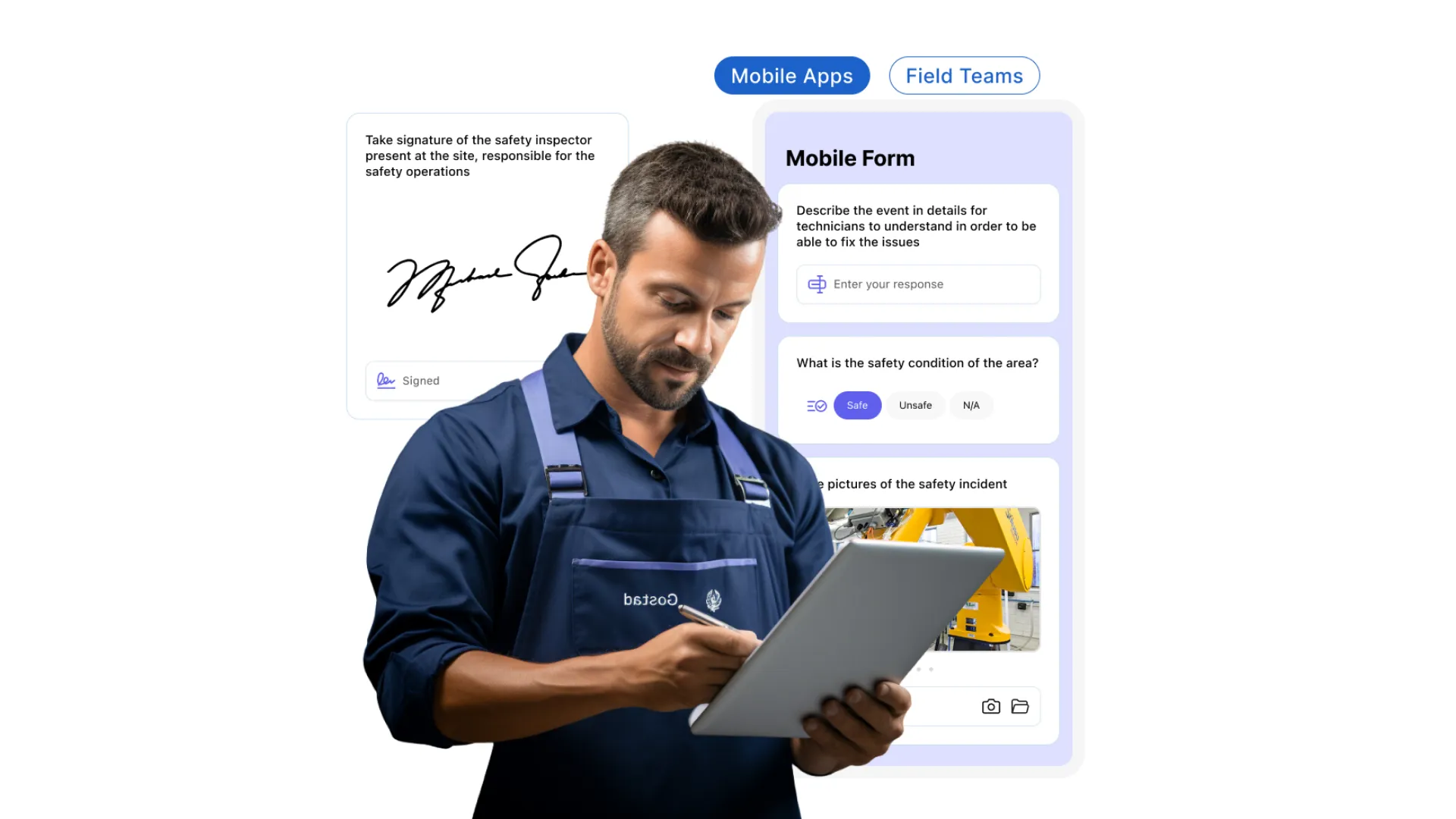
Axonator offers industrial companies a cloud-based platform for quality control software for manufacturing that can be used whenever and wherever needed.
It helps organizations save time and effort while maintaining high-quality standards by simplifying and streamlining quality control activities.
Key Features
- Asset Management: Engage in an exhaustive assessment of all asset kinds, conditions, maintenance schedules, locations, and asset work procedures to give firms the best planning, audit, and compliance capabilities.
- Inspection & Maintenance: Workflows that can be customized to automate essential inspection tasks. Send data to the relevant team automatically, get approvals, establish follow-up activities, assign remedial actions, and produce reports automatically.
- Digital Checklists: Using configurable checklists, perform preventative and predictive maintenance operations. Maintain your assets by documenting maintenance history, current condition, location, use, and so on.
Pricing
- Contact the vendor to get a Quote-based Plan
4. Qualtrax
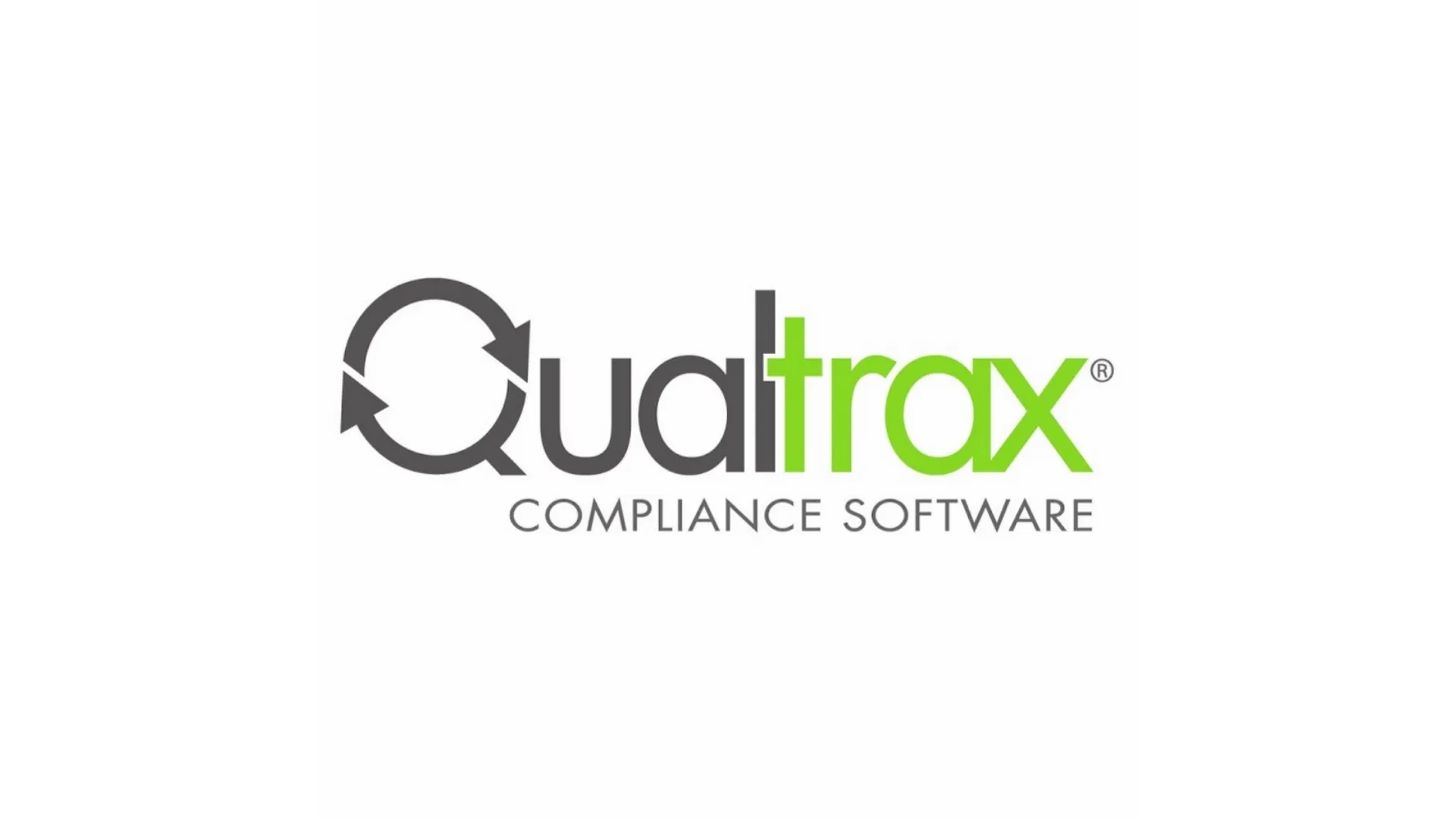
Organizations can manage their quality, compliance, and document control demands with this comprehensive compliance management software.
As one of the best quality control software for different businesses, the tool provides a consolidated system for companies to manage their policies and processes while staying in line with industry norms and standards.
Key Features
- Compliance with Standards: To ensure that auditors know precisely where to go, provide hyperlinks in your quality manual that take them straight to essential document parts, not simply the first page. Put another way, before conducting an internal or external audit, integrate each standard with the relevant artifact and quickly identify any gaps.
- Reduce Audit Prep Time: The whole feature set of Qualtrax is unique, and using it reduces audit prep time—for many clients, to almost nothing. To calibrate your quality management system, use an existing Internal Audit procedure or create your own.
- Reduce Risk Across Your Organization: By observing your processes in real-time, you can take a process-based approach to risk management. The workflow module in Qualtrax brings what you do from the whiteboard to the web, decreasing uncertainty via necessary inputs and role-based ownership at each stage.
Pricing
- Contact the vendor to get a Quote-based Plan
5. InfinityQS (Enact)
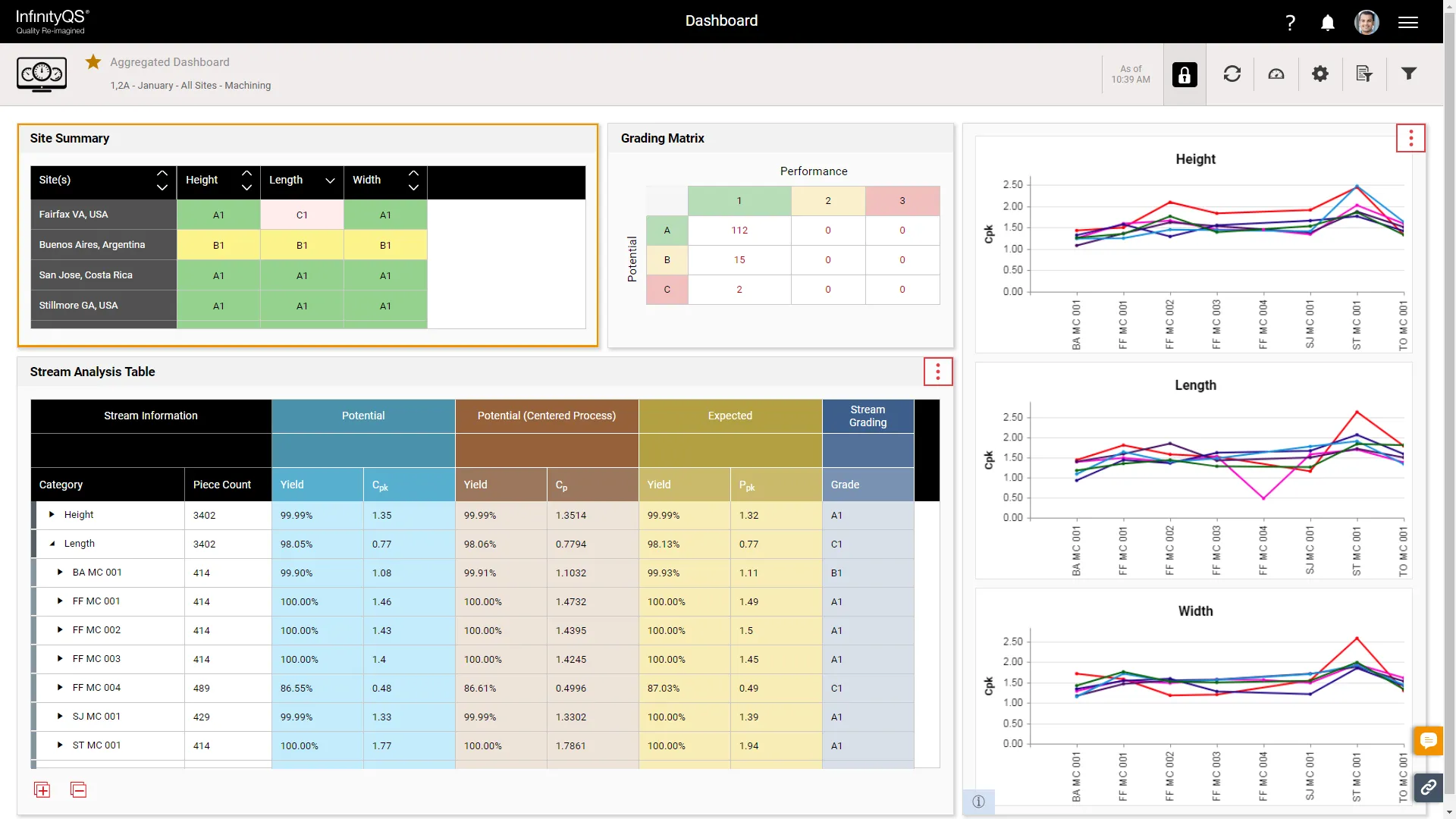
Offering real-time insights into operations, this cloud-based software solution helps businesses improve their quality management procedures.
Its purpose is to lessen the likelihood of product recalls, consumer complaints, and other quality-related concerns by assisting users in quickly identifying and fixing such issues.
Key Features
- Capture Real-Time Data: Manufacturing optimization relies heavily on consistent, dependable data. Therefore, it's time to throw out spreadsheets, paper records, and manual data input. You can utilize InfinityQS to automate the gathering of quality and process data from all of your production lines and facilities.
- Unify Quality Data: InfinityQS stores all of your data in a centralized, unified place rather than in different data silos scattered across the company. As a consequence, procedures and quality have been improved, and data analysis has become more thorough and complete.
- Improve Decision Making: The capacity to evaluate historical data from all your processes and product lines—true enterprise visibility—provides you with extraordinary operational knowledge. Feeds, speeds, temps, and weights—get all the data you need to make smart choices.
Pricing
- Contact the vendor to get a Quote-based Plan
6. ComplianceQuest
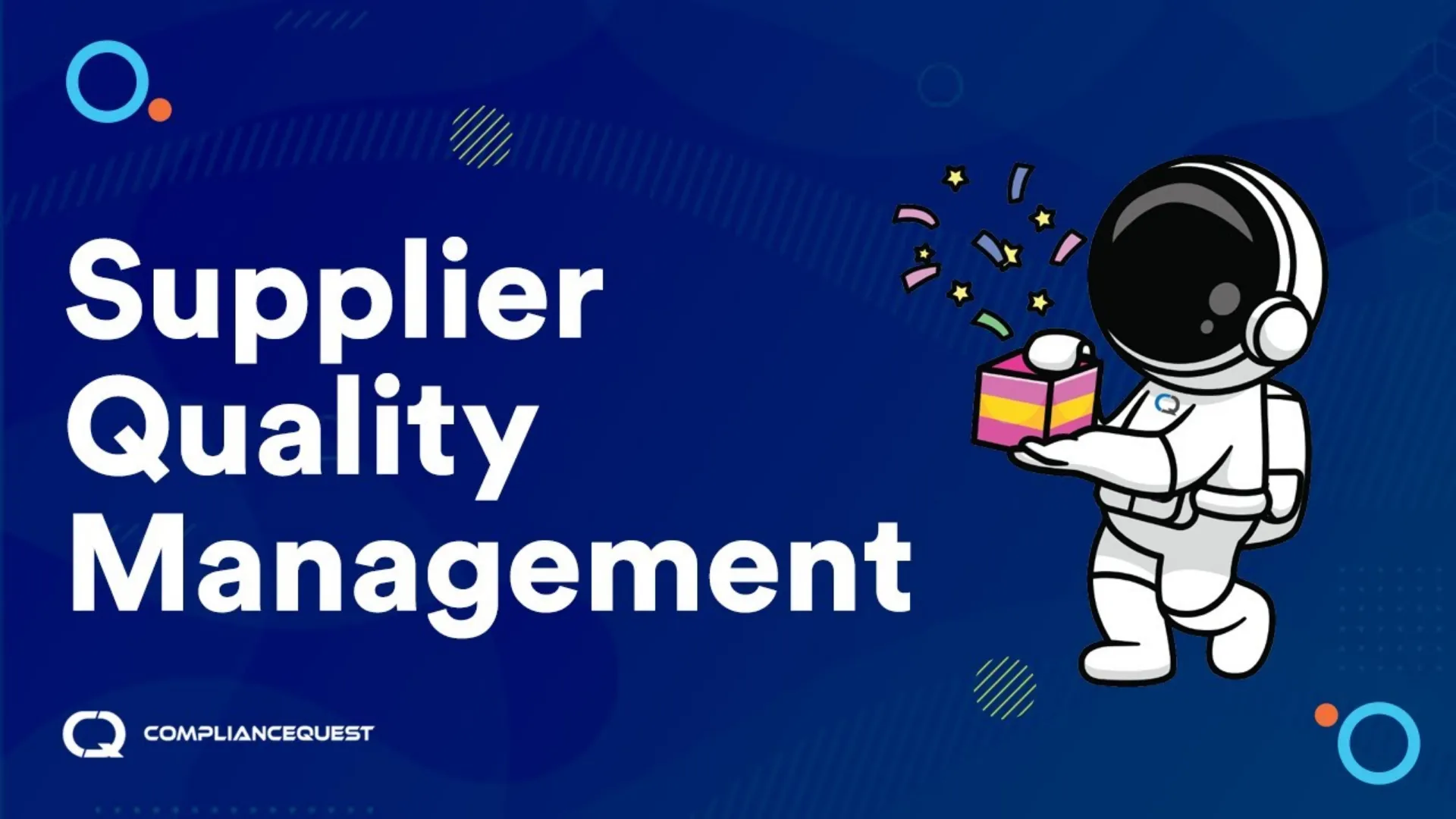
Up next on our quality control software for manufacturing list, we've got ComplianceQuest .
Make the most of your manufacturing abilities to stay ahead of the competition with the help of ComplianceQuest's cloud-based Quality Management System (QMS). It automates and optimizes your global manufacturing management process.
By concentrating on these three key areas, the solution's modular design allows it to address all elements of manufacturing-related quality control software for manufacturing, hence assisting in the maintenance of product quality:
The manufacturing QMS software from ComplianceQuest allows manufacturers to keep an eye on quality and make sure their products are up to par with what customers want.
Key Features
- User-Oriented Interface: An intuitive interface is a hallmark of high-quality manufacturing software, allowing users to access the data they need to make informed choices quickly.
- Automated Workflows: CQ's manufacturing quality software includes a decision tree for recognizing reportable hostile occurrences.
- Cloud-based QMS: Cloud-based manufacturing QMS software analyzes trends, records result related to individual products, launches change campaigns via dashboards, deviations by product, and reports on open/closed modifications.
Pricing
- Contact the vendor to get a Quote-based Plan
7. UniPoint
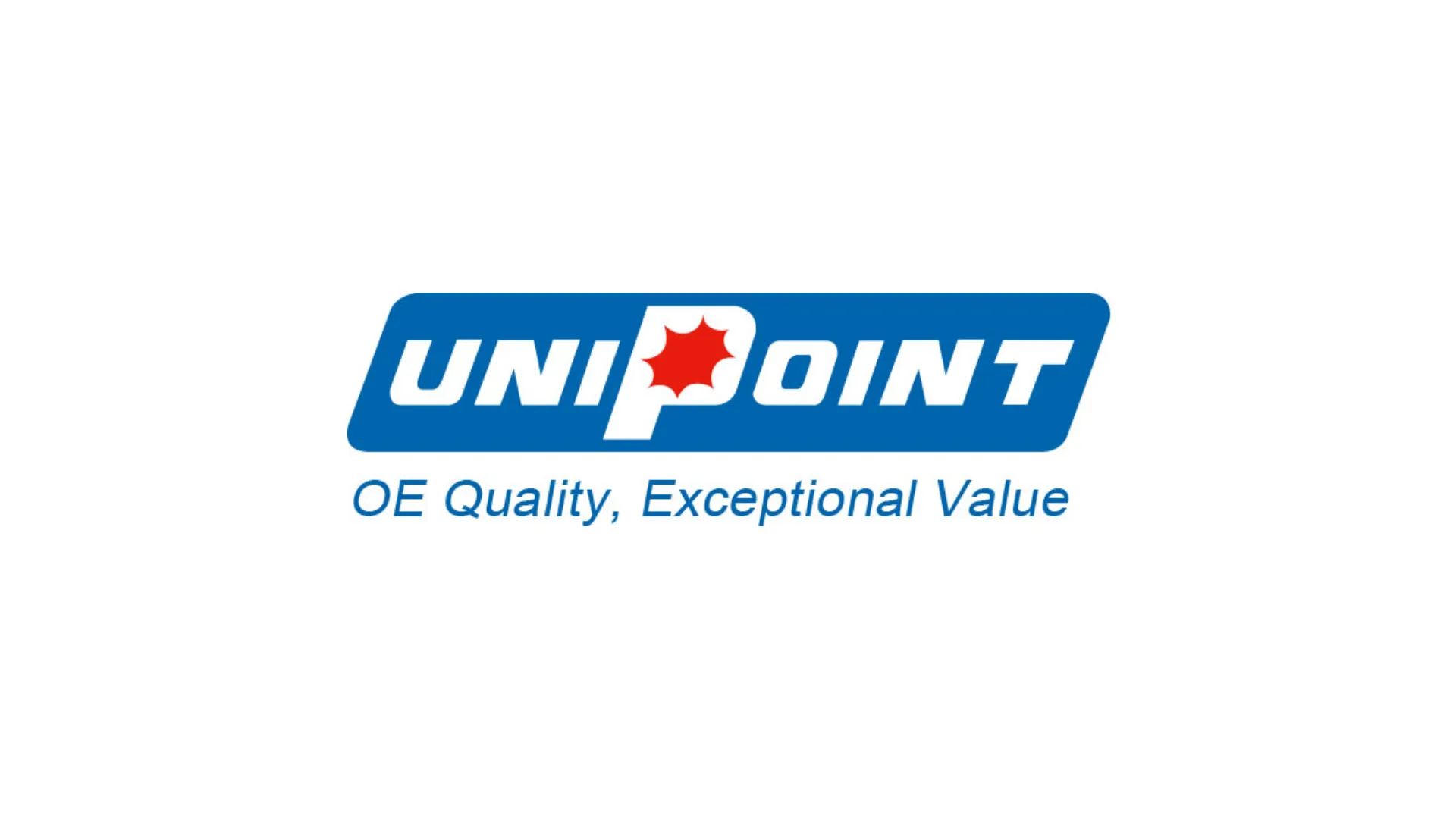
When it comes to quality control software for manufacturing for industrial production, UniPoint is a pioneer (QMS).
The chemical, food and beverage, automotive, and medical sectors are just a few of the many that can benefit from its ERP-integrated quality management systems (QMS).
To help organizations automate their quality control procedures, UniPoint has three parts: core, add-on, and web. These parts make up its extensive toolbox.
Standard features found in these modules include document control, non-conformance, and action for both corrective and preventive purposes. In addition to validation and auditing, the add-on modules include health and safety and inspection.
Transitioning to a mobile quality management system (QMS) using online requests and mobile inspection is as easy as utilizing the web modules.
Key Features
- ERP-Integrated QMS: By providing a central hub for all quality and compliance-related activities and eliminating the need for repetitive data entry, an integrated QMS/ERP platform improves efficiency and accuracy.
- Flexible Deployment: With a mobile-first design, uniPoint Web can operate on any PC, tablet, or smartphone and provide complete functionality, SSL security, and optimal performance.
- Quality Automation: The executive dashboard includes over 800 built-in quality measurements or Key Performance Indicators (KPIs), allowing our customers to assess the health of their quality system at a glance.
Pricing
- Available upon request
8. Basetwo
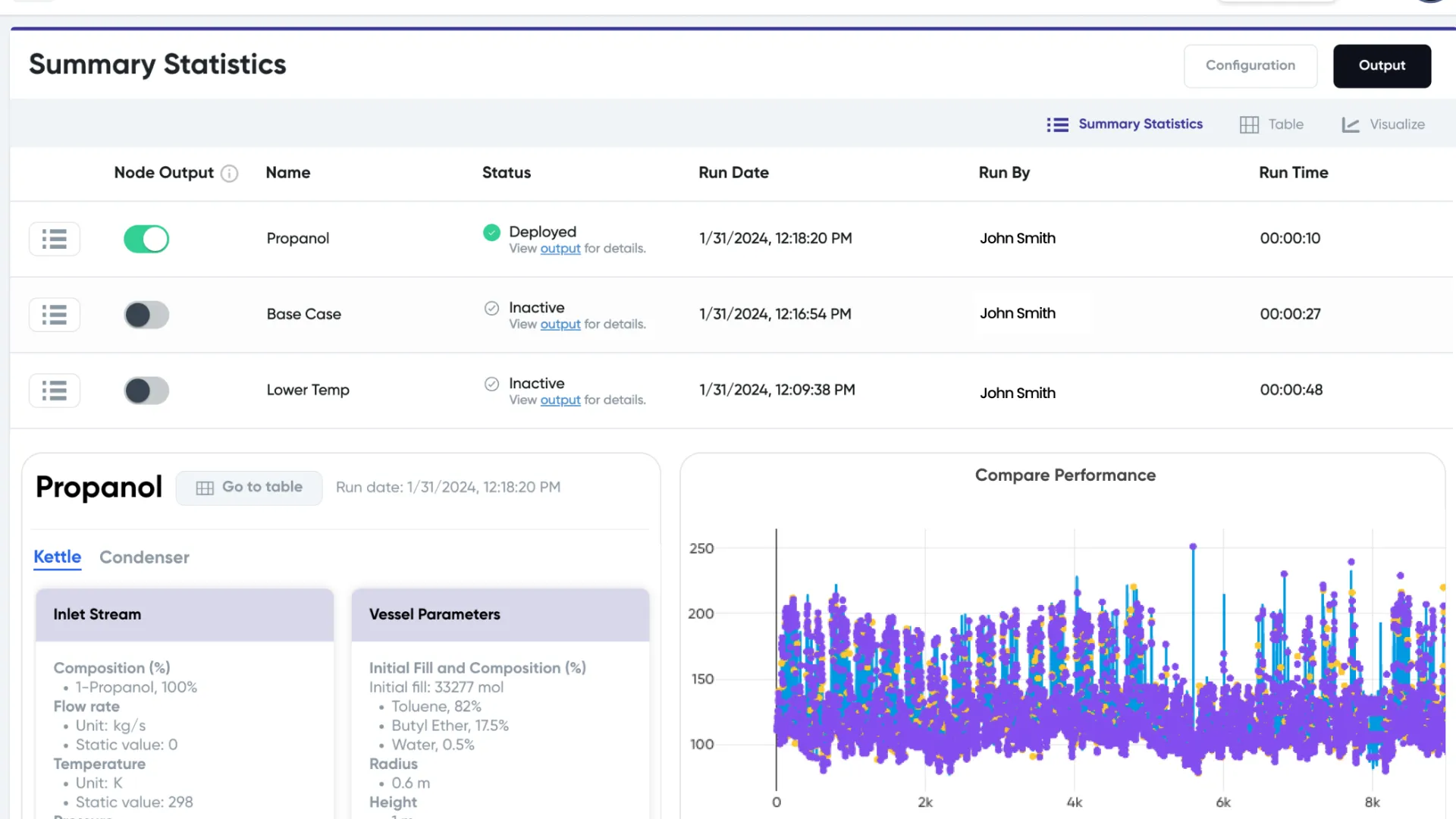
When it comes to process engineering, Basetwo is a web-based software solution that offers an AI-powered copilot to assist make optimal decisions.
With Basetwo, teams can quickly install digital twins for manufacturing facilities, allowing for quality control. By simulating and analyzing data in real-time, these virtual environments improve quality control and resemble the manufacturing process.
While most digital twin implementations need substantial effort and coding knowledge, the low-code AI platform Basetwo makes it easy to install strong process control, making it an excellent option for a quality control system in manufacturing.
Key Features
- Rigorous Testing and Validation: Facilitates thorough testing and validation of models, ensuring their reliability for deployment.
- Built-in Dynamic Optimization and Process Control Recommendations: Provides real-time optimization capabilities and offers actionable recommendations for process control enhancement.
- Empowerment for Teams: Enables teams to discover optimal control points and conduct in-silico experiments, fostering innovation and efficiency.
Pricing
- Contact the vendor for pricing.
9. Tulip
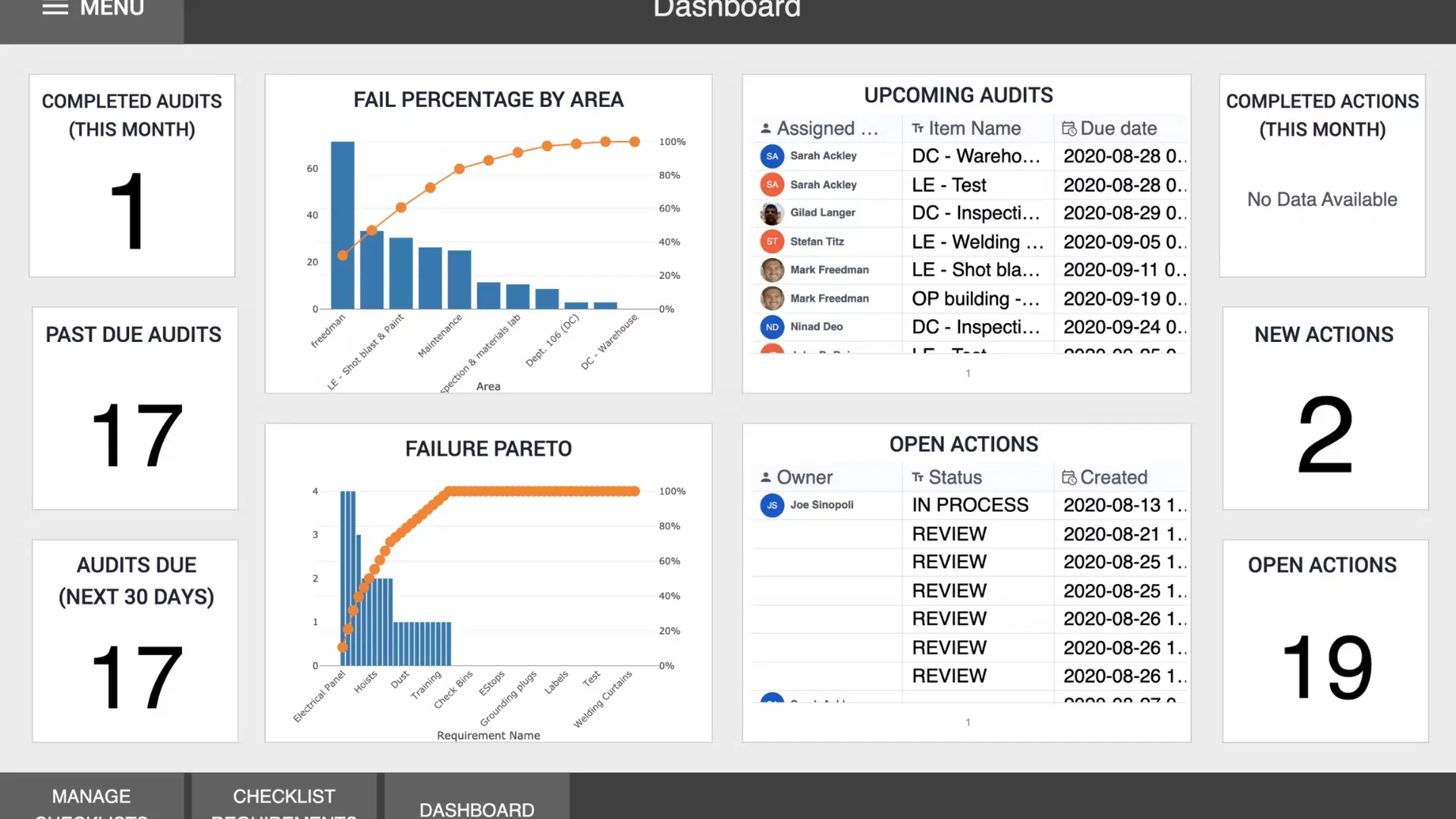
Streamline your manufacturing process with customized digital tools - easy instructions for complicated assemblies, dynamic flexibility for unique builds, coding-free integration, insights powered by artificial intelligence, and real-time, relevant data.
Using digital workflows and quality control methods, manufacturing businesses can create bespoke applications, optimize shop floor processes, and find improvement opportunities using Tulip software.
However, there aren't many instruments for statistical process control, and using Tulip to its full potential necessitates expensive hardware upgrades.
Key Features
- Process Visualization and Control: Offers intuitive visualization tools for monitoring and controlling processes in real-time.
- Automation Capabilities: Automates machine downtime alerts, scheduling tasks, and integrating with other systems for seamless operation.
- Quality Checks and Validation: Provides robust quality checks and validation mechanisms to ensure adherence to standards and specifications.
Pricing
- Essentials Package: $1200 per interface per year
- Professional Package: $2400 per interface per year
- Enterprise Package: Contact for pricing (minimum 10 interfaces)
- Regulated Industries Package: Contact for pricing (minimum 10 interfaces)
10. Alpha Software
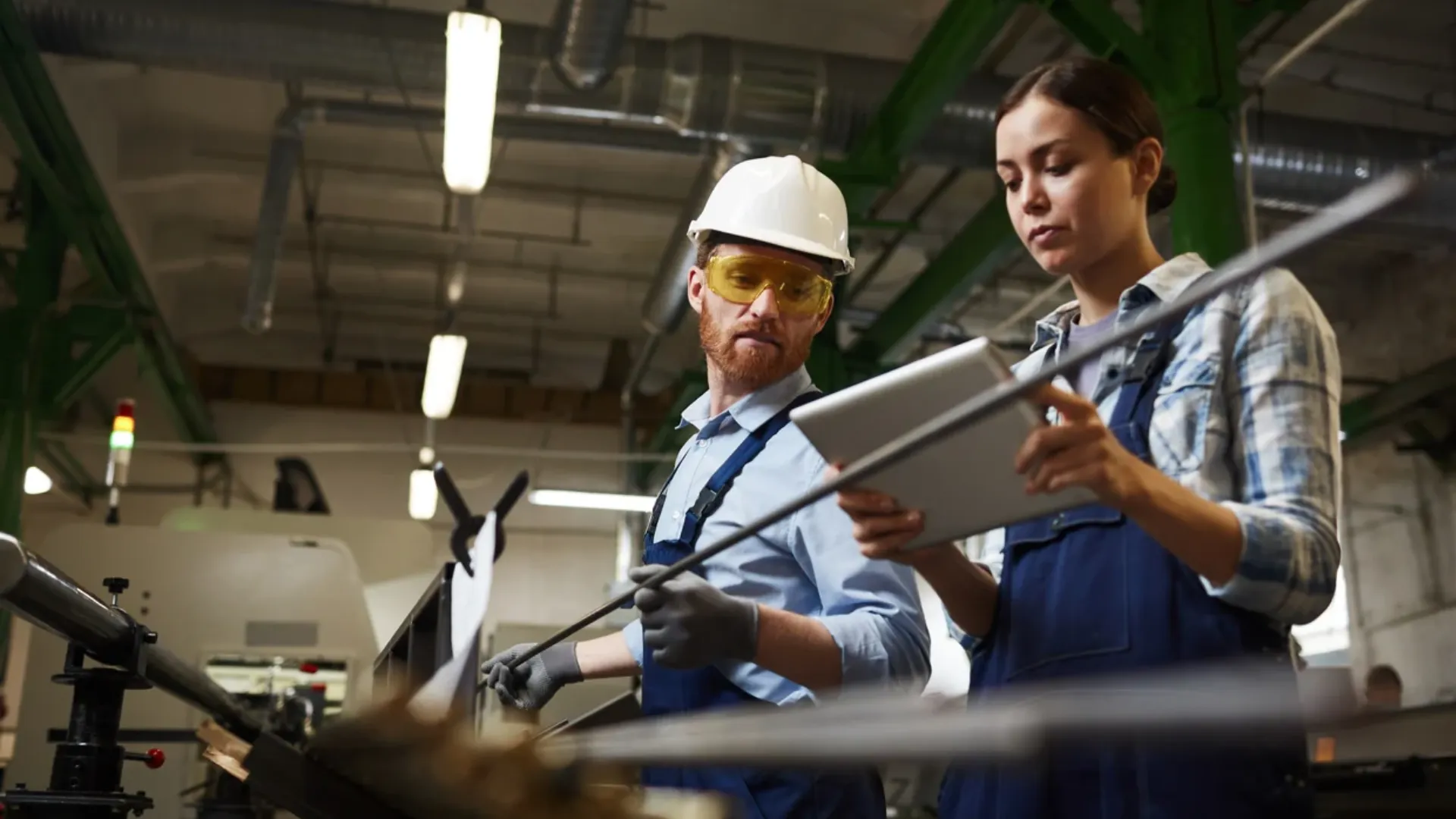
Alpha Software assists manufacturing businesses in optimizing their processes, allowing workers to be more productive whether they are on the road, in the warehouse, or on the factory floor.
To facilitate the integration of new systems, processes, and data investments, manufacturers have the option to develop bespoke business applications for use by managers, engineers, assemblers, inspectors, and delivery/repair personnel.
With the help of Alpha Software's solutions, manufacturers may create a variety of applications for collecting and delivering production data on the go. These apps include Gemba Walk, 5S audit checklist, equipment inspection, non-conformance, and safety.
Key Features
- Advanced Offline Functionality: Utilize patented features to develop offline applications that seamlessly operate even without an internet connection, enabling access to on-device data effortlessly.
- Comprehensive Deployment Capabilities: Equipped with all necessary tools to create and deploy applications to various platforms, including cloud services, any Internet Service Provider (ISP), or your organization's infrastructure.
- Seamless integration with Any System: Leverage robust APIs and toolsets for seamless integration with a wide range of web services, data sources, and workflow systems.
Pricing
- Contact the vendor for pricing.
What is Quality Control (QC)?
Quality cannot be defined in only one way. Regardless of the relative definition of "value," quality control is the practice of testing and measuring goods and services to guarantee they satisfy a standard.
A business can assess, maintain, and enhance product quality using this technique.
Quality Control's main goal is to seek out and fix any violations of specified quality standards. This procedure involves checking and monitoring goods or services at different stages of manufacturing or delivery to ensure they satisfy the intended level of quality.
QC is also focused on avoiding faults or mistakes from happening in the first place by adding controls and improvements to the manufacturing or service delivery processes.
What is Quality Control Software For Manufacturing?
Gartner defines Quality Management Software as "the business management system" that includes internal quality rules and standard operating procedures (SOPs).
Manufacturing Quality Control Software is often included as part of a Quality Management System (QMS).
In today's increasingly competitive environment, maintaining quality is critical for organizational success. Due to increased saturation, businesses have been pushed to extend their operations and incorporate complicated supply chains. Investing in quality management software enables businesses to take on quality problems impacting employees, suppliers, customers, and partners with greater urgency.
Quality control software for manufacturing allows for the digital monitoring and administration of quality control, quality assurance, risk management, and quality improvement.
The focus of factory management software is not just on product and service quality. Quality managers should also pay attention to equipment as well as individual worker performance.
Key Components of Manufacturing Quality Control Software
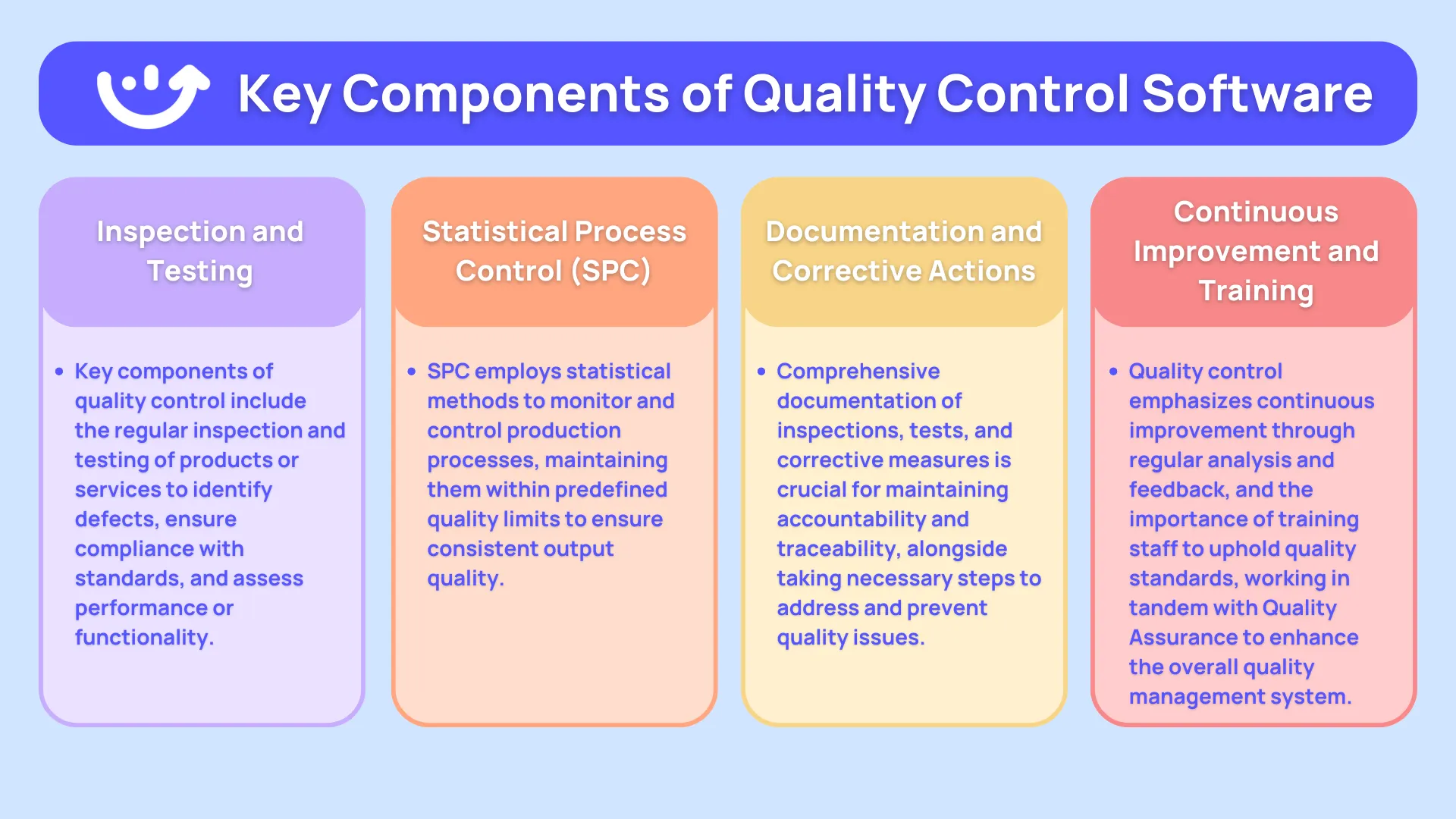
Quality Control can include the following key components:
- Inspection: The process of evaluating goods, materials, or services on a regular basis to detect faults, noncompliance, or deviations from quality standards.
- Testing: The process of doing numerous tests and measurements to evaluate the performance, functionality, or features of a product or service.
- Statistical Process Regulator (SPC): The use of statistical methods to monitor and regulate production processes in order to ensure that they stay within acceptable quality boundaries.
- Documentation and Records: To preserve traceability and accountability, complete records of inspections, testing, and corrective actions must be kept.
- Corrective Action: Taking the necessary steps to fix any recognized quality concerns and avoid their recurrence.
- Training and Education: Providing staff with the skills and information they need to maintain quality standards successfully.
- Continuous Improvement: Analyzing data and input on a regular basis to find areas for improvement and to enhance the overall quality management system.
Quality Control is closely connected to Quality Assurance (QA), another quality management concept.
While QC is concerned with discovering and resolving faults, QA is concerned with preventing them from arising in the first place by establishing strong systems and procedures.
QC and QA work together to create the foundation of a company's quality management system, ensuring that goods and services continually meet or exceed customer expectations and regulatory requirements.
What are the Regulatory Compliances the Manufacturing Industry Must Adhere To?
ISO 9001 is a critical regulatory standard for the manufacturing sector.
This standard is essential for businesses across sectors that wish to operate more effectively and attract smarter consumers.
The latest ISO 9001:2015 change moves the emphasis from documentation to risk-based process management.
While ISO 9001 is one of the most important laws for businesses, others like as ISO 14001, ISO 18001/45001, ISO 31000, and GHGRP must also be followed. Manufacturers must also follow Good Manufacturing Practices, which include methods, procedures, and documentation, in order to minimize recalls and penalties while also reducing losses and waste.
.webp)
%201%20(1).webp)