When was the last time you were required to sign a mountain of documentation for work? Before signing, did you give each line a thorough read, or did you just glance at the words? Have you verified that all tasks have been finished? Did you have facts and proof to back that up?
When paperwork is required to prove adherence to rules, laws, or quality standards, this problem arises often across many different types of businesses.
Aside from being unethical, pencil whipping can lead to serious problems including legal liability, reputational harm, and operational failures in an era when public scrutiny of companies' openness and accountability is at an all-time high.
Several reasons, including a lack of enthusiasm for processes, job demands, and time limits, contribute to the common practice of pencil whipping.
Priced on per user or per location basis
Available on iOS, Android and Web
What is Pencil Whipping?
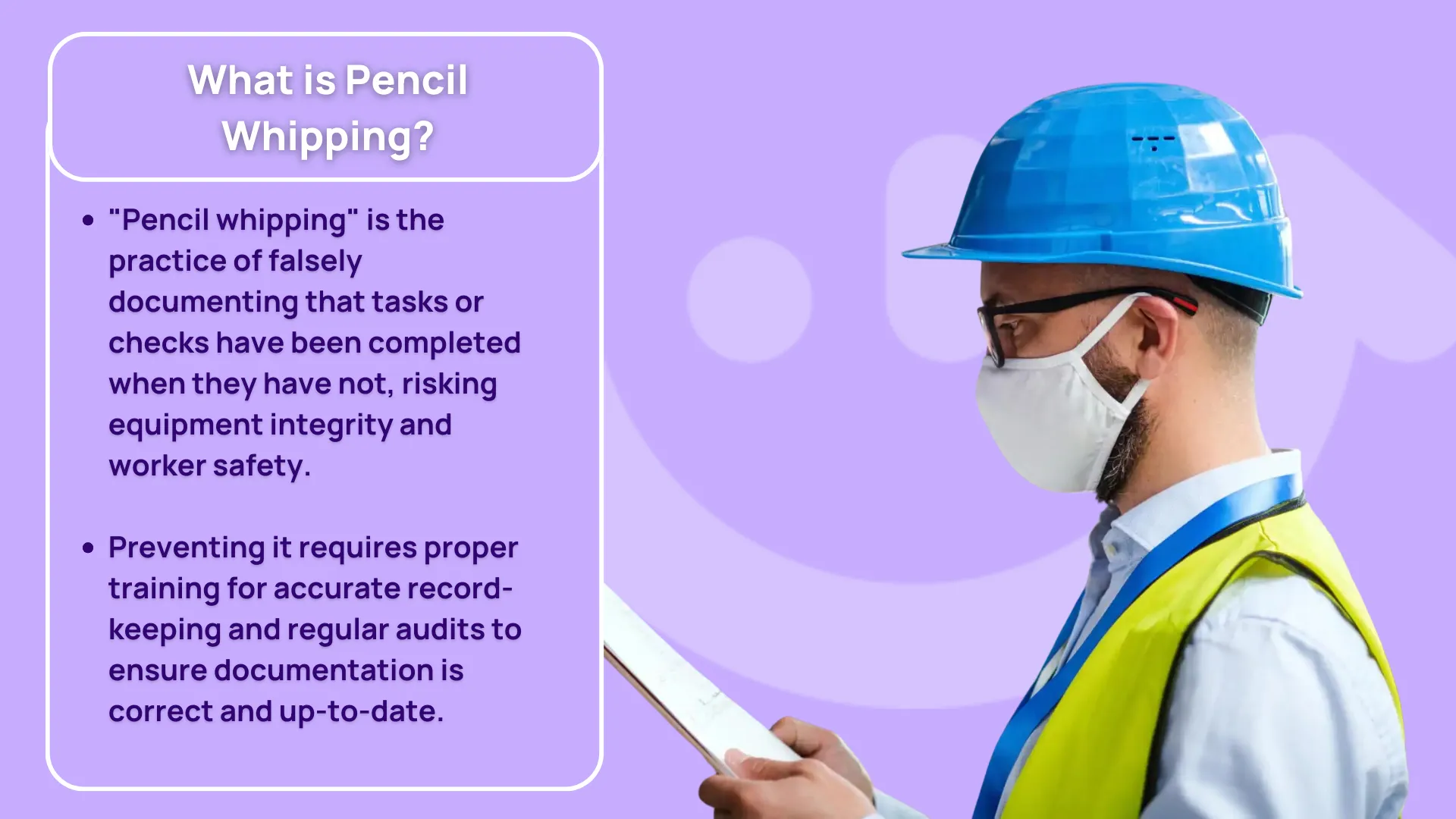
"Pencil whipping" refers to the practice of inaccurately documenting processes or recording misleading information. Pencil whipping has varying degrees of gravity, from a simple disciplinary penalty to even criminal prosecution.
Pencil-whipping, also known as 'to pencil whip,' refers to the act of falsely indicating that work has been completed to nearly or fully 100% when, in reality, it has not even begun or is only partially completed. This frequently results in equipment being compromised and worker safety being put at risk.
The best way for facilities managers to stop employees from "pencil whipping" is to teach them how to properly record information and then hold them responsible when they mess up. Also, make sure all records are correct and up-to-date by auditing documents regularly.
Common Causes of Pencil Whipping
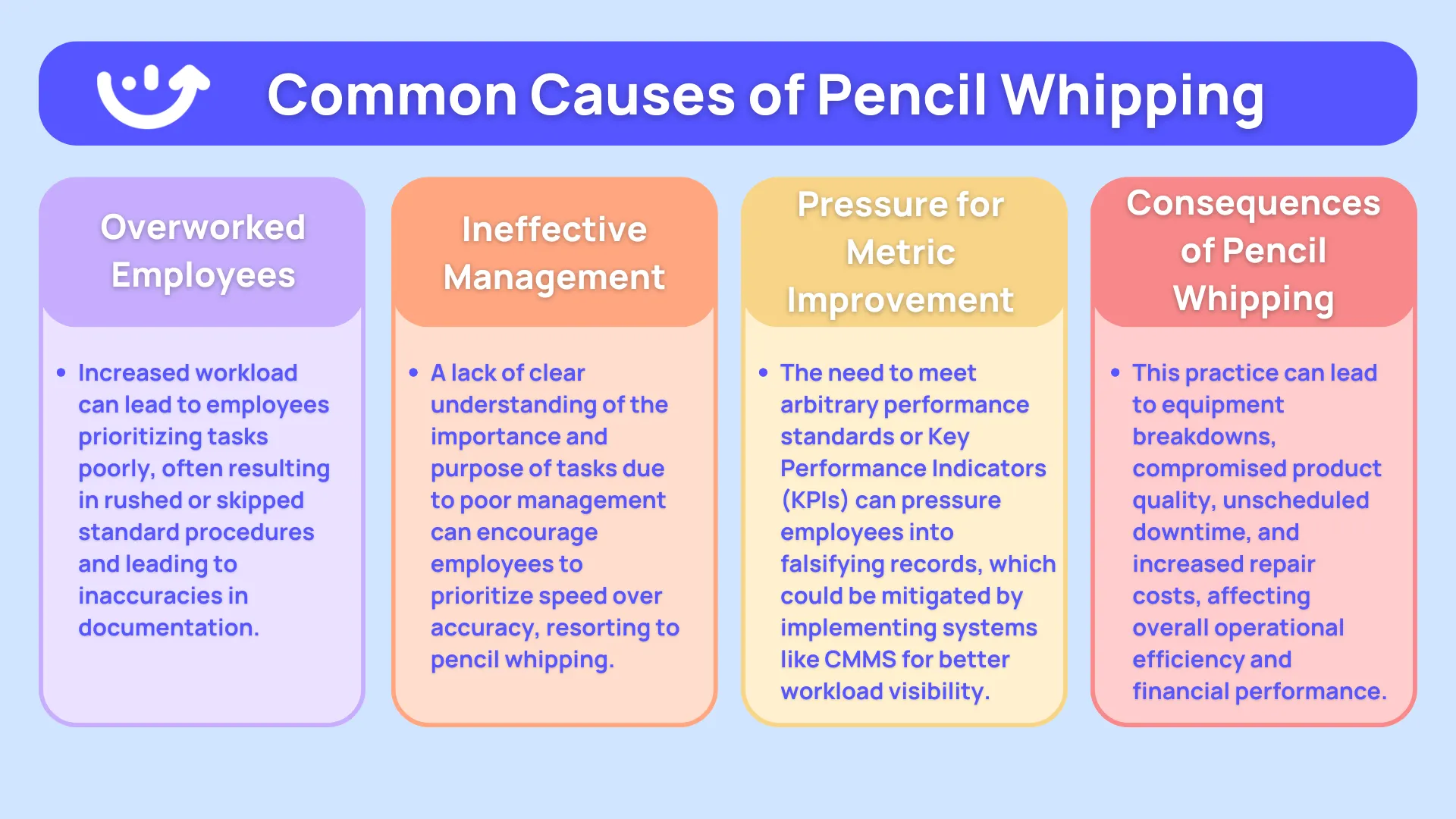
Pencil whipping occurs for a number of reasons, not all of which are related to negligence in the workforce. Pencil-whipping may be caused by and contribute to a number of organizational factors:
1. Overworked Employees
Employees are more prone to neglect certain jobs in favor of others when there is more work than there are workers. This implies that they are likely to rush through a standard inspection or another unimportant process.
2. Ineffective Management
Employees may not always understand the real purpose behind an assignment or process due to poor management. To expedite the process and prioritize quantity above quality, workers who lack an understanding of the need for accuracy and meticulousness may resort to pencil-whipping.
3. Pressure for Metric Improvement
Pencil whipping can come from employees feeling under pressure to satisfy arbitrary performance standards, or Key Performance Indicators (KPIs). This could be minimized by using a computerized maintenance management system (CMMS), which gives managers and workers visibility into how much work each person is required to do.
4. Equipment Breakdowns
Falsifying inspection and maintenance records to cut down on time or satisfy performance targets may leave important problems unattended, which can cause equipment and other assets to break down sooner than they should. This could compromise product quality in addition to interfering with operations and adding to the expense of repairs or replacements.
5. Unscheduled Downtime
Organizations run the danger of unscheduled breaks in production, inventory checks, and maintenance operations when maintenance chores are not completed to a high enough standard or when inspection reports are fabricated.
This can have a cascading impact that causes delays in projects, messes with timetables, and costs money. Unplanned downtime puts a burden on resources as workers and maintenance managers try to find and fix problems while coming under increasing pressure from stakeholders who want quick fixes.
Pencil-Whipping Examples To Help You Understand Use Cases
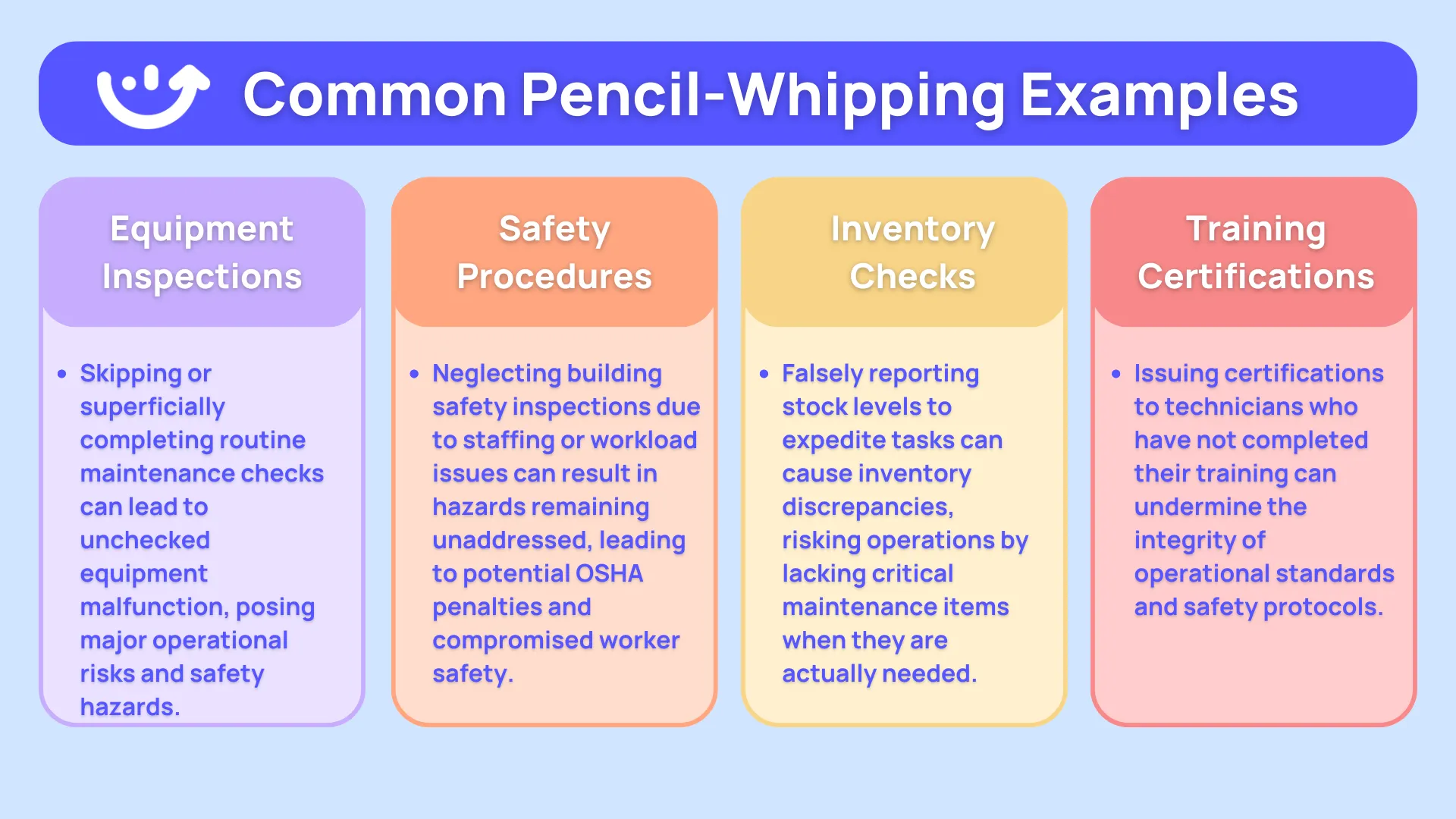
These traditional instances of pencil whipping demonstrate how major operational risks might arise from facility management staff inattention.
1. Equipment Inspections
To ensure worker safety and maintain assets in optimal condition, regular maintenance inspections are essential. Nevertheless, some professionals could neglect to do routine checks or assume everything is satisfactory without doing a comprehensive examination.
They cross off items on the checklist, give it to their manager, and sometimes, the manager even gives their approval without asking questions. What was the outcome? After months of neglect, equipment has an unplanned malfunction.
2. Safety Procedures
Building safety inspections are essential for identifying and removing hazards. However, since their facilities are crowded or understaffed, busy facility managers could neglect these inspections.
Pencil-whipping results from this carelessness, which puts off maintenance and may result in significant penalties from the Occupational Safety and Health Administration (OSHA).
3. Inventory Checks
Facilities that handle a lot of components sometimes struggle with inventory control. Employees that report exaggerated stock figures to complete a job are guilty of pencil whipping, which puts the company at risk for possible inventory discrepancies and the eventual requirement for a critical maintenance item that isn't truly in stock.
4. Training Certifications
Certifications can be granted to some technicians even when they haven't finished their training yet. This is another pencil whip hotspot that has to be avoided, regardless of how much experience they have with the subject matter or how much training they have had related to it.
How to Prevent Pencil Whipping
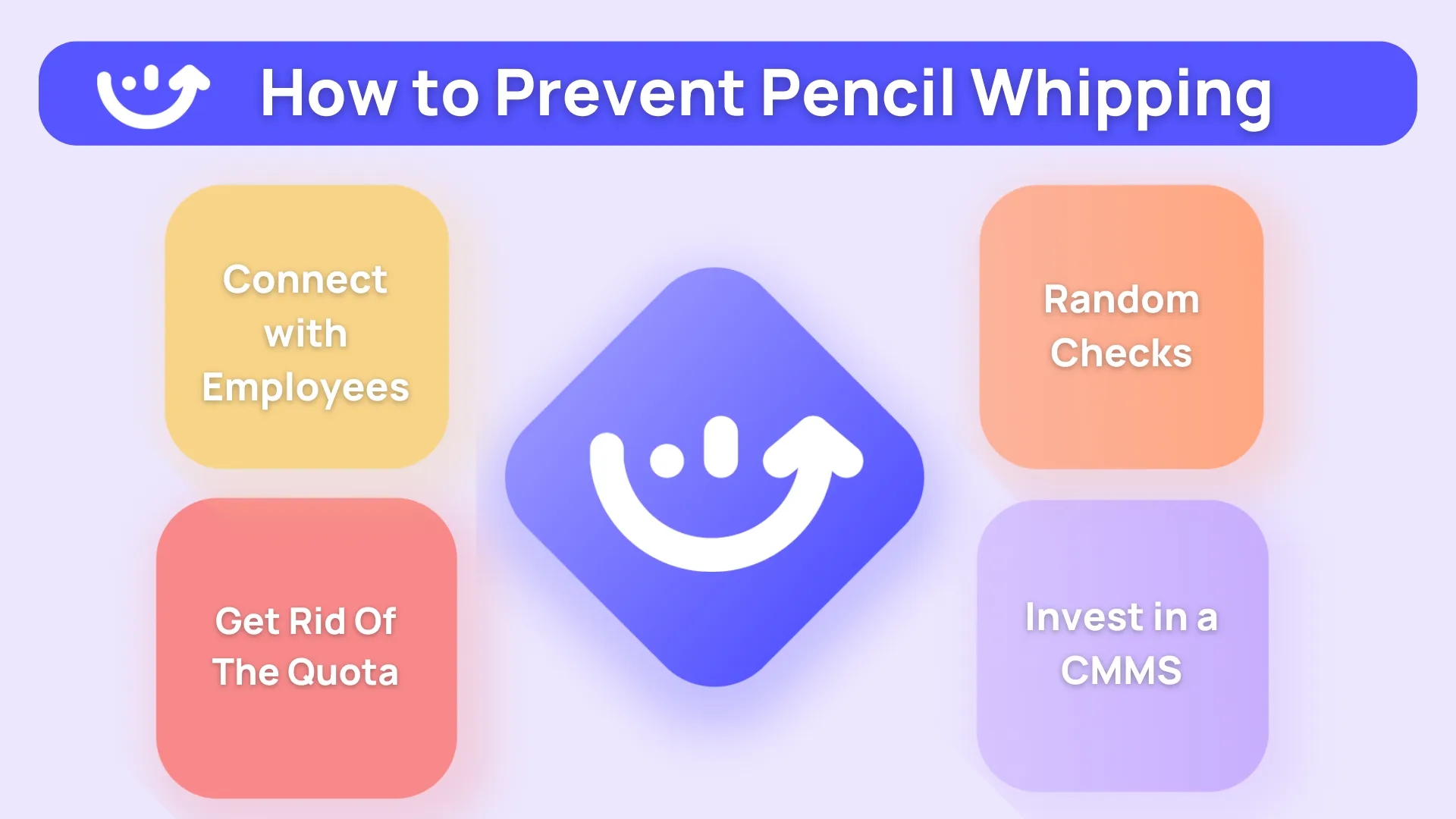
There has been a shift away from pencil whipping and toward digital checklists and forms, which are quickly replacing paper forms in many sectors.
Thankfully, you can get more in-depth information and analyze completed checklists in real time using cutting-edge inspection software. There is an issue if you continue to have events despite your safety KPIs looking good. If you suspect pencil whipping, you could quickly analyze completed checklists and relevant KPIs to find out and stop it. There will be no need to rummage through stacks of paperwork to locate the specific finished safety inspection you need.
Once pencil-whipping becomes routine among your staff, it might be hard to put a stop to it. But you can easily steer clear of it if you see it early and take precautions.
To reduce and, ideally, eradicate this risky activity, let's have a look at some easy adjustments that you could make.
1. Connect with Employees
Enhancing maintenance operations involves building relationships with your employees, discussing both successes and failures. This fosters a culture of open communication and collaboration, making everyone feel valued and contributing to a positive work environment.
2. Random Checks
Powerful CMMS reporting capabilities allow managers to swiftly identify ineffective regulations, areas of disregard for safety, and problematic machines.
Furthermore, management can modify methods to decrease downtime, enhance safety, and prolong asset life by monitoring asset health and maintenance performance.
3. Get Rid Of The Quota
Employees can act irresponsibly and fail to perform the necessary checks if they get notified that the business wants a certain quantity of items by the end of the week.
The same holds true when incentives and rewards are tied to increased production speed. Instead, do away with the quota and instead incentivize your workers to care more about the company as a whole.
4. Invest in a CMMS
Another excellent option for establishing responsibility at every level is maintenance management software. The use of a CMMS for scheduling and tracking work provides maintenance managers with a clearer view of the number of jobs they are really allocating and whether it is fair.
In addition, managers can gain a better understanding of the situation and make more informed choices every day based on key performance indicators (KPIs) when they have access to a dashboard that displays a summary of these measures.
It becomes more difficult for technicians to pencil whip when they have a CMMS software on their mobile smartphone that lets them monitor work as they go.
This is because they need to input data, such as the components utilized and when the work order was begun and finished. Additionally, technicians have a quick way to provide feedback where future actions are readily indicated when they may make comments to inspections using a CMMS.
Important assets to your organization's operations can have CMMS alerts added to them, which increases transparency for each work order done on those assets. In addition, a CMMS that allows users to upload user manuals equips technicians with all the necessary knowledge to do any work on an asset.
Put Pencil Whipping in the Past with Xenia
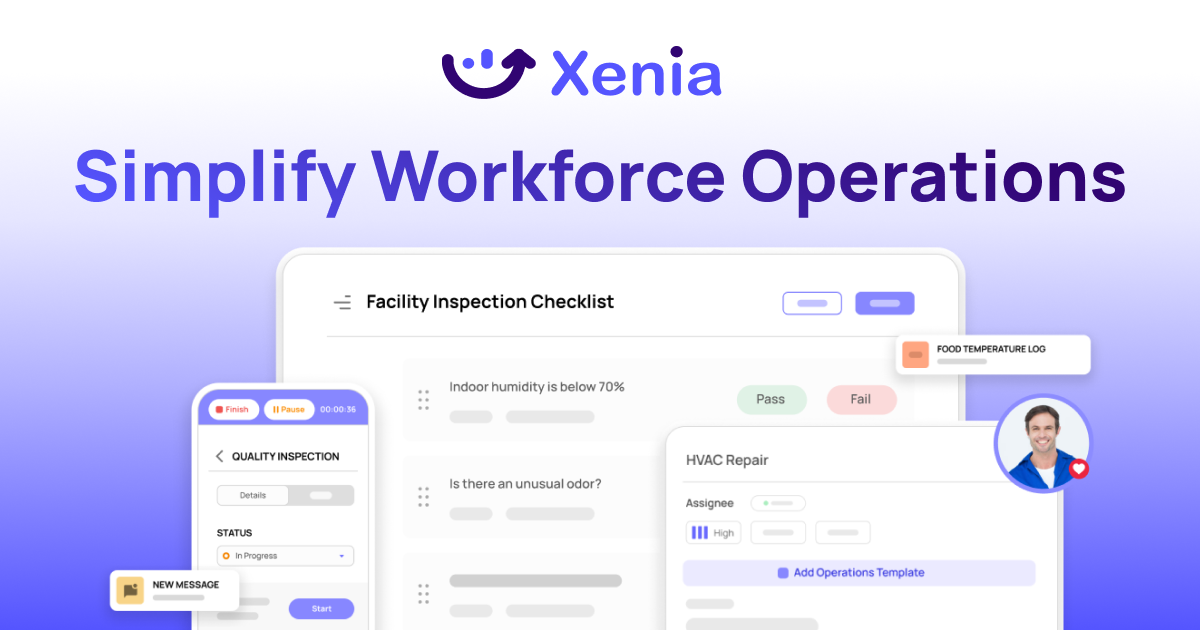
Xenia is a state-of-the-art solution that transforms maintenance management and all kinds of operational activities through transparency at all levels of your organization.
Our platform simplifies work order creation, scheduling, and monitoring, empowering maintenance managers to optimize workflows effectively.
With Xenia, you gain comprehensive oversight, providing a holistic view of maintenance activities. This comprehensive oversight facilitates informed decision-making and proactive management techniques.
The tool's user-friendly dashboards offer quick insights into critical maintenance key performance indicators (KPIs), enabling managers to make data-driven decisions for improved efficiency and productivity.
As a mobile-first solution, Xenia ensures accessibility anytime, anywhere, facilitating real-time collaboration and monitoring for managers and technicians alike.
Managers can pass or fail inspections, ensuring accuracy and integrity in maintenance activities.
Don’t Let Pencil-Whipping Blind You
Pencil whipping typically begins when some individuals skip inspections due to workload or communication gaps.
Over time, this issue can escalate, impacting others within the organization without immediate detection. However, with CMMS software, you can effectively mitigate pencil whipping and streamline maintenance operations effortlessly.
Frequently Asked Questions
1. Which industries are more susceptible to pencil whipping?
Pencil whipping is prevalent across various industries, but certain sectors, such as aviation, construction, healthcare, and food processing, are more prone to it due to stringent safety regulations and compliance pressure.
2. How can I educate employees to deter pencil whipping?
To discourage pencil whipping, provide thorough training on the significance of accurate reporting and the ramifications of falsifying records. Promote open communication and establish clear reporting protocols.
3. What legal repercussions can result from pencil whipping?
The legal consequences of pencil whipping vary based on industry and the severity of the falsified records. In regulated sectors like healthcare or aviation, pencil whipping may lead to fines, license revocation, or criminal charges in severe cases.
4. Can you provide examples of pencil whipping incidents?
Instances of pencil whipping include falsely certifying completed inspections, neglecting mandatory safety checks, and inaccurately documenting maintenance activities. These incidents can result in equipment failures, workplace accidents, and compromised safety standards.
.webp)
%201%20(1).webp)