Operational analytics is a powerful tool that helps facility managers make data-driven decisions to improve efficiency and productivity. And with the right digital tools, like Xenia, facility managers can collect, analyze, and act on that data to streamline operations and achieve better outcomes.
Picture this: you're a facility manager tasked with maintaining your organization's buildings, equipment, and infrastructure. You're constantly juggling work orders, preventive maintenance schedules, safety inspections, and team communication, all while trying to keep everything running smoothly. It's a lot to handle, but luckily, you have operational analytics and digital tools on your side.
Priced on per user or per location basis
Available on iOS, Android and Web
In this blog post, we'll take you on a journey through the world of facility management and show you how operational analytics and digital tools can make your life easier. We'll cover everything from the basics of operational analytics and its importance in facility management to the benefits of using digital tools like work order management, preventive maintenance, safety inspections, checklists and logs, and centralized communication.
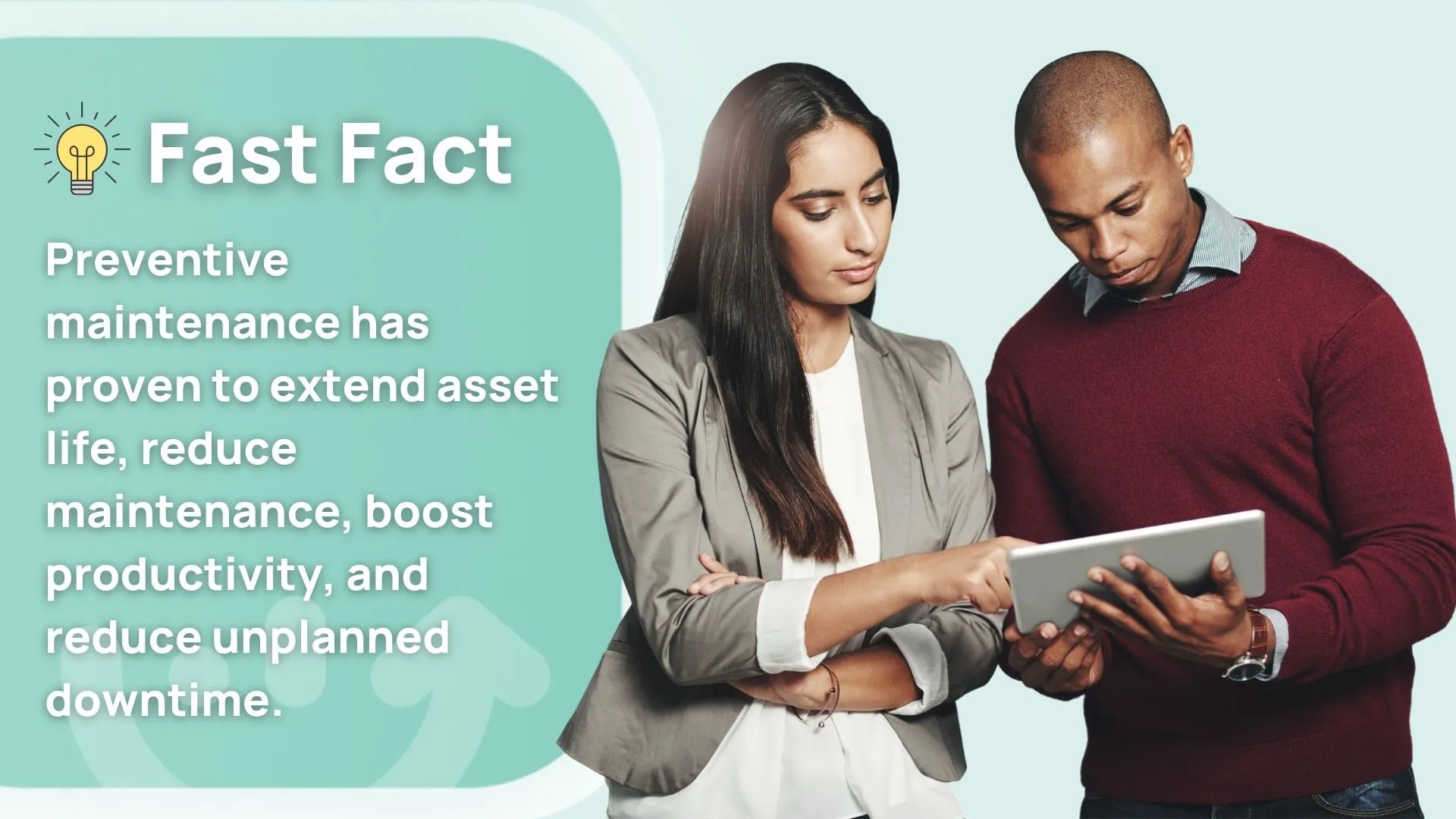
But we're not just going to give you a bunch of information and leave you to figure it out independently. We'll provide tips on how to implement digital tools for operational analytics in facility management, including guidance on how to choose the right tools and train your staff to use them effectively.
By the end of this post, you'll be armed with the knowledge and tools you need to master facility management of operational analytics with digital tools. So, if you're ready to streamline your operations, reduce downtime, and improve productivity, keep reading to learn more!
What is Operational Analytics?
Operational analytics involves using advanced analytics techniques to extract insights from data related to an organization's operations. This process can provide valuable information on their organization's performance, allowing them to identify areas for improvement and optimize their processes.
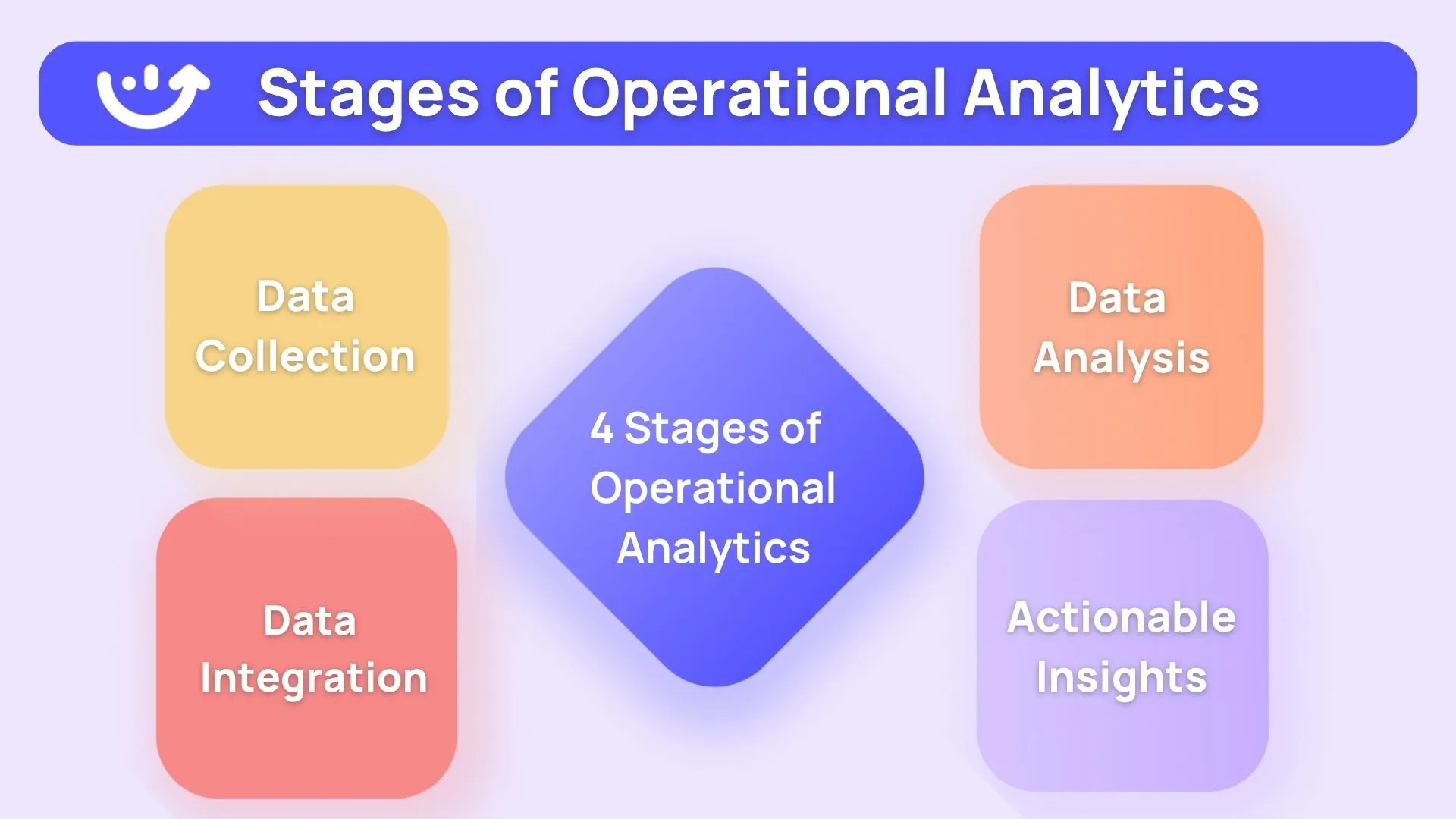
In facility management, operational analytics involves collecting data on various aspects of operations and using it to improve efficiency, reduce costs, and enhance overall performance. Critical components of operational analytics in facility management include asset management, preventive maintenance, safety inspections, and work order management. By utilizing operational analytics, facility managers can identify inefficiencies, prioritize tasks, and optimize resources to achieve better outcomes.
So what exactly does operational analytics entail? Here are some key components:
- Data Collection: Operational analytics begins with collecting data from various sources within an organization. This can include data on equipment performance, maintenance activities, work orders, safety inspections, etc.
- Data Integration: Once the data is collected, it must be integrated into a central repository to ensure that it is accessible and usable for analysis. This can involve merging data from different sources and formats into a standardized format.
- Data Analysis: After the data is collected and integrated, it can be analyzed using various analytical techniques. These include statistical analysis, data visualization, machine learning, and predictive analytics.
- Actionable Insights: The goal of operational analytics is to extract actionable insights from the data that can be used to drive improvements in an organization's operations. This can include identifying areas for process improvement, optimizing preventive maintenance schedules, improving safety and quality standards, and more.
By leveraging operational analytics, facility managers can better understand their organization's operations which leads to a variety of benefits.
Benefits of Using Operational Analytics for Facility Management
Operational analytics can provide numerous benefits to facility managers, helping them optimize their processes, improve productivity, and enhance the overall performance of their operations. Here are some of the key benefits of using operational analytics in facility management:
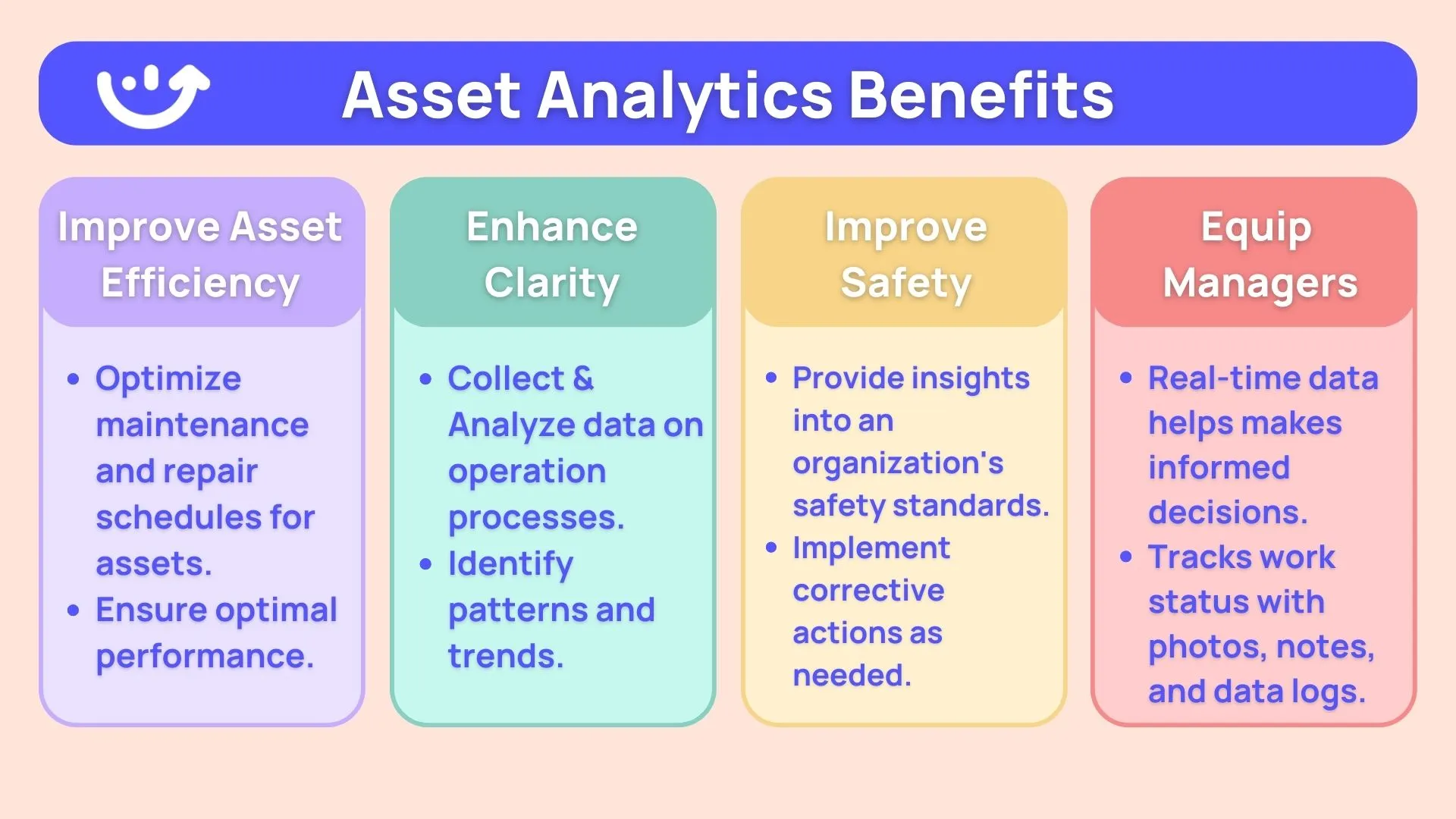
- Improved Asset Efficiency and Decreased Downtime: Operational analytics can help facility managers optimize their equipment and assets' maintenance and repair schedules, ensuring that they are operating at optimal levels and reducing unplanned downtime.
- Enhanced Clarity Around Operations: By collecting and analyzing data on their operations, facility managers can better understand how their processes are functioning and identify areas for improvement. This can include analyzing data on work orders, safety inspections, and maintenance activities to identify patterns and trends.
- Improved Safety and Quality Standards: Operational analytics can also help facility managers improve their safety and quality standards by providing insights into their organization's performance. This can include identifying areas where safety and quality standards are not met and implementing corrective actions to address these issues.
- Equipping Managers with Data for Informed Decisions: By providing facility managers with real-time data on their operations, operational analytics can help them make informed decisions about their organization's performance. This can include tracking work status, photos, notes, and data logs on every asset, location, individual, and team and using this information to drive improvements in productivity and efficiency.
Digital Tools for Operational Analytics in Facility Management
Digital tools are essential for operational analytics in facility management. They provide facility managers with a range of capabilities, including data collection and analysis, work order management, preventive maintenance scheduling, safety inspections, and communication. Various tools are available for operational analytics in facility management. Some offer all-in-one solutions, while others are designed to provide specific capabilities.
Numerous digital tools can help facility managers collect, analyze, and leverage data to optimize their operations and drive continuous improvement. Here's an overview of some of the key digital tools for operational analytics in facility management:
- Computerized Maintenance Management Systems (CMMS): CMMS systems are designed to help facility managers track maintenance activities and manage work orders. They can provide real-time data on equipment performance and maintenance schedules, enabling facility managers to optimize maintenance activities and reduce unplanned downtime.
- Enterprise Asset Management (EAM) Systems: EAM systems are similar to CMMS systems but are designed to manage the entire lifecycle of an organization's assets. They can provide insights into asset utilization, maintenance costs, and overall asset performance, enabling facility managers to optimize their operations and drive continuous improvement.
- Internet of Things (IoT) Sensors: IoT sensors can be used to collect real-time data on equipment and asset performance, enabling facility managers to identify potential issues before they occur and optimize their maintenance activities.
- Digital Checklists and Logs: Digital checklists and logs can be used to collect data on safety inspections, maintenance activities, and other operational processes. They can provide real-time data on performance, enabling facility managers to identify areas for improvement and optimize their operations.
- Communication and Collaboration Tools: Communication and collaboration tools can help facility managers and their teams stay connected and work together more effectively. These tools can include messaging apps, video conferencing platforms, and project management software.
Digital tools can help facility managers collect and analyze data to optimize operations and drive continuous improvement. But how can digital tools like Xenia help facility managers implement operational analytics in their day-to-day operations? We'll explore that in more detail in the next section.
How Digital Tools Improve Operational Analytics in Facility Management
Digital tools improve operational analytics in facility management by enabling data-driven decision-making, automating manual processes, and streamlining operations. Xenia's features, such as work order management, preventive maintenance scheduling, safety inspections, checklists and logs, and centralized communication, can help facility managers in their day-to-day operations. Using digital tools for operational analytics, facility managers can increase asset efficiency, reduce unplanned downtime, and enhance safety and quality standards.
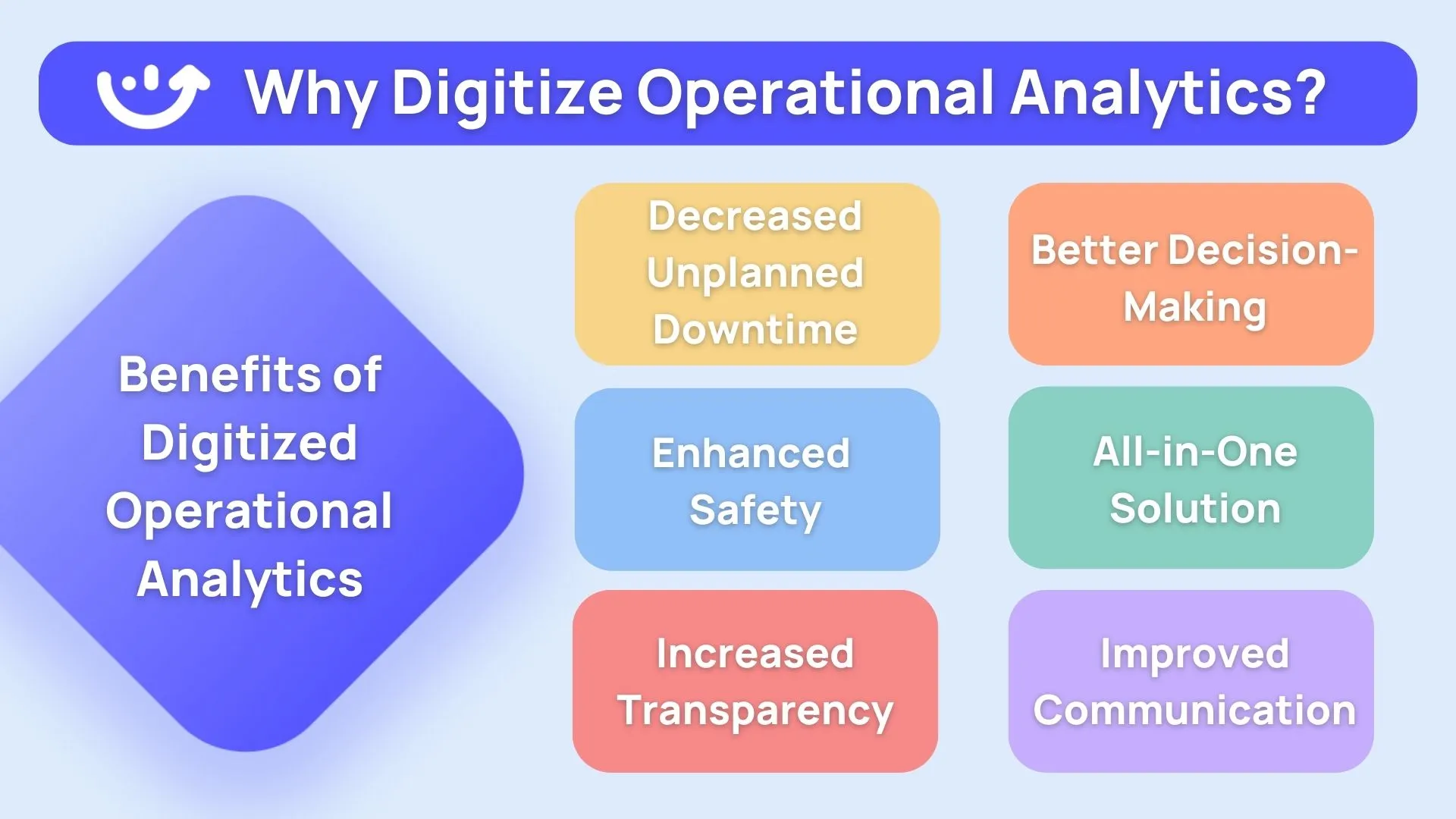
Digital tools can significantly improve operational analytics in facility management by enabling facility managers to collect, analyze, and leverage data in real time. Here are some of the ways that digital tools can improve operational analytics in facility management:
- Improved Asset Efficiency and Decreased Unplanned Downtime: Digital tools can provide real-time data on equipment and asset performance, enabling facility managers to optimize maintenance activities and reduce unplanned downtime. By identifying potential issues before they occur, facility managers can ensure that their assets operate optimally, improving overall efficiency and productivity.
- Enhanced Safety and Quality Standards: Digital tools can be used to collect data on safety inspections, maintenance activities, and other operational processes, providing real-time data on performance. By leveraging this data, facility managers can identify areas for improvement and drive a lean operations culture that prioritizes safety and quality.
- Increased Transparency around Individual and Team Operations: Digital tools can provide real-time data on individual and team performance, enabling facility managers to identify areas for improvement and optimize their processes. By tracking progress in real-time, facility managers can ensure that their teams are working efficiently and effectively.
- Equipping Managers with Data to Make Informed Decisions: Digital tools can provide facility managers with real-time data on workforce productivity, including live updates on work status, photos, notes, and data logs on every asset, location, individual, and team. This data can help managers make better-informed decisions and drive continuous improvement.
- All-in-One Solutions for Operational Analytics: Tools like Xenia provide an all-in-one solution for operational analytics in facility management, enabling facility managers to collect, analyze, and leverage data in real time. Facility managers can streamline their processes and improve efficiency using an all-in-one solution.
- Improved Communication and Collaboration: Digital tools can provide a centralized platform for communication and collaboration between facility managers and their teams. By enabling real-time communication, digital tools can help streamline workflows and ensure everyone is on the same page. This can improve overall efficiency and productivity while reducing the likelihood of miscommunication or errors. Additionally, digital tools can facilitate collaboration between teams, enabling facility managers to identify areas for improvement and optimize their processes.
Implementation of Digital Tools for Operational Analytics in Facility Management
Implementing digital tools for operational analytics in facility management requires careful planning and execution. When choosing digital tools, facility managers should consider cost, ease of use, and compatibility with existing systems. They should also provide staff with training and support to ensure they can use the tools effectively. Here is a quick guide to implementing digital tools for operational analytics successfully.
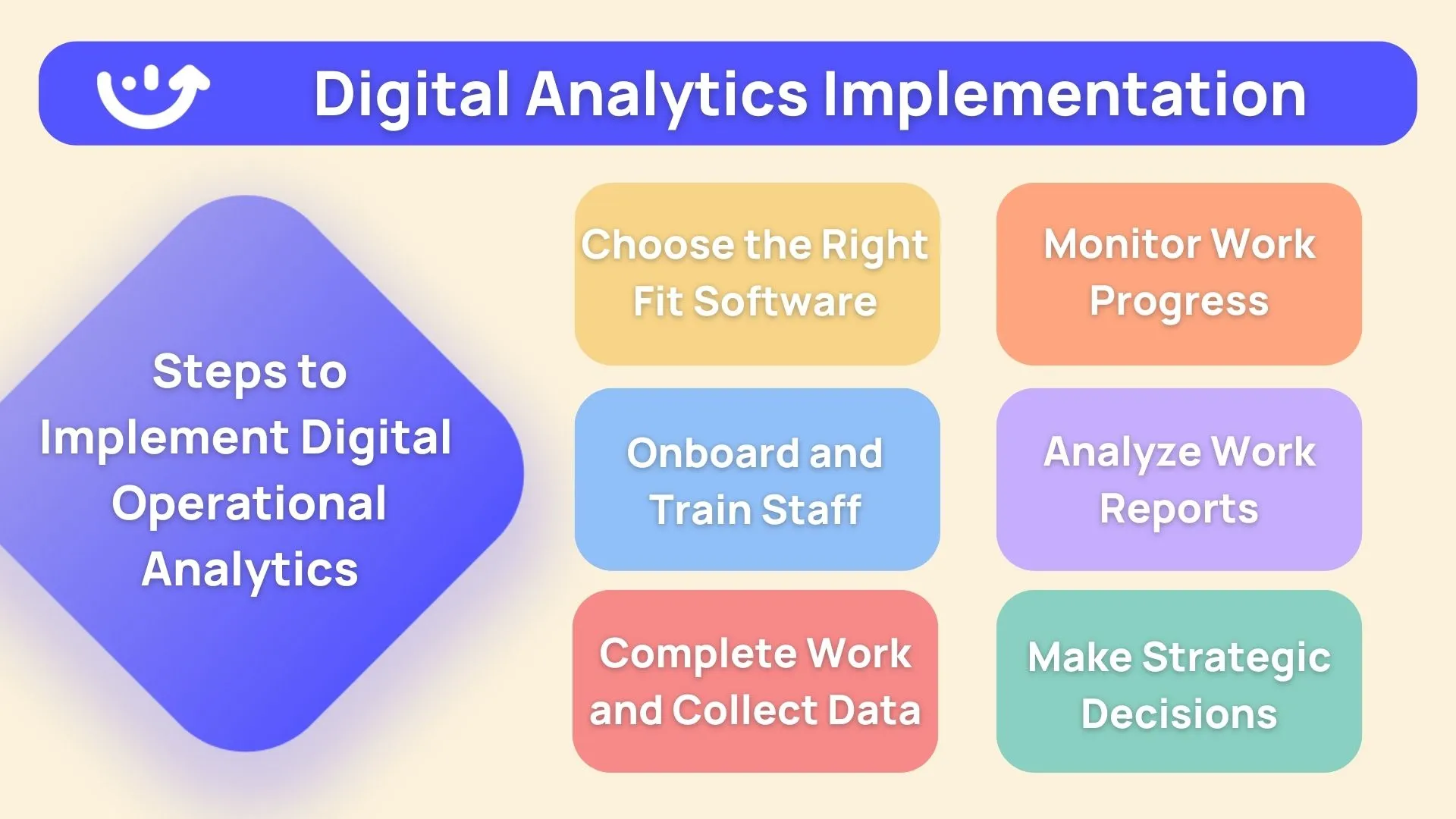
- Choosing the Right Tools: Consider factors such as the size of your facility, the complexity of your operations, and the features offered by different tools.
- Training Staff: Once you have chosen your digital tools, you must provide adequate training to ensure they can use them effectively. This may involve providing online training resources, conducting on-site training sessions, or working with the tool provider to develop customized training materials.
- Integration with Existing Systems: It's important to ensure that any new digital tools you implement can integrate with your existing facility management systems. This can help to ensure a seamless transition and minimize disruption to your operations.
- Monitoring and Evaluation: Once your digital tools are in place, monitoring and evaluating their effectiveness is essential. This may involve tracking key metrics such as efficiency, productivity, and cost savings and seeking feedback from staff and stakeholders.
- Continuous Improvement: Implementing digital tools for operational analytics is not a one-time event. It requires ongoing monitoring, evaluation, and continuous improvement to ensure you get the most out of your tools and optimize your facility management processes.
- Security and Data Privacy: Always consider security and data privacy issues. This may involve implementing appropriate data security measures, such as encryption and access controls, and ensuring compliance with relevant data protection regulations.
With careful planning and execution, facility managers can successfully implement digital tools for operational analytics and realize significant benefits.
.webp)
%201%20(1).webp)