A Quality Management System (QMS) is crucial for businesses because it ensures they consistently deliver top-notch products or services.
You can use QMS to boost productivity by streamlining processes and following regulations. It also encourages a culture of getting better all the time, empowers employees, and builds trust with customers. Overall, a QMS is like a smart tool that helps businesses do things right, stand out from the competition, and build a strong reputation for success in today's fast-paced and competitive business world.
A QMS brings together all internal processes of the organization and creates projects in a more organized way. It helps organizations figure out, measure, control, and make better the important things they do to run the business.
To have a full ISO 9001 Quality Management System, you need to meet all the rules of ISO 9001, and that includes the paperwork you need to do.
What is ISO 9001?
ISO 9001 is a globally recognized standard that helps organizations improve their performance and meet customer expectations, regardless of the businesses' size or the industry.
It's all about establishing, implementing, maintaining, and continually improving a quality management system (QMS) to ensure consistently high-quality products or services.
Priced on per user or per location basis
Available on iOS, Android and Web
Why is ISO 9001 important?
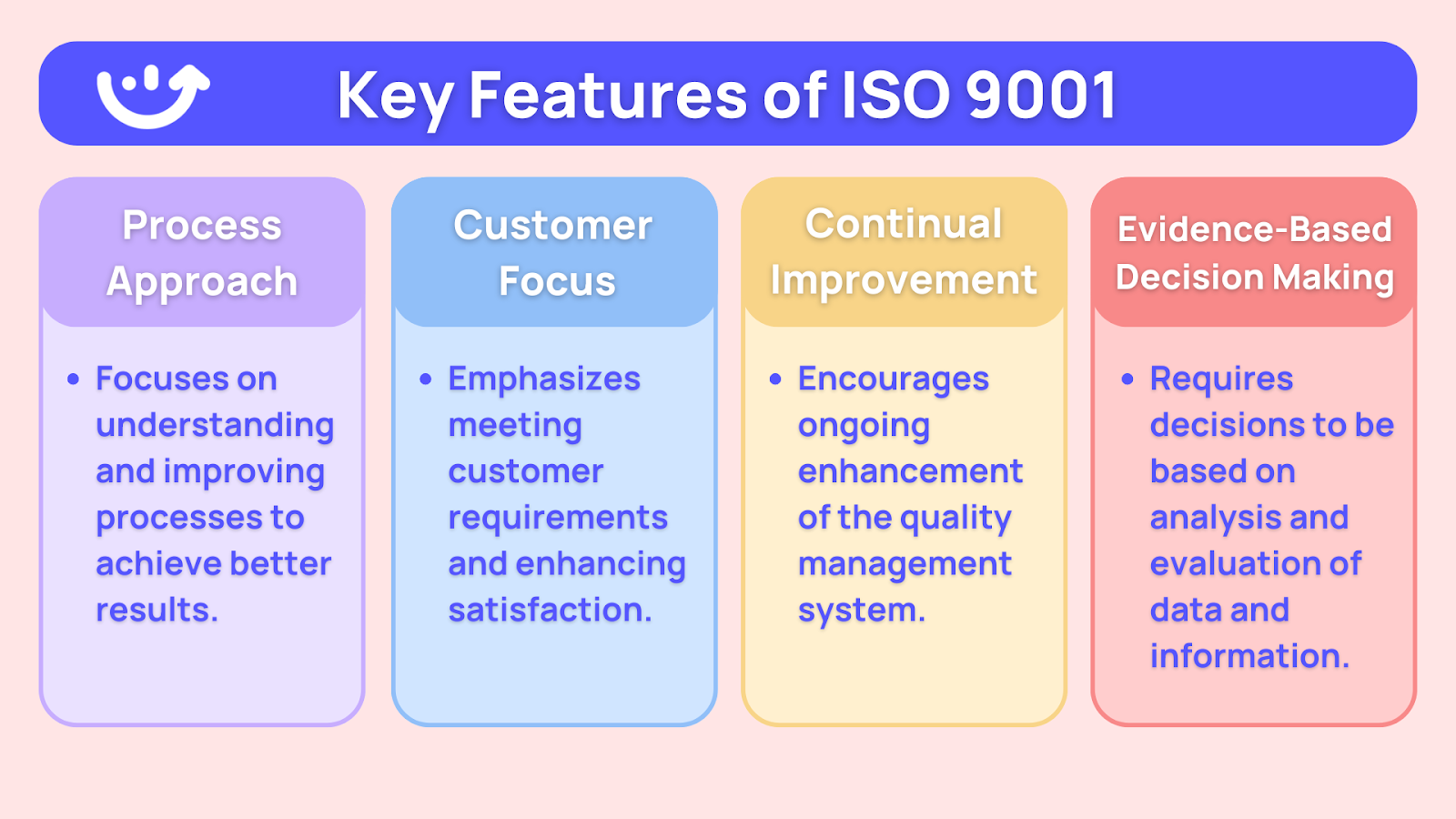
When you implement ISO 9001, it means your organization has set up effective processes and trained its staff to consistently deliver top-notch results. Here's why ISO 9001 is so important: it's the most widely used quality management standard worldwide, with over a million organizations in 189 countries getting certified. While certification isn't mandatory, having ISO 9001 in place carries numerous benefits.
- Customer Confidence: ISO 9001 ensures your organization has strong quality control processes, building trust and satisfaction among customers.
- Effective Complaint Resolution: The standard provides guidelines for efficiently handling customer complaints, contributing to timely and satisfactory solutions.
- Process Improvement: ISO 9001 helps identify and eliminate inefficiencies, reduce waste, streamline operations, and make informed decisions, leading to cost savings and better outcomes.
- Ongoing Optimization: Regular audits and reviews, encouraged by ISO 9001, enable organizations to continually refine their quality management systems. It not only helps stay competitive but also ensures long-term success.
In simpler terms, ISO 9001 is like a quality blueprint that, when followed, not only boosts customer trust but also helps your organization become more efficient, responsive to customer needs, and better equipped for long-term success.
What topics does ISO 9001:2015 cover?
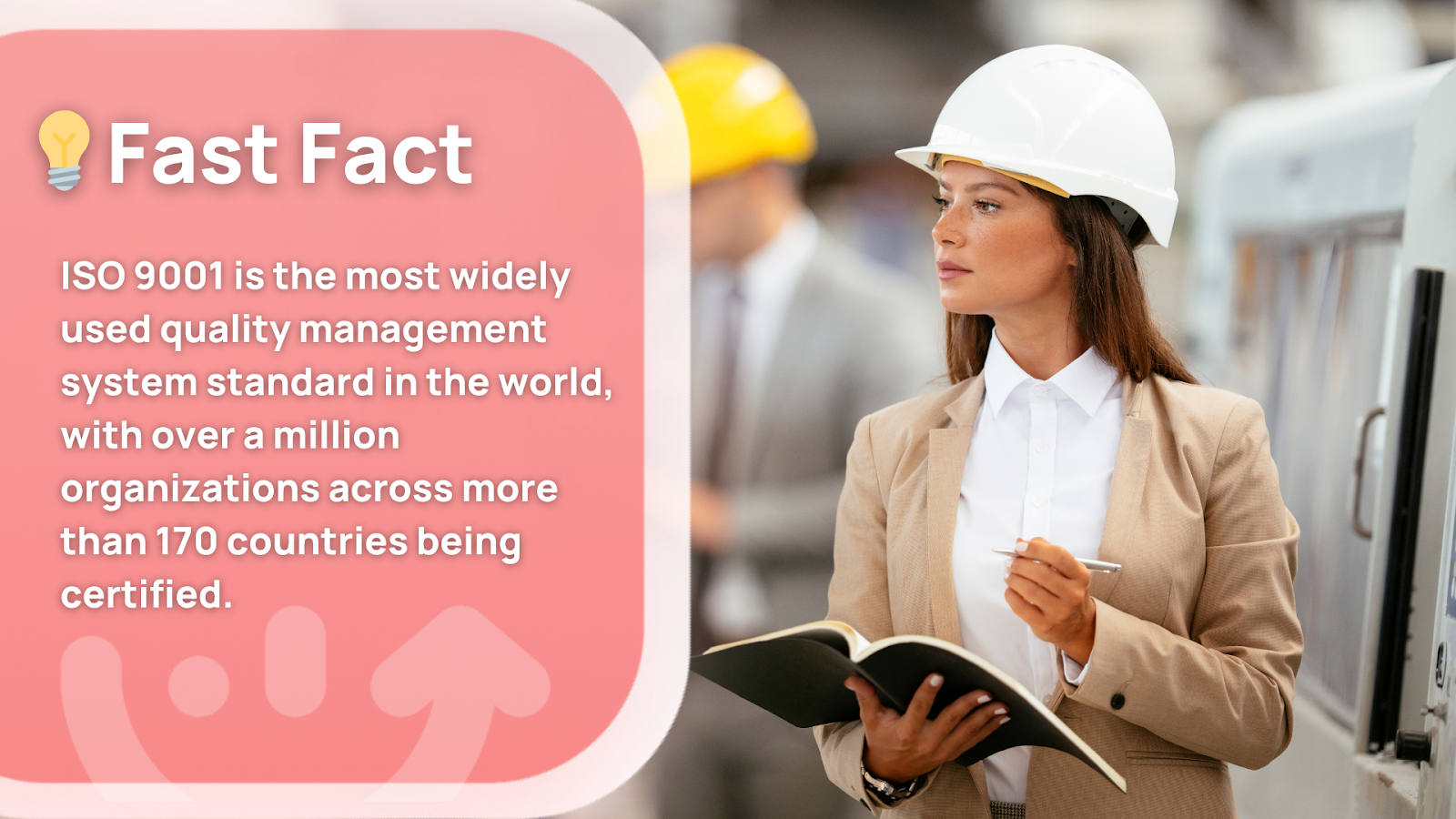
ISO 9001 operates on the plan-do-check-act methodology, offering a structured way for organizations to establish effective quality management. It takes a process-oriented approach to document and review the necessary structure, responsibilities, and procedures. Here are some key areas covered by the standard:
- Requirements for a QMS: Involves documenting information, planning, and determining how processes interact.
- Responsibilities of Management: Outlines the role and duties of organizational leadership in ensuring quality.
- Management of Resources: Covers aspects like human resources and the work environment.
- Product Realization: Encompasses the steps from design to delivery of a product or service.
- Measurement, Analysis, and Improvement: Includes activities such as internal audits and corrective/preventive actions to enhance the QMS.
The 2015 revision of ISO 9001 introduced several changes to keep pace with evolving organizational environments. These updates include:
- New Terminology: Introducing new language to align with contemporary practices.
- Restructured Information: Organizing information in a more streamlined manner.
- Emphasis on Risk-Based Thinking: Encouraging a focus on risk to enhance the application of the process approach.
- Improved Applicability for Services: Making the standard more relevant and applicable to service-oriented organizations.
- Increased Leadership Requirements: Putting a stronger emphasis on leadership roles within the organization.
In simpler terms, these updates ensure that ISO 9001 stays relevant in today's dynamic business landscapes, emphasizing adaptability, risk management, and effective leadership for organizations striving for quality excellence.
The requirements of ISO 9001
ISO 9001 outlines its requirements through a framework known as Annex SL, comprising ten clauses that address four critical domains:
- Management Responsibility: It involves delineating the areas within the Quality Management System (QMS) that demand the attention, involvement, and accountability of the management team.
- Resource Management: This clause specifies how resources, encompassing personnel, infrastructure, and facilities, should be allocated to ensure optimal performance and efficiency.
- Product Realization: Within this domain, the ISO 9001 Standard provides details on how a business should operate to deliver a high-quality service or product, outlining the necessary processes and procedures.
- Measurement, Analysis, and Improvement: This clause offers guidance on evaluating the effectiveness of the Management System. It provides methods for measurement and analysis, facilitating the continual improvement of the system over time.
Benefits of ISO 9001
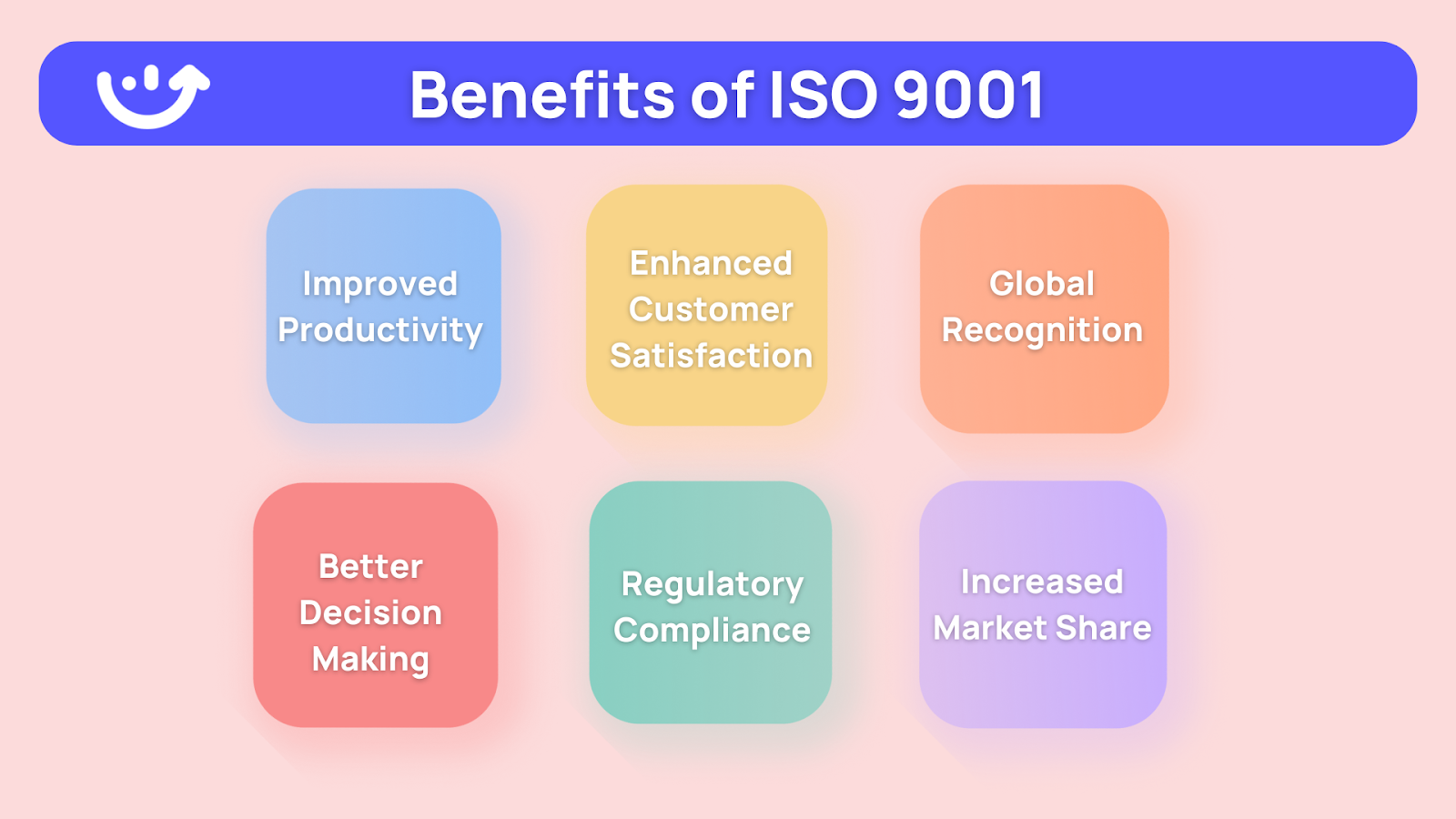
Implementing an ISO 9001 Quality Management System (QMS) offers several advantages, including streamlined processes, error reduction, time savings for management, and enhanced internal communication. Companies embracing this approach enjoy heightened employee morale, improved customer retention, and increased revenues.
In essence, ISO 9001 certification demonstrates an organization's customer-centric focus and dedication to delivering high-quality services. The key benefits of adopting the ISO 9001 framework include:
- Increased Efficiency: By adhering to industry best practices and prioritizing quality, organizations can effectively reduce costs.
- Revenue Growth: ISO 9001 certification solidifies a business's reputation as a committed and trustworthy entity. This credibility leads to winning more tenders and contracts, increased efficiency, customer retention, and a rise in repeat business.
- Enhanced Customer Satisfaction: Understanding customer needs and minimizing errors instills confidence in customers regarding the organization's ability to consistently deliver quality products and services.
- Improved Supplier Relationships: ISO 9001 certification establishes best-practice processes, contributing to more efficient supply chains. This, in turn, boosts suppliers' confidence in the organization's processes.
- Elevated Employee Morale: Improved internal communication ensures that everyone is aligned with a common agenda, fostering higher levels of employee satisfaction and engagement.
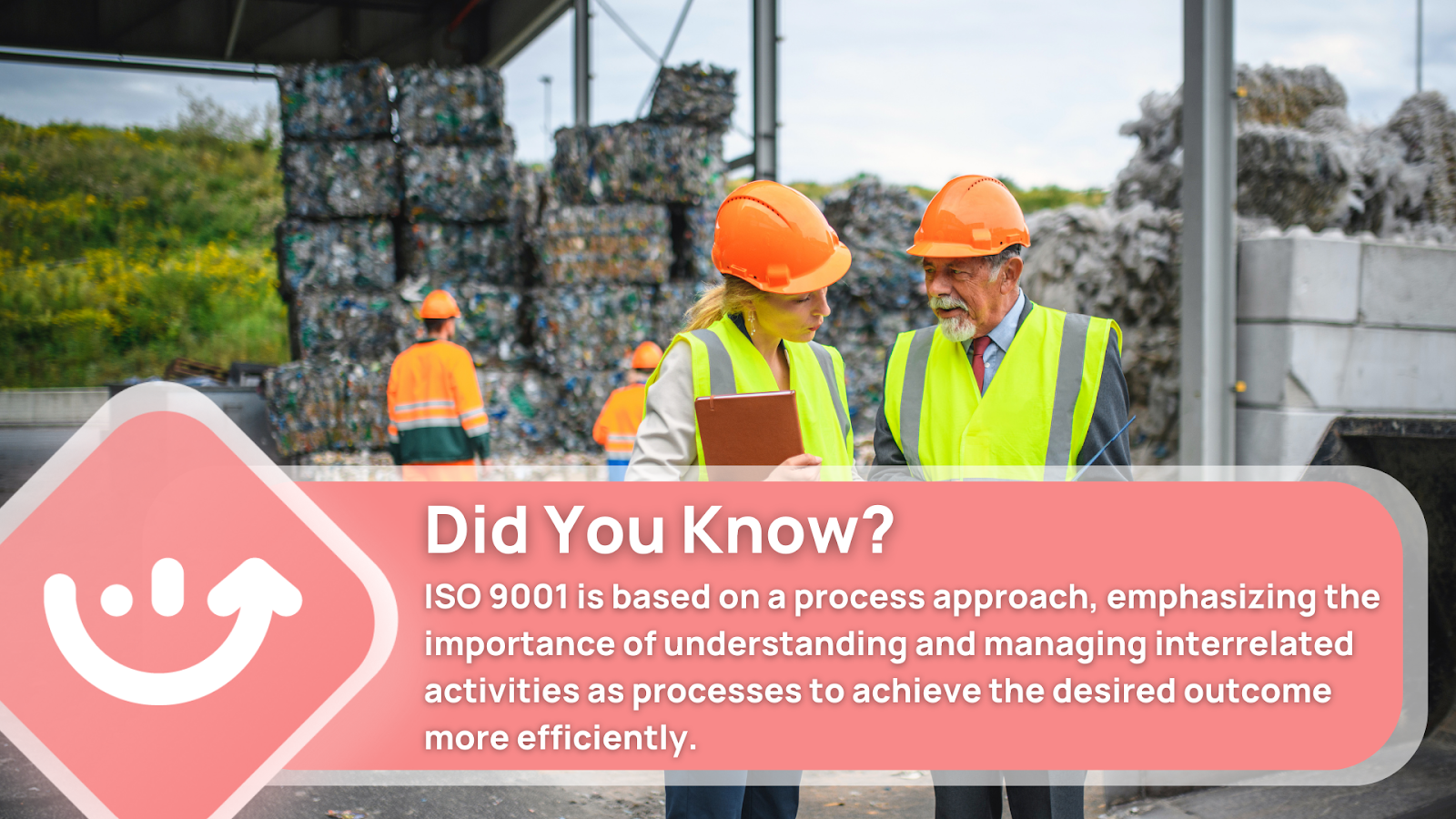
ISO 9001 Steps Implementation for Your Business
Implementing ISO 9001 in your business involves several key steps to ensure a smooth and effective process. Here's a simplified guide to help you navigate the ISO 9001 implementation:
- Commitment and Leadership:
Secure commitment from top management to support and lead the implementation of ISO 9001. Leadership involvement is crucial for the success of the Quality Management System (QMS).
- Establish a Quality Policy:
Define a clear and concise quality policy that aligns with your business goals. Ensure that the policy reflects your commitment to meeting customer requirements and continually improving your processes.
- Identify Relevant Processes:
Identify and document the key processes within your organization. This includes processes related to product/service realization, support processes, and management processes.
- Risk Assessment:
Conduct a risk assessment to identify potential risks and opportunities related to your processes. This step is essential for effective risk-based thinking in the QMS.
- Develop Procedures and Documentation:
Create the necessary documentation, including procedures, work instructions, and forms. Ensure that these documents support the effective implementation of the QMS and are accessible to relevant personnel.
- Employee Training:
Provide training to employees on the requirements of ISO 9001, their roles within the QMS, and the importance of quality management. Ensure that everyone is aware of their responsibilities.
- Internal Communication:
Establish effective communication channels to ensure that relevant information about the QMS is shared within the organization. This fosters a culture of collaboration and quality awareness.
- Implementation of Processes:
Roll out the documented processes within your organization. Monitor and measure their effectiveness in achieving the desired outcomes, and make adjustments as needed.
- Monitoring and Measurement:
Implement a system for monitoring and measuring key processes and performance indicators. This data will be valuable for assessing the effectiveness of the QMS.
- Internal Audits:
Conduct internal audits to evaluate the conformity and effectiveness of your QMS. Internal audits help identify areas for improvement and ensure compliance with ISO 9001 requirements.
- Management Review:
Hold regular management reviews to assess the QMS's ongoing suitability, adequacy, and effectiveness. This involves analyzing data, evaluating performance, and making decisions for improvement.
Establish a process for addressing non-conformities and implementing corrective actions. Additionally, consider proactive measures to prevent potential issues from arising.
- Certification:
If desired, engage a certification body to conduct an external audit for ISO 9001 certification. This step is not mandatory but can enhance your organization's credibility and market competitiveness.
- Continuous Improvement:
Foster a culture of continuous improvement by encouraging feedback, analyzing performance data, and implementing changes to enhance the effectiveness of the QMS.
ISO 9001 FAQs
Who should implement ISO 9001?
Any organization, regardless of size or industry, seeking to improve quality management and customer satisfaction should implement ISO 9001.
Is there a standard tailored to my sector based on ISO 9001?
Yes, many sectors have specific standards built on ISO 9001. For example, automotive has ISO/TS 16949, and aerospace has AS9100.
What are the key topics covered by ISO 9001?
ISO 9001 covers customer focus, leadership, process improvement, employee engagement, and continuous improvement.
How does ISO 9001 differ from ISO 14001?
ISO 9001 focuses on quality management, while ISO 14001 is for environmental management. They address different aspects of an organization's operations.
What sets ISO 9001 apart from ISO 13485?
ISO 9001 is a general quality management standard, while ISO 13485 specifically targets organizations in the medical device industry.
Where can I seek assistance with auditing ISO 9001?
You can hire certified auditors or consultancies specializing in ISO standards for assistance with auditing ISO 9001.
What does ISO 9001 certification involve, and is it necessary for my organization?
Certification involves a third-party audit confirming compliance with ISO 9001. While not mandatory, certification signals a commitment to quality and can enhance credibility and competitiveness.
.webp)
%201%20(1).webp)