Frontline execution in contemporary workplaces has everything to do with precision, swiftness, and lucidity. It does not matter whether you are working in a retail business, a restaurant, a factory, or doing field service work; paper-based checklists are over.
Meet visual checklist software, a go-anywhere, change-everywhere tool that helps make your operations more reliable, understandable, and responsible.
It is not just an exercise of checks and balances. It is about showing that something has been done, and done well, with photos, videos, annotations, and live updates.
In this article, we are going to deconstruct how visual checklist systems work, how they improve frontline productivity, and what to look for in such a best-in-class system.
It is your one-stop guide to learn, compare, and apply the use of digital checklist tools to your modern teams.
Priced on per user or per location basis
Available on iOS, Android and Web
What is Visual Checklist Software?
Visual checklist software is an online app that helps people track, confirm, and record jobs through rich media such as photos, videos, annotations, and electronic signatures.
Compared to standard checklist applications, the visual checklists provide a mobile-first user experience with live tracking, compliance oversight, and automation of tasks.
The tool makes communication between on-site teams and managers efficient and helps close the gap because they have visual evidence and have access to the data in real time. Rather than giving verbal communications on task progress or waiting long periods to get email reports, managers get to see evidence of their work as it occurs, quite literally.
They’re used across industries, from restaurant inspection checklists for managers to retail store audits by teams who need more than a checkbox to confirm something’s done. Think of it as your team’s operational truth serum: transparent, visual, and built for action.
Why Visual Checklists Matter
Let’s say your team is prepping a retail store for a seasonal reset.
A simple checklist might ask: “Is the signage updated?” but a visual checklist goes further. It makes the employee take a live picture of the sign, the location is tagged, and everything can be marked as well.
This isn’t just helpful—it’s transformative.
- Accountability: You see the work done. No assumptions.
- Visual Proof: No room for confusion or guessing.
- Location-stamped: Know how the job has been carried out.
- Triggers & Alerts: Create solutions in a matter of seconds.
- Dashboards: Performance and exception visions.
How It Works (In Simple Terms)
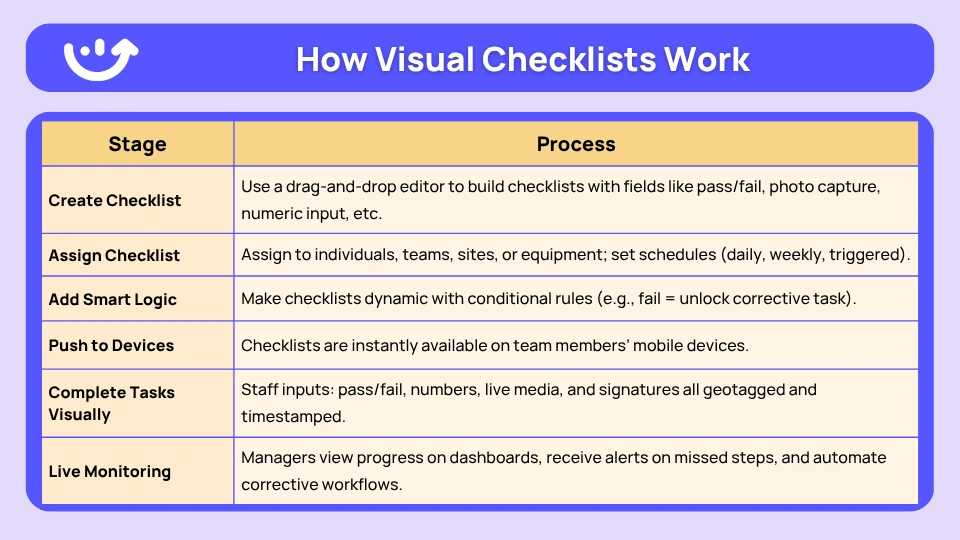
Visual checking software helps convert your daily work processes into regular visual steps that are simple to follow, simple to monitor, and impossible to cheat. This is how the whole thing ends up:
The first one is that you develop a checklist through a drag-and-drop editor. You do not require any technical knowledge to use it; select the steps, select the type of input fields (such as pass/fail, photo, number entry), and you can tabularize logically.
Then, you can assign the checklist to individuals, groups, places, or even to equipment. You have options of scheduling it to repeat, either daily or weekly, or according to some triggers.
Add smart conditional logic to make the checklist responsive. For example:
- “If freezer temp is above 40°F, prompt user to take a photo and alert manager.”
- “If the answer is ‘Fail,’ unlock a corrective task with photo capture.”
Once it’s ready, the checklist is pushed to mobile devices. Whether your team is on the floor, in the field, or moving between sites, they get notified instantly.
As tasks are completed, staff interact with a touch-friendly interface. Instead of just ticking a box, they:
- Tap the pass/fail buttons
- Enter numeric readings
- Take live photos and videos
- Add annotations
- Capture digital signatures
All inputs are timestamped and geotagged, ensuring on-site compliance.
Managers and operators can track progress live via dashboards. Missed steps show up immediately. Automatic alerts or actions to be carried out on exceptions are created: no chasing needed.
Simply put: With zero micromanaging, you get visibility, traceability, and accountability. Teams remain keen, work is done to standard, and things that are going bad are spotted before the damage is complete. It is a smarter, visually-changed method in running the operations without anything falling through its cracks.
Who Uses Visual Checklist Software?
1. Retail Chains
Retail teams rely on visual checklist tools for:
- In-store marketing verification with photo proof
- Planogram compliance audits
- Store opening/closing checklists
- Product stock checks with annotated images
- Merchandising resets using photo-required steps
- Staff onboarding with visual SOPs
- Weekly store walks with regional managers
Retailers benefit greatly from the ability to capture visual data instantly from each location. It allows corporate teams to enforce brand standards, validate execution, and roll out campaigns faster, with photographic proof to show it.
Check out this Retail Store Pre-Opening Checklist.
2. Restaurants
Restaurant operators benefit through:
- Food safety inspections with photo-documented temps
- FOH/BOH daily prep routines
- Health inspection readiness with signature capture
- Live photo evidence of sanitization procedures
- Real-time flagging of expired items or broken equipment
- Staff training SOPs with embedded visual walkthroughs
- Menu display compliance
Restaurant chains especially appreciate how mobile visual checklists reduce the prep time before health inspections, while simultaneously improving compliance across all shifts.
3. Facilities Management
Facility teams use visual checklists to:
- Conduct routine maintenance with annotated photo capture
- Launch inspections via QR code at asset locations
- Track repairs with geo-stamped visual logs
- Validate the condition of machinery with visual inputs
- Third-party inspection and vendor visits to the documents
- Take walk-throughs in heavy traffic volume areas
- Reduce the time taken to reply to urgent work orders
Facilities professionals depend on photo-based documentation to ensure assets are functioning, issues are resolved quickly, and contractors are held accountable.
4. Hospitality
Hotels and resorts apply these tools for:
- Housekeeping SOPs with room readiness photos
- Brand standard enforcement across chains
- Visual checks of minibar, amenities, and cleanliness
- Pre-check-in condition verification
- Room turnover tracking and defect reporting
- Guest room audits before VIP arrivals
- Maintenance checks before occupancy
This helps hotel brands maintain consistent guest experiences, no matter the property. Plus, the photographic proof can reduce disputes around room conditions.
5. Safety & Compliance
Compliance officers leverage visual checklists for:
- Fire extinguisher and emergency equipment inspections
- OSHA documentation with annotated observations
- Evacuation route checks with geolocation
- Real-time alerts for failed checklist items
- Training verifications with digital sign-off and image-proof
- On-the-spot visual investigations during audits
- Regular safety drills with photographic records
Photo checklists become the compliance department’s best friend. They reduce the risk of violations while building a clear audit trail that regulators respect.
6. Construction & Industrial Teams
Frontline teams in industrial settings use them for:
- Safety toolbox talks with photo sign-in
- Equipment checkouts with pre/post-use photos
- Daily logs of site hazards with visual flags
- Compliance with PPE protocols through visual tracking
- Incident documentation with video or photo capture
- Scaffold inspections with visual tagging
- Work zone readiness assessments
Visual inputs enhance safety workflows and improve communication between crews, foremen, and safety officers.
7. Logistics & Transportation
Logistics companies use them to:
- Conduct vehicle inspections with image documentation
- Track delivery area compliance and cleanliness
- Log loading dock conditions
- Verify completed drop-offs with photo timestamps
- Standardize fleet-wide maintenance checks
- Confirm seal integrity before and after transport
- Digitally document delivery exceptions
The possibilities are endless. Any industry that needs real-world proof, operational consistency, and mobile execution can benefit from visual checklist software. From healthcare to manufacturing to property management, it’s quickly becoming the go-to solution for modern field ops.
Top Visual Checklist Software Options
Choosing the right visual checklist tool can make or break your operations. Here are a few that lead the pack:
- Xenia – Excellent for food safety and restaurant compliance.
- Lumiform – Flexible templates with strong photo capture features.
- GoCanvas – Enterprise-ready, customizable checklist, and form builder.
- FORM.com – Ideal for field service and inspections.
- ProntoForms – Rich media support with integrations for enterprise teams.
- Fulcrum – Powerful geo-enabled inspections and mobile data collection.
- Checkit – Tailored for hospitality and facilities workflows.
- MaintainX – Built for operations and maintenance with strong visual tools.
When choosing a solution, focus on mobile usability, media capture features, conditional logic, and reporting capabilities.
Key Features of Xenia That Make It Best Visual Checklist Software
Let’s not dance around it, Xenia isn’t just another checklist app. It’s a full-on operations execution system built specifically for teams that need visual proof, real-time accountability, and mobile-first usability in their daily workflows.

1. Live, Photo-Required Tasks
Xenia forces on-the-spot photo capture, no uploading old images from the gallery. It is impossible to fake it. They just need to snap photos with the camera of their device, and those can be timestamped and geo-tagged, so it happen in time and place.
Need to show a clean prep station, an expired product, or equipment damage? Snap it, annotate it, and log it. All within the flow of work. It is designed to fit the conditions of the fields and not the dream of offices.
Offline mode implies that your team could continue working in the basement, in a remote location, or in an area without a Wi-Fi signal, and Xenia will automatically sync it all when they are back online.
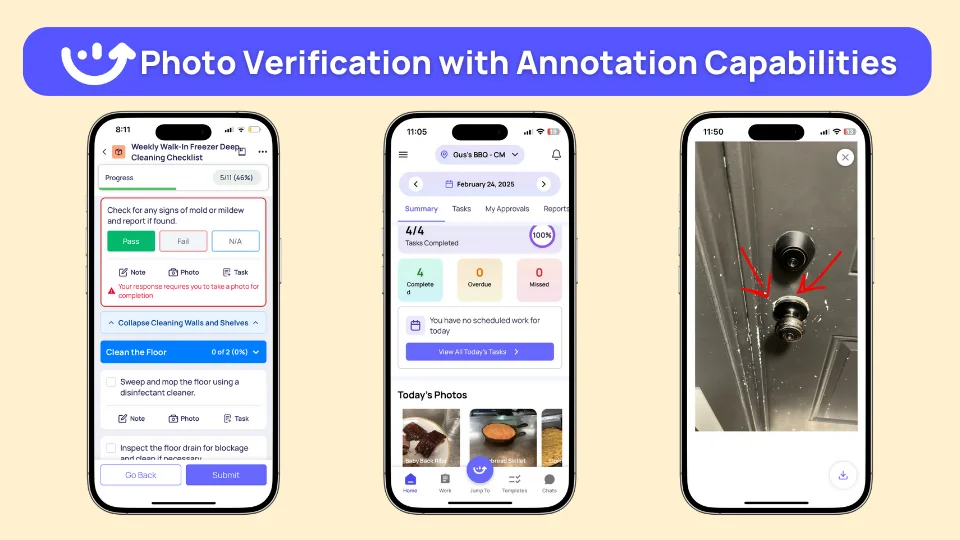
2. Mobile-First by Design
Xenia’s interface is built for frontline teams, not desk workers. Big buttons. Simple UI. Works on any mobile device, even offline. It’s optimized for the realities of fieldwork, not idealized office environments.
Offline mode means your team can keep working in a basement, remote site, or Wi-Fi dead zone, and Xenia will sync everything automatically once they're back online.
3. Smart Visual Inputs
This isn’t a checklist that just says “yes” or “no.” Xenia supports:
- Pass/Fail toggles
- Temperature fields with auto-alerts
- Conditional logic (fail a step? New task appears)
- Live photo and video capture
- Signatures for accountability
- Measurement fields (PSI, humidity, etc.)
It turns passive forms into responsive workflows. And when issues come up, Xenia adapts, prompting deeper inputs or triggering follow-ups on the spot.
.webp)
4. Real-Time Ops Visibility
With Xenia, managers see what’s happening as it happens. Dashboards show:
- Task completion by location
- Visual proof of work
- Missed or late items (color-coded)
- Checklist stats by team, shift, or asset
Forget chasing updates. Xenia gives you real-time operational clarity with visuals to back it all up.
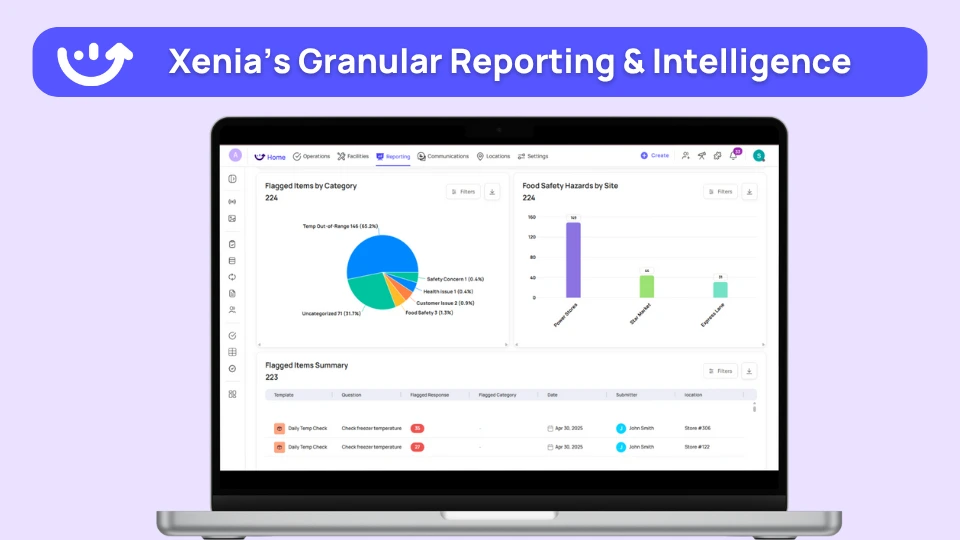
5. Logic-Driven Checklists
Xenia’s checklists aren’t static. They’re smart. You can:
- Auto-trigger corrective actions if a task fails
- Show or hide steps based on conditions
- Notify specific people when something goes wrong
- Auto-generate reports or escalate issues
This turns every checklist into a decision-making engine—automating what used to require multiple people or follow-up emails.
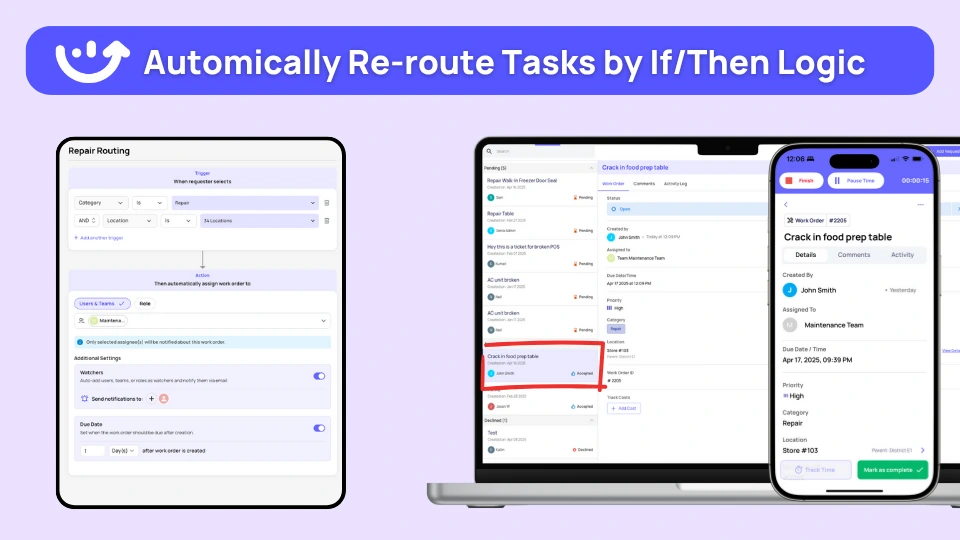
6. Visual PDF Reporting
Xenia auto-generates media-rich reports from completed tasks, perfect for audits, inspections, or team debriefs. Each report includes:
- Embedded photos and annotations
- Timestamps, locations, and checklist outcomes
- Charts and summaries to show trends
Need to prove compliance to an auditor? Or show a vendor the condition of the equipment? One-click, and you’ve got everything—visually documented.
7. QR Code Launch Points
Want to launch a checklist instantly? Just scan a QR code. With Xenia, you can tag:
- Equipment (e.g., HVAC, fridges)
- Rooms (e.g., hotel housekeeping)
- Zones (e.g., food prep areas)
Scanning launches the correct checklist, no searching, no logins, and no confusion. It's execution on demand.
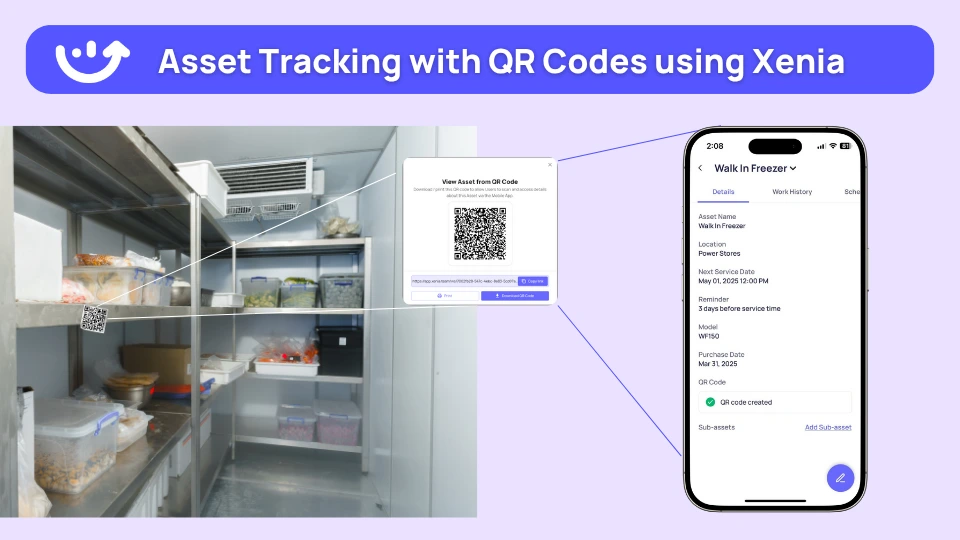
8. GPS & Time-Based Compliance
Everything in Xenia is timestamped and geotagged. You know who did the task, when, and where. This closes the loop on accountability. And in regulated industries? It’s your defense against penalties or disputes.
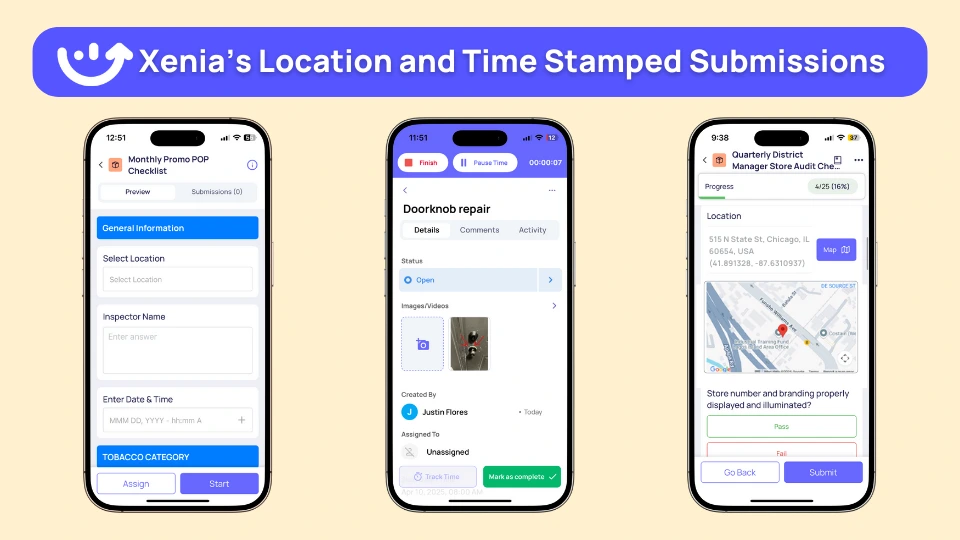
Best Practices for Visual Checklist Implementation
Implementing visual checklist software is not only an upgrade to the technological sphere, but it is a decision to change the mode of operations.
Workflows behind the software must be planned, planned, and embraced by your teams; otherwise, the software will not be effective.
Here are the best no-nonsense practices to make things work.
1. Train Your Team on the "Why" and "How"
Don’t assume everyone knows how to use mobile checklists or why it matters. It should be explained to them. Clear what live photo capture is, why it is required, and how it relates to the topic of trust, safety, and quality. Run hands-on training. Use real scenarios. Make sure your team doesn’t just check boxes; they understand the purpose behind each one.
2. Use Photo Requirements to Drive Real Compliance
Let’s be honest, without photo enforcement, shortcuts will happen. That’s human nature. The power of visual checklists lies in requiring live photo capture on the spot, not from the camera roll. This discourages pencil-whipping and faked entries. Be it a photo of a clean bathroom, a full shelf, or a fire extinguisher that works, that image documentation is your insurance policy.
3. Deploy QR Codes for Instant, Context-Aware Access
QR codes are the easiest way to launch the right checklist, at the right place, without logins or searching. Stick them on equipment, cleaning carts, room doors, or facility entry points. One scan, and boom, the right checklist appears. It is quicker, minimizes errors of a human factor, and no operations can be skipped due to the inability to locate the appropriate form.
4. Standardize the Core—But Allow for Local Flexibility
Your brand, safety, and compliance checklists should follow a standard structure across all sites. But give individual locations the freedom to add steps that fit their reality. Maybe one store has an old freezer that needs an extra check. Or a remote facility with different maintenance cycles. Standardization builds consistency; flexibility ensures adoption.
5. Use Smart Logic to Go Deeper When Needed
Checklists shouldn’t just be linear to-dos. Use conditional logic to branch deeper based on the inputs. If someone fails a step (“Temp is too high”), then prompt for a photo, a note, and a follow-up task. This approach stops issues from slipping through the cracks and makes every checklist an active quality gate.
6. Review Reports Weekly—Not Just When Something Breaks
Don’t let reports collect dust. Set a weekly rhythm. Look for trends: Are certain locations skipping steps? Are photos being uploaded with poor quality? Is a specific checklist taking too long? Visual reports show you patterns you can act on—before they become liabilities.
7. Tie Performance to Accountability
Make checklist completion part of your site reviews and individual performance metrics. Recognition for top performers and coaching for those who lag behind drive consistent adoption. When people know their visual logs are being reviewed, behavior changes.
8. Templates with Feedback and Findings
The checklists that you have should not be fixed. Amend them on a regular basis depending on the feedback of the team, issues in the audit, or changes in operations. The built-in data will help you perform tuning of what, how, and what evidence will be asked.
9. Automate Reminders and Follow-Ups
Nagging should be left to the system. Set up checklist reminders on overdue schedules. Raise a warning when tasks remain overdue. Take advantage of auto-assignments, in case a step fails. The weaker the memory is, the more tenacious is performance.
10. Use the Data to Improve Scheduling and Workflows
Checklist timestamps show you when work is actually getting done. Use that data. Shift task schedules to better match real behavior. Adjust staffing during high-friction windows. Streamline SOPs based on where people struggle or skip.
Real-World Use Cases
Visual checklist software isn’t some abstract “digital transformation” pitch—it’s real ops, on the ground, running smoother. Here’s how it plays out across industries, day in and day out.
1. Store Opening Checklists
Retail managers know the chaos that can happen when morning prep is rushed or incomplete. A visual checklist transforms that scramble into a predictable routine. Staff arrive, scan a QR code at the back door, and start checking off tasks:
- Take a live photo of the POS terminal—fully powered and updated.
- Snap the front signage to confirm it’s aligned with the day’s promo.
- Document floor cleanliness, stocked shelves, and working lights.
- Sign off with a digital signature and timestamp.
This isn’t just busy work—it’s operational insurance. Regional managers reviewing the dashboard can verify, visually, that brand standards are met before the doors even open.
Get a Retail Store Pre Opening Checklist
2. Kitchen Temperature Logs
In food service, temperature logs are more than SOP, they’re the thin line between compliance and a health code disaster.
Here’s how a photo-based checklist handles it:
- Line cooks take real-time readings of fridges and freezers using embedded thermometer fields.
- If a temp is out of range, the checklist triggers a required photo of the unit’s gauge.
- Add a note or video if there are visible frost or mechanical issues.
- An alert notifies the manager instantly before spoiled food ends up on a plate.
This kind of workflow saves thousands in food waste and protects the brand from customer safety issues or inspection failures.
3. Hotel Room Inspections
Housekeeping doesn’t just need to know what to clean—it needs to prove that the room meets standards before a guest walks in.
- Checklist step: “Is the minibar stocked?” → Snap a live photo.
- “Are linens free of stains?” → Required photo with annotation tools.
- “Any maintenance issues?” → Annotate a photo of a cracked tile and trigger a repair task.
This isn’t micromanagement—it’s consistency. And when your brand promises a certain guest experience, visual checklists make that promise visible and verifiable.
4. Franchise Brand Audits
Brand consistency across multiple locations is a nightmare without visual confirmation.
- Field reps visit each franchise store, and launch a brand standards checklist.
- For each merchandising element, they capture live photos.
- Signage alignment, product displays, and uniform compliance—all documented with visuals.
- Non-compliant items prompt immediate follow-up tasks sent to store leads.
Now, corporations don’t rely on vague reports. They get a gallery of proof—organized, searchable, and timestamped.
5. Equipment Maintenance Checks
Visual checklist software takes maintenance from reactive to proactive.
- A technician scans a QR code on an HVAC unit.
- The checklist for that specific model launches.
- The tech performs inspections: filter, thermostat, and motor—all marked with photo confirmation.
- Notes or photos of wear and tear trigger maintenance tickets.
- A digital signature seals the record.
Geo-stamping and timestamps are nothing new, but somehow you now know that the task was not only checked as done but rather completed on-site on time.
Conclusion
Visual checklist software is not another method of checking boxes it is a game changer in frontline operations. Having the power to capture rich photos and videos, mobile-first architecture, and real-time insight, they will add clarity, consistency, and confidence to your daily execution.
Running a multi-site facilities operation, a retail empire, or a chain of restaurants, going visual also means going smarter. And what are the results? Fewer errors, greater requirements, and a consistently on-point group.
When all it takes is good documentation and visibility, then switching to a visual checklist system may be the most intelligent operational change that you can make this year.
Looking for a system that does it all? Xenia is what you’re looking for.
.webp)
%201%20(1).webp)