When machinery malfunctions cause missed deadlines, unplanned downtime, and an increase in extraneous repairs, it can be very difficult to achieve your daily production goals. Even with well-maintained equipment, unplanned downtime is caused by random failures. Having older equipment is known to be the leading cause of unplanned downtime.
Deciding the best planned and reactive maintenance strategy can help reduce and impact and frequency of equipment failure, and help to improve the life of critical assets.
In this post, we will go over the fundamental different types of reactive maintenance techniques, such as reactive maintenance.
We will also discuss how OPM software may provide answers to the aforementioned ways. Maintenance approaches can benefit from machine learning and predictive analytics to improve their efficiency. Furthermore, we will look at the best-fit strategy in terms of cost and advantages, as well as how Xenia optimizes scheduled and reactive maintenance.
Available for up to 5 users
Premium for $99/month for the first 20 users (with free trial period)
Available on iOS, Android and Web
What is Reactive Maintenance?
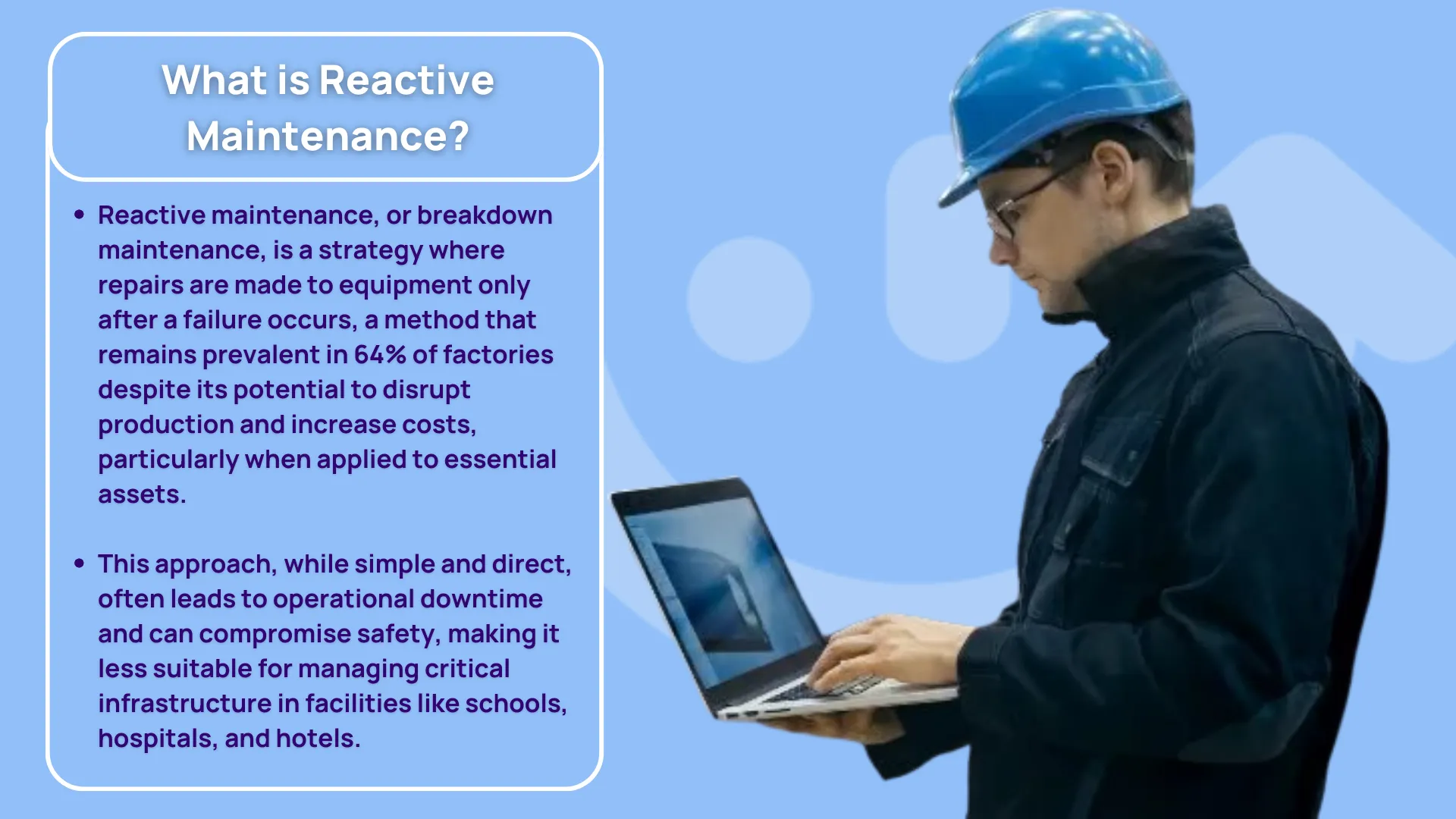
Reactive maintenance also known as breakdown maintenance, responds to equipment failures once they occur.
While this approach can be effective with low-priority equipment with a low cost to replace, if employed on essential assets, it hampers production schedules, drives up repair costs, and even creates safety issues for workers.
Facility management is one of life’s constant issues in the modern era.
The assets of schools, hospitals, and hotels are worked on constantly. The everyday breakdown of any equipment causes not only a loss of money but also to be put in predicaments while the units of operation are being fixed.
With 64% of factories using it, reactive maintenance remains the world's oldest maintenance method and continues to be widely practiced.
That’s what a recent study by Plant Engineering found.
Planned and reactive maintenance is one of the most important aspects of any manager's workflow. It is when an unforeseen issue arises like a light bulb going out or a broken A/C unit. Each issue generates a work order that notification generation of an entire process typically involves a single maintenance technician.
They either fixed the issue or viewed the issue to be bigger than what they so they contacted their manager the technician completed their portion and generated a work order.
Types of Reactive Maintenance
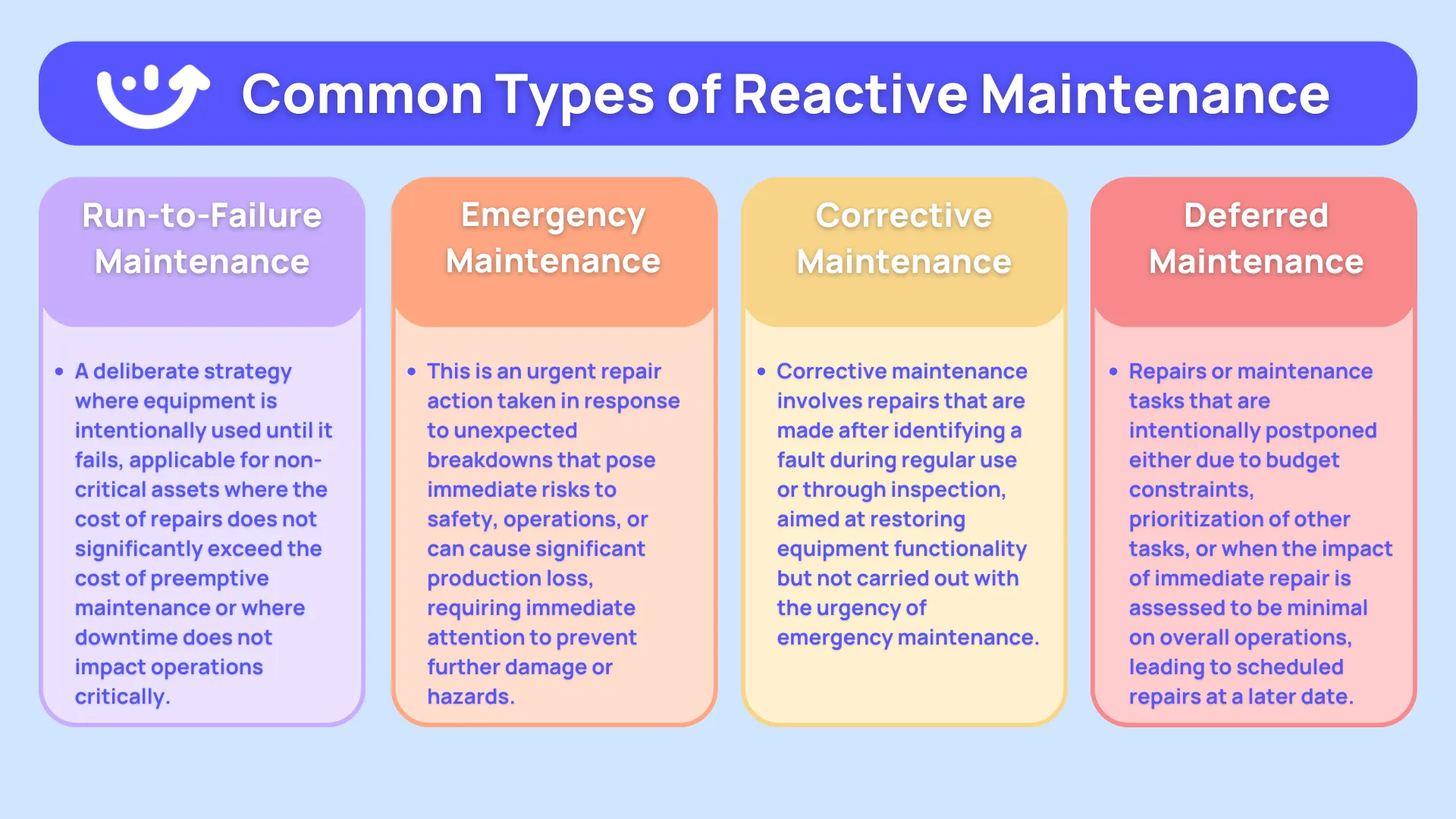
Emergency Maintenance
Immediate attention is needed to correct the situation to prevent further serious damage. Moreover, immediate repairs will help avoid additional or increased costs. (e.g. a broken water main; a no-heat situation; a flood etc.).
An example of emergency maintenance includes when a facility unexpectedly loses heat and heat must be restored as soon as possible to avoid some other issues such as frozen pipes and other water or plumbing problems. In these situations, acting as promptly as possible to prevent further damage and additional expense is the most important thing to do.
Corrective Maintenance
This type of maintenance addresses problems that do not possess immediate safety or operational risks. This could be anything from a broken vending machine at a hotel or light rust on playground equipment at a school. These are all relative issues but can be addressed with planning to allow maintenance managers to cost out parts, shop labor rates, and schedule the necessary repairs on their schedule.
Run to Failure Maintenance
Out of different maintenance types, a unique reactive strategy is Run to Failure Maintenance. This involves continuing to operate an asset until it shuts down or the maintenance manager gets a call. This would not be an emergency call, just calling after work or whenever to let you know it happened.
This wouldn’t just apply to anything that shuts down, just certain assets.
Like if a TV shuts down, get a new one. If a light bulb needs changing, do it. If a phone or computer breaks replace it. Anything that has a screen or a bulb can be replaced without anyone calling an outage report.
On the upside, one of Run to Failure Maintenance’s main advantages is the cost savings.
By not performing regular preventive maintenance or monitoring equipment, you can save operational costs. This is ideal for equipment like light bulbs, your TV, phones, some computer-related items, etc.
These items aren’t worth continuously maintaining, are easily replaceable quickly, and the facility can keep running instead of downtime.
The cost-benefit analysis of run-to-failure maintenance exposes some weaknesses of the methodology.
One of the most marked weaknesses is the chance of unexpected failures. Since assets are allowed to run until failure, unplanned breakdowns can occur. Unplanned breakdowns can halt production unexpectedly. The costs associated with breakdowns include lost production and possible collateral damage.
That being said, run to Failure Maintenance does not provide a safe approach for critical operation or safety-related equipment. Such equipment needs to function successfully, failing will cause severe consequential damages. Moreover, it will put employee safety at risk
What is Digitalization of Maintenance?
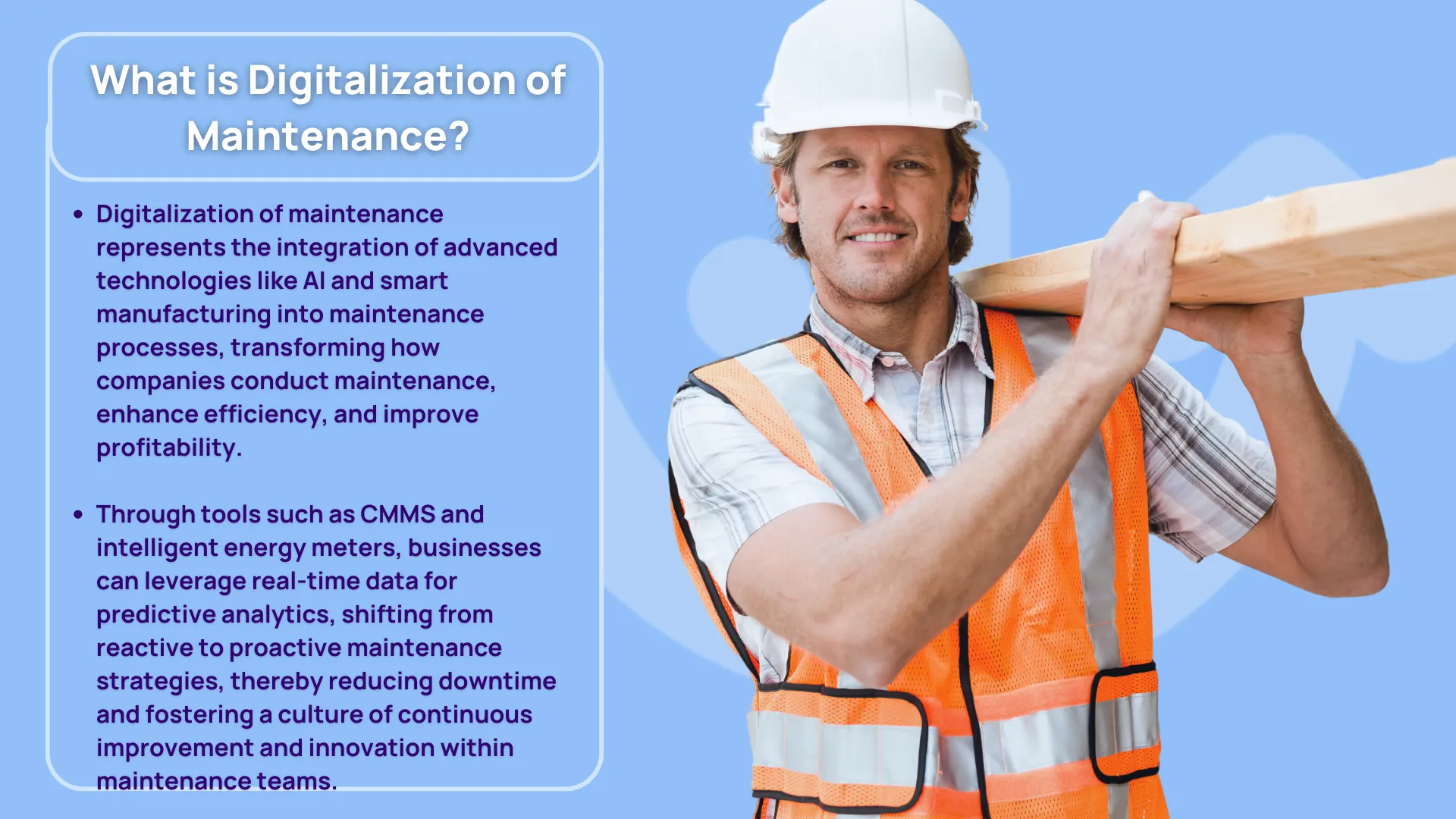
The digital transformation of maintenance, or digitalization maintenance, is a major trend in modern maintenance and is referenced in many places discussing the future of modern maintenance in industry.
This trend is prominent in global businesses, in which manufacturing, distribution, and maintenance tasks are being completely revolutionized through the use of current breakthroughs in Artificial Intelligence (AI) and Smart Manufacturing technologies.
As a result, maintenance managers have increased their profitability and their efficiency. The main achievement of this digital maintenance is eliminating unwarranted costs and expenses in the manufacturing process. Companies that use advanced technologies can create data-driven strategies to enhance decision-making, lower downtime, and finally optimize operative effectiveness.
Implementing computerized maintenance management systems (CMMS) and intelligent energy meters is a central element of this digital maintenance revolution.
These systems serve as the foundation for real-time data collection and analysis, health index calculation, and finally prescriptive corrective or predictive maintenance recommendations. By allowing real-time monitoring and predictive analytics, maintenance teams can make proactive decisions to prevent failures from taking place or spreading leading to less downtime and increased reliability.
Moreover, the digitalization maintenance processes enable companies to allocate more time to competence development, training, and execution of innovative ideas in their maintenance teams, changing the focus from reactive maintenance to proactive maintenance, significantly improving overall organizational efficiency for continuous improvement.
What is the Purpose of Digitized Maintenance?
Real-Time Data Collection
This type of maintenance makes collecting data easier. The IoT and Big Data analytics allow manufacturers to adopt an analytic approach rather than an intuitive one.
Predictive maintenance offers an unorthodox trend that can greatly decrease production costs by predictably identifying equipment failures before they even happen.
The time that maintenance professionals are required to spend on various processes has been estimated to be around 45% of their time. Digitization in maintenance operations will greatly decrease the workload of professional employees by making data access easier. Digital maintenance systems combine several key types of information in a single location.
Data-driven production also measures countless factors involved in automated manufacturing speed and allows manufacturers to experiment with and determine optimal production speeds.
Data Security
Digital maintenance systems enhance security through encrypted channels of communication between the teams and stakeholders in maintenance projects.
Encrypting the communication is important because data breaches and unauthorized access to sensitive information could otherwise be easy for unauthorized individuals.
The security of the records is even more important because they provide a backup of all maintenance, which is critical in case of unforeseen circumstances. So, if there is a fire, hardware failure, or theft, all the records will remain secure and intact.
Inventory Management
Businesses can use data from digital equipment and cloud computing to optimize spare parts, inventory, and supplies. This reduces the risk of stockouts or excess inventory, resulting in saved costs. E-maintenance tools provide an analysis of the frequency of maintenance tasks. This helps forecast inventory needs better and decreases the chance of sudden different maintenance types costs.
Cut-Down Maintenance Cost
Predictive maintenance, a product of maintenance digitization, helps reduce costs.
An organization can allocate its resources efficiently through the use of the new technology and thus reduce the time the maintenance is required to spend on each task by manipulating the technology. This transformation in the way of maintenance, from reactive to proactive, helps an organization manage costs and also raises productivity.
Better Decision Making
Digital maintenance services give companies access to up-to-the-minute data and analytics on equipment performance, maintenance needs, and other critical factors.
By using data to drive planned and reactive maintenance decisions, companies can effectively plan their schedules, allocate their resources most efficiently, and enhance their decision-making processes. The use of data in this way promotes a culture of continuous improvement in your maintenance.
The Role of Reactive Maintenance in Facility Management
Reactive maintenance software assists in different facility maintenance types and allows maintenance teams to stay on top of their operations by increasing team awareness and reducing delay while responding to repair needs.
This software functions as a centralized asset, facilitating the management of off-scheduled and reactive maintenance tasks while guaranteeing that any unexpected occurrences within the facility are dealt with with a prompt and effective response.
Advantages of Incorporating Software into Run-to-Failure Maintenance Techniques
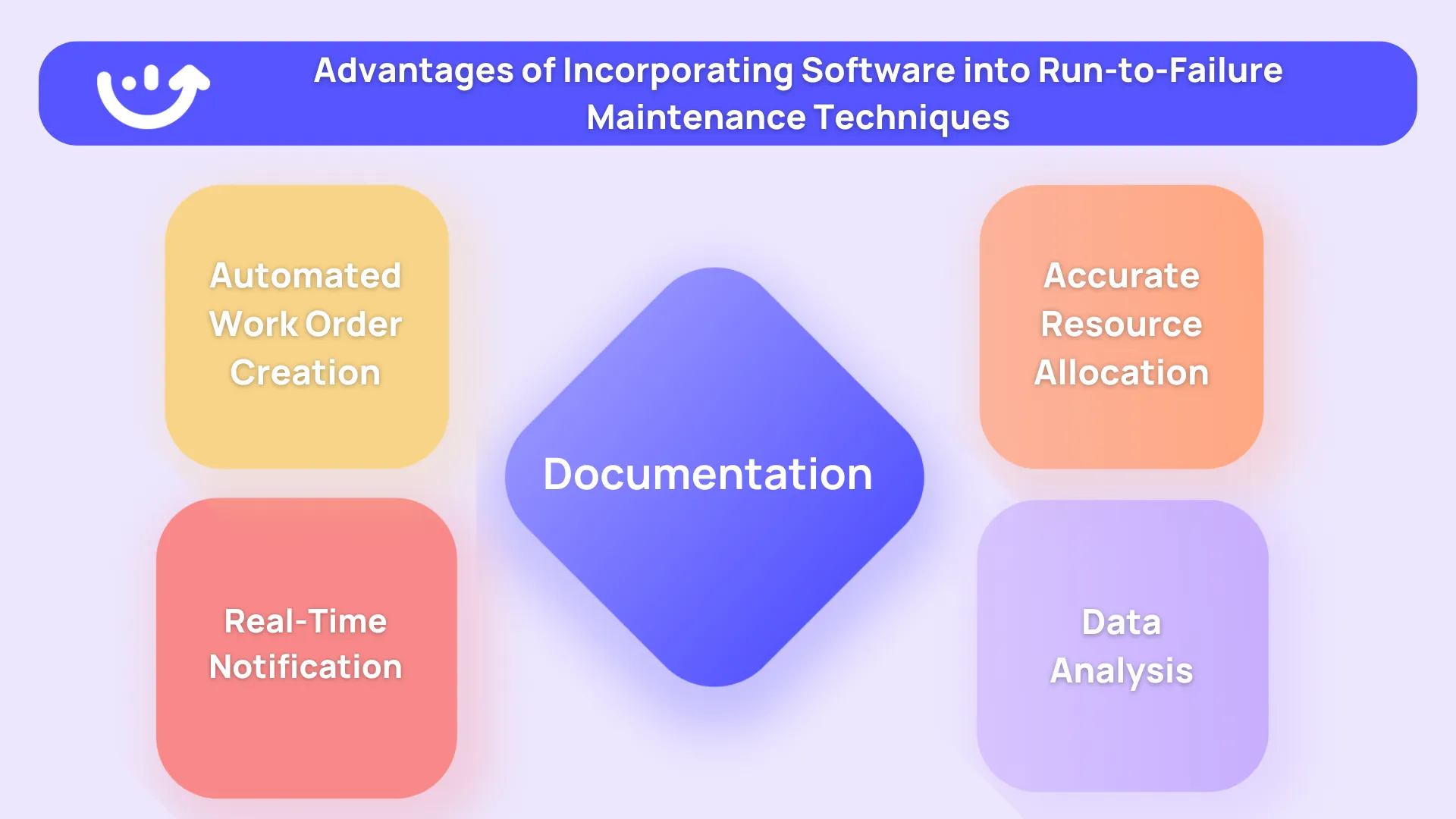
Automated Work Order Creation
Reactive maintenance software automatically creates work orders when equipment fails. This ensures that the maintenance staff is alerted to any issues quickly, allowing them to react swiftly to fix the breakdowns.
Accurate Resource Allocation
The software helps in the priority assignment of different maintenance-type tasks by differentiating between urgent and corrective maintenance. This enables an efficient allocation of resources ensuring that critical issues are attended to immediately and others are handled based on priorities.
Real-Time Notification
Implementing software into run-to-failure maintenance methods helps to monitor the health of equipment in real-time. The alerts that can be generated by software, when key performance indicators differ from acceptable values, allow a maintenance team to, ahead of time, address the potential failures.
Data Analysis
Software for planned and reactive maintenance records failure /operational histories of equipment. Analysis of this information assists in the recognition of recurring issues, tendencies, and patterns, enabling equipment managers to make informed decisions about replacement, upgrade, or changes to maintenance strategies.
Documentation
This software enables the recording of different maintenance types of activities and has an extensive reporting capability. This documentation is valuable for compliance, audits, and analysis respectively, and assists in continually improving.
Features of Reactive Maintenance Software that Help with Different Maintenance Types
Emergency Management
Planned and Reactive maintenance software has features that allow for speedy response to emergencies. This might include assigning tasks straight once, determining which lines of communication are available, and following the resolution process to ensure operational safety and occupant integrity.
Corrective Maintenance
In terms of corrective maintenance, the planned and reactive maintenance software helps plan and schedule tasks by priority and the availability of resources. It ensures that a maintenance team can effectively handle non-urgent issues to prevent any minor problems from becoming an emergency.
Run to Failure Maintenance
The software allows assets to be tracked to failure in the context of "run to failure maintenance". It provides a look into failure frequency and type, helping strategic decisions about maintaining this maintenance strategy or changing to something more proactive.
Wrapping it Up
Although it is often viewed as a burden, maintenance can be much more than a cost center. If properly carried out, planned and reactive maintenance can deliver significant cost, productivity, and risk management benefits by minimizing machine problems.
Preventing prolonged periods of inactivity by addressing unexpected equipment failures promptly safe managers against financial losses. In addition, this approach elevates productivity by ensuring sustained efficiency of equipment. Optimal Machinery working projects positive output and efficiency, leading to enhanced financial growth of the business.
Avoiding extended downtime by promptly addressing unforeseen equipment malfunctions protects against the loss of revenue. Moreover, it enhances equipment efficiency, thereby bolstering productivity. With machinery functioning optimally, operational output and efficiency rise, both of which contribute favorably to overall business performance.
IDC's forecast that 80 billion IoT devices would be online by 2025, creating more than 180 zettabytes of data, demonstrates the large amount of data that can be collected through IoT.
Organizations will be able to provide real-time data on equipment health and functionality by incorporating sensors and linked devices. The capacity to handle and analyze such a large volume of data ensures that decisions are based on the most recent, accurate, and relevant data, allowing for proactive equipment maintenance.
To support the continued operation of your equipment, you need to maintain the uninterrupted operation of your organization.
Digital solutions like advanced software, Xenia, make it easier. It enables proper audit trails, accurate record-keeping, and efficient cost accounting. By elevating reactive maintenance beyond responsiveness, the digital toolset makes it just what it needs to be—proactive maintenance that keeps operational excellence and your organization cued up like a well-oiled machine.
.webp)
%201%20(1).webp)